Химико-термическая обработка (ХТО)
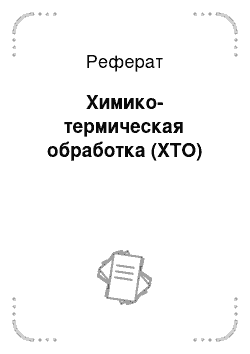
Борирование — насыщение поверхностного слоя деталей бором. Слой состоит из боридов FeB и Fe2B, толщина слоя 0,1—0,2 мм. Процесс проводят в газовой среде, расплавленных солях или электролизом буры Na2B407. Температура 850—950 °С, время выдержки — 2—6 часов. При борировании повышается износостойкость (до 10 раз), окалиностойкость, теплостойкость, коррозионная стойкость. Применяют для деталей… Читать ещё >
Химико-термическая обработка (ХТО) (реферат, курсовая, диплом, контрольная)
ХТО — совокупность технологических процессов, приводящих к изменению химического состава, структуры и металла без изменения состава, структуры и свойств его сердцевидных зон. Осуществляют ХТО с помощью диффузионного насыщения поверхности различными элементами при повышенных температурах. Под общей толщиной диффузионного слоя понимают кратчайшее расстояние от поверхности насыщения до слоя со структурой сердцевины изделия. Выбор элемента (или комплекса элементов) определяется требуемыми свойствами поверхности детали.
При ХТО одновременно протекают несколько процессов:
• образование активных атомов насыщающего элемента за счет диссоциации насыщающей среды (твердой, жидкой, газообразной). Например, диссоциация аммиака: 2NH3 —?
ЗН2 + 2NaT0M;
- • адсорбция активных атомов с образованием связей между ионами насыщающего элемента и основного металла (хемосорбция);
- • диффузия адсорбированных атомов вглубь металла с образованием диффузионного слоя.
Толщина образовавшегося диффузионного слоя х зависит от растворимости насыщающего элемента в материале, температуры нагрева и времени выдержки (рис. 8.23, а, б) при этой температуре, а также концентрации атомов насыщающего элемента на поверхности (рис. 8.23, в).
Структура диффузионного слоя образуется в той же последовательности, что и расположение однофазных облас;

Рис. 8.23. Изменение толщины диффузионного слоя ог продолжительности насыщения (а), температуры (6) и изменение концентрации по толщине диффузионного слоя (в).
х — толщина слоя; т — время; t — температура; c'0t с? — концентрация диффундирующего элемента на поверхности металла (с'0 < с?)
тей на двойной диаграмме металл — насыщающий элемент при данной температуре.
При температуре tx (рис. 8.24, а) существует только а-твердый раствор и концентрация легирующего компонента уменьшается по глубине. Насыщение при t2 сопровождается фазовой перекристаллизацией у —? а и зародыши а-фазы растут от поверхности по направлению диффузии, образуя.

Рис. 8.24. Схема диаграммы состояния железо — диффундирующий элемент (а); изменение концентрации диффундирующего элемента по толщине диффузионного слоя и строение диффузионного слоя по толщине (6):
а — фаза; у — фаза; Л3, Л4 — критические точки; tt, t2 — температуры насыщения; х — расстояние от поверхности; Л — пограничная линия столбчатые кристаллы. На границе раздела фаз у и, а устанавливается перепад концентрации и в микроструктуре появляется пограничная диффузионная линия Л (рис. 8.24, в).
Расстояние от поверхности до участка слоя с заданными параметрами (концентрация насыщающего элемента, твердость или другие характеристики) называется эффективной толщиной диффузионного слоя.
ХТО повышает твердость, износостойкость, предел выносливости, кавитационную и коррозионную стойкость, увеличивает надежность и долговечность изделия. К ХТО относятся в первую очередь цементация, нитроцементация, борирование.
Цементация — диффузионное насыщение поверхностных слоев низкоуглеродистых сталей (цементуемые стали) углеродом при нагреве в соответствующей среде — карбюризаторе (от франц. carburer— обогащать углеродом). В зависимости от применяемого карбюризатора различают два вида обработки — насыщение в твердой и газообразной средах.
Цементацию в твердом карбюризаторе используют в мелкосерийном производстве. Насыщающая среда (карбюризатор) — древесный уголь или торфяной кокс с добавками активизаторов процесса ВаС03 и Na2C03 (СаСО,), которые способствуют образованию атомарного углерода Сат и последующему его переходу в твердый раствор [С]р:

На поверхности образуется слой с повышенным содержанием углерода.
Цементация в газовом карбюризаторе проводится в среде газов, содержащих углерод. Карбюризатор — природный газ (метан) с добавками керосина и бензина. Температура процесса — 910—930 °С, время выдержки — 6—10 ч.
Реакции при насыщении:

