Разработка и исследование антифрикционных сплавов системы Al-Si-Cu-Pb и технологии изготовления из них литых деталей с целью создания нового поколения шестеренных насосов
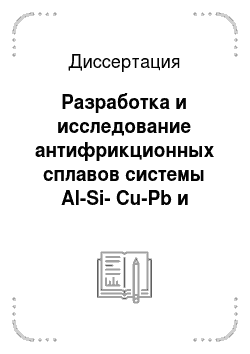
Диссертация
Для изготовления отливок из этих сплавов выбран способ литья с кристаллизацией под давлением. На основе исследований рекомендуются следующие технологические режимы литья: температура заливки — 680.730 °Стемпература матрицы пресс-формы — 180.200 °Сдавление прессования -160.240 МПавремя выдержки расплава в матрице до приложения давленияминимальное (не более 3 с) и под давлением из расчета 1… Читать ещё >
Содержание
- 1. ЛИТЕРАТУРНЫЙ ОБЗОР
- 1. 1. Детали шестеренных насосов, изготовляемые из алюминиевых сплавов
- 1. 2. Литьё с кристаллизацией под давлением сплавов цветных металлов
- 1. 3. Антифрикционные и износостойкие алюминиевые сплавы
- 1. 4. Свойства антифрикционных и износостойких алюминиевых сплавов, закристаллизованных под давлением
- 2. МЕТОДИКА ИССЛЕДОВАНИЙ
- 2. 1. Выбор сплавов, опытных отливок и режимов литья
- 2. 2. Методика исследования затвердевания и уплотнения формирующихся отливок
- 2. 3. Методика исследования качества и усадки отливок
- 2. 4. Методика исследования ликвации свинца в отливках
- 2. 5. Методика исследования структуры и механических свойств сплавов и отливок
- 2. 6. Методика исследования температурных интервалов плавления сплавов
- 2. 7. Методика исследования фрикционных характеристик сплавов
- 3. ИССЛЕДОВАНИЕ ЗАТВЕРДЕВАНИЯ И УПЛОТНЕНИЯ ПРИ ЗАТВЕРДЕВАНИИ ОТЛИВОК
- 3. 1. Исследование затвердевания и уплотнения формирующихся отливок
- 3. 2. Исследование усадки отливок
- 3. 3. Выводы по главе
- 4. ИССЛЕДОВАНИЕ СТРУКТУРЫ И СВОЙСТВ ОТЛИВОК
- 4. 1. Исследование ликвации свинца в сплавах и отливках
- 4. 2. Исследование структуры и механических свойств отливок
- 4. 3. Исследование фрикционных характеристик отливок
- 4. 4. Выводы по главе
- 5. РАЗРАБОТКА И ВНЕДРЕНИЕ В ПРОИЗВОДСТВО ТЕХНОЛОГИИ ЛИТЬЯ С КРИСТАЛЛИЗАЦИЕЙ ПОД ДАВЛЕНИЕМ ЗАГОТОВОК ДЕТАЛЕЙ ШЕСТЕРЁННЫХ НАСОСОВ
- 5. 1. Литьё с кристаллизацией под давлением компенсаторов
- 5. 2. Литьё с кристаллизацией под давлением втулок
- 5. 3. Повышение надёжности шестерённых насосов
- 5. 4. Внедрение процесса ЛКД в производство
- 5. 5. Экономическая эффективность процесса ЛКД
- 5. 6. Выводы по главе
Список литературы
- Пляцкий В.М. Кристаллизация под поршневым давлением. — М.: Маш-гиз, 1950. — 62 с.
- Пляцкий В.М. Литейные процессы с применением высоких давлений. -М.: Машгиз, 1954. 224 с.
- Пляцкий В.М. Штамповка из жидкого металла М.: Машиностроение, 1964.-315 с.
- Батышев А.И. Кристаллизация металлов и сплавов под давлением М.: Металлургия, 1977. — 155 с.
- Штамповка жидкого металла: Литье с кристаллизацией под давлением / Батышев А. И., Базилевский Е. М., Бобров В. И. и др.- под ред. А. И. Батышева. -М.: Машиностроение, 1979. 200 с.
