Изготовление литейных форм
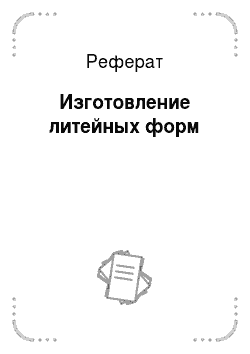
Резервуар; 2 — гильза; 3 — смесь; 4 — клапан; 5 — ресивер; 6 — сопло; 7 — надувная плита; 8 — венты; 9 — стержневой ящик; 10 — бункер Стержневая смесь из бункера 10 периодически поступает в пескодувный резервуар 1, который после этого при открытии клапана 4 заполняется сжатым воздухом из ресивера 5. В гильзе 2 резко повышается давление, и стержневая смесь 3 выталкивается через сопло 6 в полость… Читать ещё >
Изготовление литейных форм (реферат, курсовая, диплом, контрольная)
Формовка — это процесс изготовления разовых литейных форм, при котором выполняют следующие технологические операции:
- • уплотнение смеси, позволяющее получить точный отпечаток в форме и придать ей необходимую прочность в сочетании с податливостью, газопроницаемостью и другими свойствами;
- • извлечение модели из формы;
- • отделка и сборка формы, включая установку стержней.
Литейные формы делают: вручную, на формовочных машинах, полуавтоматических и автоматических линиях.
Существует три основных способа машинной формовки: в парных опоках, стопочный и безопочный.
По первому способу формы изготовляют на двух формовочных машинах с односторонними модельными плитами в двух парных опоках: одна для нижней и другая для верхней платформы (рис. 7.13).

Рис. 7.13. Схема изготовления формы в парных опоках:
а — модельные плиты верха и низа; б — изготовленные полуформы; в — собранная форма; 1, 3 — нижняя и верхняя полуформы; 2 — литниковая система; 4 — стержень; 5 — полость формы; 6, 7 — модели низа и верха; 8 — модельная плита; 9 — штырь; 10 — питатель При стопочной формовке формы изготовляют по двусторонним модельным плитам (рис. 7.14).

Рис. 7.14. Установка форм по стопкам:
1 — канал; 2 — полость формы; 3 — двухсторонняя плита; 4 — рым-болт; 5 — литник При безопочной формовке на автоматических линиях (рис. 7.15) формы изготовляют в формовочной камере по модельным плитам 2, 4. Уплотненный ком 6' формовочной смеси плунжером 3 проталкивается по плите 7 до соприкосновения с предыдущим комом 8, образуя полость 9. В результате получается непрерывный ряд форм, заливаемых из ковша 11.

Рис. 7.15. Схема автоматической линии для безопочной формовки:
1 — бункер; 2, 4 — модельные плиты; 3 — плунжер; 5 — формовочная смесь; 6,8 — формовочный ком; 7 — плита; 9 — полость литейной формы; 10 — отливка; 11 — ковш Существует несколько методов уплотнения формовочной смеси.
Прессование
Под воздействием давления сжатого воздуха в прессовом поршне 5 (рис. 7.16) колодка 1 входит внутрь наполнительной рамки 3 и уплотняет формовочную смесь 2 в опоке 4. Плотность смеси уменьшается по мере удаления от прессовой колодки. Способ используют для формовки в невысоких опоках (высотой 200−250 мм).

Рис. 7.16. Схема прессования.
Встряхивание
Уплотнение встряхиванием ведут в пневматической формовочной машине (рис. 7.17). Сжатый воздух подают в нижнюю часть цилиндра 1 (рис. 7.18), при этом стол 2 поднимается на высоту 25−80 мм. При открытии выхлопного окна сжатый воздух выходит в атмосферу и стол 2 с моделью 3 падает на торец цилиндра 1. Формовочная смесь в опоке 4, продолжая двигаться по инерции, уплотняется. Стол обычно совершает 120−200 ударов в минуту. Бо? льшую плотность имеют слои смеси вокруг модели.

Рис. 7.17. Машина формовочная пневматическая встряхивающая.

