Другие работы
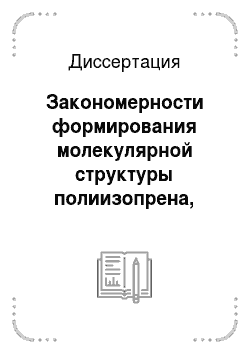
Научная новизна. Показано, что каталитические системы на основе галогенидов цинка позволяют с высоким выходом синтезировать растворимые полимеры полиизопрена с мономодальным молекулярно-массовым распределением (ММР). Установлена высокая эффективность окситрихлорида ванадия в катионной полимеризации изопрена с получением полимеров с полимодальным ММР и аномально высокой среднемассовой молекулярной…
Диссертация 
Эритроциты млекопитающих являются удобной моделью для изучения механизмов окислительных повреждений, поскольку они доступны в больших количествах, не содержат ядер и митохондрий и не способны к синтезу белков. Они циркулируют в крови 120 дней и более других клеток контактируют с кислородом и его активными формами. Постоянное взаимодействие с кислородом вызывает аутоокисление содержащегося…
Диссертация 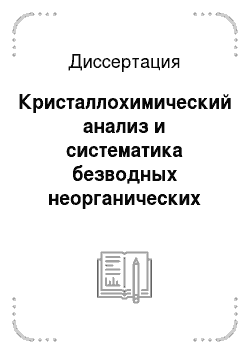
Апробация работы и публикации. Результаты диссертационной работы представлялись на II и III Национальной кристаллохимической конференции (Черноголовка, 2000, 2003 гг.), III Национальной конференции по применению рентгеновского, синхротронного излучений, нейтронов и электронов для исследования материалов (Москва, 2001 г.), XX Международной Чугаевской конференции по координационной химии…
Диссертация 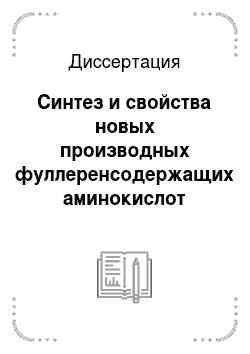
Начиная с 1990 года, когда были разработаны методы получения и выделения фуллеренов в макроколичествах, ведутся интенсивные исследования их химических свойств. В настоящее время они приобретают всё большую практическую направленность. Связано это с тем, что многие соединения фуллеренов показали весьма ценные свойства. Диады и триады фуллерена с различными супрамолекулярными объектами такими…
Диссертация 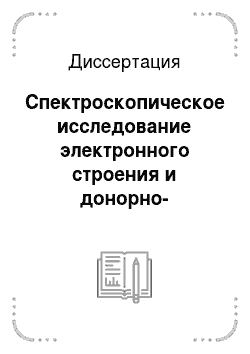
Электроноакцепторные свойотва атомов F в CgF5H принимают более кислотный характер С-Н связи по сравнению о CgCfcgH (рКа С6Н6 = 37, CgPgH = 23, CgCe5H = 30.5 /133/. Для пентафтор-фенильного кольца показана возможность изменения соотношения резонаноного и индуктивных эффектов CgF^ группы для мезомерных карбанионов типа (С6Р5С-Вв')%+, где R = r'= cOOEt, Си, COPh и др. /134/. Существенно, что атом…
Диссертация 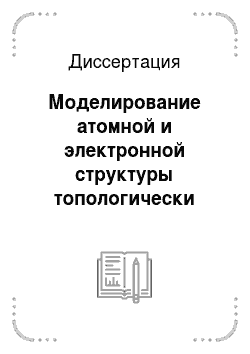
В данной работе автор ставил перед собой следующие основные задачи. ¡-.Разработать общий метод изучения строения и прогнозирования свойств неупорядоченных металлических структур. Имеется в виду построение методики, синтезирующей ряд достижений теории некристаллических систем последнего времени, свободной от подгоночных параметров, и потому пригодной для предсказания поведения исследуемого…
Диссертация 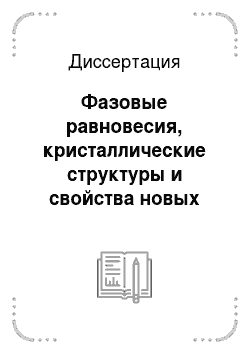
Апробации работы и публикации. Материалы диссертации докладывались и обсуждались на Международном симпозиуме «Принципы и процессы создания неорганических материалов» (III Самсоновские чтения) (Хабаровск, 2006) — Международной конференции «Keys issues in Chemistry and Environmental problems» (Улан-Батор, 2006) — Научно-практической конференции преподавателей, научных работников и аспирантов ВСГТУ…
Диссертация 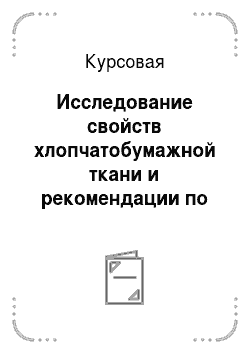