- Батышев А.И. Кристаллизация металлов и сплавов под давлением. 2-е изд. — М.: Металлургия, 1990. — 144 с.
- Специальные способы литья: Справочник / под ред. В. А. Ефимова.- М.: Машиностроение, 1991. С. 342−365.
- Гилевич И.Б., Белоусов Н. Н. Литье с кристаллизацией под давлением на машинах литья под давлением // Литейное производство, 1989, № 12. С. 16.
- Штамповка поршня из жидкого металла /Савицкий А.Б., Масюкевич А. В., Зуев А. Б. и др. // Литейное производство, 1969, № 3. С. 27.
- Suzuki S. Vertical squeeze casting of aluminum components // Modern Costing, 1989, V. 79, № 10. P. 38−40.
- Young R.P. Application of real time process control in the production of high performance light alloy casting / 62-ud World Foundry Congress. Philadelphia, 1996.-P. 1−13 (Доклад № 29).
- Ueno J., Uchida M., Sose U. Squeeze casting: present and future // Die casting technology: Mater. Congress. October. 18−21, 1993. — Cleveland (Ohio).- P.413−418. (Доклад T93−135).
- Chadwick G.A. A rationale towards understanding quality in cast metal products // Foundry man, 1995. V. 88, № 1. P. 20−23.
- Цветное литье / под ред. И. Ф. Колобнева. М.: Машиностроение, 1966. -С. 362−365.
- Сергеев П.С. Штамповка жидких цветных металлов и сплавов. JL: Суд-промгиз, 1957. — 88 с.
- Соскин JIJML, Токарев Н. С. Штамповка деталей из жидкого металла. JI.: Лениздат, 1957. — 124 с.
- Барановский М.А., Вербицкий Е. И. Штамповка жидких металлов. -Минск. Госиздат БССР, 1963. 75 с.
- Красильщик Н.Л., Смирнов К. Н. Штамповка жидкого металла. М.: Машпром, 1962. — 52 с.
- Батышев А.И. Совмещенные способы литья и прессования: Обзор. М., НИИМАШ, 1971.-48 с.
- Батышев А.И. Формирование отливок под воздействием давления, вибрации, ультразвука и электромагнитных сил: Обзор. М., НИИМАШ, 1977. -54 с. (серия С-3).
- Батышев А.И., Безпалько В. И. Литье с кристаллизацией под давлением сплавов цветных металлов: Обзор. М., ЦНИИТЭИ приборостроения, 1985. -48 с. (ТС-9. Экономика и технология приборостроения, вып. З).
- Батышев А.И., Безпалько В. И., Любавин А. С., Батышев К. А. Литье с кристаллизацией под давлением: Обзор. М., ВНИИТЭМР, 1989. — 54 с. (Серия «Технология и оборудование литейного производства, вып. 1).
- Батышев К.А. Литье с кристаллизацией под давлением. М.: Изд-во МГОУ, 2009.- 167 с.
- Марков В.В., Белявский Г. И. Двойное прессование при жидкой штамповке // Литейное производство, 1976, № 3. С. 41.
- Марков В.В., Гейко И. В. Силовые характеристики при жидкой штамповке /В сб. «Управление строением отливок и сплавов». Горький, 1984. — С. 122 127.
- Тимофеев Г. И., Пименов Н. П. Особенности питания отливок при литье с кристаллизацией под давлением // Литейное производство, 1990, № 3. С. 2425.
- Марков В.В. О влиянии трения между отливкой и формой на потери усилий при жидкой штамповке // Литейное производство, 1981, № 4, — С. 19.
- Питание заготовок при штамповке из жидких сплавов / Пименов Н. П., Тимофеев Г. И., Казаринов И. Б. и др. // Судостроительная промышленность. Серия «Технология и организация производства», 1990, № 23. С. 26−31.
- Липчин Т.Н. Структура и свойства цветных сплавов, затвердевших под давлением. М.: Металлургия, 1994. — 128 с.
- Липчин Т.Н. Получение заготовок поршней литьем с кристаллизацией под давлением. Пермь: Изд. ТГУ, Пермское отделение, 1991. — 136 с.
