Механизация строительства цементобетонных покрытий
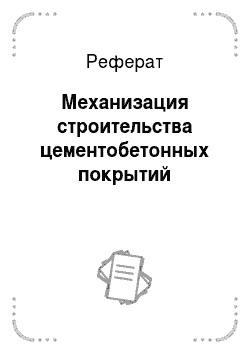
Глубинные вибраторы 3 являются основным оборудованием для уплотнения бетонной смеси, во многом определяющим дальнейшее качество покрытия. Они позволяют полностью прорабатывать смесь с осадкой конуса не менее 2,5 см по всей ширине укладываемой полосы. 9−14 глубинных вибраторов закрепляют на поворотной трубе на расстоянии 0,60 — 0,53 м один от другого под углом 15° — 20° к горизонту при допускаемом… Читать ещё >
Механизация строительства цементобетонных покрытий (реферат, курсовая, диплом, контрольная)
Цементобетонные покрытия относятся к усовершенствованным покрытиям капитального типа, отвечающим современным требованиям автомобильного движения. Достаточная шероховатость обеспечивает надежное сцепление колес автомобиля. Срок службы цементобетонных покрытий составляет до 30 лет.
Цементобетонные покрытия устраиваются на дорогах преимущественно I и II категорий при весьма интенсивном и тяжелом движении, особенно в районах, недостаточно обеспеченных местными каменными материалами.
Основания для цементобетонных покрытий выполняются из щебня, гравия, песка, а также из грунта, укрепленного вяжущими материалами (цементом, битумом). Толщина цементобетонных покрытий определяется расчетом и колеблется в пределах 18−24 см.
Цементобетонные покрытия разделяются на сборные и монолитные. Сборные покрытия устраивают из плит, изготовленных на заводах железобетонных изделий; монолитные покрытия выполняются из бетона, укладываемого в покрытие непосредственно на дороге.
Преимуществами цементобетонных покрытий являются высокая прочность, износостойкость, ровность, шероховатость. В отличие от асфальтобетонных покрытий, являющихся выравнивающими, цементобетонные покрытия являются еще и несущими нагрузку от автотранспорта.
Слабым местом этих покрытий являются температурные швы, которые устраивают для компенсации изменения длины при колебаниях температуры. Через швы при недостаточной гидроизоляции может проникнуть вода в основание, плиты теряют контакт с грунтом, под ними вначале возникают полости, а затем плиты разрушаются.
При строительстве монолитного цементобетонного покрытия бетонная смесь на подготовленное основание укладывается комплектом машин. В середине прошлого века такой комплект машин выполнялся на рельсовом ходу. В состав рельсового комплекта входили рельс-формы, изготовленные из специального профиля, листовой стали и узкоколейного рельса длиной 4 м каждый, которые укладывались в две нитки длиной 1 километр.
В дальнейшем отказ от трудоемких операций по монтажу и демонтажу рельс-форм привел к созданию комплектов безрельсовых машин на гусеничном ходу.
По зарубежным данным, применение безрельсовой технологии строительства покрытий позволяет получить экономический эффект в размере 4000−5000 долларов США на 1 км, повысить темп строительства покрытий до 2 км в смену и более. Например, при строительстве дороги № 1−8 в Калифорнии в 1971 году за 20-ти часовой рабочий день было уложено с помощью гусеничного бетоноукладчика «Автогрейд» 5,13 км бетонного покрытия толщиной 21 см (8310 м бетона).
В нашей стране создан безрельсовый комплект машин ДС-110, дающий возможность в едином потоке осуществлять профилирование дорожного полотна, устройство и отделку покрытия со средним суточным темпом примерно в пять раз превышающим темп работ с применением колесно-рельсовых машин. Среднесуточный геми работ составляет 1500 погонных метров дорожного полотна шириной 8,5 м.
В состав комплекта входят три основные гусеничные машины (рис. 5.1): профилировщик земляного полотна и оснований ДС-108 7, бетонораспределитсль ДС-109 2 и бетоноукладчик ДС-111 5, а также две машины на пневмоходу для отделки и ухода за свежеуложенной бетонной смесью: трубчатый финишер ДС-104А 4 и машина для устройства шероховатой поверхности и нанесения пленкообразующих материалов ДС-105А.
5.
