Разработка высокоэффективной ресурсосберегающей технологии производства колец из жаропрочных сплавов на основе исследования процесса осадки заготовок
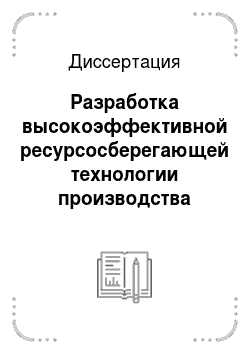
Диссертация
В настоящее время ужесточаются требования к повышению топливной экономичности летательных аппаратов. Активно разрабатывают и внедряют экономичные крупногабаритные двигатели нового поколения, в которых используют кольца диаметром до (3200−3600) мм и высотой до (800−1200) мм. В энергетическом и атомном машиностроении установлена общемировая тенденция перехода на сверхкритические параметры пара… Читать ещё >
Содержание
- Глава 1. Аналитический обзор литературы
- 1. 1. Разновидности, назначение и способы производства кольцевых изделий
- 1. 2. Характеристика основных операций производства колец
- 1. 2. 1. Осадка заготовок
- 1. 2. 2. Прошивка заготовок
- 1. 2. 3. Раскатка кольцевых заготовок
- 1. 3. Характеристика основных методов исследования местных деформаций при горячем деформировании заготовок
- 1. 4. Характеристика объектов деформирования
- Выводы по аналитическому обзору литературы
- Глава 2. Исследование основных технологических параметров при горячем деформировании заготовок
- 2. 1. Исследование деформированного состояния заготовок при осадке
- 2. 2. Влияние диаметра прошивня на распределение местных деформаций в заготовке при прошивке
- 2. 3. Исследование теплового состояния заготовок при осадке и прошивке
- 2. 4. Расчет усредненных показателей деформации (коэффициентов укова) при раскатке колец
- 2. 5. Разработка конструкции бойков для управления занообразованием при осадке заготовок
- 2. 6. Правовая защита разработанного инструмента
- Выводы по Главе 2
- Глава 3. Планирование полного факторного эксперимента при поиске оптимальных условий осадки заготовок комбинированным инструментом
- 3. 1. Установление параметров оптимизации процесса осадки
- 3. 2. Подбор технологических факторов
- 3. 3. Составление матрицы планирования эксперимента
- 3. 4. Результаты планирования и эксперимента на ЭВМ
- 3. 5. Составление уравнений регрессии
- 3. 6. Обоснование интегрального параметра оптимизации
- 3. 7. Интерполяция результатов расчета параметров оптимизации
- 3. 8. Поиск области оптимума процесса осадки при производстве колец
- 3. 9. Разработка программ и графоаналитического инструмента для расчета технологических факторов процесса осадки заготовок
- Выводы по Главе 3
- Глава 4. Разработка промышленной технологии горячего деформирования колец
- 4. 1. Изучение технического состояния производства колец на ОАО «Русполимет»
- 4. 2. Построение и последовательный план промышленного эксперимента
- 4. 3. Обоснование, разработка и реализация новой технологии горячего деформирования заготовок
- Выводы по Главе 4
- Глава 5. Оценка эффективности и ресурсосбережения разработанной технологии горячего деформирования заготовок
- ВЫВОДЫ ПО ДИССЕРТАЦИИ
Список литературы
- Патон Б.Е., Медовар Б. И. Горячая раскатка стальных колец и обечаек. К.:
- Наукова думка", 1993. 240 с.
- Ильин М.М. Производство стальных цельнокатаных колец заготовок. — М.:
- Гос. изд. обор, пром.", 1957. 127 с.
- Костышев В.А., Шитарев И. Л. Раскатка колец. Самара, 2000. — 208 с.
- Охрименко Я.М. Технология кузнечно-штамповочного производства.
- Учебник для вузов. Изд. 2-е, перераб. и доп. М.: «Машиностроение», 1976.-560 с.
- Соколов Л.Н., Золотухин Н. М., Ефимов В. Н. Ковка слитков на прессах. К.:1. Техшка", 1984. 127 с.
- Исаченков Е.И. Технология и оборудование кузнечно-штамповочногопроизводства. Экспресс-информация, № 9, 1980, С. 1−9.
