Исследование и разработка технологии для получения трубчатых заготовок из жаропрочных и коррозионностойких сплавов методом ротационного редуцирования
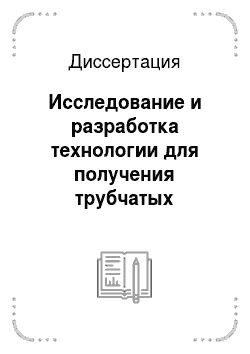
Диссертация
Предоставляя уникальные возможности обеспечения и регулирования требуемых характеристик деталей за одну технологическую операцию, ротационная вытяжка может выполняться с использованием относительно несложного оборудования, и, как правило, не требует дорогостоящей или сложной в изготовлении оснастки. Вместе с тем, процесс ротационной вытяжки на сегодняшний день является недостаточно изученным… Читать ещё >
Содержание
- 1. СОСТОЯНИЕ ВОПРОСА И ПОСТАНОВКА ЗАДАЧИ ИССЛЕДОВАНИЙ
- 1. 1. Характеристика объекта исследования
- 1. 2. Возможные процессы изготовления трубных заготовок
- 1. 2. 1. Традиционные процессы изготовления трубных заготовок
- 1. 2. 2, Ротационные методы обработки металлов
- 1. 3. Характеристика предложенной технологии
- 1. 3. 1. Определение процесса и возможности ротационной вытяжки
- 1. 3. 2. Разновидности и классификация процессов ротационной вытяжки
- 1. 3. 3. Оборудование и инструмент для ротационной вытяжки
- 1. 3. 4. Развитие механизации и автоматизации процессов ротационной вытяжки
- 1. 4. Развитие теоретического анализа процесса ротационной вытяжки
- 1. 5. Выводы
- 2. ТЕОРЕТИЧЕСКИЙ АНАЛИЗ
- 2. 1. Анализ напряженно-деформированного состояния при ротационной вытяжке
- 2. 2. Оценка допустимой степени деформации при обратном ротационном редуцировании
- 2. 3. Определение площади пятна контакта и расчет компонент рабочего усилия
- 2. 4. Выводы
- 3. МЕТОДИКА И РЕЗУЛЬТАТЫ ЭКСПЕРИМЕНТАЛЬНЫХ ИССЛЕДОВАНИЙ
- 3. 1. Задачи экспериментальных исследований
- 3. 2. Материалы и образцы
- 3. 3. Техника эксперимента
- 3. 4. Планирование экспериментов
- 3. 5. Экспериментальные исследования
- 3. 5. 1. Предварительные эксперименты
- 3. 5. 2. Экспериментальное установление зависимостей между параметрами получаемых деталей и факторами процесса
- 3. 5. 3. Изменение структуры и свойств исследуемого материала при ротационном редуцировании
- 3. 6. Выводы
- 4. ПРАКТИЧЕСКОЕ ПРИМЕНЕНИЕ РАЗРАБОТАННЫХ МЕТОДИК И РЕКОМЕНДАЦИИ ПО ИСПОЛЬЗОВАНИЮ ПРОЦЕССА РОТАЦИОННОЙ ВЫТЯЖКИ
- 4. 1. Общие принципы разработки технологии РВ с использованием программируемых станков с трехроликовыми раскатными головками
- 4. 2. Методика конструирования оснастки
- 4. 2. 1. Конструирование роликов
- 4. 2. 2. Расчет и конструирование опорных колец
- 4. 2. 3. Расчет и конструирование сепаратора
- 4. 3. Виды технологических отказов при ротационной вытяжке сплава ХН60ВТ и методы их устранения
- 4. 4. Обратная ротационная вытяжка с гидравлическим подпором стенки
- 4. 5. Экономические показатели процесса
- 4. 6. Выводы
Список литературы
- Ротационная вытяжка с утонением стенки.: Дис. док. техн. наук. — Тула. -1997.-506 с. 2. Горюнова Н.А.
- Многооперационная ротационная вытяжка цилиндрических оболочек.: Дис. канд. техн. наук. Тула. — 1999. — 222 с. 3. Гредитор M.JI.
- Давильные работы и ротационное выдавливание. — М.: Машиностроение, 1984.-239 с. 4. Кирьянов А.А.
- Исследование и разработка технологических основ процесса ротационной вытяжки.: Дис. канд. техн. наук. — Новосибирск, 1998. — 148 с.
- Ковка и штамповка: Справочник. М.: Машиностроение. — 1987. -т.4. — с. 234−2766. Корольков В.И.
- Математическое, методическое и программное обеспечение процессов ротационной вытяжки из листа и труб.: Дис. док. техн. наук. Воронеж, 1997.-450 с. 7. Могильный М.И.