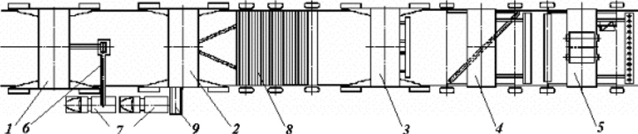
Рис. 5.1. Комплект машин на гусеничном ходу ДС-110.
Кроме того, в состав комплекта входит навесное и прицепное оборудование для выполнения вспомогательных технологических операций: подвешенный к профилировщику конвейер-перегружатель ДС-98А 6 для удаления излишков материала на обочину или в автосамосвал 7; тележка для перевозки арматурных сеток ДС-103А 8, прицепляемая к распределителю; погружатсль арматурной сетки в цементобетонную смесь ДС-102А, присоединяемый к бетоноукладчику; асфальтоукладочное оборудование ДС-106А профилировщика или распределителя.
В комплект входят два трейлера ДС-107 грузоподъемностью 40 т для перевозки машин комплекта.
С комплектом машин ДС-110 используют нарезчики и заливщики швов.
Для нормальной работы комплекта производительностью не менее 1 км в день на строительстве должен работать цементобетонный завод с двумя бетоносмесительными установками СБ-109А (производительностью 135 м /ч каждая) или с одной установкой СБ-118 (производительностью 240 м/ч). Эти передвижные установки непрерывного действия готовят цементобетонные смеси с осадкой конуса не менее 1 см, крупностью заполнителей до 70 мм.
Все машины комплекта максимально унифицированы между собой по ходовой части, гидроприводу и системе автоматики.
Базой профилировщика, бетонораспределителя и бетоноукладчика служит унифицированное четырехопорное гусеничное шасси с автоматической следящей системой, на котором оборудуют рабочие органы той или другой машины (рис. 5.2).
На основной раме 14 сварной конструкции размещены силовая установка /, пульт управления /3 и кабина оператора. Рама при помощи консольных опор /0 соединяется шарнирно с гусеничными тележками 9.
Изменение направления движения машины осуществляется одновременным поворотом передних и задних гусеничных тележек. Для соблюдения необходимых в поворотной паре углов поворота каждой тележки их вилки соединены механизмом рулевой трапеции.
Передняя или задняя пара тележек поворачивается гидроцилиндром, закрепленным на основной раме, через тяги. Гидроцилиндрами поворота передних или задних гусеничных тележек можно управлять дистанционно с пульта управления или автоматически щуповыми преобразователями курса машины 5 по направлению натянутого вдоль дороги шнура 7.
Гусеничные тележки выполнены одинаковой конструкции и различаются только правым и левым исполнением. Каждая тележка является ведущей и приводится в движение от гидромотора, питаемого от насоса переменной производительности. Крутящий момент от гидромотора передается на ведущее зубчатое колесо гусеницы через планетарный редуктор и цепную передачу.
Гусеничные тележки длиной 3 м и шириной 0,4 м обеспечивают высокую проходимость машине по земляному полотну строящейся дороги.
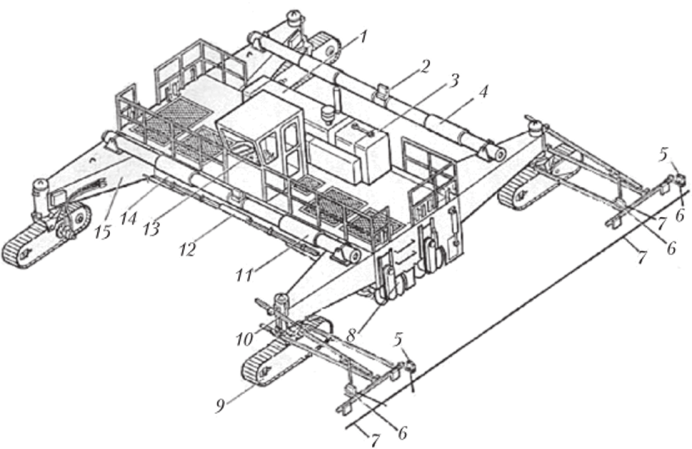
Рис. 5.2. Унифицированное четырехопорное гусеничное шасси 1 — силовая установка; 2 — преобразователь поперечного уклона; 3 — бак; 4, 11 — алюминиевые трубы; 5 — преобразователи курса движения; 6 — преобразователи продольного профиля; 7 — шнур; 8 — рабочие органы; 9 — гусеничная тележка; 10 — консольная опора; 12 — гидроцилиндр; 13 — пульт управления; 14 — рама; 15 — опора.
