Изготовление зубчатых колес, материалы и точность
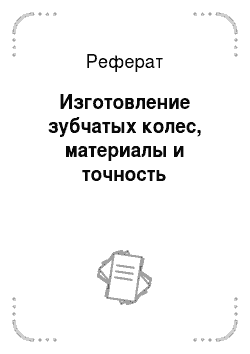
Изготовление зубчатых колес. Существует два метода нарезания зубьев: копирование и обкатка. Метод копирования заключается в прорезании впадин между зубьями модульными фрезами дисковыми (рис. 6.7, а) или пальцевыми (рис. 6.7, б). После прорезания каждой впадины заготовку поворачивают на шаг зацепления. Профиль впадины представляет собой копию профиля режущих кромок фрезы. Для нарезания зубчатых… Читать ещё >
Изготовление зубчатых колес, материалы и точность (реферат, курсовая, диплом, контрольная)
Изготовление зубчатых колес. Существует два метода нарезания зубьев: копирование и обкатка. Метод копирования заключается в прорезании впадин между зубьями модульными фрезами дисковыми (рис. 6.7, а) или пальцевыми (рис. 6.7, б). После прорезания каждой впадины заготовку поворачивают на шаг зацепления. Профиль впадины представляет собой копию профиля режущих кромок фрезы. Для нарезания зубчатых колес с разным числом зубьев необходим разный инструмент. Метод копирования малопроизводительный и менее точный, чем при обкатке. При шлифовании фрезу заменяют шлифовальным кругом соответствующего профиля. Метод обкатки основан на воспроизведении зацепления зубчатой пары, одним из элементов которой является режущий инструмент — червячная фреза (рис. 6.8, а), долбяк (рис. 6.8, б) или инструментальная рейка (гребенка) (рис. 6.8, в). При нарезании зуборезной гребенкой заготовка вращается вокруг своей оси, а инструментальная рейка 1 совершает возвратно-поступательное движение параллельно оси заготовки 2 и поступательное движение параллельно касательной к ободу заготовки. Гребенками нарезаются прямозубые и косозубые колеса с большим модулем зацепления. При нарезании червячной фрезой, имеющей в осевом сечении форму инструментальной рейки, заготовка и.

Рис. 6.7.
фреза вращаются вокруг своих осей, обеспечивая непрерывность процесса. Долбяк имеет форму шестерни с режущей кромкой. Он совершает возвратно-поступательное движение вдоль оси заготовки и вращается вместе с заготовкой. Фрезой и гребенкой нарезаются цилиндрические коле;

Рис. 6.8.
са с внешним расположением зубьев, для нарезания колес с внутренним и внешним расположением зубьев используются долбяки.
Материалы зубчатых колес. Если механическая обработка производится после термической, то твердость зубчатых колес должна быть НВ < 350. Такой материал используется в мелкомодульных передачах и в передачах с модулем т < 2. Для уменьшения размеров зубчатых колес (обычно при т > 2) необходимо упрочнить рабочую поверхность зуба, что увеличивает допускаемые контактные напряжения. Объемная закалка используется для сталей 40Х, 40ХН2МА и др. до HRC3 < 45. Такая закалка делает сердцевину менее пластичной, что способствует поломке зубьев. У современных зубчатых колес сохраняют вязкую сердцевину, а упрочняют лишь рабочую поверхность зуба термическими (поверхностная закалка ТВЧ), химико-термическими методами (цементацией и азотированием) и методом физического воздействия высоких энергий (лазерной закалкой, ионным азотированием) и др. При цементировании сталей 12ХНЗА, 18Х2НМА, 15ХФ твердость поверхности HRC3 = 56…62. При азотировании сталей 38Х2Ю, 38Х2МЮА твердость поверхности HRC3 = 50…55. При ионном азотировании твердость поверхностного слоя HRC3 = = 80…90. При лазерном упрочнении HRC3 = 56…60. При поверхностном упрочнении рабочей поверхности зуба масса редуктора снижается в 1,5…2 раза и соответственно уменьшаются его габариты и стоимость.
Точность зубчатой передачи. В стандарте предусмотрены степени точности зубчатых передач от 1 до 12 — от более точной к наименее точной. Наибольшее распространение имеют точности: 5 — высокая (о > 20 м/с), 6 — повышенная (до v = = 20 м/с), 7 — нормальная (до v = 12 м/с), 8 — пониженная (до v — 6 м/с), 9 — грубая (до и = 3 м/с). Значения наибольших допустимых скоростей и приведены для прямозубых передач, а для косозубых их необходимо увеличить примерно в 1,5 раза. При выборе степени точности также учитываются условия работы передачи и предъявляемые к ней требования.
Степень точности характеризуется следующими основными показателями:
- ? нормой кинематической точности колеса, устанавливающей величину полной погрешности угла поворота зубчатых колес за один оборот. Она является важным показателем для высокоточных и делительных механизмов;
- ? нормой плавности работы колеса, определяющей величину составляющих полной погрешности угла поворота зубчатых колес, многократно повторяющихся за один оборот колес. Она связана с неточностью изготовления по шагу и профилю и вызывает дополнительные динамические нагрузки в зацеплении;
- ? нормой контакта, характеризующей полноту прилегания боковых поверхностей сопряженных зубьев, оценивается пятном на рабочей поверхности зуба после контакта с вращающимся колесом, зубья которого смазаны краской. Степень точности должна соответствовать окружной скорости в зацеплении. Чем выше окружная скорость, тем выше должна быть точность передачи и ее элементов.

Боковой зазор между зубьями влияет на работу реверсивных передач (рис. 6.9, где IT: — допуск, /nmin, jn max — минимальный и максимальный боковой зазор). Он должен обеспечивать вращение колес и устранять заклинивание. Боковой зазор jn определяется видом сопряжения колес от, А до Н: наибольший зазор у сопряжения А, наименьший — у Н. У передач с модулем т > 1 установлены виды сопряжении А, В, С, Z), Еу Н. Обычно используется сопряжение В, а у реверсивных передач С. У мелкомодульных передач т < 1 применяются виды сопряжений Dy Еу Fy Gy Н. Чаще используются сопряжения Еу а при реверсе — F. Допускается использовать различные степени точности по отдельным показателям, например при т > 1 7—6—7—By а при одинаковых показателях 7—7—7—В записывают 7—Б.