Комплексная обработка глубоких отверстий переменного сечения в деталях из легких сплавов
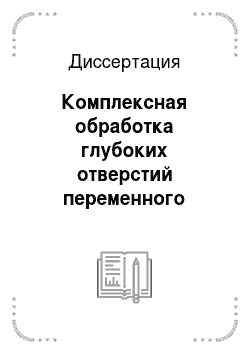
Диссертация
При обработке различных материалов способ гибридной обработки арматуры (ГОА) обладает рядом преимуществ перед традиционными технологическими методами получения отверстий. При исследованиях процессов получения глубоких каналов было доказано, что при ультразвуковой интенсификации анодного растворения арматуры возможна обработка отверстий с минимальным диаметром 8−10 мкм при соотношении глубины… Читать ещё >
Содержание
- ГЛАВА 1. СОВРЕМЕННЫЕ ТЕХНОЛОГИЧЕСКИЕ ПРОБЛЕМЫ ОБРАБОТКИ ГЛУБОКИХ ОТВЕРСТИЙ В ЛЕГКИХ СПЛАВАХ
- 1. 1. Виды деталей из легких сплавов
- 1. 2. Механическая обработка
- 1. 3. Физико-технические методы обработки
- 1. 4. Гибридные методы обработки
- 1. 4. 1. Гибридная обработка металлической формирующей арматуры
- 1. 4. 2. Технологические сложности реализации способа ГО А, выбор метода окончательной обработки
- 1. 4. 3. Особенности моделирования ГОА в матрицах с высокой проводимостью
- 2. 1. Разработка общих методологических положений
- 2. 2. Методика проведения теоретических и экспериментальных исследований
- 2. 3. Этапы проведения теоретических и экспериментальных исследований
- 2. 3. 1. Физическое моделирование процессов анодного растворения арматуры в матрицах из алюминиевых сплавов при интенсификации процесса УЗП
- 2. 3. 2. Математическое моделирование процесса на основе разработанных физических моделей
- 2. 3. 3. Исследование анодного растворения электропроводящих материалов арматуры и матрицы в УЗП
- 2. 3. 4. Исследование процессов окончательной обработки матриц
- 2. 3. 5. Разработка комплексных технологических процессов
- 3. 1. Моделирование движения анодной границы
- 3. 1. 1. Моделирование воздействия кавитации на процесс движения анодной границы
- 3. 1. 2. Влияние геометрических характеристик отверстия на процесс ГОА
- 3. 1. 3. Взаимовлияние термодинамических свойств электролитов на процесс развития кавитации при растворении арматуры
- 3. 1. 4. Влияние видов кавитации на моделирование ГОА
- 3. 2. Система модельных коэффициентов и их численное выражение
- 3. 3. Математическое моделирование процессов ГОА
- 3. 3. 1. Определение общего дифференциального уравнения процесса ГОА
- 3. 3. 2. Моделирование процесса предельного движения анодной границы
- 4. 1. Определение технологических условий ГОА
- 4. 2. Определение диапазона пассивации матриц из алюминиевых сплавов
- 4. 3. Рабочие режимы растворения арматуры в нейтральных электролитах
- 4. 4. Рабочие режимы растворения арматуры в щелочных электролитах
- 4. 5. Рабочие режимы растворения арматуры в легких сплавах
- 4. 6. Проверка адекватности математической модели
- 5. 1. Производство армированных заготовок
- 5. 2. Определение и корректировка технологических режимов. ИЗ
- 5. 3. Маршрутные комплексные технологические процессы
- 5. 4. Физическое и математическое моделирование процессов окончательной обработки матриц
- 5. 5. Определение режимов окончательной фрезерной обработки матриц из алюминиевых сплавов
Список литературы
- Алюминиевые сплавы. Применение алюминиевых сплавов. Справочное руководство / Редакционная коллегия И. В. Горынин и др.- Москва.: «Металлургия», 1978.-267 с.
- Алюминиевые сплавы (свойства, обработка, применение) / Пер. с нем.- Под ред. М. Е. Дрица.- М.: Металлургия, 1989. 680 с.
- Антропов А.И. Теоретическая электрохимия / А. И. Антропов. М.: Высшая школа, 1969. — 348 с.
- Аппен A.A. Температуроустойчивые неорганические покрытия / A.A. Аппен. Л.: Химия, 1977. — 381 с.
- Араманович И.Г. Уравнения математической физики / И.Г. Арамано-вич, В. И. Левин. М.: Наука, 1964. — 288 с.
- Аранцев В.А. Электрохимическая обработка отверстий с малыми размерами сечений и отверстий повышенной глубины / В. А. Аранцев // Прогрессивные электрофизические и электрохимические методы обработки. Саратов, 1979.- С.31−33.
- Балыпин М.Ю. Научные основы порошковой металлургии и металлургии волокна / М. Ю. Балыпин, С. С. Кипарисов.- М.: Металлургия, 1978. -184 с.