- Липчин Т.Н. Измельчение структуры и свойств сплавов при воздействии на расплав давления // Литейное производство, 1985, № 7. С. 9−10.
- Батышев А.И. Теплосиловые условия формирования отливок при литье с кристаллизацией под давлением // Литейное производство, 1982, № 4. С. 2022.
- Безпалько В.И., Батышев А. И. Структура и физико-механические свойства силуминов, отлитых с кристаллизацией под давлением // Литейное производство, 1986, № 7. С. 8−9.
- Батышев А.И. Литье с кристаллизацией под давлением: теория и практика // Изв. вузов. Цветная металлургия, 1996, № 3. С. 41−45.
- Батышев А.И. Характер и результаты воздействия давления на затвердевающую отливку // Вестник машиностроения, 1996, № 8. С. 19−21.
- Безпалько В.И. Литье с кристаллизацией под давлением силуминов. М.: Изд-во МГОУ, 2012. — 208 с.
- Бидуля П.Н., Чурсин В. М. Исследование прессованного литья из медных сплавов /В сб. «Новые технологические процессы литейного производства». 4.1.-М., 1967.-С. 364−368.
- Бронтвайн Л.Р., Чурсин A.M. Отливки из сурьмяных бронз.- М.: Машиностроение, 1985. 112 с.
- Белоусов H.H. Затвердевание отливок из цветных сплавов в условиях приложения давления /В сб. «Затвердевание металлов».- М.: Машгиз, 1958. С. 176−214.
- Белоусов H.H., До донов A.A. Кристаллизация отливок из цветных сплавов в условиях приложения давления /В сб. «Кристаллизация металлов», — М.: Изд. АН СССР, 1960. С. 279−297.
- Влияние высокого давления при кристаллизации на структуру и свойства алюминиевых сплавов /Абрамов A.A., Паутова Д. М., Боричева И. К. и др. // Литейное производство, 1989, № 3. С. 5−6.
- Постников Н.С. Упрочнение алюминиевых сплавов и отливок. М.: Металлургия, 1983. — 119 с.
- Ясинский К.К., Бурыгин A.A., Постников Н. С. Формирование структуры и свойств высокопрочных алюминиевых сплавов в процессе жидкой штамповки /В сб. «Прогрессивные способы плавки литейных сплавов». Киев, 1987. -С. 78−83.
- Золоторевский B.C. Современные литейные алюминиевые сплавы // Металловедение и термическая обработка металлов, 1993, № 7. С. 11−16.
- Векшин В.И. Жидкая штамповка точных отливок // Литейное производство, 1972, № 1.-С. 20.
- Неймарк Е.И., Комаров В. А. Жидкостная штамповка // Электронная техника (Серия 7), 1972. Вып. 1(49). С. 87−92.
- Белоусов H.H., Варич Н. И., Щербаков Г. И. Исследование влияния тепловых условий затвердевания отливок под поршневым давлением на субмикроструктуру алюминиевых сплавов /В сб. «Теплофизика в литейном производстве». Минск, 1963. — С. 234−243.
- Рыжиков A.A., Марков В. В. Характер кристаллизации и свойства отливок из цветных сплавов в условиях штамповки жидкого металла / В сб. «Новые технологические процессы литейного производства». 4.1. М., 1967. — С. 335 339.
- Жидкая штамповка поршней из алюминиевых сплавов /Рубцов Ф.Г., По-тураев В.М., Губенко В. А. и др. /Сб. трудов НИПТИАММаш. Челябинск, 1968.-С. 127−133.
- Дядечко Г. П., Стеблюк В. И., Красножен И. М. и др. Выбор давления прессования металла в закрытой матрице в период кристаллизации // Литейное производство, 1975, № 9. С. 32.
- Постников Н.С., Черкасов В. В. Прогрессивные методы плавки и литья алюминиевых сплавов. -М.: Металлургия, 1973.
- Волкова A.B., Лившиц В. Б. Получение алюминиевых отливок повышенной плотности // Приборы и системы управления, 1978, № 10. С. 51,52.
- Брежнев JI.B., Батышев А. И. Использование элементов современной технологии при литье с кристаллизацией под давлением // Литейщик России, 2002, № 9.-С. 16−17.