Преимущества газовой цементации:[1]
- 2) поддерживается заданное количество углерода (углеродный потенциал) в среде, а следовательно, в слое;
- 3) ускорение процесса за счет проведения последующей термической обработки непосредственно после цементационного нагрева;
- 4) из-за небольшой продолжительности процесса рост зерна меньше, структура после обработки дисперснее.
Процесс газовой цементации используют в массовом производстве деталей, работающих при трении поверхности. После цементации обязательно проводится термическая обработка для получения заданных свойств цементованного слоя и сердцевины изделия. Цементованное изделие после термической обработки имеет поверхностный слой толщиной 0,1—0,7 мм со структурой мартенсита отпуска с включениями глобулярных карбидов; сердцевина, в зависимости от химического состава стали, может иметь структуру сорбита, троостита или даже низкоуглеродистого мартенсита. Твердость поверхности HRC 58—62, сердцевины — HRC 38−42.
Термическая обработка цементованных изделий:
- • закалка прямо с температуры цементации или с подстуживанием с последующим низким отпуском — для деталей из наследственно-мелкозернистых сталей, у которых требуется только высокая твердость поверхности;
- • охлаждение на воздухе после цементации, затем закалка от 850—900 °С и низкий отпуск для деталей из наследственно-крупнозернистых сталей с повышенными требованиями к свойствам детали;
- • двойная закалка и последующий низкий отпуск для измельчения структуры цементованного слоя и сердцевины.
Азотирование стали — процесс диффузионного насыщения поверхностных слоев стали азотом для повышения износостойкости, твердости, предела выносливости, коррозионной стойкости поверхности. Твердость азотированного слоя — IIV1000—1200 сохраняется при работе до 500—600 °С.
Азотирование — окончательная обработка изделия. Перед азотированием проводят закалку с высоким отпуском для упрочнения сердцевины изделия и получения структуры сорбита отпуска, а также механическую обработку для получения окончательных размеров детали.
Азотированию в герметических камерах, куда с определенной скоростью подается аммиак, подвергаются углеродистые стали (0,4% С) и стали, легированные элементами, образующими нитриды (Al, Mo, V, Ti, Сг, Мп). Охлаждение с печью в потоке аммиака.
Структура азотированного слоя определяется диаграммой Fe — N и при рабочих температурах 500—650 °С возможно образование в слое следующих фаз: е (нитрид Fe2N переменного состава); у' — нитрид Fe.^N переменного состава; а — азотистый феррит. Формирование азотированного слоя приводит к увеличению удельного объема и возникновению остаточных сжимающих напряжений, повышающих, а ,.
Разновидности процесса азотирования:
- • ионное азотирование (в тлеющем разряде) — между катодом (деталью) и анодом (установкой) в среде газа возбуждается тлеющий разряд. Происходит ионизация азотосодержащего газа, и ионы азота, бомбардируя поверхность катода, нагревают его до температуры насыщения и диффундируют в глубину слоя. Преимущество — ускорение процесса при температуре 470—580 °С и давлении 1,3 • 102— 13−102 Па;
- • азотирование в жидких средах (тенифер — процесс) проводя ! при 570 °C в течение 0,5—30 часов в жидкой среде расплавленных цианистых солей — 40% KCNO, 60% NaCN + + 15% (NFI2)2C03, 45% Na2C03, через которую пропускают сухой воздух. Соли расплавляют в тигле из титана, из-за низкой температуры в сталь диффундирует в основном азот; общая толщина карбонитридного слоя — 150—500 мкм;
- • нитроцементация — одновременное насыщение поверхностных слоев стального изделия азотом и углеродом, осуществляется в газовой среде смесью науглероживающего газа и аммиака при температуре 830—870 °С, с последующей закалкой и низким отпуском. Структура поверхностного слоя толщиной 0,2—0,8 мм — мелкокристаллический мартенсит, карбонитриды и аустенит остаточный, HRC 56—62.
Применяется вместо газовой цементации, имеет преимущества: более низкая температура процесса, мельче зерно, меньше коробление, выше сопротивление износу, но стоимость процесса выше. Обычно процесс рекомендуют для деталей сложной конфигурации, которые склонны к короблению;
• цианирование (одновременное насыщение поверхностных слоев стального изделия азотом и углеродом) проводят в расплавленных солях (NaCN, NaCl, ВаС12), содержащих группу CN при температуре 820—950 °С. После цианирования проводят закалку с низким отпуском.
Реакции с выделением атомарного азота и углерода:

Низкотемпературное цианирование (при 570 °C, выдержка до 3 часов) приводит к существенному повышению предела выносливости и коррозионной стойкости, твердости. Применяется для инструмента из быстрорежущих и штамповых сталей для повышения износостойкости.
Недостатком цианирования является токсичность процесса, что требует принятия специальных мер защиты.
Другие виды химико-термической обработки стальных изделий.
Борирование — насыщение поверхностного слоя деталей бором. Слой состоит из боридов FeB и Fe2B, толщина слоя 0,1—0,2 мм. Процесс проводят в газовой среде, расплавленных солях или электролизом буры Na2B407. Температура 850—950 °С, время выдержки — 2—6 часов. При борировании повышается износостойкость (до 10 раз), окалиностойкость, теплостойкость, коррозионная стойкость. Применяют для деталей, работающих на износ, штампов, деталей пресс-форм и машин литья под давлением.
Цель диффузионного насыщения металлами {металлизация) — повышение коррозионной стойкости, жаростойкости деталей машин. Диффузионная металлизация может проводиться в твердых, жидких или газообразных средах при повышенных температурах.
Силицирование — насыщение поверхностных слоев кремнием. Структура слоя — a-твердый раствор кремния в Fe (a). Толщина слоя 0,3—0,5 мм. При этом происходит повышение коррозионной стойкости поверхности изделия.
Хромирование — насыщение поверхностных слоев хромом. Структура слоя — a-твердый раствор хрома в а-железе и карбиды (Fe, Cr)7C3, (Fe, Сг)23С6. Толщина слоя 0,1—0,2 мм. Применяется для повышения коррозионной стойкости, износостойкости поверхности изделия.
Алитирование — насыщение поверхностных слоев алюминием, проводится при температуре 800—1000 °С. Структура слоя — a-твердый раствор алюминия в Fe (a) и слой А1203. Толщина слоя 0,2—0,5 мм. Главная цель — повышение коррозионной стойкости за счет слоя А1203.
Цинкование — насыщение поверхностных слоев цинком. Применяется для повышения коррозионной стойкости полуфабрикатов и специальных деталей холодильников, компрессоров и др.
- [1] возможность автоматизации и механизации процесса;