Обеспечение работоспособности нефтегазохимического оборудования с механической неоднородностью
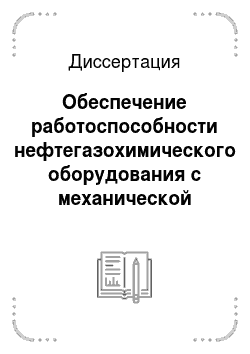
Диссертация
Для работоспособности оборудования существенное значение имеют сварочные напряжения. Одним из простых и дешевых методов их снятия является предварительное нагружение сварного соединения, которое можно сочетать с предпусковыми гидравлическими испытаниями аппаратуры и трубопроводов. При создании в стенках аппаратов напряжений, соответствующих пределу текучести, возможно полное снятие сварочных… Читать ещё >
Содержание
- 1. Проблема механической неоднородности
- 1. 1. Основные факторы нарушения работоспособности нефтега-зохимического оборудования (сосуды, аппараты и трубопроводы)
- 1. 2. Роль механической неоднородности в повышении и оценке ресурса оборудования
- 1. 3. Основные подходы к оценке ресурса оборудования с механической неоднородностью
- 1. 4. Выводы по главе
- 2. Создание теоретической базы расчетной оценки остаточного ресурса оборудования с механической неоднородностью
- 2. 1. Продольные и кольцевые прослойки в сосудах, работающих под давлением
- 2. 2. Предельное состояние мягких прослоек в зонах действия краевых сил и моментов
- 2. 3. Влияние формы разделки кромок под сварку мягкими швами на несущую способность оборудования
- 2. 4. Предельное состояние композитных прослоек
- 2. 5. Поддерживающий эффект в мягких прослойках сосудов при их совместной деформации с мягкими участками
- 2. 6. Контактное разупрочнение твердых прослоек соединений при их совместной деформации с мягкими участками
- 2. 7. Роль деформационного строения при оценке ресурса оборудования с механической неоднородностью
- 2. 8. Выводы по главе
- 3. Работоспособность стыковых соединений оборудования с механической неоднородностью
- 3. 1. Геометрическая и механическая неоднородность элементов оборудования
- 3. 2. Особенности напряженно-деформированного состояния элементов оборудования со смещением кромок
- 3. 3. Исследование статической прочности элементов оборудования с различной геометрией швов, выполненных со смещением кромок
- 3. 4. Расчетная оценка несущей способности сварных элементов со смещением кромок с мягкими и твердыми прослойками
- 3. 5. Выводы по главе
- 4. Работоспособность соединений базовых элементов оборудования типа охватывающих и охватываемых деталей
- 4. 1. Напряженно-деформированное состояние сварных угловых швов элементов нефтехимического оборудования
- 4. 2. Исследование несущей способности сварных соединений, выполненных по ресурсосберегающей технологии
- 4. 3. Натурные испытания
- 4. 4. Исследование трещиностойкости основного металла и сварных соединений при отрицательных температурах
- 4. 5. Влияние механической неоднородности на работоспособность соединений типа охватываемых и охватывающих деталей
- 4. 6. Выводы по главе 4
- 5. Разработка методов расчетной оценки долговечности нефтегазохимического оборудования с механической неоднородностью
- 5. 1. Определение остаточного ресурса элементов оборудования в условиях малоциклового нагружения
- 5. 1. 1. Определение упруго-пластических коэффициентов концентрации деформации и напряжений
- 5. 1. 2. Исследование малоцикловой усталости
- 5. 1. 3. Натурные испытания сварных элементов
- 5. 1. 4. Влияние остаточных напряжений на ресурс оборудования при циклическом нагружении
- 5. 1. 5. Учет деформационного старения при оценке остаточного ресурса в условиях малоциклового нагружения
- 5. 1. 6. Оценка остаточного ресурса элементов оборудования с мягкими и твердыми прослойками при многоцикловом и малоцикловом нагружении
- 5. 1. 7. Расчеты ресурса элементов оборудования по критериям малоцикловой трещиностойкости
- 5. 1. 8. Оценка ресурса элементов оборудования в условиях одновременного действия малоцикловых нагрузок и механохимичес-кой коррозии и использованием критериев механики разрушения
- 5. 2. Расчетная оценка остаточного ресурса элементов оборудования с мягкими прослойками в условиях длительного статического нагружения и механохимической коррозии
- 5. 2. 1. Определение остаточного ресурса элементов оборудования с мягкими и твердыми прослойками
- 5. 2. 2. Влияние остаточных напряжений на ресурс элементов оборудования при одновременном действии напряжений и коррозии
- 5. 2. 3. Коррозионно-механические испытания
- 5. 3. Выводы по главе
- 5. 1. Определение остаточного ресурса элементов оборудования в условиях малоциклового нагружения
Список литературы
- Аснис А.Е., Иващенко Г. А. Повышение прочности сварных конструкций. — Киев: Наукова Думка, 1979. — 193 с.
- Ахметзянов М.Х. Исследование концентрации напряжений в пластической области при помощи фотоупругих покрытий. Изв. АН СССР ОТН. Механика и машиностроение. — 1963, — № 1. — с. 159−162.
- Абдуллин И.Г., Гареев А. Г., Мостовой A.B. Коррозионно-механическая стойкость нефтегазопроводных систем (Диагностика и прогнозирование долговечности). Уфа: Гилем, 1997. — 220 с.
- Агапкин В.М., Борисов С. Н., Кривошеин Б. Л. Справочное пособие по расчетам трубопроводов. М.: Недра, 1987. — 102 с.
- Абдуллин P.C. и др. Повышение работоспособности угловых швов нефтеаппаратуры. (P.C. Зайнуллин, Г. В. Москвитин, А.Г. Грибанов) Реакторы каталитических процессов и аппаратуры для подготовки нефти. М.: 1991. -21−26 с.
- Абдуллин P.C. Разработка ресурсосберегающей технологии изготовления элементов нефтехимической аппаратуры типа охватывающих и охватываемых цилиндров. 05.04.09. Автореферат. УНИ, 1990. 24 с.
- Абдуллин P.C. Расчетная оценка ресурса сосудов с механической неоднородностью. Химическое и нефтегазовое машиностроение, 1998, № 3. С. 8−9.