- Брежнев Л.В., Батышев А. И., Батышев K.A., Полянчиков О. Г. Гидравлический пресс для литья с кристаллизацией под давлением алюминиевых сплавов // МГОУ-ХХ1-Новые технологии, 2012, № 5−6. С. 7−8.
- Челышев А.П., Еманов Л. Ф., Овчинников ЕЛ. Изготовление деталей типа «фланец» методом литья с кристаллизацией под давлением // Кузнечно-штамповочное производство, 1985, № 6. С. 22,23.
- Макогон А.Д., Платонов В. Н., Попов В. М. Жидкая штамповка дизельных поршней из алюминиевых сплавов // Литейное производство, 1985, № 10.- С. 22−23.
- Клевцов Г. В., Бакиров Ж. Т., Жижерин А. Т. и др. Влияние способов литья на структуру и усталостную прочность алюминиевого сплава ВАЛ8 // Изв. вузов. Цветная металлургия, 1990, № 5. С. 96−102.
- Белов H.A. Влияние эвтектических фаз на характер разрушения высокопрочных литейных сплавов // Металловедение и термическая обработка металлов, 1995, № 6. -С. 20−24.
- Строганов Г. Б. Высокопрочные литейные алюминиевые сплавы, — М.-: Металлургия, 1985. 216 с.
- Баев В.А. Влияние давления на литейные и физико-механические свойства алюминиевых сплавов /В сб. «Литье с применением давления». Киев, 1991.-С. 83−89.
- Герасименко В.Т., Гавриленко В. М., Селиванов В. А. Повышение механических свойств отливок путем управления при жидкой штамповке силуминов /В сб. «Прогрессивные способы управления процессом формирования отливок». Киев, 1989. — С. 78−80
- Шишляев В.Н., Гришин И. Л. Свойства сплава АЛ9М при литье с кристаллизацией под давлением /В сб. «Тепловые и физико-химические процессы в отливках и формах». Пермь, 1989. — С. 118−121.
- Шиняев А.Я., Литвинова А. И., Пивкина О. Г. Структура и механические свойства сплавов системы Al-Si, полученных кристаллизацией под давлением // Металловедение и термическая обработка металлов, 1983, № 2. С. 44−46.
- Никитин В.И., Никитин К. В. Наследственность в литых сплавах. Самара, 2008.-248 с.
- Батышев А.И., Безпалько В. И., Любавин A.C. и др. Затвердевание отливок из высокопрочных алюминиевых сплавов под давлением // Литейное производство, 1991, № 11. С. 8,9.
- Беллавина E.H. Особенности формирования структуры заготовок, полученных методом жидкой штамповки /Сб. «Литье и кристаллизация магниевых и алюминиевых сплавов под давлением». Пермь, 1980.-С. 117−120.
- Борисов Г. П. Давление в управлении литейными процессами. Киев: Наукова думка, 1988. — 272 с.
- Ефимов В.А., Эльдарханов. Физические методы воздействия на процессы затвердевания сплавов. М.: Металлургия, 1995. — 272 с.
- Котлярский Ф.М. Формирование отливок из алюминиевых сплавов.- Киев: Наукова думка, 1990. 216 с.
- Suzuki S. Extrusion casting // Imono, Journal Japan Countrymen’s Society. -1969. V. 41, № 7. P. 524−538.
- Fijii N., Fijii M., Morimoto S. Endless des Gusstuck-querschnittes beam Pressgiessen vonciner Al-8% Si Legierung // Aluminium (BRD), 1985. H. 61, № 9.-S. 673−679.
- Murakami N., Kaneko Y., Kuruda K. Flussigpressen von Aluminium // Giesserei- Praxis, 1980, № 8. S. 106−111.
- Gotoh Y., Kataoka Y., Ohfukune Y., Suzuki S. Praktische Anwendungen des Pressgiessen von Aluminum-Knitlegierungen // Aluminium (BRD), 1987. H. 63, № 2. -S. 161−167.
- Aweda J.O., Adeyemi M.B. Experimental determination of heat transfer coefficients during squeeze casting of aluminium // Journal of Materials Processing Technology, 2009. V. 209, № 3. P. 1477−1483.
