Формирование пористой структуры в изделиях на основе железа и титана с заданными физико-механическими и эксплуатационными свойствами
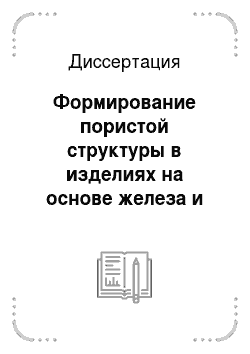
Диссертация
Определены условия взаимодействия атмосферы сухого воздуха с поверхностью металлов в обычной атмосферных условиях и изолированном объеме. Защитные свойства окисной пленки на поверхности титановых сплавов сохраняются: а) при нагреве в обычных атмосферных условиях: в течении 1 часа при нагреве в электропечи до 650 °C, — 30 мин. при ЭКН до 900 °C,-5 мин. при ЭКН до 1000°Сб) в герметичном контейнере… Читать ещё >
Содержание
- Глава 1. Актуальность проблемы изготовления изделий из порошковых материалов с заданными свойствами
- 1. 1. Эффективность изготовления деталей из конструкционных порошковых материалов
- 1. 2. Анализ существующих и перспективных методов изготовления изделий из порошковых материалов
- 1. 3. Обоснование направления и методик исследований, выбор оборудования
- 1. 4. Выводы
- Глава 2. Исследование влияния факторов активирования взаимодействия атмосферы сухого воздуха с поверхностью сплавов на основе железа и титана на технологичность изготовления и свойства конструкций
- 2. 1. Взаимодействие в обычных атмосферных условиях
- 2. 2. Взаимодействие в изолированном объеме
- 2. 3. Взаимодействие с атмосферой сухого воздуха при ГЛР в среде аргона и азота
- 2. 4. Выводы
- Глава 3. Исследование влияния активирующих факторов процесса холодного прессования на изменение структуры и усадки образцов имитаторов конкретных изделий
- 3. 1. Общие закономерности формования порошков
- 3. 2. Исследование образцов имитаторов колец припоя из сплава впр-16.:. бо
- 3. 3. Исследование на образцах имитаторах корпуса замка из порошкового сплава на основе титана
- 3. 4. Исследование на образцах имитаторах гермошайб из порошкового сплава на основе титана
- 3. 5. Выводы
- Глава 4. Кинетика, температурная зависимость и механизм активирования образования диффузионного соединения порошковых частиц из материалов ЖГр1 и 2М2А
- 4. 10. природе образования соединения в твердофазном состоянии
- 4. 2. Исследование активизации процесса диффузионного взаимодействия порошковых частиц в холоднопрессованных заготовках
- 4. 3. Закономерности формирования пористости и свойств спеченных заготовок
- 4. 4. Выводы
- Глава 5. Влияние условий диффузионного взаимодействия порошковых частиц сплава 2М2А и листовых заготовок сплава ВТ20 на свойства композиционных конструкций
- 5. 1. Исследование условий взаимодействия порошковых частиц из сплава 2М2А и листовых заготовок из сплава ВТ20 при спекании
- 5. 2. Исследование влияния условий спекания на свойства комбинированных из порошка и листа деталей
- 5. 3. Проведение ресурсных испытаний и оценка эксплуатационных свойств конкретных деталей
- 5. 4. Выводы
Список литературы
- Андриевский Р.А. Введение в порошковую металлургию / Р. А. Андриевский // Фрунзе: Илим, 1988. 172 с.
- Порошковая металлургия в СССР. История. Современное положение. Перспективы / Под ред. И. Н. Францевича и В. И. Трефилова // М.: Наука, 1986.-294 с.
- Левин Б.Е. Физико-химические основы получения, свойство и применение ферритов / Б. Е. Левин, Ю. Д. Третьяков, Л. М. Летюк // М.: Металлургия, 1979. 468 с.
- Гегузин Я.Н. Физика спекания / Я. Н. Гегузин // М.: Наука, 1984.312 с.
- Андриевский Р.А. Порошковое материаловедение / Р. А. Андриевский // М.: Металлургия, 1991.- 205 с.
- Criswell D. Nat. Powder Met. Conf., Montreal. May. 24 -27. 1982. Proc. Princeton, 1983. — P.115 — 146. Экспресс-информация «Порошковая металлургия». 1986. № 3. С. 4 — 9.
- Раковский B.C. Порошковая металлургия в машиностроении. Изд. 3-е / B.C. Раковский, В. В. Саклинский // М.: Машиностроение, 1972. 126 с.
- Джонс В.Д. Основы порошковой металлургии. Прессование и спекание / Пер. с англ. под ред. Балыиина М. Ю. и Натансона А. К. // М.: Мир, 1965−405 с.
- F.V. Level: in «Powder Mettallurgy», 257, 1980, Princeton, NY, Metal Powder Industries Federation.
- H.I. Ullrich et al: Microchem. Acta, 1983, (1), 175.
- Dislocation activated sintering processed. Schatt W., Friedrich E. «PowderMet.», 1985, 28, № 3, 140−144.
