Технология сварки углеродистых и низко-и среднелегированных закаливающихся сталей

Наряду с потерей пластичности металлом околошовной зоны из-за резкой подкалки или чрезмерного роста зерна на образование холодных трещин при сварке закаливающихся, особенно среднелегированных высокопрочных сталей, оказывает попадающий в металл водород. Поэтому для сталей рассматриваемого типа при сварке необходимо принимать меры по предупреждению попадания водорода в зону сварки. Для этого… Читать ещё >
Технология сварки углеродистых и низко-и среднелегированных закаливающихся сталей (реферат, курсовая, диплом, контрольная)
Состав и свойства сталей, основные сведения о свариваемости
Для изготовления различных изделий в машиностроении используют также углеродистые и низколегированные стали, содержание углерода в которых увеличено по сравнению с его содержанием в низкоуглеродистых и низколегированных конструкционных сталях общего назначения. Эти конструкционные машиностроительные стали применяют, как правило, после закалки с отпуском и реже в нормализованном состоянии. В зависимости от режима термообработки временное сопротивление этих сталей составляет 600… 1500 МПа. Содержание углерода в них равно 0,25…0,5% при суммарном легировании до 3…4%. Примерами марок низколегированных сталей этой группы могут служить 35Х, 40Х, 35Г2, 40Г2, 50Г2, 30ХГТ, 30ХГНА, 30ХГСА и другие. По чувствительности к термодеформационному циклу сварки к этой же группе можно отнести углеродистые стали марок 30, 35, 40, 45, 50 и другие, а также низколегированные теплоустойчивые хромомолибденовыс и хромомолибдснованадисвыс стали, которые длительное время сохраняют высокие прочностные свойства при работе в условиях повышенных температур (450…600 °С), оцениваемые пределом ползучести и длительной прочности. Примерами их могут быть хромомолибденовые стали 12МХ, 12ХМ, 15ХМ, предназначенные для работы при.
450. .550°С, и хромомолибденованадиевые — 12Х1МФ, 20ХМФЛ, 15Х1М1ФЛ и др., предназначенные для работы при 550…600 °С. Эти стали используют в основном в энергетическом, химическом и нефтехимическом машиностроении. Так, например, литейные стали 20ХМФЛ и 15Х1М1ФЛ применяют для отливки корпусов турбин и запорной арматуры, а деформируемые стали 12МХ, 15ХМ, 12Х1МФ, 15Х1М1Ф — для изготовления корпусов аппаратов, технологических трубопроводов, паропроводов и поверхностей нагрева котлов.
Для изготовления сосудов высокого давления, тяжело нагруженных машиностроительных изделий и других ответственных конструкций используют среднелегированные высокопрочные стали, которые после соответствующей термической обработки (закалки с отпуском) обладают временным сопротивлением 1000…2000 МПа при достаточно высоком уровне пластичности. Для сталей этой группы характерно содержание углерода до 0,5% при комплексном легировании в сумме.
5.. 10%. Примерами этой группы сталей могут быть стали марок ЗОХГСНА, ЗОХ2ГСНВМА, 42Х2ГСНМА, 40ХГСНЗМА, ЗЗХЗНВФМА, 43ХЗСНВФМА и др. Кроме названной группы сталей, в промышленности все более широкое применение находят стали с таким же уровнем прочности, но со значительно меньшим содержанием углерода (0,12…0,17%), что существенно улучшает их свариваемость.
Среднеуглеродистые низкои среднелегированные стали для сварных конструкций, в основном, относятся к перлитному классу. Однако некоторые стали этой группы, содержащие 5…6% и более легирующих элементов, относятся к мартенситному классу.
Свариваемость закаливающихся сталей. Основными причинами, снижающими свариваемость среднеуглеродистых низкои среднелегированных сталей, являются:
- 1) высокая склонность к образованию холодных трещин из-за повышенного содержания углерода, легирующих элементов и воздействия водорода;
- 2) трудность получения равнопрочных сварных соединений;
- 3) пониженная стойкость металла шва к образованию кристаллизационных трещин, обусловленная повышенным содержанием углерода и воздействием серы.
Методы предупреждения возникновения кристаллизационных трещин в металле шва при сварке этой группы сталей мало отличаются от применяющихся при сварке углеродистых сталей. Для этого часто идут по пути некоторого ограничения содержания в шве углерода и кремния, уменьшающих стойкость металла шва против кристаллизационных трещин, и замены их такими элементами, как марганец, хром, молибден, ванадий и др., увеличивающих эту стойкость. При этом вместе с тщательным выбором композиции шва осуществляют его рафинирование и модификацию. Одновременно используют и технологические меры, применяя режимы, обеспечивающие высокий коэффициент формы провара, а также меры по снижению темпа нарастания сварочных деформаций.