- Lynch R.F., Olley R.P., Callagher P.C.J. Squeexe casting of aluminum // Die casting and Metal Mould, 1977. V. 8, № 2. P. 7−8.
- Lynch R.F., Olley R.P., Callagher P.C. J. Squeeze casting aluminum // Die casting engineer, 1976. V. 20, № 5. P. 12−20.
- Rozak G.A., Goddard D.M. Yield and tensile strengths of squeeze cast and treated AZ91 magnesium and A3 5 6 aluminum // Die casting technology: NADS A. Cleveend, 1993. P. 419−428. (T93−136
- Chatterjee S., Das A.A. Some observations of the effect of pressure on the solidification of Al-Si eutectic alloys // British Foundryman, 1973. V. 66, № 4. P. 119−124.
- Maleki A., Shafyei A., Niroumand B. Effects of squeeze casting parameters on the microstructure of LM13 alloy // Journal of Materials Processing Technology, 2009. V. 209, № 8. P. 3790−3797.
- Second report of Institute working group T20 the squeeze-casting, process // Foundryman, 1994. V. 87, № 11. P. 386−390.
- Clegg A.J. Squeeze casting in context // Foundry Trade Journal, 1986. V. 9, № 28.-P. 31−38.
- Williams G. Squeeze former combines casting with forcing // Foundry Grade Journal, 1984. V. 154, № 2. P. 66−70.
- Chattopadhyay H. Simulation of transport process in squeeze casting // Journal of Materials Processing Technology, 2007. V. 186, № 1−3. P. 174−178/
- Murthy G.R.K. Process development and applications for strategic materials/components // Journal Institute Engineer (India), 1988. V. 68, № 4. P. 101−107.
- Holecek S., Brezina J., Kubelicek L. Kolbenherstellung mach dam Pressgiess-Verfahren // Aluminium (BRD), 1988, H. 64, № 1. S. 80−83.
- Grigerova T., Grudkowa L., Behan B. Gefugebildung des untereutekischen Silumins bee der Erstarrung under dam Drunk in sum Jail isolierten Kokille // Giesserei Rundschau, 1993, H. 40, № ¾. S. 26−32.
- Stancek L., Sroka J., Sroka P. Meted hodnotenia Vplyvu procesovycu parametric liatia s crystallization pod tlakom // Slevarenstvi, 1992, № 2. S. 30−36.
- Glasnost tuhnutia odliatkov so slating typo Al-Si latish s technetium pod tlakom /Dzugas P., Vilcko J., Batysev A.I. h // Slevarenstvi, 1991, № 4. S. 107 116.
- Stancek L. On potential influence of pressure in solidification process in squeeze casting (SC) / Die Casting technology: NDASA. Cleveland, 1993. P. 399 408. (T93−133).
- Stancek L., Vanko B., Sedlacek E., Batysev A.I. Takove liatie & automo-bilovy priemysel // Strojarstvo Strojirenstvi, 2008, № 8. S. 92−94.
- Станчек Jl., Батышев А. И., Седлачек Е., Батышев К. А. Получение тиксо-тропной структуры в отливках при литье с кристаллизацией под давлением // Литейщик России, 2005, № 12. С. 54−57.
- Stancek L., Vanko В., Sedlacek Е., Batysev A.I. Takove liatie & automo-bilovy priemysel // Strojarstvo Strojirenstvi, 2008, № 8. S. 92−94.
- Станчек Л., Батышев А. И., Ванко Б., Седлачек Е. Влияние скоростей охлаждения течения расплава на структуру отливок при литье с кристаллизацией под давлением // Литейное производство, 2011, № 3. С. 14−20.
- Батышев А.И., Станчек Л. Литье с кристаллизацией под давлением // Литейное производство, 2003, № 4. С. 16−19.
- Stancek L., Batysev A.I., Caplovic L., Batysev K.A. Metallographic Verification of the model of the flow enforced during solidification under high external pressure // Die Casting Engineer, March 2007 S. 56 60/
- Станчек Л., Батышев А. И., Ванко Б., Седлачек Е. Влияние скоростей охлаждения течения расплава на структуру отливок при литье с кристаллизацией под давлением // Литейное производство, 2011, № 3. С. 14−20.
