Основные требования и меры безопасности при литье под давлением, по выплавляемым моделям и в кокиль
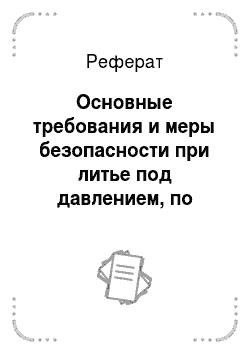
Наиболее трудоемкой и сложной из этих операций является заливка жидкого металла. Автоматически работающие машины для литья под давлением имеют специальные заливочно-дозирующие устройства. Очистку поверхности раскрытых пресс-форм проводят обдувкой сжатым воздухом и металлическими щитками, перемещаемыми пневматическими устройствами. Смазка после очистки наносится распылением специальными… Читать ещё >
Основные требования и меры безопасности при литье под давлением, по выплавляемым моделям и в кокиль (реферат, курсовая, диплом, контрольная)
Изготовление отливок литьем под давлением
В соответствии с ГОСТ 10 580–2006 [2.3] оборудование для литья под давлением (ЛПД) включает в себя:
- — машины для литья под давлением;
- — манипуляторы для заливки металла, удаления отливок, смазки пресс-форм;
- — гибкие модули для литья под давлением.
При проведении литейных работ на данном оборудовании наиболее вероятно воздействие на работников следующих опасных и вредных факторов:
- — незащищенные подвижные части оборудования;
- — острые кромки и шероховатости на поверхности заготовок, деталей оснастки и инструмента;
- — повышенное напряжение в электрической цепи оборудования;
- — повышенная температура поверхности оборудования и материалов (более 45°С) и возможность получения термических ожогов;
- — пожарная опасность;
- — возможность травмирования работников при случайном доступе в зону работы манипулятора;
- — возможность создания давления в цилиндре прессования до закрытия пресс-формы;
- — повышенное содержание вредных паров и аэрозолей в воздухе рабочей зоны;
- — повышенный уровень шума;
- — повышенный уровень электромагнитных излучений от нагревательных устройств;
- — повышенный уровень инфракрасного излучения;
- — повышенные физические нагрузки (тяжесть труда).
На самом первом этапе работ оценку опасности риска проявления этих и других факторов при реализации технологии рекомендуется проводить по методике, приведенной в гл. 7.
Помещение, в котором эксплуатируются машины для литья под давлением, должно иметь не менее двух выходов. На рис. 18.1—18.3 приведено несколько схем выполнения литья разными способами с указанием некоторых элементов защиты, которые надо устанавливать на оборудовании в соответствии с требованиями норм. Эти схемы помогут лучше понять необходимость выполнения требований безопасности, которые приведены ниже.
Пресс-формы перед запрессовкой металла должны быть просушены и подогреты до температуры, установленной в технической документации. Перед каждой запрессовкой металла пресс-формы следует очищать от посторонних включений с помощью специальных приспособлений, исключающих попадание человека в опасную зону. Реле времени на кристаллизацию отливки должно быть настроено на время, достаточное для затвердевания пресс-остатка. При необходимости осмотра и обслуживания пресс-форм со стороны, противоположной рабочему месту оператора, машина отключается.

Рис. 18.1. Схема процесса литья на установке литья под низким.
давлением:
- 1 — тигель с расплавом металла; 2 — металлопровод; 3 — камера тигля;
- 4 — металлическая форма; 5 — отливка; 6 — воздуховод; 7 — герметизирующая
крышка; 8 — нагреватели Со стороны, противоположной рабочему месту, в зоне нахождения пресс-формы должна быть установлена вертикальная вентиляционная панель или поворотный зонт сверху машины для вытяжки вредных паров и газов с отсосом воздуха в количестве не менее 3600 м3/ч с каждого квадратного метра панели. Если выделяется небольшое количество вредных веществ, то при проведении анализа риска от вредных веществ в карте экспертной оценки надо отметить, что установка местных отсосов не требуется. Форма для анализа возможных вредных факторов приведена в табл. 7.1.

Рис. 18.2. Схема технологии литья колесного диска из алюминия под низким давлением и приборы контроля температуры и давления.
Для дозированной подачи расплавленных сплавов следует применять устройства, исключающие пролив расплава или разбрызгивание во время выдачи доз. Подогрев тигельных раздаточных печей для машин литья под давлением следует проводить электрическим током или газом. При этом газовые горелки следует оснащать устройствами контроля пламени и предохранителем дефицита газа. Перед заливкой металла в автоклав крышка автоклава должна быть закрыта и закреплена. Во избежание выбросов расплавленного металла не допускается забрасывать «холодные» отходы (литники, брак отливок) в тигель раздаточной печи. Температура загружаемых отходов устанавливается технологическим процессом, утвержденным в установленном порядке. Загрузку металла в тигель следует проводить медленным опусканием при выключенной печи.
Между раздаточной печью и машиной следует устанавливать отбортованные в сторону машины металлические щиты высотой не менее 2 м или другие средства защиты зеркала расплавленного металла. Между соседними машинами должны быть установлены щиты из листовой стали не короче машины и не менее 2 м по высоте или другие средства защиты от разбрызгивания металла. Расстояние между щитом и машиной со стороны обслуживания должно быть не менее 2 м. Это надо учесть при разработке планировки размещения оборудования и обеспечить необходимый удобный доступ к местам периодического контроля.
Используемые в гидросхемах (гидроприводах) оборудования жидкости должны быть трудновоспламеняемыми. Рекомендуется использовать вместо минерального масла водно-эмульсионные и другие неорганические негорючие жидкости.

