Расчет режимов сборки соединений

Где / — максимальный (расчетный) натяг в соединении, мм; 5 — термический сборочный зазор, мм (0,01. .0,03 в зависимости от величины d и L); ка — коэффициент линейного расширения материала в 1/град: для стали — 11,0 • ю 6; для бронзы — 17,5 • 10 6; для алюминиевых сплавов — 23,82 • 10 6; 7о — температура окружающей среды, берется со знаком (+) при нагреве и (-) при охлаждении. По этой величине… Читать ещё >
Расчет режимов сборки соединений (реферат, курсовая, диплом, контрольная)
- 1. Выделить 2−3 гладких соединения с натягом (посадка подшипников на вал, посадка зубчатых колес па ват, запрессовка в корпус каких-либо деталей и т. п.).
- 2. Выбрать метод получения соединения: запрессовка под действием осевой силы или тепловой сборки (нагрев или охлаждение).
- 3. Рассчитать необходимое усилие запрессовки или температуру нагрева (охлаждения).
- 4. Выбрать наиболее ответственное резьбовое соединение и определить необходимый момент затяжки.
- 5. Изобразить в виде технологических эскизов эти операции (приложение 12, чертеж 3).
Методические указании
Прочность и относительная неподвижность соединений деталей с натягом обеспечивается силами трения, которые возникают пал действием давления" создаваемого натягом.
Сбо]жа под действием осевой силы. В процессе сборки к одной из двух деталей прикладывается осевая сила Р. Расчет силы запрессовки приведен в главе 4, значения модуля упругости и коэффициента Пуассона даны в табл. 11.1. При расчете усилия напрессовки подшипников студенты часто допускают ошибку, принимая за наружный диаметр напрессовываемой втулки (внутреннего кольца подшипника) наружный диаметр подшипника, а не диаметр дорожки качения внутреннего кольца.
Таблица 11.1.
Значения модулей упругости Е и коэффициента Пуассона ц для некоторых материалов.
Материал. | Е • 104МПа. | Р. |
Сталь. | 19,6… 20,6. | 0,3. |
Чугун. | 7,4… 10,5. | 0,25. |
Бронза. | 8,4. | 0,35. |
Латунь. | 7,8. | 0,38. |
Пластмасса. | 0,05…3,5. | 0,38. |
Сборка с термовоздействием производится путем нагрева охватывающей или охлаждения охватываемой детали. Температура нагрева (охлаждения) для получения теплового сборочного зазора б в соединении:
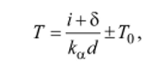
где / - максимальный (расчетный) натяг в соединении, мм; 5 — термический сборочный зазор, мм (0,01. .0,03 в зависимости от величины d и L); ка — коэффициент линейного расширения материала в 1/град: для стали — 11,0 • ю 6; для бронзы — 17,5 • 10 6; для алюминиевых сплавов — 23,82 • 10 6; 7о — температура окружающей среды, берется со знаком (+) при нагреве и (-) при охлаждении.
Постановка гаек. Момент затяжки резьбового соединения с метрической резьбой определяется по формуле.

где d — диаметр резьбы в мм; - поправочный коэффициент на материал болта.
Сталь. | А12. | 30, 35. | ||||||
0,66. | 0,77. | 0,88. | 0,88. | 0,92. | 1,0. | 1,15. | 1,2. |
По этой величине выбирается механизированный инструмент (пневмоили электровинтоверты). При ручной сборке длина гаечного ключа может быть принята равной в среднем 14d. Тоста усилие на рукоятке ключа.

оно не должно превышать 160 Н.
Для некоторых операций по согласованию с преподавателем должны быть представлены карты эскизов (3−4 шг.), на которых поясняется процесс сборки (запрессовки, свинчивания) либо контроля (зазор в зацеплении, радиальное биение), либо схема установки или строповки тяжелых деталей (с.е.). На эскизах процесс сборки изображается в конце перехода. Конструктивно показываются инструмент и установочные элементы приспособления, непосредственно контактирующие с поверхностями соединяемых деталей (см. приложение 12).
Содержание отчета.
- 1. Эскизы соединений (2−3 шт.) с указанием размеров, выдерживаемых при сборке, схемы установки деталей с изображением конструктивных элементов приспособлений.
- 2. Расчет параметров режимов операции (усилия запрессовки, температуры нагрева, момента затяжки). Выводы по допустимости рассчитанных режимов.
Контрольные вопросы
- 1. За счет чего обеспечивается прочность соединения деталей с натягом?
- 2. В чем достоинства и недостатки получения соединений с натягом методом на прессовки (запрессовки) и методом нагрева (охлаждения)?
- 3. Чем ограничивается применение метода напрсссовки (запрессовки) и метода нагрева (охлаждения)?
- 4. Какие требования существуют по выполнению операций напрсссовки (запрессовки)?
- 5. Как выполняются операции сборки с применением нагрева (охлаждения)?