- Konopka Z. Otrzymywanic i glasnost kompoxytu AK9-Pb // Krzepnigcie metallic stupor. Til. Wroclaw. (ПНР), 1989. — S. 125−134.
- Wierzbicka B. Struktura i wlasnosci odlewu prasowaneao v stanie cieklym // Prace naykowe Justiutu technologii Budowy maszyn Politechniki Wraclawskiey, 1988. T. 35,-S. 160−164.
- Castellani C., Ouvre B. Forge age liquide dune coiffe support-moteur //
- Hommes et fonderie, 1992, № 6 7. P. 13−18.
- Lewis R.W., Han Z.Q., Gethin D.T. Three-dimensional finite element model for metal displacement and heat transfer in squeeze casting process // Comptes rendus. Mecanique/Academie des sciences, Paris, 2007. V. 335. S. 287−294.
- Anspach A. Zum Feussigpressen in der Giesserei // Giessereitechnik, 1979. H. 25, № 10.-S. 308−313.
- Tietmann A., Welschof К., Baldner К., Kopp R. Giesschmieden neue Moglichkeiten der Prozessverurzung // Stahl und Eisen, 1989, H. 109, № 6. S. 59−62.
- Zhang Milan, Xing Shuming, Xiao Liming и др. // Journal of University of Science and Technology Beijing, 2008. V. 15, № 3. P. 339−343.
- Han Z., Huang X., Luo A.A. и др. A quantitative model for describing crystal nucleation in pressurized solidification during squeeze casting // Scripta materi-alia, 2012. V. 66, № 5. P. 215−218.
- Строганов Г. Б., Ротенберг В. А., Гершман Т. Б. Сплавы алюминиевые с кремнием. М.: Металлургия, 1977. — 272 с.
- Амосов В.М., Потанин С. А. // Автомобильная промышленность, 1960, № 4.-С. 9−12.
- Shivandath R., SenguptaР.К., Egne J.S. //BritishFoundryman, 1977, V.70, № 11.-P. 343 -356
- Clegg A.J., Das A.A. // British Foundryman, 1977, V.70, № 11. P. 333 339.
- Буше H.A. Миронов A.E., Марков Т. Ф. Новый антифрикционный сплав АОЮС2 // Тяжёлое машиностроение, 2005, № 10. С. 27−29.
- Карачарова Е.Г., Миронов А. Е. Антифрикционные алюминиевые сплавы с повышенными свойствами // Литейное производство, 2011, № 10. С. 12−15.
- Карбаткин И.И., Буше H.A., Горячева И. Г., Зайчиков A.B. Влияние состава алюминиевых антифрикционных сплавов на процессы образования защитных плёнок при контактном взаимодействии // Трение и износ, 2006. Т. 27, № 4.-С 355−360.
- Гершман И.С. Описание процесса схватывания методами неравновесной термодинамики теории самоорганизации // Трение и износ в машинах и механизмах, 2009, № 4. С. 3−5.
- Гершман И.С., Гершман Е. И. Каталитическое действие при трении // Трение и износ. Т. 32, № 6. С. 571−578.
- А.с. № 351 920 (СССР). Антифрикционный сплав на основе алюминия / Винницкий А. Т. и др. Б.И., 1972, № 28.
- А.с. № 425 962 (СССР). Сплав на основе алюминия / Тихомиров В. М. и др.-Б.И., 1974, № 16.
- Патент № 2 030 475 (РФ). Антифрикционный сплав на основе алюминия / Потеряев Ю. П. и др. О.И., 1995, № 9.
- Aluminum-lead crankshaft bearing alloys // Automotive Engineering, 1989. V. 97, № 12.-P. 21−25.
- Srivastawa S.K., Mohan S., Agarwala V. The effect of aging on wear characteristics of recast leaded aluminum alloys // Metallurgical and Materials Transaction A., 1994. V. 25, № 4.-P. 851−856.
- Чашечкина Ж.Ю., Орлов Д. Б. Антифрикционные алюминиевые сплавы с повышенным содержанием свинца для подшипников скольжения ДВС // Машиностроитель, 1996, № 1.-С. 10−14.
