Систематические погрешности механической обработки
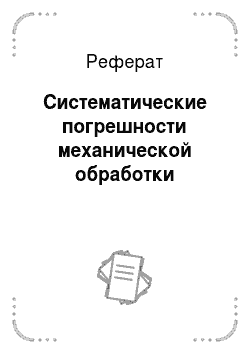
Систематические погрешности обработки заготовок могут быть вызваны неправильной установкой опор станков, искривлением направляющих при монтаже, оседании фундаментов, а также прогибом под действием собственной массы. Систематическая погрешность — это такая погрешность, которая для всех заготовок рассматриваемой партии остаётся постоянной или же закономерно изменяется при переходе от каждой… Читать ещё >
Систематические погрешности механической обработки (реферат, курсовая, диплом, контрольная)
Систематическая погрешность — это такая погрешность, которая для всех заготовок рассматриваемой партии остаётся постоянной или же закономерно изменяется при переходе от каждой обрабатываемой заготовки к следующей.
Причинами возникновения систематических погрешностей обработки являются: неточность, износ и деформации станков, приспособлений и инструментов; деформации заготовок, тепловые процессы, происходящие в технологической системе, погрешности теоретической схемы обработки, погрешности наладки технологической системы на размер; погрешности измерений.
Погрешности, связанные с неточностью, износом и деформацией станков
Металлорежущие станки выпускаются промышленностью с определённой степенью точности. Существуют станки нормальной, повышенной, высокой, особо высокой точности и особо точные. Для каждой группы станков ГОСТом определены нормы точности станков в ненагруженном состоянии. Так, например, для токарно-винторезного станка мод. МК6056Р (станок нормальной точности средних размеров) определены следующие характеристики геометрической точности:
- — радиальное биение конца шпинделя 0,01 мм;
- — торцовое биение шпинделя 0,01−0,02 мм;
- — биение конического отверстия в шпинделе 0,02 мм;
- — прямолинейность направляющих станины 0,02 мм;
- — параллельность оси шпинделя направлению движения каретки в вертикальной плоскости на длине 300 мм 0,02- 0,03 мм;
- — в горизонтальной плоскости 0,01−0,015 мм.
Таким образом, даже новый станок имеет погрешности геометрической точности, которые полностью или частично передаются в процессе механической обработки на заготовку в виде систематических погрешностей. На рис. 1.9 показаны примеры влияния погрешностей станков на обрабатываемые заготовки.

Рис. 1.9. Примеры переноса погрешностей станков
При непараллельности оси шпинделя токарного станка направлению движения суппорта в горизонтальной плоскости (рис. 1.9, а), заготовка становится конической.
При непараллельности оси шпинделя токарного станка направлению движения суппорта в вертикальной плоскости (рис. 1.9, б), заготовка приобретает форму гиперболоида вращения.
При неперпендикулярности оси шпинделя вертикальнофрезерного станка к плоскости стола в продольном направлении (рис. 1.9, в), на обрабатываемой заготовке появляется вогнутость, которая зависит от диаметра фрезы, угла наклона шпинделя и ширины обрабатываемой поверхности.
При неперпендикулярности оси шпинделя вертикальнофрезерного станка к плоскости стола в поперечном направлении (рис. 1.9, г) возникает непараллельность обработанной плоскости заготовки относительно установочной.
Биение посадочных поверхностей шпинделей токарных станков, которое может быть вызвано неточностью их изготовления или неправильной регулировкой подшипников, приводит к искажению формы обрабатываемой заготовки в поперечном сечении: овальность, некруглость, разбивка отверстий и т. д.
Перенос погрешности станков на обрабатываемые заготовки имеет место и у всех других типов станков: сверлильных, шлифовальных, координатно-расточных, фрезерных, строгальных и т. д.
К увеличению систематических погрешностей обрабатываемых заготовок ведёт износ станков в процессе их эксплуатации, происходящий неравномерно. Больший износ имеют поверхности станков, которые наиболее интенсивно используются при его работе, например направляющие. Причём износ таких поверхностей происходит неравномерно по их длине: у токарных станков средних размеров участок наибольшего износа направляющих находится на расстоянии.
- 350. .400 мм от торца шпинделя (на рис. 1.9, д показана лунка износа). Это вызвано тем, что в этом месте осуществляется наиболее интенсивное движение суппорта, поскольку станок предназначен для обработки валов средних размеров
- 300. .500 мм.
Систематические погрешности обработки заготовок могут быть вызваны неправильной установкой опор станков, искривлением направляющих при монтаже, оседании фундаментов, а также прогибом под действием собственной массы.