Особое внимание уделяется характеристике свойств изделия и формулированию требований в зависимости от его назначения и условий эксплуатации. Выделяются свойства одежды, связанные с ее устойчивостью к различным воздействиям: механическим (при растяжении, изгибе, трении) и физико-химическим (воды, света, светопогоды, тепла, холода, огня, излучений, химических реактивов и т. п.). Осуществление…
Курсовая 
Рентгеноструктурным анализом установлено, что двукратная окислительная обработка блочного алюмоникелевого контакта приводит к появлению в его составе фазы № 0, способствующей увеличению активности катализатора в процессе метанирования С02. Показано, что изученный катализатор в интервале Т- 450.600°С позволяет достичь равновесных глубин превращения С02 в СН4 при объемных скоростях подачи…
Диссертация 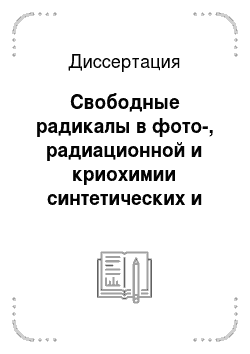
Окисиуглеродаиз природных — целлюлозунитратцеллюло^ зУхВР®1есщуижгнин. Выбор полистирола и полиэтилена был обусловлен не только широким применением этих полимеров в различных областях современной техники (в радиои электротехнике, в машиностроении, производстве синтетического каучука, в медицине и производстве бытовых товаров), но и вследствие недостаточной изученности радикальной стадии…
Диссертация 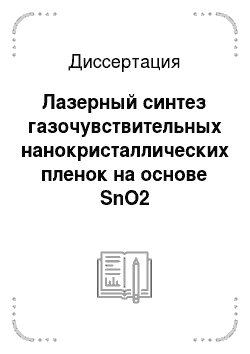
Первые исследовательские работы по лазерному синтезу пленочных полупроводников, диэлектриков, халькогенидов и металлоорганических соединений выявили основные проблемы технологии, в первую очередь влияние свойств лазерной плазмы: стабильности, зависимости ее зарядового и кластерного состава от потока мощности и длины волны излучения на состав, структуру и функциональные свойства образующегося…
Диссертация 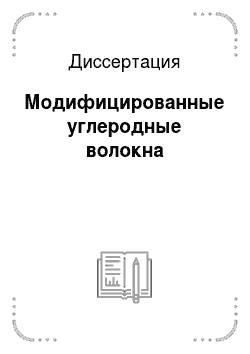
Одним из приемов «мягкой химии» является электрохимический синтез, который протекает на границе электрод/электролит (поверхность раздела). Особенностями электрохимического синтеза является то, что процесс протекает близко к поверхности электрода, что приводит к образованию продуктов, которые не могут быть получены при химическом синтезе. Электрохимический синтез является низкотемпературной…
Диссертация 
Золкин П. И., Лукин Э. Ю., Лысенко С. А., Маркелова И. М. Тез. доклада «Разработка и внедрение усовнршенственных методов контроля углеродных конструкционных материалов.» Межотраслевая конференция по углеродным материалам. г. Челябинск, 1983, с. 17−18. Кутейников А. Ф., Степанов А. Н., Золкин П. И. и др. Исследование изменения фазового состава материалов углерод-кремний, углерод-бор методом…
Диссертация 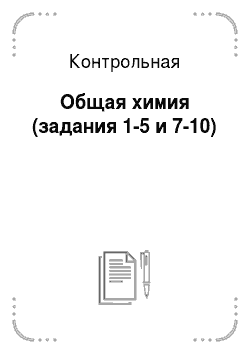
К d-элементам относят металлы побочных подгрупп IVIII групп, кроме лантаноидов и актиноидов, принадлежащих к f-элементам. Валентными орбиталями у d-элементов являются одна ns-орбиталь, три пр-орбитали и пять (n1)d-орбиталей. Электронная конфигурация валентного слоя имеет общую формулу (nl)dbnsa. Величина, а может принимать значения 1 и 2 (у палладия, а = 0), величина b от 1 до 10. Для всех…
Контрольная 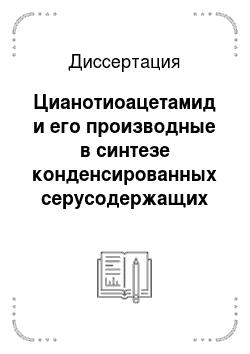
Актуальность проблемы. Проблема разработки препаративно удобных, экономичных и экологически безопасных методов синтеза функционально замещенных конденсированных гетероциклов, потенциально обладающих практически важными свойствами, постоянно находится в центре внимания исследователей. Учитывая этот факт и то, что бии полициклические азины, содержащие фрагмент «пиридиновое ядро — атом серы…
Диссертация