Светолучевая обработка.
Технологические процессы в машиностроении

Светолучевая обработка основана на воздействии на поверхность заготовки сфокусированного электромагнитного излучения (света), энергия которого, преобразуясь в рабочей зоне в теплоту, вызывает нагрев, плавление, испарение и ионизацию паров обрабатываемого материала. Фокус луча; 2 — форсунка; 3 — плавающий стакан; 4 — линзы; 5 — микрометр; 6' — лазерный луч; 7 — впуск газа; 8 — деталь; 9 — брусок… Читать ещё >
Светолучевая обработка. Технологические процессы в машиностроении (реферат, курсовая, диплом, контрольная)
Светолучевая обработка основана на воздействии на поверхность заготовки сфокусированного электромагнитного излучения (света), энергия которого, преобразуясь в рабочей зоне в теплоту, вызывает нагрев, плавление, испарение и ионизацию паров обрабатываемого материала.
Применение света для обработки стало возможным после создания оптических квантовых генераторов — лазеров. Рабочий диапазон длин волн производственных лазеров — 0,3−300 мкм, плотность потока энергии Р ~10'6 Вт/м2 не имеет равных среди других видов лучевой обработки. С помощью лазера осуществляют следующие процессы: размерную обработку, резку, закалку, наплавку, легирование, сварку.
Существуют твердотелые, газовые и полупроводниковые лазеры. Для механической обработки используют твердотелые лазеры, рабочим элементом которых является рубиновый стержень, состоящий из оксида алюминия, активированного 0,05% хрома. Они работают в импульсном режиме, генерируя импульсы когерентного монохроматического красного цвета. Применяют также газовые лазеры, которые могут работать как в непрерывном, так и в импульсном режимах.
Работа оптических квантовых генераторов основана на принципе стимулированного генерирования светового излучения. При включении пускового устройства лазера электрическая энергия, запасенная в батарее конденсаторов, преобразуется в световую энергию импульсной лампы. Свет лампы отражателями корпуса фокусируется на рубиновый стержень, в результате чего атомы хрома приходят в возбужденное состояние. Взаимодействие фотонов с возбужденными атомами дает лавинообразные потоки фотонов в различных направлениях. Наличие у стержня торцовых зеркальных поверхностей приводит к тому, что при многократном отражении усиливаются свободные колебания в направлении его оси вследствие стимулирования возбужденными атомами. Спустя 0,5 мс более половины атомов хрома приходят в возбужденное состояние, и система становится неустойчивой. Вся запасенная в стержне энергия резко одновременно высвобождается, и кристалл испускает яркий красный свет. Лучи света имеют высокую направленность, расходимость обычно не превышает 0,1°. Системой оптических линз луч фокусируется на поверхности обрабатываемой заготовки.
Энергия светового импульса лазера обычно невелика и составляет 20−100 Дж, но она выделяется в миллионные доли секунды и сосредотачивается в луче диаметром около 0,01 мм. В фокусе диаметр светового луча составляет всего несколько микрометров, что обеспечивает температуру около 6000−8000°С. В результате поверхностный слой материала заготовки, находящийся в фокусе, мгновенно расплавляется и испаряется. Основными характеристиками лазерного излучения являются мощность (Вт), длина волны (0,4−10,6 мкм), длительность (мс) и форма импульсов, расходимость пучка. Соответственно типовая структурная схема лазерной установки с твердотельным лазером, схема головки и работа лазера приведены на рис. 12.14−12.16.
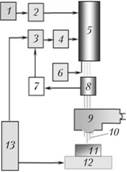
Рис. 12.14. Типовая структурная схема лазерной установки с твердотельным лазером:
1 — зарядное устройство: 2 — емкостный накопитель; 3 — система управления; 4 — блок поджига; 5 — лазерная головка; 6 — система охлаждения; 7 — система стабилизации энергии излучения; 8 — датчик энергии излучения; 9 — оптическая система; 10 — сфокусированный луч лазера; 11 — обрабатываемая заготовка; 12 — координатный стол; 13 — система программного управления.
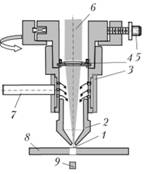
Рис. 12.15. Схема лазерной режущей головки для обработки материалов:
1 — фокус луча; 2 — форсунка; 3 — плавающий стакан; 4 — линзы; 5 — микрометр; 6' - лазерный луч; 7 — впуск газа; 8 — деталь; 9 — брусок.
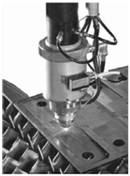
Рис. 12.16. Лазерная головка в работе.
Метод позволяет осуществлять: прецизионную резку тонколистовых металлов с точностью не хуже 20 мкм и неметаллических материалов; изготовление прокладок, разжимных колец, клапанных пластин, плоских пружин из самых разнообразных материалов; нанесение произвольных растровых или векторных изображений на металлические и неметаллические заготовки; разметку поверхности изделий перед обработкой.
Так же можно перфорировать практически любые материалы (рис. 12.17); упрочнять поверхности и режущие кромки инструмента и готовых деталей, в том числе и с помощью микролегирования, обрабатывать фрезы, шестерни, валы, поверхности скольжения, режущие кромки инструментов, выполненных из инструментальных сталей и сплавов.
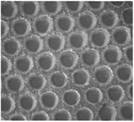
Рис. 12.17. Прошивка отверстий диаметром 50 мкм в нитриде бора.
Преимущества лазерной обработки: высокая скорость резки, невысокая стоимость расходных материалов (газ).
Недостатки: термическая закалка и оплавление кромок, дополнительная механическая обработка.