- Абдуллин J1.P., Абдуллин P.C. Определение ресурса накладных элементов сосудов и трубопроводов. В кн. «Обеспечение работоспособности нефтяной аппаратуры и трубопроводов». Салаватская городская типография, г. Салават-2000 с. 73 -77.
- Абдуллин P.C., Черных Ю. А. Ресурсосберегающая технология изготовления толстостенной аппаратуры. В кн. «Обеспечение работоспособности нефтяной аппаратуры и трубопроводов». ГП Салаватская городская типография. Салават, 2000. — с. 23−33.
- Зайнуллин P.C., Абдуллин P.C., Абдуллин JT.P. Формирование остаточных напряжений при сварке сосудов, находящихся под давлением. Химическое и нефтяное машиностроение, 2000, № 3-е. 12−13.
- Биргер И.А., Шорр Б. Ф., Иосилевич Г. Б. Расчет на прочность деталей машин. М.: Машиностроение, 1993. — 640 с.
- Болотин B.B. Ресурс машин и конструкций. М.: Машиностроение, 1990.-448 с.
- Бакши O.A., Зайнуллин P.C. О снятии сварочных напряжений в соединениях с механической неоднородностью приложением внешней нагрузки. Сварочное производство, 1973, № 7. — с. 3 — 7.
- Бакиев A.B. Технологическое обеспечение качества функционирования нефтегазопромыслового оборудования оболочкового типа: Автореферат дис. на соискание ученой степени доктора технических наук: 05. 04.07. М., 1984. — 38 с.
- Брукс Л.Э. Гидростатические методы испытаний трубопроводов. -Инженер-нефтяник. 1967. — № 10. — с. 74−78.
- Бубнов В.А. Деформационная обработка энергосберегающий метод снятия остаточных напряжений. — М.: Химическое и нефтяное машиностроение, № 8, 1998. — с. 30−34.
- Бобров В.А., Гусаков Б. Ф., Бобков К. А. Диагностика состояния сосудов и аппаратов на целлюлозно-бумажном комбинате. // Химическое и нефтяное машиностроение. № 4, 1994. с. 13−14.
- Болотин В.В. Ресурс машин и конструкций. М.: Машиностроение448 с.
- Бабин Л.А., Быков Л. И., Волохов В. Я. Типовые расчеты по сооружению трубопроводов. -М.: Недра, 1979. 176 с.
- Бородавкин П.П. Подземные магистральные трубопроводы. М.: Недра, 1982. 324 с.
- Бакиев A.B. Технология аппаратостроения: Учебное пособие. Уфа: Изд-во УГНТУ, 1995. — 297 С.
- Биргер И.А., Шорр Б. Ф., Иосилевич Г. Б. Расчет на прочность деталей машин. М.: Машиностроение, 1993. — 640 с.
- Бакши O.A., Качанов JI.M. О напряженном состоянии пластичной прослойки при осимметричной деформации. Изв. АН СССР. Механика, 1965, № 2, с.134−137.
- Безухов Н.И. Основы теории упругости, пластичности и ползучести. М.: Высшая школа, 1967. — 635 с.
- Берман У.И., Кузнецов Л. И., Орленков Е. А. Исследование структурных изменений в соединениях из сплавов ЭП199, полученных сваркой с принудительным охлаждением. Физика и химия обработки материалов, 1974, № 3.-е. 68−73.
- Берман У.И., Петров A.B., Швец М. Я. Влияние принудительного охлаждения при сварке на термическое растрескивание жаропрочных дисперсионно-твердеющих материалов. Сварочное производство, 1978, № 4, с. 19−20.
- Бакши O.A., Ерофеев В. П. Напряженное состояние и прочность стыкового шва с Х-образной разделкой. Сварочное производство, 1971, № 1Гс. 4−7.
- Бакши O.A., Анисимов Ю. И., Зайнуллин P.C. и др. Прочность и деформационная способность сварных соединений с композиционной мягкой прослойкой. Сварочное производство, 1974, № 10-е. 3−5.
- Бакиев A.B. Технология аппаратостроения. Уфа: УГНТУ, 1995.297 С.
- Бакиев A.B., Халимов А. Г., Зайнуллин P.C. Исследование свариваемости жаропрочных малоуглеродистых сталей типа 15Х5М. Нефть и газ, 1978, № 4-с. 81−84.
- Бакиев A.B., Халимов А. Г., Зайнуллин P.C., Афанасенко Е. А. Пути повышения качества и надежности сварного нефтехимического оборудования из хромомолибденовых сталей. // Обзорная информация. Серия ХМ-9. М.: ЦИНТИхимнефтемаш, 1987ГС. 32.
- Бакши O.A., Зайцев H.JL, Шрон Р. З. Повышение несущей способности нахлесточных и тавровых соединений с лобовыми швами. -Сварочное производство, 1977, № 9-с. 3−5.
- Бакиев A.B., Зайнуллин P.C., Гумеров K.M. Напряженное состояние в окрестности острых концентраторов напряжений в элементах газонефтяного оборудования. Нефть и газ, 1988, № 8,-с. 85−88.
- Владимиров А.И., Кершенбаум В .Я. Проблемы сертификации нефтегазового оборудования. // Нефтегазовые технологии. № 3, МАЙ-ИЮНЬ, 1998. с. 8−9.
- Вайсберг П.М., Канайкин В. А. Комплексная система диагностики и технической инспекции газопроводов России. Доклады Международной конференции «Безопасность трубопроводов», Часть 1, Москва, 1995,-с. 12−24.
- Гумеров K.M., Колесов A.B. Методы определения коэффициентов интенсивности напряжений в окрестности V образных концентраторов напряжений. — Заводская лаборатория, 1989, № 6,-81−84.
- Гумбров .Г., Зайнуллин P.C., Ямалеев K.M. и др. Старение труб нефтепроводов. М.: Недра, 1995. — 218 с.
- Гутман Э.М. Механохимия металлов и защита от коррозии. М.: Металлургия, 1981. — 271 с.
- Гутман Э.М., Зайнуллин P.C. Определение прибавки к толщине стенок сосудов и трубопроводов на коррозионный износ. 1983, — № 11. — с. 38−40.