- Бартл Д. Технология химической и электрохимической обработки поверхностей / Д. Бартл, О. Мудрох. М.: Машиностроение, 1991. — 712 с.
- Белый В.А. Металлополимерные материалы и изделия / В. А. Белый, Н. И. Егоренков, Л. С. Корецкая.- М.: Химия, 1979. 310 с.
- Бернштейн М.Л. Термомеханическая обработка металлов и сплавов / М. Л. Бернштейн.- М.: Металлургия, 1968. Т. 1. 596 е.- Т. 2. 597 с.
- Бойко А.Ф. Высокочастотное электроэрозионное прошивание отверстий малого диаметра / А. Ф. Бойко // Электронная обработка материалов.1980. № 1,-С. 86−88.
- Бобринец А.Н. Размерная электрохимическая обработка металлических пленок на диэлектрическом основании: Дис. канд. техн. наук (05.03.01. процессы механической и физико-химической обработки, станки и инструмент) / А. Н. Бобринец. — Тула, 1981. — 216 с.
- Брабец Б.И. Проволока из тяжелых и цветных металлов / Б.И. Бра-бец. М.: Металлургия, 1984. — 296 с.
- Васильев A.A. Технологические возможности и закономерности многоэлектродной электроэрозионной-электрохимической обработки отверстий: Дис. канд. техн. наук. 05.03.01. Тула, 1980. 214 с.
- Вероман В.Ю. Ультразвуковая обработка материалов / В.Ю. Веро-ман, А. Б. Аренков. Л.: Машиностроение, 1971. — 167 с.
- Витязь П.А. Разработки белорусского республиканского НПО порошковой металлургии в области новых материалов и технологий, их использование в машиностроении / П. А. Витязь, Е. В. Звонарев // Порошковая металлургия (Киев), 1993. № 6. — С. 4 — 16.
- Владимиров B.C. Уравнения математической физики/В.С.Владимиров. М.: Наука, 1981. — 512 с.
- Гайдученко Э.И. Электроэрозионная обработка отверстий малых диаметров / Э. И. Гайдученко. JI., 1967. 173 с.
- Гинберг A.M. Ультразвук в химических и электрохимических процессах машиностроения / A.M. Гинберг. М.: Машгиз, 1962. — 107 с.
- Григорьев В.А. Интенсификация виброабразивной обработки деталей с наложением электрохимического процесса / В. А. Григорьев // Алмазная и абразивная обработка деталей машин и инструмента. Пенза, 1981. — С. 44 — 45.
- Гопиенко В.Г. Способы производства порошковой продукции из алюминия и его сплавов / В. Г. Гопиенко.- JL: ЛДНТП, 1980. 20 с.
- Грилихес С.Я. Защитно-декоративные покрытия алюминия / С. Я. Грилихес. Л.: ЛДНТП, 1990. — 223 с.
- Грилихес С.Я. Обезжиривание, травление и пассивирование металлов / С. Я. Грилихес. Л.: Машиностроение, 1987. — 112 с.
- Гришина Е.П. Влияние свойств поверхностных пленок на технологические показатели процесса электрохимической обработки титановых сплавов: Автореф. дис. канд. техн. наук. 05.03.01. Кишинев, 1985. — 17 с.
- Давыдов А.Д., Анодное поведение металлов при электрохимической обработке / А. Д Давыдов, В. Д. Кащеев // Итоги науки и техники. 1977. — Т.9, Электрохимия. — ВИНИТИ. — С. 154−187.
- Дежкунов Н.В., Кувшинов Г. И., Прохоренко П. П. Захлопывание ка-витационных полостей между двумя стенками в ультразвуковом поле / Н. В. Дежкунов, Г. И. Кувшинов, П. П. Прохоренко // Акустический журнал. 1983. -Т.29, № 6. С. 754 — 757.
- Дикусар А.И. Электродные процессы и процессы переноса при электрохимической размерной обработке металлов / А. И. Дикусар, Г. Р. Энгель-гардт, В. И. Петренко, Ю. Н. Петров. Кишинев: Штиинца, 1983. — 207 с.
- Иванов Н.И. Разработка и исследование некоторых методов интенсификации прошивочных операций размерной электрохимической обработки: Дис. канд. техн. наук. 05.03.01. Тула, 1969. — 181 с.
- Ивенсен В.А. Феноменология спекания / В. А. Ивенсен. М.: Металлургия, 1985.-247 с.
- Кавтарадзе О.Н. Оборудование и оснастка, электроды-инструменты для электроискровой обработки с наложением ультразвуковых колебаний / О. Н. Кавтарадзе // Электронная обработка материалов. — 1984. № 4. С.70
- Заявка N413507 (Япония) МКИ В 23 В 51/00 Керамическое сверло с алмазным покрытием / О. Наоике, М. Хидэки, Т. Номура. 1992.
