Повышение служебных свойств поверхности конструкционных низкоуглеродистых сталей методом лазерного легирования
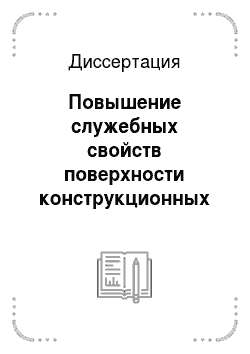
Диссертация
При обработке поверхности сталей и сплавов импульсным лазерным излучением также появляется ряд особенностей по сравнению с непрерывной. Во-первых, благодаря меньшей длины волны, импульсное излучение больше поглощается поверхностью материалов. Во-вторых, за счет уменьшения ^ расфокусировки лазерного луча при одной и той же мощности лазера можно добиться значительного повышения плотности мощности… Читать ещё >
Содержание
- Введение 1. Аналитический обзор и постановка задачи
- 1. 1. Лазерная обработка материалов
- 1. 1. 1. Взаимодействие лазерного излучения с веществом
- 1. 1. 2. Особенности нагрева и охлаждения при лазерной обработке
- 1. 1. 3. Классификация методов поверхностной лазерной обработки
- 1. 2. Лазерное легирование поверхности металлов
- 1. 2. 1. Обоснование выбора компонентов легирующих композиций
- 1. 2. 2. Формирование структуры при лазерном легировании
- 1. 2. 3. Свойства поверхностных слоев после лазерного легирования
- 1. 3. Постановка задачи
- 1. 1. Лазерная обработка материалов
- 2. Методика экспериментальных исследований
- 2. 1. Материал исследования
- 2. 2. Методика процесса лазерной обработки
- 2. 3. Методика определения микрогеометрии поверхности
- 2. 4. Методика металлографических исследований
- 2. 5. Рентгеноструктурный анализ
- 1. 6. Микрорентгеноспектральный анализ
- 1. 7. Методика дюрометрических исследований
- 1. 8. Методика определения микрохрупкости структуры легированного слоя
- 1. 9. Измерение коэффициента теплопроводности
- 1. 10. Определение коррозионной стойкости в жидких средах
- 1. 11. Определение триботехнических свойств
- 3. Исследование структуры поверхностных слоев сталей после лазерного легирования
- 3. 1. Распределение химических элементов в зоне лазерного воздействия
- 3. 2. Формирование фазового состава поверхности
- 3. 3. Исследование микроструктуры поверхностных слоев
- 3. 4. Формирование структуры поверхностных слоев
- 3. 5. Влияние температурно-временных параметров на устойчивость структурного состояния слоев лазерного легирования
- Выводы по главе
- 4. Исследование свойств поверхностных слоев сталей после лазерного легирования и производственные испытания
- 4. 1. Физические и механические и свойства
- 4. 1. 1. Роль структуры и химического состава легированных слоев при формировании теплофизических свойств
- 4. 1. 2. Влияние состава поверхности на распределение микротвердости в зоне лазерного воздействия и в зоне термического влияния
- 4. 2. Эксплуатационные свойства
- 4. 2. 1. Коррозионная стойкость
- 4. 2. 1. 1. Механизм коррозии легированных слоев сталей
- 4. 2. 1. 2. Влияние рН среды
- 4. 2. 1. 3. Влияние состава легирующих композиций и материала основы
- 4. 2. 2. Износостойкость
- 4. 2. 1. Коррозионная стойкость
- 4. 3. Практическое использование результатов исследований
- 4. 1. Физические и механические и свойства
- Выводы по главе
Список литературы
- Clifton W. Draper. Laser Surface Alloying: The State of the Art // Journal of Metals. 1982. — Vol. 34. — № 6, P. 24−32.
- Kusinski I. Laser melting of T1 Hight Speed Tool steel // Metallurgical Transactions. — 1988. — Vol. 19A, Str. 377−382.
- Kusinski I. Obrobka laserowa srednioweglowych stali chromowych //Hutnik. -1988.- № 7, Str. 218−225.