- Гутман Э.М., Зайнуллин P.C. Оценка скорости коррозии нагруженных элементов трубопроводов и сосудов давления. Физико-химическая механика материалов. — 1984, — № 4. — с.95−97.
- Гутман Э.М., Зайнуллин P.C., Зарипов P.A. Кинетика механохимического разрушения и долговечность растянутых конструктивныхэлементов при упруго-пластических деформациях. Физико-химическая механика материалов. — 1984, № 2. — с. 14−17.
- Гутман Э.М., Зайнуллин P.C.K методике длительных коррозионно-механических испытаний металла газопромысловых труб. Заводская лаборатория. — 1987, № 4. 63−65.
- Гутман Э.М., Зайнуллин P.C., Шаталов А. Г., Зарипов P.A. Прочность газопромысловых труб в условиях коррозионного износа. М.: Недра, 1984. 84 с.
- Гумеров P.C., Комплексная система обеспечения работоспособности нефтепроводов. Автореферат дис. на соискание ученой степени доктора технических наук: 05.15.12. УГНТУ, Уфа, 1997. 47 с.
- Гафаров H.A., Гончаров A.A., Кушнаренко В. М. Методы контроля сварных конструкций, контактирующих с наводороживающими средами. // Сварочное производство. № 12, 1997. с. 18−21.
- Гумеров K.M., Бакши O.A., Зайцев Н. Д., Колесов A.B. Исследование напряжений в сварных соединениях с V образными концентраторами. В кн.: Применение математических методов и ЭВМ в сварке. — Ленинград: ЛДНТП, 1987-С. 73−77.
- Галлямов А.М. Роль структурных факторов в формировании ресурса элементов нефтехимического оборудования из ст. 3. Автореферат диссертации на соискание ученой степени канд техн. наук. 05.04.09. Уфа, 1996.- 21 с.
- Гумеров А.Г., Зайнуллин P.C., Ямалеев K.M. и др. Старение труб нефтепроводов. М.: Недра, 1990. 224 с.
- Гальперин E.H., Рачков В. И., Кутепов С. М. и др. Методика прогнозирования остаточного ресурса безопасной эксплуатации сосудов и аппаратов по изменению параметров технического состояния. М., 1993. 90 с
- Гутман Э.М. Механохимия металлов и защита от коррозии. М.: Металлургия, 1981. — 271 с.
- ГОСТ 6996–66. Сварные соединения. Методы определения механических свойств. М.: Изд-во стандартов, 1978. — 55 с.
- ГОСТ 20 911–75. Техническая диагностика. Основные термины и определения. М.: Изд-во стандартов, 1978. — 14 с.
- ГОСТ 27.002−83. Надежность в технике. Термины и определения. -М. Изд-во стандартов, 1983. 30 с.
- ГОСТ 1497–73. Металлы. Методы испытаний на растяжение. М.: Изд-во стандартов, 1977. — 40 с.
- ГОСТ 25–506−85. Расчеты и испытания на прочность. Методы механических испытаний металлов. Определение характеристик трещиностойкости (вязкости разрушения) при статическом нагружении. М.: Изд-во стандартов, 1985. — 61 с.
- ГОСТ 25.507−85. Методы испытаний на усталость при эксплуатационных режимах нагружения. М.: Изд-во стандартов, 1985. — 31 с.
- ГОСТ 14 349–80. Сосуды и аппараты. Нормы и методы расчета на прочность. М: Изд-во стандартов, 1980. — 61 с.
- ГОСТ 25 859–83. Сосуды и аппараты стальные. Нормы и методы расчета на прочность при малоцикловых нагрузках. Изд-во стандартов, 1983.-30 с.
- ГОСТ 25 215–82. Сосуды и аппараты высокого давления. Обечайки и днища. Нормы и методы расчета на прочность. М.: Изд-во стандартов, 1986. -8 с.
- ГОСТ 24 755–81. Сосуды и аппараты. Нормы и методы расчета на прочность укреплений отверстий. М.: Изд-во стандартов, 1981. — 20 с.
- ГОСТ 25.504−82. Расчеты и испытания на прочность. Методы расчета характеристик сопротивления усталости. М.: Изд-во стандартов, 1982.- 80 с.
- Давлетшина Ф.А. Восстановление несущей способности действующего продуктопровода с ослабленной силой. Автореферат дис. на соискание ученой степени кандидата технических наук: 05.15.13. УГНТУ, Уфа 1991.-25 с.
- Зайнуллин P.C., Махов А. Ф., Набережнев A.B. и др. Определение остаточного ресурса сосудов и аппаратов нефтеперерабатывающих заводов. -М.: ЦИНТИХИМНЕФТЕМАШ, 1991. 55 с.
- Зайнуллин P.C. Механика катастроф. Обеспечение работоспособности оборудования в условиях механохимической повреждаемости. МНТЦ «БЭСТС». Уфа, 1997. — 426 с.
- Зайнуллин P.C., Вахитов А. Г. Влияние предыстории нагружения на ресурс сварных обечаек с острыми угловыми переходами. МНТЦ «БЭСТС». -Уфа, 1997. -24 с.
- Зайнуллин P.C. Обеспечение работоспособности оборудования для подготовки и переработки нефти в условиях механохимической повреждаемости. Дис. на соискание ученой степени доктора технических наук: 05.04.09. УНИ, Уфа, 1987. — 523 с.
- Зайнуллин P.C., Гумеров А. Г., Морозов Е. М. и др. Гидравлические испытания действующих нефтепроводов. М.: Недра, 1990. 224 с.
- Зайнуллин P.C., Чабуркин В. Ф., Зыков А. К. и др. Методика контроля и оценки пригодности труб, бывших в эксплуатации. М.: Металлургия, 1996. 12 с.
- Зайнуллин P.C., Шарафиев Р. Г., Ямуров Н. Р. и др. Оценка ресурса оборудования по параметрам испытаний и эксплуатации //Заводская лаборатория (техническая диагностика), 1996- № 6. с. 57−58.
- Зайнуллин P.C., Тулумгузин М. С., Постников B.B. Определение параметров гидравлических испытаний. Строительство трубопроводов. -1981, № 9.-с. 23−25.