- Кипарисов С. С., Либенсон Г. А., Порошковая металлургия / С. С. Кипарисов, Г. А. Либенсон. М., 1972. — 218 с
- Клоков В.В. Электрохимическое формообразование / В. В. Клоков. -Казань, КГУ, 1984. 80 с.
- Клоков В.В. Моделирование процессов электрохимической размерной обработки и работы профессора Г.Г. Тумашева / В. В. Клоков // Маш. методы решения задач теории фильтрации: Тез. докл. 2 Респ. научно-техн. семин. -Казань, 1992. С.75−79.
- Кнэпп Р. Кавитация / Р. Кнэпп, Дж. Дэйли, Ф.Хэммит. пер. с англ. -М.: Мир, 1974.-688 с.
- Коваленко B.C. Обработка материалов импульсным излучением лазеров /В.С.Коваленко. Киев: Высшая школа, 1977. — 151 с.
- Коваленко B.C. Технология и оборудование электрофизических и электрохимических методов обработки материалов / В. С. Коваленко.- Киев: Вища школа, 1983. 176 с.
- Колачев Б.А. Металловедение и термическая обработка цветных металлов и сплавов / Б. А. Колачев.- М.: Металлургия, 1992. -480 с.
- Корчагин Г. Н. Определение области устойчивости процесса ЭХО / Г. Н. Корчагин // Электронная обработка материалов. 1973. — N1. — С. 9−10.
- Коровинский В.А. Обработка и доводка отверстий и пазов малых размеров сечений проволочным инструментом на электрохимических станках модели ДСФ/В.А.Коровинский // Электрофизические и электрохимические методы обработки. 1984. — № 2. — С.10−12.
- Косычев Ю.Н. Исследование процесса ЭХО малых отверстий / Ю. Н. Косычев, В. А. Монахов, В. Б. Батуров // Электрохимическая обработка в производстве деталей авиадвигателей. Куйбышев, 1981. — С. 52−58.
- Кошляков Н.С. Уравнения в частных производных математической физики / Н. С. Кошляков, Э. В. Глиннер, М. М. Смирнов, М.: Высшая школа, 1970.-712 с.
- Кречмар Э. Напыление металлов, керамики и пластмасс / Э.Кречмар. Пер. с нем.- М.: Машиностроение, 1986. 432 с.
- Курилов П.Г. Производство конструкционных изделий из порошков на основе железа / П. Г. Курилов, В. Н. Рыбаулин.- М.: Металлургия, 1992. -128 с.
- Лаворко П.К. Оксидные покрытия металлов / П. К. Лаворко.- М.: Машиностроение, 1993.- 186 с.
- Левинсон Е.М. Отверстия малых размеров (методы получения) / Е. М. Левинсон. Л.: Машиностроение, 1977. — 152 с.
- Либенсон Г. А. Основы порошковой металлургии / Г. А. Либенсон.-М. Металлургия, 1975.-200с.
- Манин М.И. Технологические характеристики ультразвуковой обработки твердых сплавов при совмещении с процессом анодного растворения / М. И. Манин, Б. Х. Мечетнер // Вып.1, М.: Машиностроение, 1966. С. 152−156.
- Марков А.И. Ультразвуковая обработка материалов / А. И. Марков. -М.: Машиностроение, 1980. 237 с.
- Маршаков И.К. Влияние ультразвукового поля на пассивное состояние некоторых металлов / И. К. Маршаков, В. К. Алтухов // Исследования по электроосаждению и растворению металлов.- М.: Наука, 1971. С. 40 47.
- Математическое моделирование. Процессы в нелинейных средах. -М.: Наука, 1986.-312 с.
- Материалы в машиностроении. Выбор и применение. М.: Машиностроение. Т.1. Цветные металлы и сплавы, 1987. 304 е.- Т.2.Конструкционная сталь, 1987. 496 е.- Т. З. Специальные стали и сплавы, 1988. 448 е.- Т.4. Чугун, 1988. 248 с.
- Мэнсон Дж., Полимерные смеси и композиты / Дж. Мэнсон, Л. Скер-линг. Пер. с англ. Под ред. Г. Г. Бабаевского. М.: Химия, 1981. — 736 с.
- Мощные ультразвуковые поля / Под ред. Л. Д. Розенберга. М.: Наука, 1969. — 326 с.
- Назаров Н.В. Электрохимическое сверление / Н. В. Назаров // Машиностроитель, 1980. № 10. С. 25−27.
- Немилов Е.Ф. Электроэрозионная обработка материалов / Е.Ф. Не-милов. Л.: Машиностроение, 1983.- 160с.
- Несмеянов Е.А. Особенности высокоскоростного фрезерованияалюминиевых заготовок / Е. А. Несмеянов, Ю. В. Трофимов // Инновационные технологии и оборудование машиностроительного комплекса. Межвуз. сб. научн. тр. Воронеж: ВГТУ, 2009. Вып. 12. С. 78−82.
