Слои материалов и диэлектриков
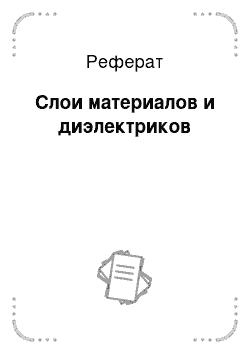
Основным методом получения тонких слоев металлов и диэлектриков служит нанесение их в вакууме. В основе метода лежат испарение материала при разогреве и последующая конденсация паров на подложке. Технологический процесс требует создания в рабочей камере разряжения и определенного состава среды. В самом процессе выделяют три фазы: образование потока вещества из испарителя, формирование потока… Читать ещё >
Слои материалов и диэлектриков (реферат, курсовая, диплом, контрольная)
Основным методом получения тонких слоев металлов и диэлектриков служит нанесение их в вакууме. В основе метода лежат испарение материала при разогреве и последующая конденсация паров на подложке. Технологический процесс требует создания в рабочей камере разряжения и определенного состава среды. В самом процессе выделяют три фазы: образование потока вещества из испарителя, формирование потока в пространстве «испаритель-подложка» и конденсация паров на подложке.
Можно выделить три обоснованных метода, используемых для получения слоев (рис. 1.5): термовакуумное нанесение, катодное распыление, ионно-плазменное распыление.
При термовакуумном распылении наносимое вещество испаряется с помощью резистивного нагрева или электронного луча. Давление в рабочей камере в этом случае должно быть.

Рис. 1.5. Методы нанесения слоев:
а — термовакуумное нанесение; б — катодное распыление; в — ионно-плазменное распыление на несколько порядков ниже, чем парциальное давление паров испаряемого вещества. Поток паров — атомарный и проходит без соударений, т. е. расстояние «испаритель—подложка» меньше длины свободного пробега. Это определяет требования к высокому вакууму в рабочем объеме под колпаком установки. Для обеспечения конденсации подложка должна иметь определенную температуру.
При этом методе (рис. 1.5, а) под колпаком 1 размещаются нагреватель подложки 2, подложкодержатель 3 с подложками 4. Для нанесения слоев одинаковой толщины на все подложки подложкодержатель приводится во вращение специальным приводом, размещаемым обычно вне рабочей камеры.
Время, в течение которого может наноситься слой, определяется положением заслонки 5. Заслонка также защищает поверхность пластины от попадания посторонних примесей при прогреве камеры для дегазации. Для предохранения внутренней поверхности колпака от запыления применяются экраны 6. Испаряемое вещество помещается в испаритель 7. Испаритель может быть выполнен в виде тигля, лодочки из тугоплавкого металла или керамики или представляет собой спираль, на которую навешаны частицы испаряемого вещества.
Плита 8 служит для установки всех устройств, через ее уплотненные вводы приводятся в движение механизмы подколпачных устройств и подается электропитание. Плита имеет отверстие для соединения с вакуумной системой.
Катодное распыление проводится при низком вакууме (0,66—1,133 Па) в среде нейтрального газа. Распыление вещества происходит иод действием бомбардировки катода ионизированными молекулами газа.
Для выполнения операции (рис. 1.5, б) в рабочей камере 1 имеются анод 2 и подложкодержатель 3 с подложками 4. Время нанесения пленки отсчитывается с момента открытия заслонки 5. Испаряемым является материал катода 6 или вещество, помещаемое на его поверхность. Катод прикрыт экраном 7. Давление в камере во время технологического процесса стабилизируется за счет управляемого натекания через игольчатый натекатель 8. Вакуумная система установки при этом работает непрерывно.
Ионно-плазменное распыление проводится при давлении 0,13—0,07 Па. В камере 1 (рис. 1.5, в) установлен подогреватель подложек 2, рядом с которым находится подложкодержатель 3 с подложками 4. Источник ионов 5 и анод 6 создают в камере ионизированную плазму 7. Отрицательный потенциал, подаваемый на мишень 8, вытягивает из плазмы ионы, которые, бомбардируя мишень, распыляют ее. Давление в камере регулируется игольчатым натекателем 9.
Достоинства методов катодного и ионно-плазменного нанесения слоев заключаются в их высокой производительности, хорошей воспроизводимости получаемых слоев и универсальности. Недостатком методов является проведение процессов в низком вакууме, что не позволяет получать слои с особо чистым составом.
Большим недостатком вакуумных установок является значительное время откачки рабочего объема, поэтому в последние годы стремятся получить установки непрерывного действия за счет создания шлюзовых камер для загрузки и выгрузки.
Слои оксида.
Слои диоксида кремния используются в ИМС для изоляции при многослойной разводке, защиты поверхности кристалла и маскирования в литографии. Наиболее распространенным способом является получение оксида с помощью термического окисления, выполняемого в диффузионных печах. В этом случае окисление кремния проводится путем пропускания через кварцевую трубу сухого или влажного кислорода в течение заданного времени.
Кроме термического окисления применяется пиролитическое осаждение. Этот процесс проводится при более низких температурах и использует реакцию между силаном и кислородом на поверхности пластины.
Возможно применение катодного и ионно-плазменного распыления кремния в смеси кислорода и аргона. Выбор метода нанесения определяется назначением слоя и совместимостью процесса с другими технологическими операциями.