Пути сокращения времени цикла обработки
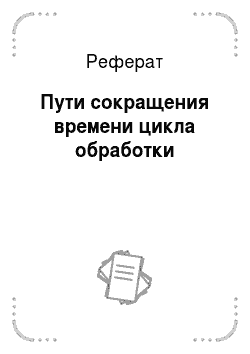
Качественные заготовки из быстрорежущей стали получают методом порошковой металлургии. Порошковая быстрорежущая сталь обладает высоким качеством структуры материала, что благотворно сказывается на режущих свойствах инструментов. После нанесения на поверхность режущих кромок тонких пленок (1—5 мкм) сверхтвердых покрытий, например TiAlN, быстрорежущие инструменты могут работать со скоростями до 125… Читать ещё >
Пути сокращения времени цикла обработки (реферат, курсовая, диплом, контрольная)
После изучения материала данной главы студент должен: знать
- • состав времени цикла обработки;
- • понятие об основном и вспомогательном времени;
- • материалы, использующиеся в современных режущих инструментах; уметь
- • повышать производительность труда за счет сокращения основного времени;
- • повышать производительность за счет сокращения вспомогательного времени;
- • использовать групповые технологические процессы в своей практической деятельности;
владеть
- • навыками выбора материала режущих инструментов;
- • использованием в технологических процессах станков с ЧПУ с целью повышения производительности;
- • достижением оптимальности технологических процессов по показателю экономичности.
Пути сокращения основного времени
К основному времени t0 при механической обработке относится сумма времени непосредственного резания ?р, при котором происходит съем стружки, и неизбежного времени врезания ?вр и перебега ?пб:

Основное время равняется отношению длины пути L, проходимого режущим инструментом по обрабатываемой поверхности заготовки, к величине минутной подачи $мин, которая равна скорости перемещения режущего инструмента, но этой поверхности.
Длина пути L равна сумме длины обрабатываемой поверхности /дст, величин врезания /вр и перебега /пб:

При i рабочих ходов длина пути увеличивается до произведения Ы.

где 5МИН — минутная подача, мм/мин.
Минутная подача при точении.

Минутная подача при обработке многолезвийным инструментом.

где 50 — подача на оборот, мм/об; s2 — подача на одно лезвие, мм/зуб; z — число зубьев многолезвийного инструмента; п — частота вращения заготовки или режущего инструмента, об/мин.
Скорость резания.

где D — диаметр обработки, мм; откуда частота вращения.

Основное время при точении.

Основное время при работе многолезвийным инструментом.

Сократить основное время можно за счет уменьшения числителя и увеличения знаменателя. Рассмотрим влияние на основное время глубины, подачи и скорости резания, т. е. тех параметров, которые относятся к режимам резания. Расчет и выбор режимов резания осуществляется в последовательности: глубина, подача, скорость резания. Правильно назначенные режимы в максимальной степени определяют достижение высокой производительности за счет сокращения основного времени.
За счет увеличения глубины можно сократить число рабочих ходов (/' в числителе). Возможности увеличения скорости резания и подачи (s и v в знаменателе) связаны с режущими способностями материалов режущих инструментов.
Виды материалов, используемые в настоящее время в режущих инструментах для лезвийной обработки, перечислены на рис. 3.1.
Быстрорежущую сталь (БС) нужно признать весьма технологичным материалом для изготовления режущих инструментов. Этот материал может до закалки подвергаться резанию лезвийными инструментами (фрезерованию, точению, сверлению и т. д.)> а после закалки — шлифованию. Это дает возможность изготавливать из быстрорежущих сталей сложные режущие инструменты: метчики, зубообрабатывающие долбяки и червячные фрезы, профильные резцы и др.

