Этапы решения задач автоматизированного проектирования промышленных аппаратов
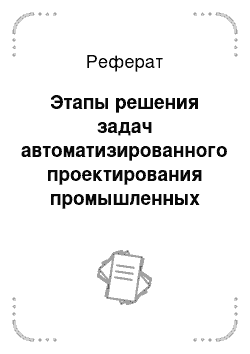
Выделение целевых продуктов, появляющихся в результате химических превращений, является одним из распространенных процессов химической технологии. Для этой цели служат процессы абсорбции, экстракции, кристаллизации, ректификации и т. д. Современные требования по снижению энергозатрат на ведение процессов разделения (к.п.д. от использования тепла при ректификации 5−10%), обусловленные ростом цен… Читать ещё >
Этапы решения задач автоматизированного проектирования промышленных аппаратов (реферат, курсовая, диплом, контрольная)
Поскольку процессам химической технологии свойственна детерминированно-стохастическая природа (при этом детерминированная составляющая определяется фундаментальными законами физической химии), то стохастическая составляющая по своей природе отражает нестационарность процессов, проявляющуюся в различном распределении элементов фаз по времени пребывания в аппарате, характеру распределения включений, по степени химического превращения, вязкости, плотности и другим физико-химическим свойствам.
Детерминированная составляющая на основе фундаментальных законов — закона Ньютона, переноса массы и энергии и т. п. — позволяет строго теоретически определить скорость протекания того или иного процесса, а следовательно, и время для достижения конечного состояния или завершенности процесса при данной скорости. Однако в промышленных аппаратах действительное время завершения процесса может не соответствовать времени, полученному на основе классических законов, так как оно зависит от условий протекания процесса в аппарате, характера структуры потоков, обусловленного конструкцией аппарата, внешнего подвода энергии, наличия в аппарате устройств, изменяющих характер и направление движения пара и жидкости, и т. д.
Если не учитывать стохастической составляющей, то непосредственный перенос результатов эксперимента, проведенного в лабораторных условиях, на промышленные аппараты невозможен.
Совершенствование методов математического моделирования и средств вычислительной техники позволило изменить методологию исследования диффузионных процессов, происходящих в аппарате.
В 1950;1960 гг. при конструировании и проектировании промышленных аппаратов широкое использование получила теория подобия, основанная на чистом детерминизме и предусматривающая использование критериальных уравнений гидродинамики и кинетики. Однако такой подход приемлем только для однофазных систем, в химической технологии, как правило, наблюдаются двухфазные многокомпонентные системы.
Учет стохастической составляющей процессов давно обусловил необходимость синтеза операторов физико-химической системы (ФХС), базирующегося на модельных представлениях о внутренней структуре процессов, происходящих в технологических аппаратах.
Основа этого подхода заключается в наборе типовых операторов, отражающих простейшие гидродинамические модели (идеального смешения, вытеснения, диффузионная модель, ячеечная и комбинированные), которые позволяют установить время завершения процесса.
Математическое описание технологического процесса в этом случае сводится, наряду с учетом детерминированного описания, к подбору комбинации простейших операторов, с тем чтобы результирующая модель достаточно точно отражала структуру реального процесса.
Рассмотрим постановку и решение задачи системного подхода к исследованию и созданию высокоинтенсивных массообменных аппаратов и технологических схем разделения.
Выделение целевых продуктов, появляющихся в результате химических превращений, является одним из распространенных процессов химической технологии. Для этой цели служат процессы абсорбции, экстракции, кристаллизации, ректификации и т. д. Современные требования по снижению энергозатрат на ведение процессов разделения (к.п.д. от использования тепла при ректификации 5−10%), обусловленные ростом цен на источники энергии, привели к интенсификации исследований по поиску более эффективных способов разделения. Это, прежде всего, разработка новых аппаратов, совмещенные процессы, рекуперация тепла продуктовых потоков внутри технологической схемы, организация парожидкостных и тепловых потоков в ректификационных колоннах и реакторах с периодическими циклами и т. д.