- Зайнуллин P.C. Влияние давления испытания на долговечность труб, работающих в коррозионных средах. Нефтяное хозяйство. — 1987, № 1. — с. 54−56.
- Зайнуллин P.C. Оценивать долговечность трубопроводов по результатам гидравлических испытаний. Строительство трубопроводов. М., 1980. — с. 32−33. .
- Зайнуллин P.C. Несущая способность сварных сосудов с острыми поверхностными дефектами. Сварочное производство. 1981, № 3.
- Зайцев К.И. Межотраслевой семинар «Старение трубопроводов, технология и техника их диагностики и ремонта». // Трубопроводный транспорт нефти. 1996, № 11,-с. 15−18.
- Зорин Е.Е. Некоторые направления развития методов и средств диагностики конструкций в процессе эксплуатации. Техническая диагностика и неразрушающий контроль. 1995, № 3−27−30 с.
- Зыков Д.К., Маслов Л. И., Пенкин А. Г. Методика проведения акустико-эмиссионной диагностики и контроля состояния материала в изделиях и технических конструкциях. М., 1994. 15 С.
- Зайнуллин P.C., Халимов A.A. Ремонт сваркой элементов оборудования из стали 15Х5М без опорожнения от продукта. // В кн.: Обеспечение работоспособности нефтяной аппаратуры. Уфа: БашНИИстрой, 1999,-с. 43−56.
- Зайнуллин P.C., Халимов A.A., Халимов А. Г. Особенности ремонта нефтегазохимического оборудования из жаропрочных хромомолибденовых сталей. // В кн.: Обеспечение работоспособности нефтепроводов и сосудов давления. Уфа, ИПТЭР, 1999,-с. 52−61.
- Земзин В.Н. Сварные соединения разнородных сталей. М.: Машиностроение, 1996. — 232 с.
- Зайнуллин Р., Бакши O.A., Абдуллин P.C., Вахитов А. Г. Ресурс нефтехимического оборудования с механической неоднородностью. М.: Недра, 1998. — 268 с.
- Зайнуллин P.C., ШарафиевР.Г. Сертификация нефтегазохимического оборудования по параметрам испытаний. М.: Недра, 1998.-447 с.
- Зайнуллин P.C., Бакши O.A., Абдуллин P.C. Ресурс нефтехимического оборудования с механической неоднородностью. М.: Недра, 1998.-268 с.
- Зайнуллин P.C., Черных Ю. А. Особенности гидравлических испытаний сосудов и аппаратов повышенным давлением. Информационный сборник ЦИНТИХИМНЕФТЕМАШ, 1992 г., № 2гс. 22−23.
- Зайнуллин P.C., Черных Ю. А., Шарафиев Р. Г. и др. Роль гидравлических испытаний в формировании показателей качества нефтегазоперерабатывающего оборудования и нефтепроводов. МНТЦ «БЭСТС», Уфа, 1997 г. 88 с.
- Зайнуллин P.C., Халимов A.A. Оценка остаточных напряжений при ремонте под давлением сосудов и аппаратов из стали 15Х5М. // В сб.: Шаг в XXI век. Тезисы докл. III -го междунар. Конгресса «Защита-98″. Секция № 2. М.: „Нефть и газ“, 1998,-с. 69−70.
- Зайнуллин P.C., Халимов А. Г., Халимов A.A. Методика определения трещиностойкости сварных соединений из закаливающихся сталей. Уфа: УГНТУ, 1996. — 27 с.
- Зайнуллин P.C., Черных Ю. А., Бубнов В. А. Снижение металлоемкости и повышение работоспособности кольцевых деталей химической нефтяной аппаратуры. М.: ЦИНТИХИМНЕФТЕМАШ, 1992 г. -77 с.
- Зайнуллин P.C., Абдуллин P.C., Осипчук И. А. Повышение прочности и долговечности сварных элементов нефтехимической аппаратуры. М.: ЦИНТИХИМНЕФТЕМАШ, 1990. 63 с.
- Зайнуллин P.C. Определение остаточного ресурса нефтепроводов. М.: Недра, 1998.-203 с.
- Зайнуллин P.C., Махутов H.A., Морозов Е. М. и др. Механика катастроф. Методика расчетной оценки ресурса элементов оборудования объектов котлонадзора. МНТЦ „БЭСТС“, Москва, 1997. 21 с.
- Зайнуллин P.C., Абдуллин P.C. Повышение ресурса сварных соединений охватывающих и охватываемых базовых элементовнефтехимической аппаратуры. В кн.: „Обеспечение работоспособности нефтяной аппаратуры“ БАШНИИСТРОЙ, Уфа, 1999. с. 14−34.
- Ибрагимов И.Г. Определение работоспособности агрегатов нефтеперерабатывающих и нефтехимических производств с использованием экспертных систем. Автореферат диссертации на соискание ученой степени доктора технических наук 05.04.09. Уфа, 47 с.
- Ито Ю., Мураками Ю., Хасебэ Н. И др. Справочник по коэффициентам интенсивности напряжений: С74 в 2-х томах. М: Мир, 1990.- 1016 с.
- Инструкция по техническому освидетельствование сварных сосудов с внутренней тепловой изоляцией (защитной футеровкой) ВНИИнефтемаш, М., 1995. 7 с.
- Инструкция по обследованию и идентификации разрушений, вызванных коррозионным растрескиванием под напряжением (КРН). М.: РАО „Газпром“, 1994. — 18 с.
- Иванова B.C., Гордиенко JI.K., Геминов В. Н. и др. Роль дислокаций в упрочнении и разрушении металлов. М.: Наука, 1965. — 180 с.
- Инструкция по безопасному ведению сварочных работ по ремонте нефте- и продуктопроводов под давлением. РД 39−147 103−36−89 / Гумеров А. Г., Зайнуллин P.C., Халимов А. Г. и др. Уфа: ВНИИСПТнефть, 1989. — 59 с.
- Игнатов В.А., Земзин В. Н., Петров Г. Л. Влияние никеля в аустенитных швах на миграцию углерода в сварных соединениях разнородных сталей. Автоматическая сварка, 1969, № 5,-с. 9−12.