Рис. 3.1. Материалы лезвийных инструментов.
Качественные заготовки из быстрорежущей стали получают методом порошковой металлургии. Порошковая быстрорежущая сталь обладает высоким качеством структуры материала, что благотворно сказывается на режущих свойствах инструментов. После нанесения на поверхность режущих кромок тонких пленок (1—5 мкм) сверхтвердых покрытий, например TiAlN, быстрорежущие инструменты могут работать со скоростями до 125 м/мин, что близко к скоростям работы твердых сплавов.
Общая тенденция в использовании режущих инструментов состоит в стремлении заменить быстрорежущие стали твердыми сплавами, содержащими меньше вольфрама и работающими на более высоких скоростях.
Твердые сплавы (ТС) являются в настоящее время самым распространенным материалом для лезвийных режущих инструментов. Около 90% всей механической обработки в мире выполняется твердыми сплавами.
Изготавливают твердые сплавы методом порошковой металлургии из смесей зерен карбидов, нитридов, карбонитридов тугоплавких металлов в связующем материале, в качестве которого используется кобальт.
Заготовки твердосплавных инструментов имеют после спекания очень высокую твердость (до HRA 90) и в дальнейшем могут обрабатываться только шлифованием алмазными кругами.
В состав порошков входят кобальт, карбиды и нитриды титана, вольфрама, тантала. Процентное содержание кобальта может колебаться в пределах 2—15%. Чем больше в составе твердого сплава кобальта, тем выше его прочность, но ниже износостойкость.
Скорость резания при работе твердыми сплавами превышает 100 м/ мин. Инструменты из твердых сплавов в последние годы прошли путь существенного совершенствования.
Появились многогранные быстросменные неперетачиваемые пластины, использование которых дает ряд технико-экономических выгод. После спекания многогранная пластина либо вообще не подвергается механической обработке, либо обработка ее минимальна. После затупления одной из режущих кромок производят поворот пластины, и в работу вступает другая кромка. Изготавливают пластины с двумя — пятью режущими кромками, кроме того, иногда пластину можно перевернуть и работать гранями другой стороны. Изношенные пластины перемалывают в порошки, не допуская потерь дефицитных материалов, что неизбежно при затачивании.
На пластины в большинстве случаев наносят сверхтвердые покрытия. Эти покрытия имеют толщину в несколько микрометров, наносят одно-, двухи трехслойные покрытия. Пластины с покрытиями имеют высокую стойкость, что позволяет работать с более высокими скоростями резания (до 250 м/мин по черным металлам) и добиваться более высокой производительности обработки.
Кроме отечественных твердых сплавов по ГОСТ 3882–74, регламентирующем}' вольфрамовые сплавы ВК, титановольфрамовые ТК, титанотанталовольфрамовые ТТ, в стране используют много твердосплавных пластин зарубежных производителей, ведущее место среди которых занимают фирмы Sandvik Coromant, Iscar, Kennametal, Hertel, Walter, Seco, Mitsubishi. Число марок превышает несколько сотен. Как разобраться в этом многообразии и грамотно использовать инструмент для оптимальной обработки конкретных материалов, чтобы получить наибольший эффект? Ведь одни сплавы обладают высокой прочностью, но недостаточной износостойкостью, иные, наоборот, при уменьшенной прочности обладают высокой износостойкостью. Область применения одних — чистовая обработка, других — черновая.
Стандарт ISO предусматривает деление всех твердых сплавов на шесть групп применения и несколько подгрупп — от 05 до 40 (табл. 3.1).
В ячейки таблицы вносят марки твердых сплавов. Деление на группы и подгруппы применения позволяет ориентироваться в эффективном использовании пластин, не допуская ошибок. Для удобства использования твердосплавные пластины маркируют не маркой материала, а буквой группы и номером подгруппы применения, а упаковка имеет определенную окраску.
Отечественные твердые сплавы ранее делились на три группы применения — Р, М и К (см. табл. 3.1).
Сплавы группы применения Р (буква латинская) предназначены для обработки материалов, дающих сливную стружку. К таким материалам относится большинство низкои среднелегированных сталей, стальное литье, ковкий чугун. Маркируются полосой синего цвета.
Сплавы группы применения М предназначены для обработки труднообрабатываемых материалов (высокопрочных и нержавеющих аустенитных сталей, высоколегированных, высокомарганцовистых, никелевых, молибденовых, вольфрамовых и ниобиевых сплавов). Маркируются полосой желтого цвета.
Сплавы группы применения К предназначены для обработки материалов, дающих стружку надлома (серый и отбеленный чугун, пластмассы, стеклопластики, бетон, древесина). Маркируются полосой красного цвета.
Увеличение содержания кобальта переводит сплав в подгруппу с увеличенным номером. Некоторые сплавы успешно работают в двух смежных подгруппах, а сплавы со сверхтвердыми покрытиями даже в разных группах применения. Это неудивительно, ведь у них вязкая, прочная сердцевина и износостойкая режущая кромка.
В последнее время образованы дополнительно три группы применения: N, 5 и Я.
Группы и подгруппы применения твердых сплавов.
Подгруппы. | Изменение свойств. | ||||
Р | М | К | |||
Т30К4. | ВК6-ОМ. | ВКЗ, ВК6-ОМ. | Износостойкость —>? | Прочность <; | |
Т15К6. | ТТ8К6. | ВКб, ВК4. | |||
Т15К6. | ТТК8Б. | ВК8. | |||
Т5К10. ТТ10К8Б. | ТТ7К12. ВК8. | ВК8. | |||
Т5К12,. ТТ7К12. | ТТ7К12. | ВК10, ВК15. |