- Tomsinsky V.S., Postnikov V.S. Structure formation in the laser borating of the steel. Key Engineering Materials, Subscription Information Vols. 46 & 47, Trans Tech Publications, Zurich, Switzerland, 1990, P. 473−484.
- A.c. 1 557 193 СССР, МКИ С 23 С 8/00. Способ лазерного легирования поверхности металла.
- Али-заде И.И., Кабанова С. В., Крапошин B.C., Петрикин Ю. В. Фазовый состав и свойства поверхностей низкоуглеродистых сталей, легированных с помощью лазерного нагрева // ФиХОМ. 1987. — № 6, С. 76−81.
- Анисимов С.И., Имас Я. А., Романов Г. С. и др. Действие излучения большой мощности на металлы. М.- Наука, 1970. — 272 с.
- Артамонова И.В., Никитин А. А., Рыжков И. А. Влияние поверхностного лазерного легирования на структуру и механические свойства стали 40XII// МиТОМ. 1989. — № 10, С. 5−7.
- Асеева Е.Н. Формирование высоких триботехнических свойств деталей лазерной обработкой: Автореф. дис. канд. техн. наук: 05.03.01. / Волгоград, 2000. 20 с.
- Бабушкин В.Б., Ворошнин Л. Г., Пархимович В. В. Особенности кристаллизации металлов и сплавов при лазерной обработке // Изв. вузов. Черная металлургия. 1990. — № 10, С. 42−44.
- Багмутов В.П., Захаров И. Н. Исследование тепловых процессов при воздействии на материал концентрированных потоков энергии // ФиХОМ. -2002. -№ 3, С. 9−17.
- Бекренев А.Н., Жаткин С. С., Паркин А. А. Исследование динамики нагрева металлов при импульсном лазерном воздействии // ФиХОМ. 1994. — № 6,1. С. 25−31.
- Бекренев А.Н., Камашев А. В. Определение границ структурно-фазовых превращений в сталях при лазерном воздействии // ФиХОМ. 1995. — № 2, С. 19−23.
- Белова С.А. Повышение эксплуатационных характеристик поверхности стали методом лазерного карбоборохромирования: Автореф. дис. канд. техн. наук / Пермь, 1999.-24 с.
- Берзина И.Г., Бурякин А. В., Гусев Э. Б. и др. Особенности зон упрочнения, полученных при борировании импульсным лазером // Изв. вузов. Физика. — 1986.-№ 7, С. 105−107.
- Берзина И.Г., Гусев Э. Б., Просолов B.C., Федина Г. Н. Влияние параметров лазерного воздействия на распределение бора в зоне упрочнения сталей и сплавов // ФиХОМ. 1990. — № 6, С. 43−47.
- Брик В.Б. Кинетика миграции атомов углерода при фазовых превращениях в стали при лазерном облучении // ФиХОМ. 1989. — № 2, С. 21−27.
- Бровер Г. И., Пустовойт В. Н., Бровер А. В., Магомедов М. Г., Холодова С. Н. Повышение качества химических покрытий лазерным облучением // Машиностроитель. 2001. — № 5, С. 38−43.
- Бровер Г. И., Федосиенко С. С., Варавка В. Н. Повышение износостойкости инструментальных сталей путем лазерного легирования // ФиХОМ. 1984. -№ 1,С. 19−23.
- Бураков В.А., Барышевская Е. Л., Буракова Н. М. Локальная цементация железа в условиях импульсного лазерного нагрева и скоростной закалки // Изв. вузов. Машиностроение. 1981. -№ 11, С. 106−111.
- Веденов А.А., Гладуш Г. Г. Физические процессы при лазерной обработке материалов. — М.: Энергоатомиздат, 1985. 208 с.
- Виноградов Б.А., Гавриленко В. Н., Либенсон М. Н. Теоретические основы воздействия лазерного излучения на материалы: Учебное пособие для вузов. — Благовещенск: Благовещенский политехнический институт, 1993. 345 с.
- Вотинов Г. Н., Постников B.C. Моделирование процесса лазерного легирования из газовой среды // Сб. науч. трудов IV Международной научно-практической конференции «Проблемы и перспективы развития литейного, 24