Рис. 7.18. Схема встряхивания.
Для уплотнения верхних слоев формы встряхивание совмещают с прессованием.
Уплотнение пескометом
Рабочий орган пескомета — метательная головка 1, которая выбрасывает пакеты смеси 5 на рабочую поверхность модельной плиты 7 (рис. 7.19).

Рис. 7.19. Схема пескомета.
Смесь уплотняется равномерно по высоте опоки 6 за счет кинетической энергии. Она подается в головку непрерывно ленточным конвейером 3 через окно 2, при вращении ковша 4 (до 20 об/с) собирается в пакеты 5 и центробежной силой выбрасывается через выходное отверстие на рабочую поверхность модели 7.
Вакуумная формовка
Сущность метода в том, что форма, изготовляемая из сухого песка, уплотняется вибрацией и упрочняется под действием атмосферного давления (рис. 7.20).

Рис. 7.20. Схема вакуумной формовки:
1 — полость вакуумирования; 2 — модель; 3 — модельная плита; 4 — основание плиты; 3, 7 — полимерная пленка; 6 — вибраторы; 8 — нагреватели; 9 — опока; 10, 11 — питатели; 12 — кварцевый песок; 13 — отливка Модельную плиту 3 (рис. 7.20, а) с моделью 2 накрывают разогретой полимерной пленкой 5. Вакуумным насосом в полости 1 откачивают воздух.
Пленка плотно прижимается к модели. На модельную плиту устанавливают опоку 9 (рис. 7.20, б), которую заполняют сухим кварцевым песком 12 и уплотняют его с помощью вибратора 6. На верхнюю поверхность накладывают полимерную пленку 7, которая за счет разряжения плотно прилегает к опоке, что способствует уплотнению песка и устойчивости формы. Затем полуформу снимают с модели (рис. 7.20, в). Вакуумирование продолжается не только при изготовлении полуформ, но и при их сборке, заливке (рис. 7.20, г, д) и затвердевании залитого литейного материала. При заливке пленка сгорает.
Процесс позволяет получать отливки 13 из различных сплавов (чугуны, стали, медные и алюминиевые сплавы) массой от нескольких грамм до нескольких тонн в условиях единичного и массового производства. В серийном и массовом производстве формовка осуществляется на автоматических линиях.
К преимуществам процесса относятся: удешевление формовочной смеси и упрощение смесеприготовления; повышение точности и чистоты поверхности отливки, благодаря отсутствию связующих и влаги в форме; упрощение выбивки форм; увеличение срока службы оснастки.
Изготовление литейных стержней
Стержни в литейной форме испытывают значительные тепловые и силовые нагрузки. Они должны обладать высокой термоустойчивостью, прочностью и в то же время хорошей выбиваемостью. В качестве материала для их изготовления широко распространены песчано-смоляные смеси, отверждаемые под действием нагрева или при вводе отвердителя. Формообразование осуществляется в стержневом ящике, полости которого могут быть заполнены стержневой смесью различными способами. В современном литейном производстве наиболее распространены пескодувные стержневые машины (рис. 7.21).

Рис. 7.21. Схема работы пескодувной стержневой машины:
1 — резервуар; 2 — гильза; 3 — смесь; 4 — клапан; 5 — ресивер; 6 — сопло; 7 — надувная плита; 8 — венты; 9 — стержневой ящик; 10 — бункер Стержневая смесь из бункера 10 периодически поступает в пескодувный резервуар 1, который после этого при открытии клапана 4 заполняется сжатым воздухом из ресивера 5. В гильзе 2 резко повышается давление, и стержневая смесь 3 выталкивается через сопло 6 в полость стержневого ящика 9. Для выпуска воздуха в надувной плите 7 и стержневом ящике 9 предусмотрены венты 8. Пескодувные машины обладают высокой производительностью и обеспечивают высокое качество уплотнения стержневой смеси.
Сущность технологического процесса изготовления стержней в нагреваемой оснастке состоит в том, что смесь с быстротвердеющим связующим (синтетической смолой) с помощью пескодувной машины вдувается в стержневой ящик, предварительно нагретый до 200−250°С. Под действием нагрева смола полимеризуется, смесь затвердевает, придавая прочность стержню. После непродолжительной выдержки (~30 с) ящик раскрывают и извлекают стержень.