- Устинов B.C. Порошковая металлургия титана. Изд. 2-е / B.C. Устинов, Ю. Г. Олесов, В. А. Дрозденко, Н. М. Антинина // М.: Металлургия, 1981.-248 с.
- Олесов Ю.Г. Цветные металлы / Ю. Г. Олесов, В. И. Западня, Р. К. Огнев и др. // 1973 № 8 — 65−66 с.
- Федорченко И.М. Металлокерамические конструкционные материалы / И. М. Федорченко, Р. К. Огнев, В. Б. Райцесс и др. // Киев: АН УССР, 1976.-75−78 с.
- Металлургия и химия титана / Институт титана // М.: Металлургия, 1970-№ 4.
- Akupa О. J. Japan Soc. Powder and Powder Metallurgy, 1976. v. 14, № 8, p. 342−347.
- Воробьев Б.Я. Производство изделий из порошков титана / Б. Я. Воробьев, Ю. Г. Олесов, В. А. Дрозденко // Киев: Техника, 1976. 174 с.
- Павловская Е.И. Сборник трудов IX Всесоюзной конференции по порошковой металлургии / Е. И. Павловская, В. М. Волгин, З. В. Горячева и др. // Рига: ЛатИНТИП, 1968. 85−88 с.
- Борок Б.А. Труды / Б. А. Борок, В. И. Гаврилова, В. Г. Тепленко и др. //ВИНИТИ, 1962. -№ 1 -3−31 с.
- Окисление металлов / Под ред. Ж. Бернара, т. I: пер. с франц. // М.: Металлургия, 1968. — 267 е., ил.
- Конюшков Г. В. Электронная техника / Г. В. Конюшков, Н. Ф. Казаков, С. А. Жуков // 1970. -т.2, сер. 10(34), 3−16 с.
- Аренсбургер Д.С. Порошковая металлургия / Д. С. Аренсбургер // 1970.-№ 2- 27−31 с.
- Спивак И.И. Порошковая металлургия / И. И. Спивак, Р. А. Андриевский, К. Л. Чевашева // 1968. № 6 — 41−46 с.
- Кипарисов С.С. Внутренне окисление и азотирование сплавов / С. С. Кипарисов, Ю. В. Левинский // М.: Металлургия, 1979. 190 е., ил.
- Райченко А.И. Порошковая металлургия / А. И. Райченко, JI.JI. Хандрос, Н. А. Муравский // 1969. № 11 — 26−30 с.
- Пинес Б.Я., Омельяненко И. Ф. ФММ, 1967, т.27, № 6, 1119−1122с.
- Кислый П.С. Порошковая металлургия / П. С. Кислый, JI.C. Голубяк // 1969.-№ 9- 18−22 с.
- Чачин В.Н. Порошковая металлургия / В. Н. Чачин, Г. К. Седяко // 1968.-№ 9−31−33 с.
- Седяко Г. К. Вопросы прочности и пластичности металлов / Г. К. Седяко // Минск: Наука и техника, 1968. — 70−74 с.
- Головкина В.Я. Вопросы прочности и пластичности металлов / В. Я. Головкина // Минск: Наука и техника, 1968. 88−90 с.
- Косторков А.Г. Порошковая металлургия / А. Г. Косторков, В. В. Скороходов // 1971. № 11 — 21 -24 с.
- Заваруха О.В. Порошковая металлургия / О. В. Заваруха, П. С. Кислый // 1970. № 6 — 41−43 с.
- Kimura Tarashi. Planseeber. Pulvermetallyrgie. 1966, v. 14, № 2, h. 85−95.
- Патент 2 020 187 МКИ РФ C22 °F. Способ термической обработки деталей из титановых сплавов. / В. И. Муравьев, А. Ф. Мельничук, Б. Н. Марьин, A.M. Петров и др. // Опубл. 30.09.94, Бюл. № 18.
- Патент RU № 2 076 029 С1. Способ подготовки заготовок из титановых сплавов под сварку / В. И. Муравьев, А. Ф. Мельничук, С. П. Мазур, A.M. Петров // Опубл. 20.10.96, Бюл. № 29.
- Патент 2 021 058 РФ МКИ В21Д. Способ горячей штамповки листовых заготовок из титановых сплавов. / В. И. Муравьев, А. Ф. Мельничук, Ф. Э. Граф // Опубл. 15.10.94, Бюл. № 19.
- Калачев Б.А. Технология термической обработки цветных металлов и сплавов / Б. А. Калачев, P.M. Габидулин, Ю. И. Пигузов // М.: Металлургия, 1980.-280 с.
- Приоритеты авиационных технологий: в 2-х Кн.1 / Науч. Ред. А. Г. Братухин. // М.: Изд-во МАИ, 2004.-Кн. 1: Гл. 1−12, 696 с. (Гл. 11 А. Г. Братухин, В. И. Муравьев, Б. Н. Марьин // Материаловедческие решения сверхзвуковой авиации. С 489−665)
- N Муравьев В. И. Исследование влияния газолазерного раскроя на формирование рельефа, структуры и химического состава поверхности реза титановых заготовок / В. И. Муравьев, А. Ф Мельничук., Р. А. Физулаков, Д. В. Матвеенко // МиТОМ, 2005. № 2 — 22−25 с.