- Когаев В.П., Махутов H.A., Гусенков А. П. Расчеты деталей машин и конструкций на прочность и долговечность. М.: Машиностроение, 1985. -224 с.
- Касаткин О.Г. Расчетная оценка сопротивляемости металла шва развитию усталостных трещин. Автоматическая сварка. — 1985. — № 12. — с. 14.
- Коцаньда С. Усталостное разрушение металлов. М.: Металлургия, 1976. — 456 с.
- Карзов Г. П., Леонов В. П., Тимофеев Б. Т. Сварные сосуды высокого давления. Л.: Машиностроением, 1982. — 287 с.
- Куркин С. А. Прочность сварных тонкостенных сосудов, работающих под давлением. М.: Машиностроением, 1976. — 184 с.
- Коваленко В.В. Повышение и оценка остаточной работоспособности сварных элементов нефтехимического оборудования со смещением кромок. Автореферат диссертации на соискание ученой степени канд. техн. наук: 05.04.09. Уфа, 1997. — 23 с.
- Коваленко В.В., Набиев P.P., Вахитов А. Г. Установка для малоцикловых испытаний. В кн.: „Проблемы технической диагностики и определение остаточного ресурса оборудования“. Уфа, УГНТУ, 1996. — с. 72−74.
- Кузеев И.Р., Куликов Д. В., Мекалова Н. В. и др. Физическая природа разрушения. Уфа: Изд-во УГНТУ, 1997. — 168 с.
- Королев Н.М. Исследование термической усталости сварных соединений разнородных сталей, выполненных электродами на никелевой основе. Химическое и нефтяное машиностроение, 1979, № 2.-е. 25−26.
- Когут Н.С., Шахматов М. В., Ерофеев В. В. Несущая способность сварных соединений. Львов: Свит, 1991. — 184 с.
- Кархин В.А., Копельман Л. А. Концентрация напряжений в стыковых соединениях. Сварочное производство, 1976, № 2-е. 6−7.
- Коваленко В. В Повышение и оценка остаточной работоспособности сварных элементов нефтехимического оборудования сосмещением кромок. Автореферат дис. на соискание ученой степени канд. техн. наук: 05.04.09. УГНТУ, Уфа, 1996. 23 с.
- Ланчаков Г. А., Степаненко А. И., Недосека, А .Я., Яременко М. А. Диагностика технического состояния трубопроводов и сосудов под давлением методом акустической эмиссии. Техническая диагностика и неразрушающий контроль, 1995, № 3.-23−26 с.
- Лютцау В.Г. Современные представления о структурном механизме деформационного старения и его роли в развитии разрушения малоцикловой усталости. В кн.: Структурные факторы малоциклового разрушения. М.: Наука, 1977. — с. 5−19.
- Лащинский A.A. Конструирование сварных химических аппаратов. Л.: Машиностроение, 1981.-382 с.
- Лях Н.Г., Гайдук Б. В. Пути повышения надежности технологического оборудования и подземных хранилищ газа, М.: Химическое и нефтяное машиностроение, № 7гс. 10.
- Лившиц Л.С. Структурная неоднородность в участках сплавления и расчет состава металла сварных соединений. Сварочное производство, 1962, № 9,-с. 1−5.
- Лившиц Л.С., Бахрах Л. П. О связи между твердостью и микроструктурой сплавления аустенитных швов на перлитных сталях и химическим составом стали и швов. Автоматическая сварка 1958, № 10.-е. 81−85.
- Ланская К.А. Высокохромистые жаропрочные стали. М.: Металлургия, 1976. — 216 с.
- Лившиц Л.С. О зоне сплавления аустенитной и перлитной стали. -Сварочное производство, 1955, № 10.-с. 14−16.
- Лившиц Л.С., Хакимов А. Н. Металловедение и термическая обработка сварных соединений. М.: Машиностроение, 1989. — 336 с.
- Мэнсон С. Температурные напряжения и малоцикловая усталость. М: Машиностроение, 1974. — 344 с.
- Махутов H.A. Сопротивление элементов конструкций хрупкому разрушению. М.: Машиностроение, 1973. — 200 с.
- Морозов Е.М. Расчет на прочность при наличии трещин. В кн.: Прочность материалов и конструкций. К.: Наукова Думка, 1975.-е. 323−382.
- Малов Е.А., Карнаух H.H., Котельников B.C. и др. Методические указания по 'определению остаточного ресурса потенциально опасных объектов, подконтрольных Госгортехнадзору России. Промышленная безопасность, 1996, № 3-е. 45−51.
- Механика малоциклового разрушения. /H.A. Махутов, М. И. Бурак, М. М. Гаденин и др.- М.: Наука, 1986. 264 с.
- Миланчев B.C. Методы расчета ресурса эксплуатации сварной нефтеаппаратуры. //НТРС „Эксплуатация, модернизация и ремонт оборудования.“, 1983, № 2,-с. 7−13.
- Муханов К.К., Ларионов В. В., Хануков Х. М. Методы оценки несущей способности сварных стальных конструкций при малоцикловом нагружении. //Расчеты на прочность. М.: Машиностроение, 1976, Вып. 17.» с. 259−284.
- Махутов H.A. Деформационные критерии разрушения и расчет элементов конструкции на прочность. М.: Машиностроение, 1981. — 272 с.
- Морозов Е.М. Под редакцией проф. Зайнуллина P.C. МНТЦ «БЭСТС». Уфа, 1997. — 390 с.
- Морозов Е.М., Зайнуллин P.C., Шарафиев Р. Г. Механика развития трещин в деталях конструкций при испытаниях и эксплуатации. Уфа.: УГНТУ, 1996. 88 с.
- Методика оценки ресурса остаточной работоспособности технологического оборудования нефтеперерабатывающих, нефтехимических и химических производств. ВНИИКТНнефтехимоборудования, Волгоград, 1991.-44 с.
- Методика определения трещиностойкости материала труб нефтепроводов. РД 39−147 103−387−87. Утверждена Миннефтепромом 24.12.82.
- Механические свойства конструкционных материалов при низких температурах. Сб. Науч. Трудов: Пер. С англ. /Под ред. Фридляндера М. Н. / М.: Металлургия, 1983. 432 с.
