Формирование покрытий с нанокристаллической и аморфной структурой плазменным напылением
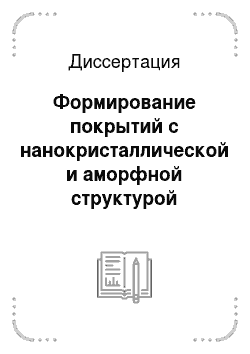
Плазменное напыление существует в нескольких модификациях: напыление в атмосфере воздуха и в инертной атмосфере с использованием камеры. Оба этих способа имеют ограничения. Разработанный и исследованный способ напыления с местной защитой от атмосферы воздуха с помощью насадки к плазмотрону занял нишу между этими двумя способами и позволил существенно снизить содержание кислорода воздуха в зоне… Читать ещё >
Содержание
- Цель работы
- Научная новизна и положения, выносимые на защиту
- Глава I. Состояние вопроса по формированию покрытий с аморфной структурой плазменным напылением
- 1. 1. Условия формирования микрослитков при скоростях охлаждения 103−108 К/с
- 1. 2. Формирование, аморфных лент при спиннинговании
- 1. 3. Формирование структуры в быстрозакаленных плазменнонапыленных покрытиях.151.3.1. Металлургические особенности процесса плазменного напыления
- 1. 3. 1. 1. Состояние частиц до соударения с подложкой
- 1. 3. 1. 2. Условия деформации, затвердевания и охлаждения частиц на подложке
- 1. 4. Существующие технологические процессы нанесения аморфных покрытий плазменным напылением
- Выводы
- Глава II. Методики, материалы и оборудование при исследовании процесса плазменного напыления покрытий с аморфной структурой
- 2. 1. Материалы и оборудование используемые для проведения, исследований
- 2. 2. Методика определения скоростей напыляемых частиц в сечении пятна напыления
- 2. 3. Методика калориметрических измерений тепловых потоков, воздействующих на подложку по зонам пятна напыления
- 2. 4. Исследования структуры и физикохимических свойств покрытий
- Выводы
Глава III. Сравнительные исследования энергетического состояния напыляемых частиц и структуры покрытий, формируемых при плазменном напылении с применением конической насадки и при традиционном способе напыления.
3.1. Измерение скоростей движения напыляемых частиц.
3.2. Измерение величин. тепловых потоков действующих на подложку
3.3. Металлографические исследования структуры покрытий полученных при напылении на неподвижные подложки.
3.3.1. Структурные состояния частиц образующих покрытия.
3.3.21 Распределение пористости в сечении пятна напыления.
3.4. Адгезионная прочность покрытий полученных при плазменном напылении.
3.5. Содержание кислорода в зоне напыления.
Выводы.
Глава IV. Исследование факторов влияющих на процесс формирования аморфной структуры в покрытиях из сплава Со58№ 1оРе5В1б8111 при плазменном напылении.
4.1. Характер затвердевания частиц сплава СозвМюРезВ]^!! при охлаждении в газовом потоке.
4.2. Особенности формирования покрытий на неподвижной подложке при плазменном напылении с использованием насадки к плазмотрону и при напылении стандартным способом.
4.2.1. Формирование покрытий при напылении без перемещения подложки.
4.2.2. Распределение частиц, содержащих выделения кристаллических фаз, в пятне напыления.
4.3. Влияние фазового состояния, размера и формы напыляемых частиц на формируемое покрытие.
4.4. Влияние энергетического состояния напыляемых частиц на-структуру формируемого покрытия.
4.5. Условия формирования покрытий с аморфной структурой на движущейся подложке.
4.5.1. Расчет температуры системы «покрытие-подложка"[28].
4.5.2. Влияние изменения скорости перемещения подложки относительно плазмотрона на структуру покрытий.864.5.3. Влияние толщины покрытия образованного за один проход на его структуру.
4.6. Структура и физико-химические свойства покрытий.
4.6.1. Адгезионная прочность покрытий.
4.6.2. Рентгеновский фазовый анализ напыленных покрытий.
4.6.3. Электронно-микроскопические исследования на просвет.
4.6.4. ББС анализ напыленных покрытий.
4.6.5. Исследование химического состава покрытий.
4.6.6. Измерения магнитных характеристик образцов покрытий.
Выводы.
Глава V. Основы технологии и оборудование для нанесения аморфных магнитномягких покрытий.
5.1. Конструкция насадки к плазмотрону для регулирования термического воздействия плазменной струи на напыляемые частицы и формируемое покрытие.