Получение равнопрочных сварных соединений из высокопрочных низкои среднелегированных сталей — не менее важная проблема их свариваемости. Трудность получения металла шва, околошовной зоны и сварного соединения в целом с механическими свойствами, равноценными или близкими к свойствам основного металла, обусловлена высокими механическими свойствами этих сталей и высокой чувствительностью к сварочному термическому циклу.
Общая схема изменения свойств металла сварного соединения в случае сварки закаливающихся сталей изображена на рис. 2. Сварное соединение включает следующие зоны и участки: 1 — сварной шов, 2 ;
участок закалки, 3 — участок неполной (частичной) закалки, 4 и 5 — участки отпуска и разупрочнения, 6 — основной металл. В сталях этого типа участок основного металла 2, нагревающийся при сварке выше температуры точки Ас3, в результате последующего достаточно быстрого охлаждения приобретает структуру закалки. В зависимости от состава стали, условий охлаждения металла конечная структура этого участка может быть получена либо полностью мартенситной, либо смешанной с тем или иным количеством более стабильных продуктов распада аустенита. Причем в этом случае структура участка от границы сплавления до температуры точки Ас3 будет неодинаковой. Распад перегретого аустенита (т. е. участка металла, прилегающего к границе сплавления и нагревавшегося при сварке выше 1100°С) приводит к образованию более крупнозернистого, крупноигольчатого мартенсита, чем на участке металла, нагревавшегося при сварке только несколько выше температуры точки Асу При этом, чем выше содержание углерода в стали, тем выше степень тстрагональности решетки мартенсита и выше его твердость, вместо пакетного дислокационного мартенсита образуется двойниковый пластинчатый мартенсит, который более склонен к образованию холодных трещин, чем пакетный. Структура зоны сплавления в связи с тем, что ее состав весьма близок к составу основного металла, является почти такой же, как структура участка перегрева.

Рис. 2. Схема изменения свойств сварного соединения закаливающейся стали:
I — исходный материал в состоянии после высокого отпуска:
II — то же после низкого отпуска; III — то же после закалки
Участок зоны термического влияния 5, который при сварке нагревался до максимальных температур между точками Ас и Ас$, после охлаждения получает структуру частичной закалки. Поэтому твердость металла этого участка снижается по мере уменьшения максимальной температуры нагрева.
Структура рассмотренных участков 2 и 3 зоны термического влияния практически не зависит от исходного состояния металла перед сваркой. В то же время участки 4 и 5 зоны, нагревавшиеся до максимальной температуры ниже точки АС> по своей структуре и свойствам могут быть различными для металла, поступившего на сварку в закаленном, высокоили низкоотпущенном состояниях. Для металла, находящегося в закаленном исходном состоянии, участки 4 и 5 получат отпуск при различных температурах и выдержках. Так, участок, прилегающий к участку частичной закалки, получит кратковременный высокий отпуск. Он обычно характеризуется структурой сорбита отпуска. По мере удаления от участка частичной закалки температура отпуска снижается и уменьшается общая продолжительность выдержки при повышенных температурах. Поэтому степень отпуска закаленного металла снижается и твердость сохраняется повышенной, в итоге в структуре исчезает сорбит отпуска и остается мартенсит. Этот участок ограничивается областью максимальной температуры 200…250 °С.
Для закаленного и отпущенного перед сваркой металла нижняя граница изменения структуры и свойств практически определяется температурой предварительного отпуска. В области, где металл при сварке нагревался ниже температуры отпуска, никаких изменений свойств не происходит. В области, нагревавшейся выше этой температуры, изменение структуры и свойств подобно рассмотренному для закаленного металла.
Обеспечить равнопрочность и высокую работоспособность сварных соединений при сварке закаливающихся сталей без последующей полной термической обработки достаточно сложно. Прочность сварного соединения, нс подвергнутого термической обработке после сварки, зависит от того, насколько изменяется структура и прочность основного металла в зоне термического влияния и металла шва под влиянием нафева при сварке. Наименее прочной при этом является зона высокого отпуска. Прочность металла в этой зоне и се ширина зависят от марки стали и применяемой технологии сварки. Чем более теплоустойчивая сталь и меньше тспловложснис при сварке, тем уже участок разупрочнения металла и меньше степень его разупрочнения.
Прочность в зоне закалки определяется нс столько пределом прочности, сколько пластическими и вязкими ее свойствами, чувствигельностыо металла к хрупкому разрушению. Среднеуглеродистые низкои среднелегированные стали в связи с повышенным содержанием углерода, а также увеличенной степенью легирования обладают высокой чувствительностью к термическому циклу сварки. Поэтому при режимах сварки, обеспечивающих удовлетворительное формирование шва, в околошовной зоне, как правило, образуются хрупкие закалочные структуры, которые в условиях сложнонапряженного состояния часто приводят к образованию холодных трещин. Для их исключения усложняют технологию сварки закаливающихся сталей. Наиболее простой и эффективный способ повышения стойкости сварных соединений против образования холодных трещин заключается в регулировании сварочного термического цикла путем выбора соответствующих способов и режимов сварки, а также использования в необходимых случаях предварительного или сопутствующего подогрева.