- Тюрин В.А., Мохов А. М. Теория обработки металлов давлением: Учебник длявузов. Волгоград: ВолгГТУ, 2000. — 416 с.
- Охрименко Я.М., Тюрин В. А. Теория процессов ковки. Учебное пособие длявузов. М.: «Высш. школа», 1977. — 295 с.
- Громов Н.П. Теория обработки металлов давлением. М.: «Металлургия», 1967.-312 с.
- Дзугутов М.Я. Пластическая деформация высоколегированных сталей исплавов. Изд. 2-е, перераб. и доп. М.: «Металлургия», 1977. — 480 с.
- Тюрин В.А. Теория и процессы ковки слитков на прессах. М.:
- Машиностроение, 1979. 240 с.
- Тюрин В.А., Янин B.B. Теория и технология процессов ковки и прессования.
- Учебное пособие. М., 2000. — 68 с.
- Полухин П.И., Тюрин В. А., Давидков П. И., Витанов Д. Н. Обработкаметаллов давлением в машиностроении. М.: «Машиностроение" — София: „Техника“, 1983. — 279 с.
- Громов Н.П. Теория обработки металлов давлением. Изд. 2-е перераб. и доп.-М.: Металлургия, 1978. 360 с.
- Сторожев М.В., Попов Е. А. Теория обработки металлов давлением. Учебникдля вузов. Изд. 4-е перераб. и доп. М.: Машиностроение, 1977. — 423 с.
- Остроушкин Г. П., Чиркин Д. П. Прогрессивные способы раскатки заготовокколец подшипников. М., 1978. — 86 с. 19Евстифеев В. В. Технология и оснастка специальных способов обработки металлов давлением. Учебное пособие.- Новосибирск, 1977. — 88 с.
- Унксов Е.П., Джонсон У., Колмогоров B.J1. Теория ковки и штамповки:
- Учеб. пособие для студентов машиностроительных и металлургических специальностей вузов. Изд. 2-е, перераб. и доп. М.: „Машиностроение“, 1992.-720 с.
- Гун Г. Я. Математическое моделирование процессов обработки металловдавлением. Учебное пособие для вузов. М.: „Металлургия“, 1983. -352 с.
- Колмогоров В.Д., Паршаков С. И., Буркин С. П. Решение технологическихзадач ОМД на микро-ЭВМ. Учебное пособие для вузов. М.: „Металлургия“, 1993. — 320 с.
- Лисицын А.И., Остренко В. Я. Моделирование процессов обработкиметаллов давлением (оптические методы). К.: „Техшка“, 1976. — 208 с.
- Д.В. Батяев, В. А. Тюрин // Известия ВУЗов. Черная металлургия.- 2010.5.- С. 68.
- Альперович М.Е. Вакуумный дуговой переплав и его экономическаяэффективность. М.: „Металлургия“, 1978. — 168 с.
- ТУ 14−1-1531−75. Поковки-штанги круглого сечения из высоколегированныхсталей и сплавов. М.: Изд-во стандартов. 1975.
- Швед Ф.И. Слиток вакуумно-дугового переплава. Челябинск, 2009. — 428 с.
- В.А. Тюрин, Д. В. Батяев // Кузнечно-штамповочное производство.
- Обработка материалов давлением. 2012. — № 10. — С. 40 — 44. 29Балясный И.М. // Кузнечно-штамповочное производство. — 1960. — № 4.-С. 19−23.
- ЗОБалясный И.М. // Кузнечно-штамповочное производство. 1961. — № 2.— С. 8−15.
- Балясный И.М. // Кузнечно-штамповочное производство. 1967. — № 5,1. С. 11−13.
- Березкин В.Г. Формоизменение при обработки металлов давлением. М.:
- Машиностроение», 1973. 152 с.
- Патент РФ № 2 028 860, В21Н 1/06. Способ изготовления стальных кольцевыхизделий. / А. Г. Береснев.
- Патент РФ № 2 342 215, В21Н 1/06. Способ изготовления раскатныхкольцевых заготовок из высоколегированных никелевых сплавов. / A.B. Конюхов, О. Н. Кутепов, Ю. В. Процив.
- Патент РФ № 2 198 760, В21Н 1/06. Способ изготовления раскатныхкольцевых заготовок из высоколегированных никелевых сплавов. / Н. М. Рябыкин, Ю. В. Процив.