- Механика разрушения и прочность материалов. Справочное пособие в четырех томах. К.: Наукова Думка, 1988. — 619 с.
- Медведев Ю.С., Мещерякова В. В. Влияние длительной эксплуатации при повышенных температурах на свойства стали Х5М. -Химическое и нефтяное машиностроение, 1972,№ 10,-с. 34.
- Методика оценки технического состояния и определения срока эксплуатации печей установок каталитического крекинга, отработавших проектный ресурс. М.: ВНИИнефтемаш, 1998. — 13 с.
- Макарова A.M., Мосендз М. А. Природа влияния металла шва на образование трещин в околошовной зоне. Автоматическая сварка, 1964, № 9-с. 1−10.
- Макара A.M. Исследование природы холодных трещин при сварке закаливающихся сталей. Автоматическая сварка, 1960, № 2, с. 9−33.
- Макаров Э.Л., Субботин Ю. В. Пути повышения сопротивляемости сталей образованию холодных трещин при сварке. // В кн.: Прочность сварных конструкций. Труды МВТУ. М.: Машиностроение, 1966. — с. 227 242.
- Медовар Б.Н. Сварка жаропрочных аустенитных сталей и сплавов. М.: Машиностроение, 1966. — 430 с.
- Морозов Е.М., Зайнуллин P.C., Пашков Ю. И., Гумеров P.C. и др. Оценка трещиностойкости газонефтепроводных труб. М.: МИБ СТС, 1997. -75 с.
- Методика оценки работоспособности труб линейной части нефтепроводов на основе диагностической информации. РД 39−147 105−191. Уфа: ВНИИСПТнефть, 1992. — с. 120−125.
- Методика проведения акустико-эмиссионной диагностики и контроля состояния материала в изделиях и технических конструкциях. М.: ДИЭКС, 1994. — 15 с.
- Николаев Г. А., Куркин С. А., Винокуров В. А. Сварные конструкции. Прочность сварных соединений и деформации конструкций. -М.: Высшая школа, 1982. 272 с.
- Никольс Р. Конструирование и технология изготовления сосудов давления. М.: Машиностроение, 1975. — 464 с.
- Новые методы оценки сопротивления металлов хрупкому разрушению. //Под ред. Ю. Н. Работнова. М.: Ми, 1972. — 440 с.
- Нейбер Г. Концентрация напряжений. М.: ГИТТЛ, 1974. — 204 с.
- Навроцкий Д.И. Расчет сварных соединений с учетом концентрации напряжений. Л.: Машиностроение, 1968. — 170 с.
- Неразрушающий контроль и диагностика. Справочник /В.В. Клюев, Ф. Р. Соснин, В. Н. Филимонов и др. Под ред. В. В. Клюева. -//Машиностроение, 1995. 488 с. ил.
- Нормы расчета на прочность оборудования и трубопроводов атомных и энергетических установок. М.:ЦИНТИхимнефтемаш, 1991. 44 с.
- Надршин A.C. Разработка методов оценки ресурса демонтированного оборудования нефтехимических производств. Автореферат дис. на соискание ученой степени канд. техн. наук. Уфа: УГНТУ, 1996. — 23 с.
- Нагуманов А.Х. Термосифонные теплообменники типа «ГАЗ-ГАЗ» для регулирации тепла запыленных дымовых газов.
- Автореферат дис. на соискание ученой степени канд. техн. наук: 05.04.09. УГНТУ, Уфа, 1999. 22 с.
- Окерблом Н.О., Демянцевич В. П., Байкова И. П. Проектирование технологии изготовления сварных конструкций. JL: Судпромгиз, 1963. — 602 с.
- ОСТ 26−291−94. Сосуды и аппараты стальные сварные. Технические требования. М.: ПИО ОБТ, 1994. — 320 с.
- Обеспечение работоспособности сосудов и трубопроводов. Под ред. P.C. Зайнуллина. М.: ЦИНТИхимнефтемаш, 1991. 44 с.
- Оценка допустимости коррозионных дефектов. Руди М. Дениса (лаборатория Соете, Ругент, Гент, Бельгия), № 4, 1997. с. 28−35. // Трубопроводный транспорт нефти.
- Порядок разработки декларации безопасности промышленного объекта Российской Федерации. М.: Госгортехнадзор РФ, 1996. — 22 с.
- Павловский Б.Р., Мирочник В. Л., Холзанов Н. В. Влияние эксплуатационного наводороживания на механические свойства иконструкционную прочность сталей ферритно-перлитного класса. М.: Химическое и нефтяное машиностроение, № 3, с. 17.
- Парилова В.А., Ушаков С. Г. Испытание и накладка паровых котлов. Учеб. Пособие для вузов. М.: Энергоатомиздат, 1986. — 320 с.
- Правила устройства и безопасной эксплуатации сосудов, работающих под давлением. М.: ПИО ОБТ, 1996. 242 с.
- Петерсон Р. Коэффициенты концентрации напряжений. М.: Мир, 1977.-302 с.
- Попов Ю.П. Единая нормативно-техническая база по диагностированию и прогнозированию ресурса оборудования. Безопасность в промышленности, 1996, № 6,-с. 14−18.
- Правила и нормы в атомной энергетике. М.: Энергоатомиздат, 1989.-524 с.
- Полипов А.Н., Погарский М. В. (Москва). Оценка опасности продольных трещин при сжатии композитных элементов. М.: Проблемы машиностроения и надежности машин. № 4, 1992. — с. 87−93.
- ПР 50.1.003−94. Порядок проведения Госстандартом России государственного контроля и надзора за соблюдением обязательных требований государственных стандартов, правил обязательной сертификации и засертифицированной продукции (работ, услуг).
- ППБО Правила пожарной безопасности в нефтяной промышленности. М.: Недра, 1987. — 23 с.
- Порядок разработки декларации безопасности промышленного объекта Российской Федерации. Госгортехнадзор Р. Ф., 1996. — 22 с.
- Прохоров H.H. Физические процессы в металлах при сварке Т.П. Внутренние напряжения, деформации и фазовые превращения. М.: Металлургия, 1976. — 600 с.
- Прохоров H.H., Шиганов Н. В., Мордвинцева а.В. Исследование деформаций и напряжений в зоне сварного шва в процессе сварки. //В кн.: Сварочная техника. М.: ГНТИМЛ, 1948,-с. 95−107.