- Приоритеты авиационных технологий: в 2-х Кн.2 / Науч. Ред. А. Г. Братухин. // М.: Изд-во МАИ, 2004.-Кн. 2: Гл. 13−31, 640 с. (Гл. 25 А. И. Пекарш, В. И. Муравьев, Б. Н. Марьин // Технология размерной лазерной обработки. С 1135—1173)
- Патент RU № 2 247 070 С1. Способ получения нитрида титана / В. И. Муравьев, Р. А. Физулаков, Д. В. Матвеенко, А. Ф. Мельничук, Б. Н. Марьин, Н. А. Семашко // Опубл. 27.02.2005, Бюл. № 6.
- Ермаков С.С. Порошковые стали и изделия. Изд. 4-е перераб. и доп. / С. С. Ермаков, Н. Ф. Вязников // М.: Машиностроение, 1990. 319 с.
- Грабин В.Ф. Основы металловедения и термической обработки сварных соединений из титановых сплавов /В.Ф. Грабин // Киев: Наукова думка, 1975.-234 с.
- Ротан О.В. Справочник по порошковой металлургии: порошки, материалы- процессы / О. В. Ротан, И. П. Габриелов // Минск: Беларусь, 1988. -176 с.
- Диффузионная сварка- материалов: справочник / Под ред. Н. Ф. Казакова //М.: Машиностроение, 1981.-271 с.
- Порошковая металлургия. Спеченные и композиционные^ материалы // Под ред. В. Шатта. Пер. с нем. // М.: Машиностроение, 1983. -520 с.
- Скороход В.В. Физико-металлургические основы спекания порошков / В. В. Скороход, С. М. Солонин // М.: Металлургия, 1984. 159 с.
- Гегузин Я.Н. Физика спекания / Я. Н. Гегузин // М.: Наука, 1984.312 с.
- Гегузин Я.Н. Как и. почему исчезает пустота / Я. Н. Гегузин // Ml: Наука, 1983.- 191 с.
- Романов- О.В., Дорошкович Е. А. Теория и технология- спекания. Киев.: Наукова Думка, 1974. 347 с.
- Патент SU 1 784 006 B22F3. Способ спекания заготовок из металлического порошка / В. И: Муравьев, А. Ф. Мельничук, Ф. Э. Граф // № 4 704 761/02- заявл. 15.03.89- опубл. 17−23.12.1992, Бюл. № 47.
- Патент RU № 2 068 021 С1. Антифрикционный спеченный материал на основе железа/ А. В. Федоров, В. Г. Гончаров, В. И. Муравьев, А. Ф. Мельничук // Опубл. 20.10.96, Бюл. № 29.
- Мельничук А.Ф. Особенности изготовления металлокерамических фильтров из порошков стали и титана // А. Ф. Мельничук, В. Г. Гончаров // Вестник КнАГТУ. Прогрессивная технология обработки металлов. Комсомольск-на-Амуре, 1995. Сб 3. Выпуск 1. -32−35 с.
- Анциферов В.Н., Черепанова Т. Г. структура спечённых сталей. М.: Металлургия, 1981. 112 с.
- Балышш М.Ю., Кипарисов С. С. Основы порошковой металлургии. М.: Металлургия, 1978. с. 18−58, 123−145.
- Шибряев Б.Ф., Павловская Е. И. Металлокерамические фильтрующие элементы. М.: Машиностроение, 1972, с. 95 100.
- Редчиц В. В., Фролов В. А., Казаков В. А., Лукин В. И. «Пористость при сварке цветных металлов» М: Издательский центр «Технология машиностроения» 2002−448с.
- Редчиц В.В., Никифоров Г. Д., Шоршоров М. Х. «Вероятность образования соединения в твердой фазе при последовательном нагреве без приложения внешнего давления» Сварочное производство 1979 № 7 С38 41.
- Коровин Н.В., Магдасиева М. Е., Соляков В. К. Порошковая металлургия, 1966, № 5, с. 32−39
- Кац С. М. Высокотемпературные теплоизоляционные материалы. М.: Металлургия, 1981. 232 с.
- Кипарисов С.С., Либенсон Г. А. «Порошковая металлургия» М: Металлургия 1980 -496с.
- Витт Р. Х. Пауль О. Порошковая металлургия материалов специального назначения. М.: Металлургия, 1977. 329 с.
- Анциферов В.Н., Берестов Б. А., Костюченко Л. Ф. и др. -Порошковые конструкционные материалы /ИПМ АН УССР. Киев, 1980, с. 3539.
- Вакутин А.П., Селиверстова Н. И. Порошковая металлургия- Нач. тр.// ПЛИ, Пермь, РИО ППИ, 1979, с. 52−55.
- Микроструктура в зоне выхода лазерного луча сплава ВТ20 после ГЛР в среде азота1. зона поверхности (аморфная) 2 зона термического влияния (кристаллическая), 3 — зона переходная (нанокристаллическая)н