- Патент № 2 038 403 (РФ). Сплав на основе алюминия АК7МгМ / Белов Н. А., Золоторевский B.C. и др. БИ., 1995, № 6.
- Патент № 2 038 404 (РФ). Сплав на основе алюминия АК7МгМ / Белов Н. А., Золоторевский B.C. и др. БИ., 1995, № 6.
- Shi М. // Manufacturing technology and machine tool (КНР), 1996, № 3. -P. 44−46.
- Горбунов В.Г., Паршин В. Д., Панин В. В. Особенности получения отливок из алюминиевых сплавов со свинцом и их свойств // Литейное производство, 1973, № 9.-С. 9−11.
- Zhang М., Zhang W., Zhao Н. и др. Effect of pressure on microstructures and mechanical properties of Al-Cu-based alloy prepared by squeeze casting // Transactions ofNonferrous Metal Society of China, 2007, V. 17, 3. P. 496−501/
- Pathak J.P., Ojha S.N. Effect of processing on microstructure and wear characteristic of an Fl-4.5Cu-10Pb alloy // Bulluten Mater. Sci., 1995, V. 18, № 8. -P. 975−988.
- Колесникова B.C., Белоусов H.H. Исследование антифрикционных свойств некоторых бронз и латуней / Трение и износ в машинах. Сб. XIV. М.: Изд. АН СССР, 1960. — С. 100−170.
- Литье с кристаллизацией под давлением антифрикционных сплавов) Батышев А. И., Любавин А. С., Безпалько В. И., Горбач С. П., Георгиевский Г. М. // Литейное производство, 1995, № 2. С. 13−15.
- Капаев Н.А., Трофимов Н. В. Атомно-абсорбционный и пламенно-фитометрический анализ сплавов. -М.: Металлургия, 1983 160 с.
- Мур Д. Основы трибоники. М.: Мир, 1979.
- Гаркунов Д.Н. Триботехника. -М.: Машиностроение, 1989.
- Силумины. Атлас микроструктур и фрактограмм промышленных сплавов: Справочное издание / Пригунова А. Г., Белов Н. А., Таран Ю. Н. и др. -М., МИСИС, 1996.- 175 с.
- Подшипники из алюминиевых сплавов / Буше Н. А. и др. М.: Транспорт, 1974.-256 с.
- Рассадин Ю.А., Рудницкий Н. М., Авинян Ю. Л. Повышение качества алюминиевых антифрикционных сплавов введением в них свинца / Повышение качества и надежности биметаллических подшипников. М., ЦНИИТЭИ Трак-торсельхозмаш, 1972.
- Research into an aluminium-babbit material stems from a need for an «intermediate bearing» // Iron Age, 1969, v. 203, № 6.
- Георгиевский М.Г., Батышев К. А., Батышев А. И. Ликвация свинца в отливках из медистых силуминов // МГОУ XXI — Новые технологии, 2005, № 5.-С. 29−32.
- Ликвация свинца в отливках из алюминиевых сплавов / А. И. Батышев, К. А. Батышев, C.B. Гольцова, М. Г. Георгиевский // Литейное производство, 2007, № 12.-С. 2−4.
- Георгиевский М.Г., Батышев К. А. Литье компенсаторов для шестеренных насосов / Сборник докладов «Прогрессивные литейные технологии». 4-я Международная научно-практическая конференция, МИСиС, 22−28 октября 2007, Москва. Москва, 2011. — С. 120−122.
- Георгиевский М.Г., Батышев К. А. Изготовление отливок из антифрикционных алюминиевых сплавов / Труды 6-й международной научно-практической конференции «Прогрессивные литейные технологии», МИСиС, 24−28 октября 2011. Москва, 2011. — С. 79−80.
- Георгиевский М.Г., Батышев К. А. Шестеренные насосы нового типа и литьё с кристаллизацией под давлением // Литейное производство, 2013, № 7. -С. 29−30.
- Патент РФ № 2 226 569. Литейный антифрикционный сплав на основе алюминия / М. Г. Георгиевский, В. А. Васин, О. В. Сомов. Б.И., 2004, № 10.