Скорость передвижения гусеничных тележек (2…54 м/мин) регулируется оператором с дистанционного пульта управления.
Машина оборудована механизмом самопогрузки (рис. 5.3). Консольная опора 2 гусеничного шасси шарнирно соединена с основной рамой 1 в трех точках: двумя нижними проушинами 6 с пальцами, штоком гидроцилиндра самопогрузки 7. Шарнирное крепление опор к основной рамс позволяет с помощью гидроцилиндров самопогрузки поднимать на высоту h" и опускать основную раму для погрузки машины на платформу трейлера. На короткие расстояния машины перевозят без разборки, на дальние — консольные опоры демонтируют вместе с гусеничными тележками 3.
Выравнивание основной рамы относительно направляющего капронового шнура производится с помощью гидроцилиндров 4 стабилизации уровня, штоки которых шарнирно соединены с гусеничными тележками вилками 5.
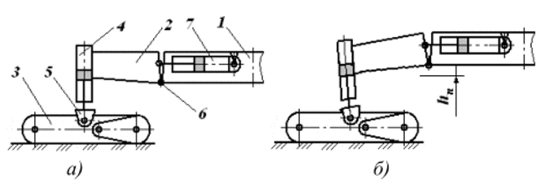
Рис. 5.3. Схема механизма самопогрузки: а — рабочее положение; б — положение самопогрузки Трубчатый финишер ДС-104А 4 и машина для устройства шероховатой поверхности и нанесения пленкообразующих материалов ДС-105А 5 (рис. 5. 1) смонтированы на унифицированном самоходном четырехколесном базовом шасси. Каждое колесо является поворотным и ведущим с приводом от индивидуального гидромотора через цепную передачу.
Профилировщик основания ДС-108 предназначен для планировки верхнего слоя уплотненного земляного полотна, а также отделки профиля основания из грунтов, укрепленных вяжущими материалами (рис. 5.4). В нижней части рамы 1 установлено рабочее оборудование, включающее шнек-фрезу 2, шнек 3, передний 4 и задний 5 отвалы.
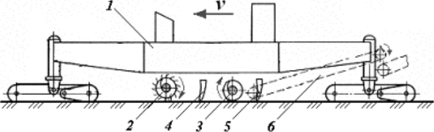
Рис. 5.4. Схема рабочих органов профилировщика основания ДС-108.
Шнек-фреза предназначена для первоначального фрезерования, рыхления и распределения фунта основания по ширине обрабатываемой полосы. Она состоит из двух автономных частей — правой и левой — длиной по 4300 мм и диаметром 762 мм (рис. 5.5).
Каждая часть шнек-фрезы выполнена из стальной трубы, на наружной поверхности которой приварены 50 стоек с держателями зубьев фрезы и шнековые лопасти правой или левой навивки. Левая (по ходу профили ровщика) часть фрезы имеет правое винтовое направление зубьев и ленты, а правая часть — левое.
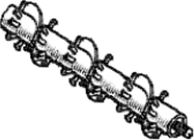
Рис. 5.5. Левая часть шнек-фрезы профилировщика основания ДС-108.
щий из двух частей, расположенных после шнек-фрезы, предназначен для предварительного профилирования основания, перемещения и равномерного распределения материалов.
Такое расположение зубьев и шнека позволяет производить встречное фрезерование поверхности с одновременным перемещением излишков грунта от центра профилировщика к краям.
Передний отвал, состоя;
Шнек также состоит из двух частей и предназначен для удаления излишков грунта на обочину дороги или на ленту конвейера-перегружателя, а также распределяет материал по ширине основания. Длина каждой из автономных частей 4300 мм, диаметр — 762 мм.
Задний отвал, состоящий из двух частей, расположенных за шнеками, окончательно профилирует поверхность. Задний отвал имеет дополнительно уширители, перемещаемые гидроцилиндром по направляющим, а также створки (в конце отвала), открывающие окно для удаления излишков грунта на продольный конвейер б (см. рис. 5.4), а с него — на конвейерперегружатель 6 (рис. 5.1).