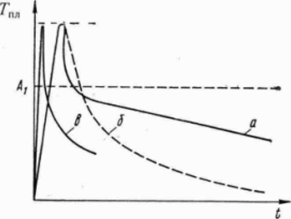
Рис. 3. Сварочные термические циклы: а — идеальный: б — при электродуговой сварке: в — при электронно-лучевой сварке.
Для многих марок закаливающихся сталей определение оптимальных режимов позволяет резко повысить стойкость сварных соединений против образования холодных трещин и в ряде случаев полностью устранить их возникновение. Идеальный термический цикл, обеспечивающий наиболее высокую стойкость сварного соединения против образования холодных трещин, приведен на рис. 3. Однако практическое осуществление циклов, близких к идеальному, при дуговой сварке сопряжено с применением весьма малопроизводительных режимов, предварительного, сопутствующего и последующего подогревов. Осуществление идеального цикла требует больших затрат груда и средств. При электрошлаковой сварке этот цикл вовсе неосуществим. Поэтому изыскивают более производительные и менее дорогие методы борьбы с холодными трещинами, чем получение идеального сварочного термического цикла.
Так, например, в случае сварки сравнительно низколегированных сталей типа 34ХМ и др. наиболее просто и экономично можно исключить образование в сварных соединениях холодных трещин повышением погонной энергии сварки qlv. При этом замедление охлаждения сварного соединения ниже точки А сопровождается смещением превращения переохлажденного аустенита в область высоких температур, что приводит к образованию структуры металла, не склонной к образованию холодных трещин. Для сталей этого типа благоприятное влияние изменений в ходе превращения переохлажденного аустенита преобладает над отрицательным влиянием, обусловленным развитием перегрева в околошовной зоне при повышении погонной энергии.
Если же стойкость сварных соединений против образования холодных трещин настолько низка, что избежать их появления путем соответствующего выбора режима сварки не удается, в отдельных случаях прибегают к регулированию термического цикла путем предварительного и сопутствующих подогревов свариваемых кромок. Особо высокую стойкость против образования холодных трещин можно получить, применяя предварительный подогрев до температуры 200…300 °С и режимы сварки с низкой погонной энергией. Соблюдение этих условий приближает реальный термический цикл сварки к идеальному. Однако для большинства широко применяемых среднеуглеродистых низкои среднелегированных сталей даже большой толщины достаточную стойкость против образования холодных трещин можно получить при использовании подогрева до температуры 150…200°С и умеренных режимов сварки. В ряде случаев при сварке металла средних и больших толщин образование холодных трещин можно предотвратить путем разофева области шва до температуры 100… 150 °C в процессе многослойной сварки с минимальными перерывами между наложением слоев.
Для низкоуглеродистых среднелегированных сталей при сварке в широком диапазоне режимов характерно превращение в области нижнего бейнита, а затем мартенсита. Поэтому при их сварке для предотвращения образования холодных трещин рекомендуется умеренный подогрев до температуры 100… 150 °C, не вызывающий существенного возрастания времени пребывания металла зоны при температурах перегрева, но обеспечивающий требуемую скорость охлаждения а)&$ для бейнитного превращения при возможно более высоких температурах.
Для среднеуглеродистых среднелегированных сталей, содержащих карбидообразующие элементы, при сварке в широком диапазоне режимов характерно мартенситное превращение. Для этих сталей важным являются значения времени пребывания металла зоны при температурах перегрева, поскольку гомогенизация аустенита и рост зерна в связи с наличием специальных карбидов в исходной структуре замедлены и их можно регулировать с помощью режима сварки. Поэтому для получения благоприятной структуры при сварке этих сталей эффективно снижение q!v путем применения методов сварки с высокой концентрацией энергии (плазменной, электронно-лучевой и лазерной) или перехода на многослойную электродуговую сварку короткими участками.