- Несмеянов Е.А. Повышение виброустойчивости оборудования при комплексной обработке / Е. А. Несмеянов, Ю. В. Трофимов // Вестник Воронежского государственного технического университета. Воронеж: ВГТУ, 2010. Т6. №.7. С. 23−26.
- Новицкий Б.Г. Применение акустических колебаний в химико-технологических процессах / Б. Г. Новицкий. М.: Химия, 1983. 191 с.
- Обработка давлением алюминиевых и жаропрочных сплавов: Сб. статей / Под ред. А. И. Колпашникова. М.: Машиностроение, 1987. 123 с.
- Обработка материалов резанием / Под ред. A.A. Панова. М.: Машиностроение, 1988. -736 с.
- A.c. 1 493 265 СССР МКИ, А 62 С 3/04 Огнепреградитель/ А. Ю. Потапов, В. В. Трофимов, В. Т. Трофимов, В. П. Смоленцев и В. И. Шукайло. Опубл. 1989. БЮЛ.№ 26.
- Олейников Б. В. Алюминий — новый минерал класса самородных элементов / Б. В. Олейников // Записки ВМО. 1984, ч. CXIII, Вып. 2, С. 210−215.
- Петров Ю.Н. Основы повышения точности электрохимического формообразования / Ю. Н. Петров, Г. Н. Корчагин, Г. Н. Зайдман, Б. П. Саушкин. Кишинев: Штиинца, 1977. — 195 с.
- Подураев В.Н. Физико-химическая обработка материалов / В.Н. По-дураев, B.C. Камалов. М.: Машиностроение, 1973. 228 с.
- Подураев В.Н. Технология физико-химических методов обработки / В. Н. Подураев. М.: Машиностроение, 1985. 264 с.
- Подшибякин В. Д. Электрохимическая обработка глубоких каналов / В. Д. Подшибякин // Производительная обработка и технологическая надежность деталей машин. Ярославль, 1979. № 8. С. 149−152.
- Прохоренко П.П. Ультразвуковая металлизация материалов / П. П. Прохоренко, В. А. Лабунов, Под ред. В. А. Лабунова. Минск: Белоруссия, 1987. -271 с.
- Прохоренко П.П. Увеличение подъема жидкости в капилляре при наличии кавитации / П. П. Прохоренко, Н. В. Дежкунов // Повышение эффективности технологических процессов в поле акустических колебаний. М.: Металлургия, 1981.-С. 146−150.
- Раковский B.C. Порошковая металлургия в машиностроении / В. С. Раковский, В. В. Саклинский. М.: Машиностроение, 1973. 126 с.
- Роман О.В. Справочник по порошковой металлургии / О. В. Роман, И. П. Габриелов. Минск: Белоруссия, 1988. 175 с.
- Рубан В.Е. Одновременная электроэрозионная прошивка отверстий, расположенных под углом к оси детали / В. Е. Рубан, А. П. Москалев, В. Н. Мирошниченко // Станки и инструмент, 1980. № 4. С. 30−31.
- Румянцев Е.М. Исследование точностных возможностей ЭХО с вибрацией электродов / Е. М. Румянцев, В. И. Волков, В. М. Бурков // Электронная обработка материалов. 1980. № 6. — С.17−19.
- Румянцев Е.М. Исследование взаимосвязи электрохимических свойств поверхностных пленок и локализация при ЭХРО титана / Е. М. Румянцев, О. И. Невский, В. И. Волков, Е. П. Гришина // Электронная обработка материалов. 1984. № 4. С. 14−17.
- Рыкалин H.H. Основы электронно-лучевой обработки материалов / H.H. Рыкалин, И. Н. Зуев, A.A. Углов. М. Машиностроение, 1978. — 239 с.
- Седыкин Ф.В. Размерная электрохимическая обработка деталей машин / Ф. В. Седыкин. М.: Машиностроение, 1976. 302 с.
- Седыкин Ф.В. Электрохимическая обработка в производстве радиоэлектронной аппаратуры / Ф. В. Седыкин, Л. Б. Дмитриев, В. В. Любимов, В. Д. Струков. М.: Энергия, 1980. 136 с.
- Сейсон К. Эффективность выполнения электроэрозионной обработкой отверстий малого диаметра / К. Сейсон Пер. с яп. // Mon. J. Just. J. Sei. Univ. Tokio. 1982. № 6. — С. 676 — 690.
- Сергеев А.П. Электроэрозионная прошивка отверстий малого диаметра / А. П. Сергеев, В. П. Смоленцев, A.A. Ягупов // Электрофизические и электрохимические методы обработки. 1981. № 4. С. 8−10.
- Смоленцев В.П. Технология электрохимической обработки внутренних поверхностей / В. П. Смоленцев. М.: Машиностроение, 1978. 176 с.