Каждая половина шнек-фрезы и шнека имеет свой независимый и взаимозаменяемый привод, состоящий из гидромотора, планетарного редуктора и цепной передачи.
Положение фрез, шнеков, передних и задних отвалов изменяется гидроцилиндрами и контролируется с помощью указателей заглубления.
Бетонораспределитель ДС-109 предназначен для приема бетонной смеси из транспортных средств со стороны обочины и равномерного распределения на 7,3 м по ширине строящегося покрытия. Машину можно применять вместо профилировщика, но с меньшей производительностью.
Рабочее оборудование состоит из шнек-фрезы 1 и отвала 2, прикрепленных снизу к основной раме (рис. 5. 6). Конструкция шнек-фрезы и его привода аналогична конструкции шнек-фрезы профилировщика.
Шнек-фреза рас предел яет цементобетонную смесь, выгруженную на основание конвейером. Слой смеси окончательно планируется вторым распределительным рабочим органом — дозирующим отвалом, состоящим, как и шнек-фреза, из двух секций.
К боковым листам рамы подвешены скользящие формы, ограничивающие ширину распределения цементобетонной смеси.
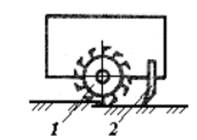
Рис. 5.6. Схема рабочих органов бетонораспределителя ДС-109.
Конструкция рабочих органов позволяет регулировать положение их краев и середины при помощи гидроцилиндров для получения однои двухскатного профиля покрытия.
Машина оснащена выдвижным конвейером 9 длиной 7200 мм, шириной 1520 мм (см. рис. 5.1). Нижняя часть конвейера образует дно приемного бункера вместимостью 3 м³ с выдвижением на обочину за габарит машины на 2,7 м для приема бетонной смеси из автосамосвалов с задней разгрузкой. Поперечное перемещение перегрузочного конвейера осуществляется канатно-блочной системой с помощью гидроцилиндра. Выдвигается конвейер в положение загрузки за 7 секунд.
В прицепе к распределителю бетона предусмотрена арматурная тележка ДС-103 (см. рис. 5.1, поз. 8). Арматурную сетку грузят на тележку автокраном, а снимают и раскладывают на бетонной смеси вручную.
Бетоноукладчик ДС-111 со скользящими формами уплотняет цементобетонную смесь, уложенную распределителем, или распределяет и уплотняет бетонную смесь, привезенную автосамосвалами и выложенную на основание перед бетоноукладчиком. Кроме того, он осуществляет полуавтоматическую закладку стержней по оси покрытия и с боков для соединения бетонируемых полос, а также оборудован нарезчиком, с помощью которого устраивает продольный шов в свежеуложенной смеси с заполнением его гидроизолирующей лентой.
Смесь распределяется по ширине шнековым распределителем I (рис. 5.7), состоящим из двух независимых частей с левой и правой навивкой винтовых лопастей. Каждая часть имеет длину 3658 мм и диаметр по виткам 457 мм. Секции снабжены независимым приводом от реверсивного гидромотора через планетарный редуктор.
Дозирующий брус 2 расположен за шнеком и служит для регулирования толщины слоя бетонной смеси. Кроме того, он создает подпор смеси в шнеке, способствуя осевому перемещению излишков смеси. Дозирующий брус с помощью четырех гидроцилиндров связан с поперечной балкой и может профилировать двухскатный профиль.
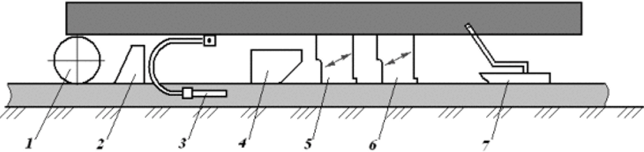
Рис. 5.7. Схема рабочих органов бетоноукладчика ДС-111.
Глубинные вибраторы 3 являются основным оборудованием для уплотнения бетонной смеси, во многом определяющим дальнейшее качество покрытия. Они позволяют полностью прорабатывать смесь с осадкой конуса не менее 2,5 см по всей ширине укладываемой полосы. 9−14 глубинных вибраторов закрепляют на поворотной трубе на расстоянии 0,60 — 0,53 м один от другого под углом 15° - 20° к горизонту при допускаемом расстоянии 5 — 6 см от нижней части корпуса до поверхности основания. Глубинный вибратор представляет собой герметичный корпус, в котором размещен электродвигатель, приводящий во вращение эксцентриковый возбудитель с частотой 180 Гц.