- Патент РФ № 2 192 328, В21Н 1/06. Способ изготовления раскатныхкольцевых заготовок из высоколегированных никелевых сплавов. / Н. М. Рябыкин, Ю. В. Процив.
- Авторское свидетельство № 1 569 065, В21Н 1/06. Способ изготовлениякольцевых изделий. / В. И. Хейфец, JI.A. Левицкий, П. П. Быков и др.
- Авторское свидетельство № 1 687 343, B21D 53/16. Способ изготовленияплоских колец из листового металла. / В. И. Ларин.
- Патент РФ № 2 332 276, В21К 1/38. Способ изготовления кольцевой детали. /
- С.Т. Басюк, В. М. Грешилов, А. П. Соловьев и др.
- Патент GB № 1 571 446, В21К 1/28. Improvements in or relating to the forging ofwheel shaped workpieces. / Hoesch Werke Aktiengesellschaft.
- Патент JP № 2 001 129 636 А 20 010 515, B21K 21/06. Method of manufacturingfor deformed ring. / Tagawa Akira, Asahi Shigemitsu.
- Патент РФ № 2 465 979, B21K 1/28, B21J 1/06. Способ производствакольцевых изделий. Бюлл. № 31, 2012. / В. А. Тюрин, Д. В. Батяев, Ю. В. Луканин, А. Л. Сапунов.
- Тюрин В.А. Методы планирования эксперимента. Раздел: Математическоепланирование и обработка эксперимента первого порядка. Курс лекций. -Москва: МИСиС., 1979. 78 с.
- Спиридонов A.A., Васильев Н. Г. Планирование эксперимента приисследовании и оптимизации технологических процессов. Учебное пособие. Свердловск, изд. УПИ им. С. М. Кирова, 1975, с. 140.
- В.А. Тюрин, Д. В. Батяев // Известия ВУЗов. Черная металлургия.- 2013.3.- С. 8−10.
- В.А. Тюрин, И. В. Ларионов, Д. В. Батяев // Известия ВУЗов. Чернаяметаллургия.- 2013.- № 7.- С. 49 51.
- ТУ 14−1-1530−75. Поковки из сталей и сплавов для деталей машин. М.: Издво стандартов. 1976.
- ОСТ 1 90 396−91. Кольца цельнокатаные точные из легированных, коррозионностойких, жаропрочных и жаростойких сталей и сплавов. Общие технические условия. М.: Изд-во стандартов. 1992.
- В.А. Тюрин, Д. В. Батяев, Ю. В. Луканин, А. Л. Сапунов, A.C. Волков,
- В.А. Чицварин // Кузнечно-штамповочное производство. Обработка материалов давлением. 2013. — № 6. — С. 23 — 28.
- ТУ 1−1018−98. Прутки из жаропрочного сплава марки ХН62ВМЮТ-ВД
- ЭП708-ВД). М.: Изд-во стандартов. 1998.
- Захаров С.Н. Справочник экономических терминов. Учебное пособие. М.:1. МИСиС", 2000. 197 с.
- Коноплицкий В, Филина А. Это бизнес. Толковый словарь экономическихтерминов. М.: «Альтерпресс», 1996. — 256 с.
- Автотрейдинг транспортно-экспедиционное предприятие // Тарифы и сроки.
- Расчет стоимости отправки. URL: http://www.ae5000.ru/rates/calculate (дата обращения 28.04.2013).
- Ковка и штамповка. Справочник. В 4-х т. / Ред. совет: Е. И. Семенов (пред.) идр. М.: «Машиностроение», 1985 — Т.1. Материалы и нагрев. Оборудование. Ковка / Под ред. Е. И. Семенова, 1985. — 568 с.
- Разработка экономических и организационных вопросов при курсовом идипломном проектировании: Учеб.-метод. Пособие / О. В. Юзов, А. М. Седых, Ф. И. Щепилов, Т. М. Петракова. М.: «МИСиС», 2001. -132 с.
- Сорокин В.Г., Гервасьев М. А. Стали и сплавы. Марочник: Справ, изд. М.:
- Интермет Инжиниринг", 2001. 608 с. 58Масленков С. Б. Жаропрочные стали и сплавы. Справ, изд. — М.: Металлургия, 1983. — 192 с.