- Смоленцев В.П. Электрохимическое получение отверстий малого диаметра в диэлектриках / В. П. Смоленцев, В. В. Трофимов // Электронная обработка материалов. 1987. № 6. С. 43−48.
- Pat. N5159167 (USA). МКИ В 23 Н 7/32,В 23 Н 7/30 Способ и устройство для электроэрозионного прошивания. Structure for and method of electrical discharge machining/ S.E. Chaikin, D.L.Brettager-Raycon Corp. 1992
- Заявка 57−184 638 (Япония). Способ обработки мелких отверстий/ 1п-oue Kiyochi. 1983.
- Pat. N4386256 (USA). Способ ЭЭО с введением ультразвуковых колебаний// Machine method and apparatus. Inoue Kiyoshi- Inoue Japax, Research Incorporated. 1983.
- Pat. N5030596 (USA) Способ изготовления спеченных алмазов. МКИ С 04 В 35/56 / Kume Shoichi, Yoshida Haruo, Suzuki Kazutaka, Tasaki Yoshio, Ikuta Shiro, Ishikava Masamitu, Mashida Mishide- Agency of Industrial Science J
- Technology Ministry of International Trade & Indastry. 1991.
- Pat. N5183632 (USA). Способ изготовления тормозных дисков из композита на основе алюминия. МКИ В 22 F 3/14 / K. Manabu, A. Masaro. Method of manufacturing an aluminium-base composite disc rotor. Akebono Brake Ind. Co., LTD. — 1993.
- A.c. № 1 673 329 СССР МКИ В 23 H 3/00, 9/14 Способ изготовления диэлектрических деталей с отверстиями / В. П. Смоленцев, В. Т. Трофимов и В. В. Трофимов. Опубл. 1991. Бюл. № 32.
- A.c. № 944 850 СССР МКИ В 23 Н 1/25 Способ электрохимической обработки / В. П. Смоленцев, Т. П. Литвин, В. А. Перов, A.B. Попов, В.Н. Анти-пов. Опубл. 1982. Бюл. № 27.
- A.c. N1299719 СССР МКИ В25 Н 15/00 Способ электрохимической обработки металлических покрытий на диэлектриках /В.В. Трофимов, В. П. Смоленцев, А. И. Болдырев, З. Б. Садыков. Опубл. 1987. Бюл. № 12.
- A.c. N1808498 СССР МКИ В23 В 35/00 Способ обработки отверстий и алмазно-абразивное сверло для его осуществления / В. В. Бурмистров, В. В. Гусев, Л. Н. Феник, В. Н. Дубовик, Е. Б. Щепановский. Опубл. 1993. Бюл. № 14.
- Патент РФ № 2 207 231 МКИ В23Н 5/06, 3/00 Способ комбинированной обработки поверхностей в армируемых электропроводящих материалах / В. Т. Трофимов, В. В. Трофимов, Ю. В. Трофимов. Опубл. 2003. Бюл. № 18.
- A.c. N814588 СССР МКИ В23 Н 11/08 Станок для глубокого сверления отверстий малого диаметра / Шушпан Ю. И., Беловол Ю. С., Маликовский В. В., Чередник B.C., Омельчук B.C. Опубл. 1981. Бюл. № 19.
- Теория и технология производства порошковых материалов и изделий: Сборник научных трудов. Новочеркасск, 1993. с. 114−122.
- Технологические лазеры. Справочник в двух томах. М.: Машиностроение, 1991. Т. 1,2. 645 с.
- Тихонов В.Н. Аналитическая химия алюминия / В. Н. Тихонов. М.: Наука, 1971.-266 с.
- Трофимов В.В. Комбинированная обработка глубоких каналов в армируемых материалах: Дис. док. техн. наук. 05.03.01. Воронеж, 1998. 330 с.
- Трофимов В.Т. Применение процессов электрохимической обработки металлических вставок при изготовлении профильных микроотверстий /
- B.Т.Трофимов, В. В. Трофимов // Сборник трудов Всесоюзной научно-технической конференции «Разработка и реализация новых механических и физико-химических методов обработки». М.: МВТУ, 1988. С. 41−42.
- Трофимов В.В. Получение отверстий в труднообрабатываемых материалах / В. В. Трофимов, В. Т. Трофимов // М.: Машиностроитель, 1993. № 10.1. C.13- 14.
- Трофимов В.В. Комбинированные методы обработки и испытаний / В. В. Трофимов, В. П. Смоленцев, В. Т. Трофимов. Монография. Деп. в ВИНИТИ 15.04.97, М1253-В97. 219 с.
- Трофимов В.В. Электрохимическая обработка металлических вставок в диэлектрических материалах/В .В. Трофимов // Электрохимические и электрофизические методы обработки материалов. Тула: ТПИ, 1986. С. 27−32.