За глубинными вибраторами расположена двухсекционная виброзаслонка (вибробрус-дозатор) 4. На каждой части длиной 3750 мм установлено по два электромагнитных вибратора с вертикально направленными колебаниями частотой 50 Гц и амплитудой 0,02 — 0,03 мм. Назначение виброзаслонки состоит во вторичном распределении и выравнивании смеси после ее проработки глубинными вибраторами.
Над камерой глубинных вибраторов установлена распределительная труба для введения воды в смесь. В средней части камеры установлено оборудование для запрессовки в бетонную смесь штырей продольного шва. Аналогичное устройство установлено сбоку камеры глубинных вибраторов для запрессовки Г-образных штырей в боковую поверхность покрытия для соединения смежных полос покрытия.
Виброзаслонка окончательно дозирует слой проработанной глубинными вибраторами смеси с одновременным вибрированием его поверхности для получения верхнего тонког о слоя цементного раствора. Такой слой уменьшает сопротивление передвижению двух следующих за виброзаслонкой качающихся брусьев 5 и 6 и тем самым сводит к минимуму образование на поверхности борозд от протаскивания средних и крупных фракций заполнителя бетонной смеси.
Передний и задний качающиеся брусья окончательно уплотняют смесь, формируют покрытие необходимого профиля и выглаживают поверхность. Брусья состоят из двух частей коробчатого сечения, каждая длиной 4000 мм. Возвратно-поступательное движение брусьев в поперечном направлении относительно укладываемого покрытия осуществляется механизмом, состоящим из гидромотора, планетарного редуктора, кривошипного вала и толкающих кулис.
Окончательная отделка поверхности производится плавающей плитой 7, состоящей из двух частей, каждая из которых имеет длину 3750 мм и ширину 61 см. В рабочем положении плавающая плита скользит по поверхности покрытия иод действием силы тяжести, в транспортное положение поднимается гидроцилиндрами.
Боковые скользящие формы формируют боковые поверхности бетонного покрытия. Эти формы в верхней части шарнирно прикреплены к раме и отводятся в стороны тремя гидроцилиндрами с каждой стороны машины.
Бетоноотделочная машина (трубчатый финишер) ДС-104А предназначен для окончательной отделки поверхности покрытия. Машина работает челночным способом непосредственно за бетоноукладчиком, совершая проходы вперед и назад до качественного выглаживания поверхности. Машина монтируется на четырехколесном базовом шасси (рис. 5.8).
Выглаживающая труба / является основным рабочим органом финишера и представляет собой алюминиевую трубу диаметром 203 мм, состоящую из двух секций длиной 6100 мм. Секции предназначены для отделки двухскатного покрытия.
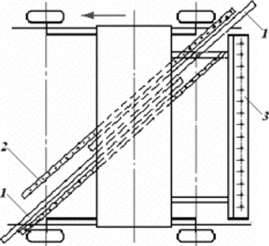
Рис. 5.8. Схема рабочих органов трубчатого финишера ДС-104.
Труба прикреплена к траверсе с помощью скоб и цепей, обеспечивающих свободное перемещение трубы относительно траверсы. Трубы не имеют возможности перекатываться по поверхности покрытия, передают на бетонную смесь только силу тяжести. Над ними установлены два трубопровода 2 с 21 соплом на каждом для смачивания алюминиевых труб.
Сзади к рамс кронштейнами прикреплена тканевая драга 3, которая орошается водой и передвигается по поверхности цементобетонного слоя.
Распределитель пленкообразующих материалов ДС-105А представляет собой машину производительностью до 1500 погонных метров в смену, которая в комплекте следует за финишером (рис. 5.9).
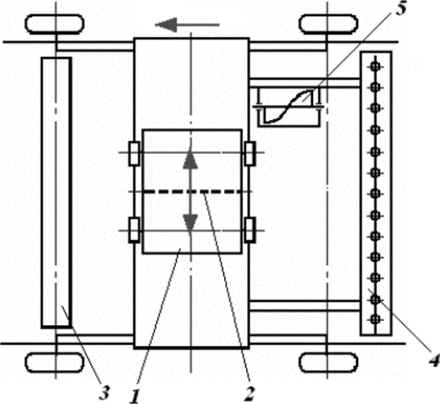
Рис. 5.9. Схема рабочих органов распределителя пленкообразуюших материалов ДС-105А.