- Ротационная вытяжка оболочковых деталей на станках. — М.: Машиностроение, 1983. — 190 с.
- Попов Е.А., Ковалев В. Г., Шубин И.Н.
- Технология и автоматизация листовой штамповки. М.: Издательство МГТУ им. Н. Э. Баумана. — 2000. — с. 158−1739. Радюченко Ю.С.
- Ротационное обжатие. М. Машиностроение. — 1972. — 176 с. 10. Романовский В.А.
- Справочник по холодной штамповке. М. Машиностроение. — 1976. — с. 212 218
- Ротационная вытяжка на станах типа СРГ (руководящий технический материал). / Раков Л. А. и др. М.: НИАТ. — 1983. — 127 с. 12. Смирнов В.В.
- Исследование процесса ротационного выдавливания тонкостенных сосудов шариковыми раскатными головками.: Дис. канд. техн. наук. — Тула. — 1970. — 212 с. 13. Суворов И.К.
- Обработка металлов давлением. М.: Высшая школа. -1980. — 368 с. 14. Сулиман Мустафа
- Ротационная вытяжка цилиндрических оболочек. М.: Машиностроение. -1984.- 128 с.
- Анализ процесса холодной поперечной прокатки (ротационного выдавливания). / И. И. Казакевич. Кузнечно-штамповочное производство.-1973.- № 7. — с.21−24
- Барабащук В.И., Креденцер Б. П., Мирошниченко В. И. Планирование эксперимента в технике. Киев: Техшка. — 1984. — 200 с.
- Бородин Н.М., Бочаров В.Б.
- Влияние холодной пластической деформации на свойства сталей и сплавов при ротационном выдавливании. // Материалы научно-технической конференции Воронежского ПИ. 1972. — с. 28−34
- Влияние нестационарной стадии ротационного выдавливания на качество изделий. / А. С. Маленичев и др. // Технология машиностроения.- Тула. -1973.-вып.29.-с. 31−33
- Влияние режимов ротационного выдавливания на качество изделий. / В. А. Шмелев и др. // Сборник трудов Уральского НИИЧЕРМЕТ, — 1975.-вып.24. с. 42−45
- Внеконтактная деформация при поперечной и поперечно-винтовой прокатке. / И. И. Казакевич // Технология легких сплавов. 1973.- № 11. — с. 16−19
- Выбор параметров процесса ротационного деформирования на оправке полых цилиндрических изделий. / В. Н. Витвицкий // Технология машиностроения. Выпуск 22. Тула, 1972 — с. 219−229
- Горский В.Г., Адлер Ю. П., Талалай A.M.
- Планирование промышленных экспериментов (модели динамики). — М.: Металлургия. 1978. — 112 с.
- ГОСТ 10 006–80 Трубы металлические. Методы испытания на растяжение.
- ГОСТ 166–73 Штангенциркули с ценой деления 0,1 мм. Технические условия.
- ГОСТ 17 410–78 Контроль неразрушающий. Трубы металлические бесшовные цилиндрические.
- ГОСТ 2789–73 Шероховатость поверхности. Параметры и характеристики.
- ГОСТ 577–68 Часовые индикаторы с ценой деления 0,01 мм. Технические условия.
- ГОСТ 6507–89 Микрометры с ценой деления 0,01 мм. Технические условия.
- Изготовление деталей автомобилей методом ротационного выдавливания. / В. И. Оленев, А. Н. Савостьянов и др. // Технология легких сплавов.- 1973.-№ 11.-с. 25−26
- Изготовление трубчатых профильных заготовок методом поперечной прокатки. / Ю. А. Верник, Б. П. Симонов, В. Г. Лузганов. // Технология легких сплавов.- 1973.- № 11.- с. 26−29
- Исследование процесса ротационного выдавливания на станах типа СРГ. / В. П. Осипов, В. И. Елисеев // Технология легких сплавов.- 1973.- № 11. — с. 2225
- К оценке усилия ротационной вытяжки цилиндрических деталей. / Е. А. Белов // Исследования в области пластичности и обработки металлов давлением. Сборник научных трудов. Тула. — 1986. — с. 105−160
- Методика проектирования технологических процессов ротационного выдавливания шариковыми раскатными головками. В. В. Смирнов,
- И.П.Ренне, Л. Г. Юдин, А. С. Маленичев. // Технология легких сплавов.- 1973.-№ 11. -с. 27−29
- Обработка металлов давлением. Операции ковки и штамповки. Термины и определения: ГОСТ 18 970–84
- Определение силовых параметров процесса ротационной вытяжки тонкостенных оболочек. / Добровольский И. Г., Степаненко А. В., Шиманович И. М. // Весщ Акадэми Беларускай ССР. 1983.- № 4. — с. 142−147
- Опыт применения методов ротационного выдавливания для изготовления кольцевых деталей. / Ю. М. Молотов, В. Л. Арутюнов, С. Н. Волков. // Технология легких сплавов.- 1973.- № 11. — с. 31−33
- Оценка стойкости инструмента при ротационной вытяжке. / А. С. Маленичев, А. И. Вальтер // Кузнечно-штамповочное производство. 2001. — № 1. — с. 3234
- Применение процесса ротационного выдавливания для изготовления деталей из титановых сплавов. / И. С. Тачкова, Печаев В. Ф. // Технология легких сплавов.- 1973.-№ 11. -с. 18−19
- Разработка технологии изготовления бесшовных цилиндрических тонкостенных обечаек методом раскатки. / Назарцев Н. И., Свитов Б. В. // Стали и сплавы цветных металлов. 1974. — с. 41−47
- Расчет мощности привода валков при установившемся режиме прокатки-волочения (ПВ). / Выдрин В. Н., Агеев Л. М., Сухарев В. А. // Технология легких сплавов.- 1976.- № 10. — с. 27−28
- Ротационное выдавливание роликовыми раскатными головками.