Сплавы группы применения N выделены в последние годы из группы применения К, предназначены для обработки алюминиевых сплавов, меди и ее сплавов. Маркируются полосой зеленого цвета.
Сплавы группы применения S выделены из группы применения М, предназначены для обработки жаропрочных сталей и титановых сплавов. Маркируются полосой розового цвета.
Сплавы группы применения Я предназначены для обработки материалов высокой твердости. Маркируются полосой серого цвета.
Пластины импортного производства маркированы дополнительно к марке сплава подгруппой применения.
Подгруппы применения 05, 10, 20, 30, 40 перечислены в порядке повышения прочности сплава. Одновременно с повышением прочности снижается износостойкость. Например, сплав Т5К10 (РЗО), который содержит 10% кобальта, обладает большей прочностью в сравнении со сплавом Т15К6 (Р15 — Р25), и еще большей прочностью, чем сплав Т30К4 (Р05). Но последний из перечисленных сплавов является наиболее износостойким.
Сплав ВКЗ-М (Я10) обладает высокой износостойкостью, а сплав ВК8 с меньшей износостойкостью, но с более высокой прочностью работает в нескольких подгруппах применения (К20 — КЗО).
Безвольфрамовые твердые сплавы (керметы) пригодны для чистовой обработки, при которой они показывают по износостойкости и качеству обработки зачастую лучшие результаты, чем вольфрамосодержащие сплавы.
К сверхтвердым материалам (СТМ) относят алмазы, композиты и режущую керамику.
1. Алмазы подразделяются на естественные и искусственные. Этот материал является наиболее твердым из всех существующих в природе. Однако он совершенно непригоден для обработки на высоких скоростях черных металлов (стали и чугуна) в связи со сродством элемента (углерода), из которого он состоит, и который одновременно входит в состав обрабатываемого материала. Из крупных (свыше 1 карата) зерен алмазов изготавливают резцы для обработки цветных металлов и их сплавов, инструменты для правки абразивных кругов.
В качестве абразивного материала мелкие алмазные зерна и порошки служат для шлифования и притирки твердых сплавов. Алмазы широко используют в инструментах, которыми правят шлифовальные круги. Стойкость шлифовальных кругов сравнительно невелика. Это обусловлено двумя причинами:
- 1) зерна тупятся;
- 2) круги засаливаются. Последний термин означает насыщение связки круга срезанными продуктами шлифования.
При правке алмазный правящий инструмент выкрашивает затупившиеся зерна и срезает засаленную связку. Более подробно это будет рассмотрено в разделе шлифования.
2. Композиты по своим свойствам и способам изготовления подобны искусственным алмазам. И те и другие изготавливают из исходного сырья при высокой температуре и высоком давлении. Для алмазов сырьем служат порошки углерода, для композитов — нитрид бора. Марки широко используемых композитов: 01, 05, 10.
Композит 01 — кубический нитрид бора, имеет название эльбор (ленинградский бор). Этот материал прекрасно работает по чугуну и закаленной стали, но плохо — по стали незакаленной. При спекании образуются монокристаллы, имеющие малые размеры (диаметр 4 мм и длина б мм).
Кристаллы композита 05 хорошо работают по чугуну и по стали невысокой твердости. Из них изготавливают круглые пластинки диаметром 6 мм, которые используют в конструкции двухи трехрядных торцовых фрез, работающих с достаточно большой глубиной резания.
Композит 10 (гексанит) имеет очень высокую прочность. К примеру, резцами из композита 10 можно растачивать закаленные кулачки токарных патронов. При резании композитами закаленных стали и чугуна оптимальной скоростью резания является 100 м/мин, при резании не закаленного чугуна можно поднимать скорость до 400—800 м/мин.
Абразивными кругами из эльбора на керамической связке шлифуют и затачивают инструменты из быстрорежущей стали.
3. Режущую керамику получают путем спекания диоксида алюминия А1203. Используют белую, серую и черную керамику. В состав серой и черной керамики входит карбид титана TiC. Белая и серая керамика прекрасно работают по незакаленной стали со скоростью до 250 м/мин, черная — по чугуну и по закаленной стали со скоростью 100 м/мин. Из керамики изготавливают многогранные пластины различной формы.
Имеется керамика на основе оксида кремния.
Используют также керамику в виде сверхтвердых покрытий твердосплавных пластин.
Сверхтвердые материалы, работающие на высоких скоростях резания, востребованы на станках с ЧПУ. Во-первых, закрытая ограждениями зона резания создает безопасные условия работы оператора. Во-вторых, высокая частота вращения определяет высокую минутную подачу перемещения режущих инструментов относительно заготовок. На ручных станках рабочий не успевал среагировать, когда требовалось прекратить движение подачи, а для станков с ЧПУ такой проблемы не существует.
Появилась возможность заменить традиционное шлифование закаленных поверхностей лезвийной обработкой. Выбор материала режущей части инструмента для «твердого точения», «твердого фрезерования» (такие термины приняты в технической литературе) осуществляют в соответствии с рис. 3.2.

Рис. 3.2. Выбор материала инструмента для лезвийной обработки закаленных поверхностей.
Металлорежущие станки по силовым и скоростным характеристикам обязаны не ограничивать возможности режущих инструментов. В последние десятилетия мощность главных приводов возросла примерно в пять раз, а верхний предел частоты вращения шпинделя — более чем в два раза.