Рис. 18.3. Схема технологии литья под давлением на машине с горячей.
камерой прессования:
а — исходное положение; б — запрессовка металла в пресс-форму; в — извлечение отливки; 1 — тигель с расплавом металла; 2 — камера прессования;
- 3 — прессующий поршень; 4 — металлопровод; 5 — неподвижная часть прессформы; 6 — подвижная часть пресс-формы; 7 — плита толкателей; 8 — отливка;
- 9 — гидроцилиндр механизма прессования; 10 — система нагрева расплава
При литье под давлением наиболее опасной зоной является место соединения матриц пресс-форм (позиции 5, 6, 7 на рис. 18.3), так как при неплотном их запирании возможен выплеск расплава. Специальные запорные устройства, замки кокилей и пресс-форм должны обеспечивать плотное соединение матриц и надежное их запирание. Для предупреждения несчастных случаев эта зона должна закрываться предохранительным щитком, устанавливаемым на формодержателе или на одной из матриц пресс-формы.
Работа на машинах литья под давлением допускается при наличии:
- — блокировки от произвольного запирания при монтаже прессформы и при обслуживании машины;
- — блокировки подачи рабочего давления при раскрытой прессформе;
- — блокировки раскрытия пресс-формы;
- — блокировки при удалении металлических стержней и отливки из раскрытой пресс-формы при наличии рабочего давления над зеркалом расплава;
- — клапана аварийного ручного сбрасывателя давления;
- — защитных кожухов или щитов, перекрывающих зоны возможного случайного разбрызгивания расплавленного металла.
Важно также предусмотреть установку осушителей (влагоотделителей) сжатого воздуха или инертного газа, используемых для создания рабочего давления. Должна иметься аппаратура для обеспечения технологической выдержки отливки в пресс-форме. Наиболее правильно — установить вытяжную вентиляционную панель с отсосом воздуха не менее 2000 м3/ч с каждого квадратного метра панели. Нужно устройство, предотвращающее повышение давления газа в дозаторах и печах выше допустимого.
Горячие отливки возле машин следует складировать в специальную тару. Отливки следует удалять от машин транспортными средствами. Это важно учесть при расстановке оборудования на участке, при выборе необходимых расстояний до другого оборудования и мест для тары.
На рис. 18.4—18.6 приведены примеры установок литья под давлением и показаны некоторые важные меры и элементы защиты от травмирования подвижными частями оборудования, от поражения электрическим током, показано расположение рабочих мест, устройств удаления вредных веществ и т. д. Из приведенных на рис. 18.4—18.6 примеров оборудования видно, что литье под давлением является высокомеханизированным процессом. Управление рабочими органами машины при прессовании, удалении отливки осуществляют с пультов или при помощи рычажных механизмов. Вручную выполняют такие операции, как заливка дозы сплава в камеру прессования, очистка поверхности пресс-формы от тонких пленок металла, смазка поверхности пресс-формы и камеры прессования.
Наиболее трудоемкой и сложной из этих операций является заливка жидкого металла. Автоматически работающие машины для литья под давлением имеют специальные заливочно-дозирующие устройства. Очистку поверхности раскрытых пресс-форм проводят обдувкой сжатым воздухом и металлическими щитками, перемещаемыми пневматическими устройствами. Смазка после очистки наносится распылением специальными устройствами, работающими в автоматическом режиме. Участки очистки отливок ручным механизированным инструментом с абразивными кругами должны быть оборудованы местной вытяжной вентиляцией с устройством боковых пылеприемников, решеток в полу или верстаке.

Рис. 18.4. Пример расположения машин на участке литья под давлением с системой местной вытяжной вентиляции, с ограждением опасных зон, с тележками для транспортировки отливок.
Автоматизация машин и операций обрубки литников, очистки заусенцев позволяет создавать в цехах автоматические линии с участками для литья под давлением. Обрубку отливок проводят при температуре не выше 45 °C. Места обрубки и очистки отливок оборудуют постоянными или переносными ограждениями для защиты работающих от отлетающих осколков.