- Повышение остаточного ресурса трубопроводов с накладными элементами (Руководящий документ). Разработчики: Зайнуллин P.C., Мокроусов С. Н., Абдуллин P.C., Абдуллин Л.Р.): ИПТЭР, Уфа, 1999. 20 с.
- РД 50−345−82. Методические указания. Определение характеристик трещиностойкости (вязкости разрушения) при циклическом нагружении. М.: Изд-во стандартов, 1983. — 95 с.
- РД 26−6-87. Методические указания. Сосуды и аппараты, стальные. Методы расчета на прочность с учетом смещения кромок сварных соединений, угловатости и неокруглости обечаек. М.: НИИхиммаш, 1987. -28 с.
- РД 39−147 103−361−86. Руководящий документ. Методика по выбору параметров труб и поверочного расчета линейной части магистральных нефтепроводов на малоцикловую прочность. Уфа, ВНИИСПТнефть, 1987. — 30 с.
- Рыкалин H.H., Алексеев Е. К., Прохоров H.H. // В кн.: Деформации при сварке конструкций. М.: Изд-во АН СССР, 1943,-с. 14−18.
- Рыкалин H.H. Тепловые основы сварки. 4.1. Процессы распространения тепла при дуговой сварке. М.-Л.: Изд-в'о АН СССР, 1947. -272 с.
- Романив О.H., Никифорчин. Механика коррозионного разрушения конструкционных сплавов. М.: Металлургия, 1986. — 294 с.
- РД 0385−95. Правила сертификации поднадзорной продукции для потенциально опасных промышленных производств, объектов и работ. -Госгортехнадзор России, 1995. 8 с.
- Стеклов О.И. Прочность сварных конструкций в агрессивных средах. М.: Машиностроение, 1976. — 200 с.
- Стеклов О.И. Мониторинг и прогноз ресурса сварных конструкций с учетом их старения и коррозии. // Сварочное производство. № 1, 1997. с. 16−22.
- Соркин JI.C. Остаточные напряжения в сварных соединениях трубопроводов ТЭС. М.: Энергоатомиздат, 1998. — 192 с.
- Семушкин О.Г. Механические испытания металлов. М.: Высшая школа, 1972. — 304 с.
- Серенсен C.B. и др. Несущая способность и расчеты деталей машин на прочность. М.: Машиностроение, 1975 — 488 с.
- Самсонов Ю.А., Феденко В. И. Справочник по ускоренным испытаниям судового оборудования. JL: Судостроение, 1981- 200 с.
- Структура и коррозия металлов и сплавов. / Под ред. Ульянина Е. А. М.: Металлургия, 1989. — 400 с.
- Сборка и сварка змеевиков трубчатых печей / Технологическая инструкция. Волгоград: ВНИИПТхимнефтеаппаратуры, 1987. — 62 с.
- СНиП 3.05.05−84. Технологическое оборудование и технологические трубопроводы. Mv 1985. — 29 с.
- Сергеева Т.К. Стресскоррозионное разрушение магистральных газопроводов России. Международная научно-практическая конференция по проблеме: Безопасность трубопроводов. -М.: 1995, С. 139−164.
- Суханов В.Д. Определение свойств металла по измерениям твердости. В кн.: «Проблемы механики сплошных сред в системах добычи и транспорта нефти и газа». Материалы Конгресса нефтепромышленников России. Уфа, 1998. — 83−84 с.
- Силкин В.М., Ковех В. М. и др. Оценка безопасности газопровода по критерию трещиностойкости / Надежность газопроводных конструкций. -М.: ВНИИ природных газов, 1990. с. 21−30.
- Суханов В.Д. Структура ремонтных работ на бездействующих трубопроводах. В кн.: «Проблемы механики сплошных сред в системах добычи и транспорта нефти и газа». Материалы Конгресса нефтепромышленников России. Уфа, 1998. — 70−73 с.
- Стеклов О.И. Стойкость материалов и конструкций под напряжением. М.: Машиностроение, 1990. — 384 с.
- Сурков Ю.П. и др. Анализ причин разрушения и механизмов повреждения магистрального газопровода из стали 17ГС . Физико-химическая механика материалов. — 1989, № 5. — с. 21−25.
- Сабиров У.Н. Разработка методов, оценки работоспособности трубопроводов для перекачки широкой фракции легких углеводородов (ШФАУ). Автореферат дис. на соискание ученой степени канд. техн. наук: 05.15.13. ВНИИГАЗ, Москва, 1999. 25 с.
- Собачкин A.C. Особенности технологии сварочных работ при ремонте нефтепроводов без остановки перекачки. Автореферат дис. на соискание ученой степени канд. техн. наук: 05.03.06. ЧПИ, Челябинск, 1991. -20 с.
- Сагинбаев Р.Х. Повышение работоспособности базовых элементов с патрубками в агрегатах нефтегазохимических производств. Автореферат дис. на соискание ученой степени канд. техн. наук: 05.04.09. УГНТУ, Уфа, 1999.-23 с.
- Суханов В.Д. Оценка качества демонтированных нефтепроводов. Автореферат дис. на соискание ученой степени канд. техн. наук: 05.15.13. УГНТУ, Уфа, 1999. 22 с.
- Томсен и др. Механика пластических деформаций при обработке металлов. М.: Машиностроение, 1969. — 504 с.
- Тимошенко С.П., С. Войновский-Кригер. Пластинки и оболочки. -М.: Физматгиз, 1963.
- Турмов Г. П. Определение коэффициента концентрации напряжений в сварных соединениях Автоматическая сварка, 1976, № 10, с. 14−16.
- Теоретические основы сварки / Под ред. Фролова В. В. М.: Высшая школа, 1970. — 592 с.
- Технология электрической сварки плавлением / Под ред. Патона Б. Е. Киев: Машгиз, 1962. — 663 с.
- Школьник JI.M. Скорость роста трещины и живучесть металла. -М.: Металлургия. 1973ю — 216 с.
- Шахматов М.В., Ерофеев В. В., Гумеров K.M. и др. Оценка допустимой дефектности нефтепроводов с учетом их реальной нагруженности. Строительство трубопроводов, 1991, № 12, с. 37−41.