5.2. Разработка основ технологии нанесения экранирующих покрытий на корпуса изделий.
5.2.1. Подготовка поверхностей под нанесение покрытий.
5.2.2. Механизм для перемещения напыляемой детали и плазмотрона
5.2.3. Система подачи порошка в плазменную струю.
5.3. Вредные факторы, влияющие на окружающую среду, и условия труда при плазменном напылении.
5.4. Магнитомягкие экраны на корпусах электромеханических изделий.
Выводы.
Глава VI. Формирование наноструктурных плазменных покрытий 132 6.1. Формирование нано размерных упрочняющих фаз в плазменных покрытиях из сталей, чугунов и сплавов на основе железа.
6.3. Плазменные керметные покрытия с наноразмерным карбонитридом титана [63].
6.4. Формирование композиционных наноструктурных покрытий. 175 6.4. 1. Формирование пористой структуры плазменных покрытий при произвольном угле соударения напыляемых частиц с подложкой.
6.4.2. Формирование наноструктурных биоактивных покрытий на границе раздела композиционного материала «костная ткань — имплантат»
Выводы.
Список литературы
- Русович Н., Анализ теплообмена при разных условиях сверхбыстрой закалки. Метастабильные и неравновесные сплавы./ Под ред. Ефимова Ю.В.-М.- Металлургия, 1988. с.140−187.
- Ruhl R.C. Cooling Rates in Splat Cooling. Mater. Sci. and Eng. 1967, v. l, № 6, p.313−320.
- Манов В.П., Попель С. И., Булер П. И. Влияние состава расплава на структурночувствительные свойства аморфных сплавов Fe-B u Pd-Si. Расплавы. 1989, № 1, с.23−35.
- Muhlbach Н., Stephani G., Sellger R. Cooling Rate and Heat Transfer Coefficient during Planar Flow Casting of Microcrystalline Steel. Ribbons, Inernat. J. of Rapid Solidif. 1987, v.3, p.83−94.
- Vogt E. On the Heat Transfer Mechanism in the Melf Spinning Process. Internat. J. of Rapid Solidif., 1987, v.3. p.131−146.
- Huang S.C., Fiedler H.C. Effects of Wheel Surface Conditions on the Casting of Amorphous Metal Ribbons. Met. Transact. 1981, V.12A, № 6, p.1107−1112.
- Fidler H., Illgen L., Barth M. Influence of C02 gas flow around the melt puddle on the surface roughness of Fe79Bi4Si ribbons. Materials Science and Engineering. 1991, V. A133, p.657−661.
- Vincent A.J.B., Bewlay B.P., Cantor B. Cooling rates and microstructure in planar flow cast Ni-20 wt% Al. I. Materials Science. Letters. 1987, v.6, p.121−124.
- Bewlay B.P., Cantor B. Photo calorimetric cooling rate measurement on 316 L stainless steel rapidly solidified by melt spinning. Int. J.Rapid. Solidificat. 1986, v.2, № 2, p. 107−123.
- Кудинов В.В., Пекшев П. Ю., Белащенко В. Е., Солоненко О. П., Сафиуллин В. А. Нанесение покрытий плазмой./- М.: Наука. 1990−408 с.
- Могеап С., Cielo P., Dallaire S., Temperature evolution of plasma-sprayed niobium particles impacting on a substrate. Surface and Coatings Technology, 1991, v.46, p.173−187.
- Кудинов B.B. Плазменные покрытия,— M.: Наука, 1977- 184с.
- Fauchais P., Grimaud A., Vardelle A. La projection par plasma: une revue. Ann. Phys. Fr.1989, 14, p.261−310.
- Сафаи С., Герман Г., Материалы, получаемые плазменным напылением. Сверхбыстрая закалка жидких сплавов: Сб. научных трудов. Под. ред., Германа Г.-М.: Металлургия, 1986. с.146−172.
- Могеап С., Lamontagne М., Cieio P. Surface and Coat. Technolog. 1992, v.53, № 2, p.107—114.
- Барвинок В.А. Управление напряженным состоянием и свойствами плазменных покрытий.- М.: Машиностроение, 1990.-384с.
- Калита В.И., Берниковский Б. К., Коптева О. Г. Структура и физико-механические свойства плазменных покрытий. XI Всесоюзная конференция. Теория и практика газотермического нанесения покрытий. Дмитров. 1989 г. с.52−55.