- И.П.Ренне, В. В. Смирнов, Л. Г. Юдин и др. // Кузнечно-штамповочное производство.- 1975.- № 8. с. 17−22
- Ротационное выдавливание шариковыми раскатными головками. /И.П.Ренне, В. В. Смирнов, Л. Г. Юдин и др. // Кузнечно-штамповочное производство.- 1975.-№ 6.-с. 14−18
- Ротационное изотермическое формообразование заготовок осесимметричных деталей типа дисков/ Бурлаков И. А., Плехов В. А. // Технология авиационного двигателе- и агрегатостроения: Сб. тр. НИИД.1 561 993. № 2. С. 177−179.
- Современное состояние процессов раскатки тонкостенных тел вращения. / М. С. Сиротинский, С. В. Сухов, В. Н. Зиновьев. // Технология легких сплавов.1978.- № 10. -с. 14−17
- Теоретическое и экспериментальное исследование силовых параметров ротационного выдавливания шариковыми раскатными головками. /В.В.Смирнов, И. П. Ренне, Л. Г. Юдин, А. С. Маленичев. // Технология легких сплавов.- 1973.- № 11. с. 21−24
- Требования к геометрии стальных тонкостенных деталей, изготавливаемых ротационным выдавливанием. / А. А. Ливанов // Технология легких сплавов.-1973.-№ 11.-с. 21−24
- Троицкий В.П., Мохов А. И., Кобелев А.Г.
- Проектирование цехов обработки металлов давлением. Учебник для вузов. -ВолгГТУ. Волгоград. — 1997. — 389 с.
- Трубы бесшовные холоднодеформированные из сплава ХН60ВТ (ЭИ868): ТУ 14−3-571−77 М.: Стройиздат. 1977. — 14 с. 50. Тюрин В.А.
- Методы планирования эксперимента. Раздел: Математическое планирование и обработка эксперимента первого порядка. Курс лекций. М.: МИСиС. —1979.-77с.
- Формообразование точных заготовок сложного рельефа методом сферодвижной штамповки. / B.C. Чистяков // Технология авиационного двигателе- и агрегатостроения: Сб. тр. НИИД. 1993. № 2. С. 183−193.
- Авиационные материалы: М.: Машиностроение, 1984. — т. № 3.53. К.Н. Богоявленский
- Гидропластическая обработка металлов Л. Машиностроение 1988 г.