- Трофимов Ю.В. Технология получения отверстий малого диаметра/ Ю. В. Трофимов, В. Т. Трофимов, В. В. Трофимов // Инновационные технологии и оборудование машиностроительного комплекса. Межвуз. сб. научн. тр. Воронеж: ВГТУ, 2007. Вып. 9. С. 181−186.
- Трофимов Ю.В. Обработка армированных заготовок из алюминиевых сплавов / Ю. В. Трофимов // Вестник Воронежского государственного технического университета. Воронеж: ВГТУ, 2009. Том 5, № 10. С. 143−146.
- Трофимов Ю.В. Применение двухшпиндельных обрабатывающих центров // Бурение и нефть. 2008. № 5.- С.46−48.
- Ультразвуковая технология / Под ред. Б. А. Аграната. М.: Металлургия, 1974. 504 с.
- Уткин Н.Ф. Обработка глубоких отверстий / Н. Ф. Уткин, Ю.И. Киж-няев, С.К. Плужников- Под общ. ред. Н. Ф. Уткина. JL: Машиностроение, 1988. 269 с.
- Фумпо Б. Точная обработка металлических пластин прессованием и фототравлением / Б.Фумпо. Пер. с яп. // Цуресу гидзюцу. 1981. Т. 19. № 1. -С.52−55.
- Феттер К. Электрохимическая кинетика / К. Феттер, М. Л.: Химия, 1967. 856 с.
- Хачатурян А.П. Влияние частоты вибраций на точность и производительность процесса импульсно-циклической ЭХО / А. П. Хачатурян // Электрохимические и электрофизические методы обработки материалов. Тула: ТПИ, 1981.-С. 91−92.
- Хэтч Дж. Алюминий. Свойства и физическое металловедение. Справочник. /Дж. Е. Хэтч. М.: Металлургия, 1989. 390 с.
- Холистер Г. Материалы упрочненные волокнами / Г. Холистер, К.Томас. М.: Металлургия, 1979. 249 с.
- Хопенфельд У. Расчет и корреляция переменных процесса электрохимической обработки металлов / У. Хопенфельд, Р. Коул // Труды американского общества инженеров-механиков. Сер. Б. Конструирование и технология машиностроения. 1966. № 4. С. 130−136.
- Цукерман С.А. Порошковые и композиционные материалы. М.: Наука, 1976. 128 с.
- Чижов М.И. Гибридные технологии обработки материалов высокойпрочности / М. И Чижов, Ю. В. Трофимов // Сборник трудов победителей конкурса на лучшую научную работу, посвященного 50-летию ВГТУ. Воронеж: ВГТУ, 2006. С. 117−119.
- Чижов М.И. Оснастка для технологических универсальных станков / М. И. Чижов, Ю. В. Трофимов // Инновационные технологии и оборудование машиностроительного комплекса. Межвуз. сб. научн. тр. Воронеж: ВГТУ, 2006, С. 85−88.
- Чижов М.И. Комплексная обработка деталей из сплавов на основе алюминия / М. И. Чижов, Ю. В. Трофимов // «Студент, специалист, профессионал». Сб.тр. III международной научн.-практ. конф. Воронеж: ВГТУ, 2009. С. 177−183.
- Чижов М.И. Комплексная обработка деталей из алюминиевых сплавов/М.И.Чижов, Ю.В.Трофимов//Фундаментальные и прикладные проблемы техники и технологии. 2010.№ 6(284).- С.99−103.
- Швабе К. Проблема пассивности металлов / К. Швабе // Защита металлов. 1982. Т.28. № 4. С. 499−510.
- Щербак М.В. Основы теории и практики электрохимической обработки металлов и сплавов / М. В. Щербак. А. М. Толстая, А. П. Анисимов, В. Х. Постаногов. М.: Машиностроение, 1981. 263 с.
- Электрофизические и электрохимические методы обработки / Под ред. В. П. Смоленцева. М.: Высшая школа, 1983. Т.1, 2. 415 с.
- Электроэрозионная и электрохимическая обработка. М.: НИИМАШ, 1980. Т.1, 2. 394 с.
- Электроэрозионное прошивание отверстий в лопатках турбин. Заявка 2 254 280 Великобритания, МКИ В 23/Н 11/00 / К.С. Moloney. Опубл. 1992. Roi 1 s-Royce р/с. N9107118.3
- Armstrong R.D. The anodic dissolution of tungsten in alkaline solutions / R.D. Armstrong, K. Edmondsen, R.E. Firman // S. Electronal Chem. 1972. 40. N1. -pp. 19−28.
- Bates C. Production for aerospace industry / Charles Bates // American Machinist, 2009. N11. pp. 26−27.
- BAZ Starrag-Heckert STC-800 / Produktion. 2008, N6. S. 22−26.