По направляющим в поперечном направлении перемещается каретка /, к нижней части которой через цепи и пружины присоединена швеллерная балка со щеткой 2 длиной 3000 мм. Такое соединение позволяет удерживать щетку в вертикальном положении и обеспечивать некоторую свободу ее перемещения относительно каретки. Каретка перемещается в обе стороны тяговыми канатами, ведущие блоки приводятся во вращение от гидромотора через цепную передачу.
Спереди к раме на двух шарнирных кронштейнах подвешены распылительное устройство 4 для нанесения пленкообразующей жидкости, закрытое кожухом, и два выносных сопла для обработки боковых поверхностей.
Работа машины начинается с нанесения борозд шероховатости на поверхность цементобетонного покрытия приблизительно через 40 минут после укладки смеси. Машина работает циклично, перемещаясь вперед на следующую захватку с учетом обязательного перекрытия новой зоны работы щетки с уже обработанной частью полосы покрытия. Если ширина обрабатываемой части полосы за проход щетки составляет 3000 мм, то машину перемещают на 2900 мм.
После нанесения борозд шероховатости машину возвращают к началу участка. В начале каждой смены пленкообразующую жидкость (помароль) доставляют в бочках и расставляют их вдоль участка через 100 — 150 м. Затем насосом машины помароль перекачивают в бак с одновальным лопастным смесителем 5. После наполнения бака опускают навесное распылительное устройство так, чтобы наконечники сопел находились над обрабатываемой поверхностью на расстоянии 40 — 50 см. Расход помароли составляет 400 — 1000 г/м2 в зависимости от температуры и скорости ветра.
При отсутствии пленкообразующей жидкости, а также для укрытия свежеуложенного покрытия при дожде машина снабжена устройством для намотки и размотки полиэтиленовой пленки 3.
Машины для нарезки швов. Во избежание растрескивания цементобетонных покрытий в связи с появлением напряжений в них в период твердения и эксплуатации, в покрытиях через определенное расстояние нарезаются температурные швы расширения и сжатия. Глубина швов сжатия должна быть не менее 1А толщины покрытия, а продольных швов — не менее 1/3 толщины.
Нарезка паза деформационных швов может осуществляться в свежеуложенном бетоне по окончании отделки покрытия, или в затвердевшем бетоне в начальный период его твердения при достижении бетоном 20 — 30% проектной прочности через 8−12 часов после отделки покрытия. Для каждого способа нарезки швов применяют свои машины.
Рабочими органами машин, нарезающих швы в свсжеуложснном бетоне, являются виброножи с механизмом подъема и опускания для нарезки поперечных швов и вибродиски — для продольных швов.
Вибронож (рис. 5.10, а) представляет собой балку 4 из двух швеллеров с укрепленной между ними и выступающей вниз стальной полосой 2, являющейся режущей кромкой ножа. На верхней площадке 3 установлены вибраторы 1 кругового действия.

Рис. 5.10. Схемы рабочих органов нарезчиков швов.
Вибродиск для нарезки продольного шва (рис. 5.10, б) представляет собой диск 2, свободно вращающийся на оси. Диск установлен в кронштейне 3, на котором установлен вибратор /.
Основной недостаток нарезания швов в свежеуложенной смеси — нарушение структуры бетона в зоне шва, что приводит к его выкрашиванию. Кроме того, этот метод требует дополнительных ручных работ на исправление дефектов швов, качество которых не всегда отвечает требованиям, предъявляемым техническими условиями.
Нарезка швов в затвердевшем бетоне обеспечивает хороший внешний вид, точные геометрические очертания и ровное сопряжение поверхностей смежных плит, высокую ровность покрытия и долговечность бетона в зоне шва.
В качестве режущего инструмента используют карборундовые или алмазные диски диаметром 250 — 300 мм, вращающиеся со скоростью от 2200 до 3000 об/мин. Алмазные диски отличаются высокой прочностью и большей (в три раза) производительностью, чем корборундовыс диски.
В зависимости от температуры окружающего воздуха швы нарезают через 8−12 часов после схватывания.