Рис. 4. Термический цикл точек околошовной зоны при многослойной сварке коротыши участками: а — термический цикл точки 1:6- термический цикл точки 2
Особенность термического цикла многослойной сварки короткими участками состоит в том, что тепловые воздействия последовательно навариваемых коротких слоев складываются и замедляют скорость охлаждения отдельного слоя, образуя сложный термический цикл (рис. 4). Так, теплота второго и последующих заполняющих слоев шва не позволяет металлу околошовной зоны первого корневого слоя шва охладиться ниже определенной температуры. При сварке корневого слоя шва температура точки 1 околошовной зоны резко возрастает, превышая температуру точки Ас^, а затем резко падает (см. рис. 4, а). В момент, когда температура в точке 1 понизится до допустимого значения ТН(ТН> М — точки начала мартенситного превращения), тепловая волна от наложения второго слоя осуществит повторный нагрев металла околошовной зоны в этой точке, но до температуры более низкой, чем при сварке первого слоя. При сварке последующих слоев снова происходит некоторый подогрев, причем по мере их выполнения температурные воздействия ослабевают и процесс стремится к установившемуся температурному состоянию. По окончании процесса сварки металл околошовной зоны медленно охлаждается. При этом длительность /в пребывания металла околошовной зоны выше температуры Гв соответствует условиям завершения распада аустенита.
На рис. 4, б показано изменение температуры в точке 2, находящейся у поверхности листов. При выполнении каждого последующего слоя температура в точке 2 нарастает. При выполнении последнего слоя достигает максимума с превышением температуры точки Ас$ и после этого начинает снижаться. По прошествии /в (времени пребывания металла в интервале температур Ас$…М) температура точки 2 снижается до температуры мартенситного превращения и, если за это время не успеет произойти распад аустенита, то образуется мартенситная структура.
Для увеличения времени пребывания металла околошовной зоны при температуре выше точки М начала мартенситного превращения накладывают так называемый отжигающий валик, границы которого уже границ металла шва и тем самым не нагревают подверженный закалке металл околошовной зоны до температуры выше точки Ас$. Наплавка отжигающего валика увеличивает время пребывания металла околошовной зоны в субкритичсском интервале температур с /вдо t.
Режим многослойной сварки короткими участками характеризуется в основном двумя независимыми параметрами — погонной энергией qlv (сечением слоя) и длиной / участка, поэтому он более гибок, чем режим однопроходной сварки.
Длину свариваемого участка выбирают из условия, чтобы температура Тн околошовной зоны корневого слоя шва к моменту наложения тепловой волны следующего слоя не падала ниже точки М начала мартенситного превращения (200…350 °С) или ниже температуры, при которой наиболее вероятно образование холодных трещин (60… 150 °С).
Наряду с потерей пластичности металлом околошовной зоны из-за резкой подкалки или чрезмерного роста зерна на образование холодных трещин при сварке закаливающихся, особенно среднелегированных высокопрочных сталей, оказывает попадающий в металл водород. Поэтому для сталей рассматриваемого типа при сварке необходимо принимать меры по предупреждению попадания водорода в зону сварки. Для этого следует использовать низководородистыс сварочные материалы, высокотемпературную их прокалку, тщательно зачищать свариваемые кромки и присадочный металл от ржавчины, масел и других загрязнений. Целесообразна также термическая обработка после сварки, чаще всего высокий отпуск, позволяющий одновременно привести к распаду мартенсита, к полному снижению сварочных напряжений и к выходу водорода из сварного соединения. Во всех случаях термическую обработку сварных соединений, выполненных из среднеуглеродистых легированных сталей, следует производить своевременно, т. е. в период от окончания сварки до возможного появления холодных трещин. В зависимости от состава стали, типа соединения, технологии сварки и других факторов этот период может длиться от нескольких минут до десятка часов.
При сварке термоулучшенных среднеуглеродистых легированных сталей еще в большей мере, чем при сварке термоулучшенных низкоуглеродистых сталей, происходит разупрочнение участков зоны термического влияния. Устранить его может только общая термическая обработка всего сварного изделия (закалка и отпуск). Общий или местный отпуск, естественно, не повышает прочности разупрочненной зоны.
При изготовлении из среднелегированных сталей особо ответственных конструкций, для которых последующая термическая обработка недопустима, выполняют сварные соединения по варианту, при котором обеспечивают получение металла шва с аустенитной структурой, а для равнопрочности с основным металлом увеличивают сечение шва. При этом сварку выполняют без предварительного и сопутствующего подогревов. В этом случае металл шва, отличаясь по химическому составу от основного металла, обладает очень высокой пластичностью и вязкостью и сохраняет высокую деформационную способность как при низкой температуре, так и при ударном приложении нагрузки. Наряду с большой деформационной способностью таких швов наблюдается повышенная стойкость околошовной зоны к образованию холодных трещин, в особенности типа отколов.
Выбор технологических условий сварки среднеуглеродистых низкои срсднслсгированных сталей зависит от многих параметров: состава стали, жесткости конструкции, толщины свариваемого металла, температуры окружающего воздуха и т. п. Поэтому в каждом конкретном случае выбирают и технологические условия их сварки. Стали рассматриваемой группы относятся к наиболее трудносваривасмым.