Рис. 18.5. Пример машины для литья под давлением алюминиевых сплавов со шкафом управления, пультом управления и защитой опасных зон.
Конструкцией ручных и педальных органов управления должно быть исключено их одновременное использование. Переключатель способов управления с ручного на педальный и наоборот следует устанавливать в запираемом шкафу. Допускается устанавливать этот переключатель вне шкафа при наличии в переключателе защитного замка или съемной рукоятки. Работа оборудования, выделяющего вредные вещества, должна быть сблокирована с работой вентиляционной системы так, что при неработающей вентиляционной системе должна исключаться работа оборудования.
Машины с автоматическим управлением при технологической необходимости должны обеспечивать возможность перехода на пооперационное (ручное) управление. Одновременное включение обоих режимов должно быть исключено. Центральный пульт управления следует оборудовать сигнализацией и (или) мнемосхемой, обеспечивающими информацию о работе оборудования, а также системой аварийного отключения. Автоматические линии (или другое оборудование с большим фронтом обслуживания) должны иметь пульты дистанционного (местного) управления, сблокированные с центральным пультом и обеспечивающие аварийное отключение каждой единицы оборудования. Допускается установка одного пульта на несколько единиц оборудования, полностью просматриваемых с этого пульта.

Рис. 18.6. Пример расположения литейных машин с холодной камерой.
прессования на участке литья под давлением. Показана реализация ряда мер по безопасности труда Аварийное отключение должно действовать независимо от работы электронного оборудования. В качестве сигнальных элементов для предупреждения об опасности следует применять звуковые и (или) световые сигнализаторы, установленные в зоне видимости обслуживающего персонала и различимые в производственной обстановке.
Пультовое помещение должно быть оборудовано телефонной связью с основными службами цеха, переговорной и (или) видеосвязью с отдельными участками цеха, где размещено оборудование, а также громкоговорящей связью. В пультовых помещениях также должны быть предусмотрены приточно-вытяжная вентиляция или кондиционирование, обеспечивающее рассредоточенную подачу, получение избыточного давления и параметры воздуха по ГОСТ 12.1.005—88. Ширина проходов в пультовых помещениях должна быть не менее 1 м, а площадь, не занятая оборудованием, — не менее 2 м2 на одного оператора; должно быть предусмотрено аварийное освещение.
На рис. 18.7 приведена схема удобного расположения оборудования на рабочем месте установки литья под давлением. По такой же схеме надо действовать и при реализации других технологий на другом оборудовании.
Очень важным при этом является обеспечение безопасных проходов, проездов, свободного доступа к оборудованию и надежной защиты рабочего от возможности получения травм. При выборе расстояний между оборудованием, стеллажами, проходами, показанными на рис. 18.7, учитывались требования, приведенные в ч. II пособия и следующие дополнительные рекомендации для литейных цехов: ширина литейного помещения при расположении оборудования в два ряда — не менее.
- 12 м; расстояние между литейными машинами — 3—4 м (в зависимости от размеров машин); расстояние от печи до машины — 0,5—1,5 м; минимальная ширина прохода для подноски металла — 2 м; расстояние между щитом ограждения и машиной со стороны обслуживания не менее 1,5 м; расстояние от стены или щита до машины с торцовой стороны — не менее 1 м; высота стальных защитных щитов — не менее
- 2,5 м. Эти щиты видны на рис. 18.4. Ширина защитных щитов, устанавливаемых вдоль машин, между наружной стороны, должна быть больше длины машины на 0,4—0,6 м.

Рис. 18.7. Вариант схемы рационального расположения оборудования на рабочем месте литья под давлением
На рис. 18.7 показано, что к пусковой аппаратуре насоса 1 и к запорному вентилю аккумулятора 2 обеспечен свободный подход. Для защиты литейщика (позиция 5) от внезапного выброса металла из формы служат щиты 6, которые должны быть переносными и устанавливаться в наиболее опасных местах. Наиболее удобным можно считать расположение раздаточной печи 3 со стороны камеры прессования машины 4. Расстояние между краем печи и наиболее выступающими частями машины — около 500 мм; вторая ось печи может быть смещена на 250 мм от центра машины в сторону рабочего места литейщика 5. Высота печи над уровнем пола должна быть не более 800 мм, чтобы рабочему была удобно зачерпывать металл.
На рис. 18.8 приведен еще один вариант правильной организации рабочего места. Рабочее место литейщика находится непосредственно у машины 8, на которую устанавливают пресс-форму 4 для получения отливки.

Рис. 18.8. Пример другого варианта организации рабочего места литейщика на машине литья под давлением.
С правой стороны от машины расположена раздаточно-подогревательная печь 5. Пусковая аппаратура насоса 22 и аккумулятор 2 расположены за машиной и не мешают свободному проходу рабочего. С обеих сторон от машины установлены защитные экраны 3. Щипцы для захвата отливок, разливочные ложки, банки со смазкой хранят в специальном шкафу 9. Во время работы рабочие пользуются смазкой, которая находится в бачке 6. Щит с приборами 10, контролирующими технологический процесс, расположен так, чтобы литейщику было удобно вести контроль. На рабочем месте установлен ящик 7 или стеллаж для хранения готовых отливок, а также ящик для сборки отходов. Рабочее место оборудовано местным освещением и эффективной местной вытяжной вентиляцией 2. Расплав из плавильного отделения в раздаточно-подогревательные печи подают вспомогательные рабочие-разливщики. Устанавливают пресс-форму на машину и налаживают ее слесари-ремонтники и наладчики, обслуживающие оборудование цеха. Отливки в процессе литья через небольшие промежутки времени проверяют контролеры.