- A broad approach to spinning technology. / David Pollitt // Sheet Metal Ind.-1981.-№ 9.-pp. 38−44
- A numerically-controlled metal-forming centre for spinning of sheet metals. / H.F.Brockhoff // Sheet metal Ind.- 1981.- № 1. pp. 45−47
- Alcoa using computerized spin forge. // AWST. 1984.- № 4. pp. 18−21
- Automatic spinning a revolution in the making. / David Pollitt // Sheet Metal Ind.- 1981.-№ 7.-p. 57
- British firm robotizes spinning. // Metal stamping. 1984.- № 3. — pp. 31−33
- Case histories demonstrate metal spinning’s virtues. // Modern metals.- 1975.-№ 5.-pp. 48−56
- Flow forming under numerical control. // Metallurgia and metal foming.- 1977.-№ 8.-pp. 56−59
- Flowturning stainless steel. / K. Campbell // Sheet metal industries. 1974.- № 5. — pp. 50−53
- Forming diagrams for axissymmetric sheet metal forming. / R.B.Noyes // Sheet Metal Ind.- 1983.- № 5 pp. 28−33
- Metal spinning and shear and flow forming. / C.L.Pakham // Metallurgia and metal forming. 1976.- № 6. — pp. 45−48
- Metal spinning enters the robot age. / Sheet metal industries.- 1983, — № 3. — pp. 4651
- Metal spinning. A rewiew and update. / Charles Wick // Manufacturing engineering.- 1978, — № 1. pp. 56−60
- Modern spinning and flow-forming. / A. W. Astrop // Machinery and production engineering.- 1976.-№ 3315.-pp. 78−85
- New centre for high technology metal spinning. // Metallurgia.- 1984.- № 1. — pp. 36−41
- New horizons for metal forming. / C.L.Pakham // Metallurgia.- 1978.- № 6. pp. 17−24
- Plastic flow instability under compressive loading during shear spinning process. / Misha Gur, Jehuda Tirosh // Journal of Engineering for Industry. 1982.- № 2. -pp. 182−190
- Specify spinning. / Cristopher Davy // Engineering. 1983.- № 2. — pp. 43−45
- Spin forming of aluminium tubes: experimental observations. / R.K. Ghosh, P.B. Hattacharyya, A.K. Seal. // Indian Journal of technology. 1979.- № 1. — pp. 120 135
- Spinning: Out of the Dark Ages but not all the way. / Dan Daniels // Metalstamping. 1978. — № 7. — pp. 34−40
- The challenge of tube spinning. I I Machinery and production engineering.- 1983.-№ 3623. pp. 31−37
- Wang Qiang, Wang Tao, Z.R.Wang
- A study of the working force in conventional spinning. // Proceedings of RoMP, Beijing. 1985.-pp. 147−153
- Утверждаю" Главныишш fiep ФГУП ММПП «Салют» (Д1. Утверждаю" МГИСиС (ТУ)1. ТЕХНИЧЕСКИЙ АКТ
- Ягатям совместных научно-технических работ ФГУП ММПП «Салют» и МГЙСиС (ТУ) по разработке технологии производства трубчатых заготовок из жаропрочных и коррозпонностонких сплавов ротационной вытяжкой на трехролнковом станке с ЧПУ.
- В период с октября 2001 но октябрь 2004 г. МГИСиС (ТУ) совместно с ФГУП ММПП «Салют» выполнил следующие работы:
- Выполненные работы и полученные результаты Исполнители1 2 3
- Предложена схема модернизации станка 16А20ФЗС для реализации процесса ротационной вытяжки и произведено проектирование инструмента и оснастки. ФГУП ММПП «Салют» МГИСиС (ТУ)
- Модернизирован станок 16А20ФЗС для реализации процесса ротационной вытяжки ФГУП ММПГ1 «Салют»
- Изготовлена экспериментальная оснастка п инструмент для исследования процесса ротационной вытяжки деталей типа форсунок и переходников из жаропрочных и коррозионно-стойких сплавов. ФГУП ММПП «Салют»
- Проведено физическое моделирование и исследованы закономерности процесса ротационной вытяжки детачей типа форсунок и переходников из жаропрочных и коррозионно-стойких сплавов. ФГУП ММПП «Салют» МГИСиС (ТУ)
- Создана технология изготовления детали «Форсунка» ротационной вытяжкой. ФГУП ММПП «Салют» МГИСиС (ТУ)
- Проведен сравнительно технико-экономический анализ производства деталей типа форсунок с применением серийной технологии и технологии ротационной вытяжки. МГИСиС (ТУ)
- Начальник НИЛ ОМД Бурлаков II.A.от МГИСнС (ТУ) романцсв Б.А./аспирант Данилов В.В.передачи нау
- ОТ^ЕРЖДАЮ" ^^"""Прс^ктор МПЙСиС (ТУ)jr^yaa/ki^^o^работе1. Л.В. Кожитов2005 года. для использования в учебном процессе
- Разработчики безвозмездно передают, а Пользователи принимают для использования в учебном процессе на кафедре ОМД и НИЛ ДСПМ при проведении КНИР и дипломного проектирования следующие научно-технические материалы:
- Файлы базы данных с описанием механических, физических и технологических свойств жаропрочного сплава ХН60ВТ-
- Файлы с примерами геометрических моделей переходов ротационного редуцирования и данные для ввода исходных данных в САПР «Расчет усилия» и «Расчет инструмента» для расчетов переходов, инструмента и оснастки для ротационного редуцирования-
- Файлы данных и плакаты с примерами оформления результатов математического моделирования операций ротационного редуцирования:
- Образцы экспериментальных исследований с возможными дефектами процесса и годными изделиями.
- Ответственными за прием и хранение материалов на кафедре ОМД и НИЛ ДСПМ назначены в.н.с. Цепин М. А. и аспирант Апатов К.Ю.
- Пользователи принимают обязательство при использовании данных материалов в договорных НИР рассматривать вопрос о материальном вознаграждении Разработчиков в рамках отдельных договоров.