- Bellows G. Drilling without drills / G. Bellows, I.E. Kohis // American Machinist. 1982. N3. pp. 173 — 188.
- Bulavkin V.V. Electroerosion machining treatment of parts of aerospace complex and their conversion / V.V. Bulavkin // ISEM’XI: Int. Powder Met. Int. 1992. 24.Nl.-pp. 42−44.
- Clifton D. Some ultrasonic effects in machining materials encountered in the offshore industries / D. Clifton, Y. Imai, J.A. McGeough // Proc. 13th. Int. Matador Conf. Manchester. Manchester, 2008. pp. 119−123.
- Corfe A.G. Laser drilling of aeroengine components/ A.G. Corfe // Proc. 1st. Int. Conf. Laser Manuf. Brighton, 1−3 Nov. 2008. Kempsten Amsterdam e.a., 2008.-pp. 31−40.
- Craig N.C. Charles M. Hall and his Metall / N.C. Craig, M. Charles // J. Chem. Educ. 1986. Vol. 63. pp. 412−420.
- Dabrowskii L. Simulacja komputerova wybranych zagadnien obrobki electrochemicznej / L. Dabrowski // Konf. «Podstawy technol. masz. '91»: Pr. nauk. Inst, technol. masz. i autom. Wrocl. Ser. Konf. 1991. N18. S. 257−258.
- Electron drilling // J. Jap. Soc. Precis. Eng. 2002. 48. N18. pp. 17−29.
- Eppolito R. Electrochemical microdrilling / R. Eppolito, S. Tornicasa // Eff. Rual and Hum. Prod. Syst. Proc. Gth. Int. Conf. Prod. Res. Novy Sad, 1981. -pp. 143 — 147.
- Filter aus Sintermetall fur Gase und Flussigkeiten // Maschinenmarkt. 1994. 100. N6. S. 57.
- Funkerosieves Bohren und Profilieren von Sinditz Zechsteinrohlingen // Techn. Rept. 2003. 10. N1. S. 28−40.
- Genauigkeit gefragt. Hersteller von Tiefbormaschlnen setzen abnemen-den Bedarf Leistung entgegen // Maschinenmarkt. 2007. 99. N29. S. 10−11.
- Hertel: mandrin hydraulique, rationalisation en percage et materiaux de coupe // Mach. prod. 2003. N607. P.13−15.
- Heimle BAZ von Typ C30U/P/ Fertigung. 2005. N9, Vol.32. S.12−14.
- Hiermaier M. Electrochemisches Bohren / M. Hiermaier // Galvanotechnik. 1992. 83. N9. S. 2959−2968.
- High efficiency SX wire EDM // Mod. Mach. Shop. 2005. 67. N1. -pp. 238−240.
- High performance materials on the way to mass production. Production Engineering, 1995. 61. N3. P.17 18.
- Hobohm M. Bearbeitung der Teile aus Aluminium/ M. Hobohn // Werkstatt und Betrieb, 2008. N10. S. 14−18.
- Horizonthai BAZ AeroCell / Fertigung. 2007. Vol. 34. N9. S. 130−138.
- Hudak L. I Analysis of oxide wedging during environment assisted crack growth corrosion / L.I. Hudak, R.A. Page // Corrosion. 1983. 39. N7. pp. 285- 290.
- Erfahrungen mit «fugender Optik» / W. Hunziker / Schwei? technik. 2007. N4. S. 62−65.
- Diamond wire-edm guides // Cutting Tool Eng. 2003. 45. N4. pp. 100 102.
- Die mechanische Alternative zur funkerosiven Fertigung von Kleinstbohrungen//VDI-Z. 1989. 124. N21. S.57−81.
- EDM: a standard technology for special machines // Engineer (USA). 1998. 82. N3.-pp. 62−64.
- Electrochemic une solution astucuse peur les micropersager // Mach, prod. 2008. 30. N361. pp. 217−222.
- Electroerosion: coup de projectur sur de la haute production // Mach, prod. 2007. N602. S. 49−53.
- Geswans M. Small hole drilling in EDM / M.L. Geswans // Int. J. Mach. Tool Pes. and Res. 1979. 19. N3. pp. 165−169.
- Hammer W. The Structure of Electrolytic Solutions / W. Hammer //
- Education. New York, 1959. 317 p.
- High speed micro-hole drilling // Techno Jap. 2002. 25. N9. P.82.
- Israelson J. A progress report on cutting tool materials / J. Israelsson // Advanced Machining. 2002. 136. N12. P.39−40.
- Kauppinen V. The development of cutting tool materials from the perspective of wear resistance / V. Kauppinen // Tribologia. 1993. 12. N2. pp. 20−35.
- Korn D. Drilling and cutting of RoboDrill / D. Korn // Modern Machine Shop. 2009. N10. pp. 75−78.
- Kumar V. Charles Martin Hall and the Great Aluminium Revolution / V. Kumar, L. Milewski // J. Chem. Educ., 1987. Vol. 64. N8. pp. 47−63.