- B.C. Giessen, N.M. Madhava, R.J. Murphy, R. Ray, J. Surette. Sheet Production of an Amorphous Zr-Cu Alloy by Plasma Spray Quenching. Metall. Trans. 1977, v. 8A, № 2, p. 364- 366.
- Murakami K., Okamoto Т., Miyamoto Y. Deposition of amorphous layers of an Fe-B-Si alloy by low pressure plasma spraying. Materials Science and Engineering, 1991, v. A145, p. 215−221.
- Лепишев A.A. Закономерности формирования структуры массивных аморфных и мелкокристаллических покрытий при плазменном напылении металлических сплавов ПМ-М. / Препринт №−745Ф. ИФ СО РАН, 1993,31с.
- Murakami К., Okamoto Т., Miyamoto Y. Rapid solidification and Self-annealing of Fe-C-Si Alloys by Low Pressure Plasma Spraying. Materials Science and Engineering. 1989, v. A117, p. 207−214.
- Murakami K., Asako H., Okamoto Т., Miyamoto Y. Microstructure and Mechanical Properties of rapidly Solidified Deposited Layers Fe-C-Cr Alloys Produced by Low Pressure Plasma Spraying. Materials Science and Engineering. 1990, v. A123, p. 261−270.
- Кудинов В.В., Калита В. И., Комлев Д. И., Коптева О. Г. Анализ распределения скоростей и удельной энтальпии частиц по радиусу пятна напыления при использовании конической насадки. — Физика и химия обраб. материалов, 1992, № 5, с.82−85.
- Калита В.И., Кекало И. Б., Комлев Д. И., Тараничев В. Е. Структура и свойства массивных аморфных магнитномягких покрытий, получаемых плазменным напылением. ФММ. т.80, вып. 2., 1995, с.3548.
- Кулешов Б.М. Термовременная обработка расплава перед аморфизацией / Сталь. 1993. № 7. с. 69−74.
- Саунин В.Н. Технологические особенности плазменного напыления аморфных покрытий магнитных экранов космических аппаратов. Автореферат диссертации канд. техн. наук. —Красноярск.-1995.^42 с.
- Wei Gao, Cantor В. The Oxidation Behaviour of Amorphous and Crystalline Co58Ni10Fe5SiiiB16// Inter. J. of Rapid Solid. 1989. V.4. P. 153−179.
- Калита В. И. Комлев Д.И. Формирование аморфных магнитномягких покрытий плазменным напылением.-Перспективные материалы, 1996, № 6, с.5−16.
- Кекало И.Б., Цветков В. Ю. Особенности формирования магнитных свойств при отжиге и их температурно-временная стабильность в аморфном сплаве FesCossNiioSinB^. -ФММ, 1985, 59, вып. З, с.489197.
- Кекало И.Б., Жданов А. Н., Цветков В. Ю. Влияние отжига в поперечном магнитном поле на проницаемость аморфного сплава Fe5Co70Sii5Bi0. -ФММ, 1984, вып.6, с.1213−1215.
- Кекало И.Б., Самарин Б. А. Физическое металловедение прецизионных сплавов. Сплавы с особыми магнитными свойствами. —М.: Металлургия, 1989.-496с.
- Кекало И.Б., Введенский В. Ю., Тараничев В. Е. и др. Влияние исходного состояния аморфного сплава Co-Cr-Zr с близкой к нулю магнитострикцией на характер изменения магнитных свойств при отжиге. -ФММ, 1989, 68, вып. З, с.494196.
- Новиков В.Ю., Кекало И. Б. Магнитномягкие сплавы (кристаллические и аморфные). В кн.: Итоги науки и техники. Металловедение и термическая обработка. -М.: ВИНИТИ, 1984, 18, с.3−56.
- Люборский Ф.Е. Магнитные свойства, важные для применения в технике.- В кн.: Аморфные металлические сплавы. -М.: Металлургия, 1987, с.356−375.
- Yagi М., Sawa Т. Soft magnetic propertiffsof ultrathin Co-based amorphous alloy ribbons with thickness of 3−10mkm. -Jeet Trensactions on magnetics, 1990, v.26, № 5, p. 1409−1411.
- Рыкалин H.H., Николаев A.B., Кудинов B.B. и др. Нагрев порошка в стабилизированной магнитным полем струе при плазменном напылении. Автоматическая сварка, 1968, № 8, с.29−33.
- Линкин В.А., Пекшев П. Ю. Современная техника газотермического нанесения покрытий./ -М.: Машиностроение, 1985, 127 с.