- Шахматов М. В. Ерофеев В.В. Инженерные расчеты сварных оболочковых конструкций. Челябинск: ЧГТУ, 1995. — 229 с.
- Шахматов М.В., Ерофеев В. В. Напряженное состояние и прочность сварных соединений с переменными механическими свойствами металла мягкого участка. Сварочное производство, 1982, № 3, с. 6−7.
- Шахматов М.В. Рациональное проектирование сварных соединений с учетом их механической неоднородности. Сварочное производство, 1988, № 7-с. 7−9.
- Шахматов M.B. Несущая способность механически неоднородных сварных соединений с дефектами в мягких и твердых швах. Автоматическая сварка, 1988, № 6, с. 14−18.
- Шрон Р.З. О прочности при растяжении сварных соединений с мягкой прослойкой в условиях ползучести. Сварочное пр-во, 1970, № 5-с. 68.
- Шрейдер A.B., Дьяков В. Г. Защита от коррозии оборудования нефтеперерабатывающих и нефтехимических предприятий. Реф. Сб.: Эксплуатация, модернизация и ремонт оборудования, 1977, № 10, ЦНИИТЭнефтехим, с. 26−31.
- Шатов A.A. О вовлечении твердой прослойки в пластическую деформацию. //В кн.: Вопросы сварочного производства. Челябинск, Труды УПИ, № 63,1968, с. 102−108.
- Шарафиев Р.Г. Обеспечение безопасности нефтегазохимического оборудования параметрами испытаний и эксплуатации. Автореферат дис. на соискание ученой степени доктора техн. наук: 05.26.04., 05.04.09. КГТУ, Казань, 1999.-41 с.
- Халимов A.A. Технология ремонта конструктивных элементов нефтехимического оборудования из стали 15Х5М. Автореферат дис. на соискание ученой степени канд. техн. наук: 05.04.09. УГНТУ, Уфа, 1999. 19 с.
- Хажинский Г. М., Сухарев H.H. Расчет коэффициентов интенсивности напряжений для угловых сварных швов фланцевых соединений трубопроводов. / Монтаж и сварка резервуаров и технологических трубопроводов. -М.: 1983,-с. 58−70.
- Халимов А.Г. Обеспечение работоспособности сварного нефтехимического оборудования из хромомолибденовых сталеймартенситного класса. Дис. на соискание ученой степени докт. техн. наук -Уфа: УГНТУ, 1997. 377 С.
- Халимов A.A. Вопросы технологии сварки элементов трубопроводов из стали 15Х5М при ремонте. // В кн.: Проблемы нефтегазового комплекса России. Материалы Всероссийской научно-технической конференции. Уфа: УГНТУ, 1995, с. 23−33.
- Халимов A.A., Надршин A.C., Зайнуллин P.C. К вопросу о трещиностойкости металла длительно проработавшего оборудования. // Материалы 47-й научно-технической конференции студентов, аспирантов и молодых ученых. Том 1. Уфа: УГНТУ, 1996,-С. 73−74.
- Халимов A.A., Зайнуллин P.C., Халимов А. Г. Диагностика разрушений сварных соединений жаропрочной стали 15Х5М. // В кн.: Проблемы механики сплошных сред в системах добычи и транспорта нефти и газа. Уфа: ИПК Госсобрания РБ, 1998,-с. 92−104.
- Фармазов С.А. Оборудование нефтеперерабатывающих заводов и его эксплуатация. М.: Химия, 1978. — 352 с.
- Фокин М.Ф., Трубицин В. А., Никитина Е. А. Оценка эксплуатационной долговечности магистральных нефтепроводов в зоне дефектов. М.: ВНИИОЭНГ, 1986. — 279 с.
- Черняев К.В. Оценка прочности и остаточного ресурса магистрального нефтепровода с дефектами, обнаруживаемыми внутритрубными инспекционными снарядами. Трубопроводный транспорт нефти. — 1995. -№ 2. — с. 8−12.
- Черняев К.В. Прогнозирование остаточного ресурса линейной части магистральных нефтепроводов на основе внутритрубной дефектоскопии. Дис. на соискание ученой степени канд. техн. наук. Уфа, 1995.-200 с.
- Черняев К.В. Технология проведения работ по диагностированию действующих магистральных трубопроводов внутритрубными инспекционными снарядами. Трубопроводный транспорт нефти. — 1995? № 1 — с. 21−31.
- Черняев К.В., Васин Е. С. Применение прочностных расчетов для оценки на основе внутритрубной дефектоскопии технического состояния магистральных нефтепроводов с дефектами. Трубопроводный транспорт нефти. — 1996- № 1 — с. 11−15.275
- Черняев К.В., Васин Е. С., Трубицин В. А., Фокин м.ф. Оценка прочности труб с вмятинами по данным внутритрубных профилемеров. -Трубопроводный транспорт нефти. 1996, № 4. — с. 8−12.
- Черных Ю.А. Повышение качества нефтегазоперерабатывающего оборудования рациональным выбором свойств металла кольцевых швов и пробного давления. Автореферат дис. на соискание ученой степени канд. техн. наук: 05.04.09. УГНТУ, Уфа, 1999. 20 с.
- Ямалеев K.M., Гумеров P.C. Термический способ восстановления ресурсов пластичности металла труб нефтепроводов. Диагностика, надежность, техническое обслуживание и ремонт нефтепроводов. Уфа: ВНИИСПТнефть, 1990. — с. 27−33.
- Ясин Э.М., Черникин В. И. Устойчивость подземных трубопроводов. М.: Недра, 1968, — 176 с.
- Ямуров Н.Р. Оценка остаточного ресурса элементов нефтехимического оборудования по параметрам испытаний и эксплуатации. -В кн.: Техническая диагностика, промышленная и экологическая безопасность предприятий. Уфа: Изд-во УГНТУ, 1996. — с. 9−11.
- Ямуров Н.Р. Оценка ресурса нефтехимического оборудования по параметрам испытаний и эксплуатации. Автореферат дис. на соискание ученой степени канд. техн. наук: 05.04.09. УГНТУ, Уфа, 1997. 23 с.276