- Laser und Technologie // Maschinenmarkt. 2007. 72. N17. S. 48−54.
- Lasers and the job shop Fabricator // Mod. Mach. Shop. 2006. 65. N10. -pp. 62−68.
- McCafferty P. Effect of laser-surface melting on the behavior of an AlMn-alloy / E. McCafferty, P.V. Moore, G.T. Peace // J. Electrochem. Soc. 2004. 129. Nl.-pp. 9−17.
- Machining of parts for medical industries / Metalworking Production. 2005. Vol. 149. N7. pp. 35−37.
- Marcus S. Spot Thermal Coupling of CO2 Laser Radiation to Metallic Surfaces / S. Marcus, J.E. Lowder, D.L. Mooney // Journal off Applied Physics, 1976. Vol. 47. N7. pp. 2966−2968.
- Mayer E. Heutiger Stand des Elektronenstrahlbohrens / E. Mayer // DVS. 2000. N63. S. 143−146.
- Meyer W. Schnellbohren mit Elektronenstrahlen / W.E. Meyer // Ind. Anzeiger. 1980. 102. N73. S. 54−55.
- Mechanisches und fiinkerosives Bohren kleiner Locher // Werkstattstechnik. 1999. 72. N2. S. 83−84.
- Neue Senkerodiermaschine erlaubt das automatische, mahnlose Erodieren von Prazisionsteilen // Maschinenbau. 2007. 24. N9. S. 19−20.
- Nikumb S. Drillings of Al-alloy using pulsed CO laser / S.K. Nikumb, R.T. Shah, G. Sarkar // India I. Techology. 2003. 19. N7. pp. 281−284.
- Novak P. Materialbearbeitung mit dem Laserstrahl / P. Novak // Osterr. Ing. und Archit. 2009. 138. N3. S. 121−123.
- Osenbruggen C. Electrochemich mikrobeverben / Osenbruggen C., Van. Regt C. //Philips Techn. Tijdschr. 2004. 42. N1. pp. 22−23.
- Pnippe I. Investigation of laser-enhanced electroplating mechanism / I.G. Pnippe, R.E. Acosta, R.T. von Gutfeld // J. Electrochem. Soc. 2009. 128. N12. pp. 2539−2545.
- Process maximizes TIB a cutting contender// Tool and Prod. 2005. 61. N6. pp. 25−26.
- Puhr-Westerheide I. Einfluss abtragender Verfahren auf die Festigkeit /1. Puhr-Westerheide, R. Scharwachter, I. Timel // Werkstatttechnik. 2008. 68. N8. S. 457- 463.
- Rogers I.K. Laser drilling and cutting saves time and cost in diamond manufacturing / I.K. Rogers // Wire Ind. 1983. 50. N596. P. 440.
- Roux T. Electric discharge machining of small holes through polycristal-line diamond wire drawing blanks / T. Le Roux, M.L. Wise, D.K. Aspinwall, L. Blunt // Proc. 29th Int. Matador Conf. Manchester. Manchester, 2008. pp. 533−539.
- Die Rundbearbeitung von Leichtmaterialien mit dem schmaller Wanden vermittelst Frasen / Werkstatt und Betrieb. 2004. N10, Vol. 137. S. 54−56.
- Sakuma K. Study on Deep Hole Boring by BTA System Solid Boring Tool / K. Sakuma, B. Taguchi, A. Katsuvi // Bulletin of the Japan Society of Precision Engineering. 2001. 14. N3. pp. 143−148.
- Small hole EDM // Mod. Mach. Shop. 1995. 68. N3. P. 115.
- Seers L. Offre complete en usinage par electroerosion / L. Seers //Mach, prod. 2006. N603. S. 28.
- Spur G. Drilling of reinforced aluminium / G. Spur, H. Cartsburg // Ind. Diamond Rev. 2008. 53. N555. pp. 92−97.
- Tecniche per cambiaue la produzione I I Riv. mecc. 1999. 43. NN1019−1020.-S. 31−32.
- Tenlm H. Fein-Senkerodieren bei Mikroarbeiten / Tenlm Hugo, Baumgarten Urs // Tech. Rept. 2004. 92. N2. S. 63−65.
- Water-jet CNC machining of Aluminium Parts / Modern Application News. 2005. Vol. 39. N11.- pp. 33−34.
- Wolfgenannt M. Erfolg mit dem Laser / M. Wolfgenannt // Schweizer Maschinenmarkt. 2005. 96. N24. S. 48−50.
- Wyss R. Schleifen und Erodieren in Kombination / R. Wyss //Schweizer Maschinenmarkt. 2009. 92. N47. S. 18−23.
- Karamatsu O., Ultrasonic machining / O. Karamatsu // Kikay to cogu. Tool Eng. 2004. N7. pp. 17−24.