- Inoue A., Wang X.M. Bulk amorphous FC20 (Fe-C-Si) alloys with small amounts of В and crystallized structure and mechanical properties/ Acta Mater. 2000, v. 48, p. 1383−1395.
- Калита В.И., Комлев Д. И. К вопросу формирования металлов в аморфном состоянии. Металлы 2003, № 6, с. 30 37.
- Гуляев А.П. Металловедение. Металлургия. М. 1977. с. 647.
- Александрова Н.М., Макушев С. Ю., Лясоцкий И. В., Дьяконова Н. Б., Дьяконов Д. Л., Супов A.B. Структурообразование и свойства быстрозакаленной из расплава стали Р6М5. Сталь. 2004. № 11, с. 100 103.
- Григорович В. К. Твердость и микротвердость металлов. Наука. М., 1976 г. 230 с.
- Сафонов E.H. Структура и твердость чугуна после поверхностной закалки. МИТОМ. 2005. № 9, с. 38−43.
- Калита В.И., Комлев Д. И. Особенности формирования структуры аморфно-кристаллических покрытий при плазменном напылении. Физхом. 1996, № 4, с. 43−46.
- Калита В.И., Бочарова М. А., Трушникова A.C., Шатерников Б. Н. Структура поверхности титановых материалов, предназначенных для внутрикостных имплантатов. Металлы. 2005, № 3, с. 105 -113.
- Проблемы порошкового материаловедения. Часть VI. Плазменно-лазерные покрытия. Шмаков А. Н., Анциферов В. Н., Буланов В .Я., Ханов A.M. Екатеринбург. 2006. с. 588.
- Гуревич Ю.Г., Нарва В. К., Фраге Н. Р. Карбидостали. М.: Металлургия, 1988. 144 с.
- Хасуи А., Моригаки О. Наплавка и напыление. М.: Машиностроение, 1985. 240 с.
- Кудинов В.В., Калита В. И., Коптева О. Г. Исследование процесса формирования макро и микроструктуры частиц газотермических покрытий. Физхом, 1992, № 3, с. 88−92.
- Leigh S. Н., Berndt С.С. Evaluation of off-angle thermal spray. Surface and Coatings Technology. 1997, v. 89, p.213−224.
- Kanouff M.P., Neiser R.A., Roemer Jr., Roemer TJ. Surface Roughness of Thermal Spray Coatings Made with Off-Normal Spray Angles. Journal of Thermal Spray Technology. 1998, v. 7(2), p. 219−228.
- В.И. Калита, А. Г. Гнедовец, Д. И. Комлев. Формирование пористости при плазменном напылении. Физхом 2006. № 6, с. 26 — 31.
- Гнедовец А.Г., Калита В. И. Модель формирования макроструктуры покрытий при плазменном напылении. Физхом. 2007. № 1, с. 26 31.
- Калита В.И., Соколов В. H., Парамонов В. А. Трехмерные капиллярно-пористые покрытия. Физхом, 2000, № 4, с. 55—61.
- Соколов В.Н., Калита В. И., Юрковец Д. И., Разгулина О. В., Крылов И. К. Структура свободной поверхности трехмерных капиллярно -пористых титановых покрытий. Физхом. 2004, № 2, с. 36−41.
- Kalita Vassili I., Gnedovets Alexey G. Plasma Spraying of Capillary Porous Coatings: Experiments, Modeling, and Biomedical Applications. Plasma Processes and Polymers. 2005, 2, p. 485−492.
- Kalita V.I., Gnedovets A.G. Engineering of plasma spray porous coatings. th
- Abstracts and Full-Papers CD of 17 International Symposium on Plasma Chemistry (ISPC-17). August 7 12, 2005. Toronto, Canada, p. 962 — 963. CD Paper 536, p. 1 — 6.
- Mouzin Oliver, Soballe Kjeld, Bechtold Joan E. Loading Improves Anchorage of Hydroxyapatite Implants More than Titanium Implants. J Biomed Mater Res (Appl Biomater). 2001, v. 58, № 1, p. 61−68.
- Калита В.И., Багмутов В. П., Захаров И. Н., Комлев Д. И., Иванников А. Ю. Упрочнение плазменных покрытий электромеханической обработкой. Физхом. 2008. № 1, с. 38−42.
- Калита В. И., Умнов П. П., Куракова Н. В., Молоканов В. В., Комлев Д. И. Керметные плазменные покрытия TiB2-Ni(Ni-Mo), сформированные из механически легированных порошков. Физхом. 2008. № 3, с. 49- 55.