Создание высокоинтенсивной технологической схемы, оптимальной с учетом некоторого критерия, должно проводиться в несколько этапов: это выбор процесса (абсорбция, ректификация, экстракция и т. п.), анализ свойств компонентов и смесей, выбор технологической схемы, выбор оборудования (рис. 1.1). Каждый из этапов является достаточно трудоемким, так как связан с выполнением ряда самостоятельных задач, между собой они взаимосвязаны конечной целью. Вероятность получения оптимального варианта схемы зависит от теоретической проработки задач каждого из этапов.

Рис. 1.1. Этапы разработки технологической схемы.
Подготовленность математического обеспечения позволяет на каждом из этапов выделить ряд подзадач, соответствующих отдельным вопросам исследуемого явления.
Рассмотрим круг вопросов, которые необходимо решить на каждом этапе при выборе высокоинтенсивных массообменных.

Рис. 1.2. Состав программно-математического обеспечения при разработке технологической схемы.
аппаратов и технологических схем разделения. На рис. 1.2 приведен состав математического обеспечения.
Выбор процесса среди возможных заключается в анализе условий его реализации на основе некоторого критерия, например минимума приведенных затрат. Решение этого вопроса возможно как экспериментальным, так и расчетным путем. Естественно, расчетный метод более дешев и быстр в реализации, однако это не исключает проведение экспериментальных исследований, объем которых может быть сведен до минимума.
Проведение расчетов отдельных аппаратов позволяет оценить практическую реализуемость способа разделения и определить конкурирующие способы. Естественно, этот этап должен проводиться при наличии требований на качество и количество целевых продуктов, а также необходимых сведений о предшествующих и последующих стадиях производства. Прямой перебор всех вариантов соединения аппаратов и условий их работы практически невозможен даже на современных вычислительных машинах, поэтому необходима стратегия поиска, эффективность которой зависит от степени изученности отдельных явлений.
Следует заметить, что этапу проектирования (выбора) технологической схемы предшествует этап конструирования высокоэффективного массообменного аппарата, который, в свою очередь, включает этап конструирования отдельного контактного устройства. Составными элементами этого этапа являются определение параметров математической модели гидродинамики всех типов контактных устройств, а также кинетики процесса массопередачи в зависимости от характера движения жидкости на тарелках колонны (прямоток, противоток и т. д.) и степени перемешивания парового (газового) потока — от идеального вытеснения до полного перемешивания.
Несмотря на специфику этого этапа, предусматривающего большую серию экспериментальных и теоретических исследований с широким привлечением методов математического моделирования, автоматизации экспериментальных исследований и т. д., в каждом конкретном случае удается сформулировать их в форме, доступной для использования на следующих этапах.
Ввиду единой цели выполнение всех этапов осуществляется итерационно с уточнением отдельных параметров.
Таким образом, от того, насколько достоверны модели отдельных элементов, зависит вероятность получения оптимального варианта технологической схемы.
Разнородность решаемых на каждом из этапов задач приводит к разнообразию моделей. Следует заметить, что на каждом из этапов возможны как различная постановка задачи, так и различное описание одного и того же объекта.
Например, для описания парожидкостного равновесия в зависимости от степени неидеальности жидкой фазы можно воспользоваться целым набором моделей, основанных на уравнениях Вильсона, NRTL, Маргулеса и т. д., а также предсказания парожидкостного равновесия с использованием параметров этих моделей. Выбор конкретной модели производится в зависимости от точности воспроизведения экспериментальных равновесных данных. Помимо различных способов описания отдельных явлений многие блоки представляют собой логически завершенный набор алгоритмов. Например, накопление равновесных данных производится после проверки экспериментальных данных на термодинамическую совместимость, выбора уравнения и определения параметров.