Автоматические транспортные системы
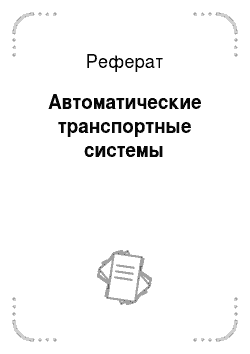
Система автоматического контроля и диагностики работы АТНС предназначается для обеспечения бесперебойного функционирования оборудования грузопереработки и его эксплуатационной надежности путем оперативного обнаружения критических и аварийных ситуаций. Система контроля и диагностики осуществляет сбор информации о состоянии наиболее ответственных узлов АТНС и элементов системы управления… Читать ещё >
Автоматические транспортные системы (реферат, курсовая, диплом, контрольная)
Автоматические транспортные системы вместе с автоматическими складами образуют единую автоматическую транспортнонакопительную систему (АТНС). Работа АТНС определяется качественными характеристиками производства и его функциональной направленностью.
Структура АТНС может быть подразделена на межцеховые, цеховые и локальные уровни (рис. 2.24).

Рис. 2.24. Уровни транспортно-накопительной системы
Транспортные связи охватывают межцеховые, межучастковые и межоперационные грузопотоки, а также все элементы перемещений, включая ориентацию и установку заготовки, съем изделий и их кассетирование.
Автоматические склады, кладовые и операционные накопители выполняют функции буферных устройств, сглаживающих нарушение ритма работы технологического оборудования.
Грузопотоки промышленного предприятия имеют множество взаимно пересекающихся и разветвленных связей (рис. 2.25).

Рис. 2.25. Грузопотоки промышленного предприятия
Местные накопители или склады содержат инструмент, оснастку, заготовки и тару. Оптимальный режим работы обрабатывающей ячейки задается многоуровневой системой управления ГАП, согласующей работу основного технологического оборудования, накопителей и транспорта. Готовые изделия, замененные или вышедшие из строя инструмент и оснастка, а также отходы по командам системы управления транспортируются в накопители. При этом могут быть предусмотрены возвратные грузопотоки многооборотной технологической тары и оснастки.
Грузопотоки определяют выбор транспортных средств. Грузы в общем случае делятся на шесть классов:
- • сыпучие,
- • штучные длинномерные,
- • штучные короткомерные,
- • штучно-массовые,
- • газообразные,
- • наливные.
Исходя из транспортно-технологических характеристик грузы классифицируются по массе, размеру, форме, способу загрузки, виду и свойствам материала.
Классификация транспортируемых изделий по массе (кг) приведена ниже: миниатюрные (до 0,01 кг), легкие (до 0,5 кг), средние (до 16 кг), переходной массы (до 125 кг) и тяжелые (более 125 кг).
По способу загрузки грузы делятся на грузы в таре, без тары, ориентированные, кассетированные, в пакетах, на спутниках или транспортируемые навалом.
По форме грузы бывают: в виде тел вращения, корпусные, дискообразные, спицеобразные и т. д.
По виду материала грузы подразделяются на металлические (сталь, цветные металлы, сплавы) и неметаллические (керамика, пластмасса, стекло, дерево и т. д.).
По свойствам материала грузы делятся на твердые, хрупкие, пластичные и магнитные.
Грузопотоки подразделяются на непрерывные и дискретные, которые, в свою очередь, могут быть ответвленными, прямоточными, возвратными или обладающими теми и другими признаками.
На основе анализа грузопотоков выбирается соответствующая структура АТНС. При многорядном расположении оборудования наиболее целесообразна структура автоматической разгрузки с разветвлением трассы, позволяющая реализовать несколько функций одним транспортным средством (рис. 2.26).
С автоматического склада заготовки в маркированной таре с помощью автоматического штабелера подаются на перегрузочный стол, который служит приемной станцией тележки, снабженной устройством для загрузки и разгрузки. Это устройство передает заготовки на накопители, а готовые изделия забирает с них по мере необходимости и в соответствии с приоритетом в обслуживании.

Рис 2.26. АТНС с разветвленной трассой:
1 — накопители, 2 — система контроля размеров, 3 — перегрузочный стол, 4 — автоматический склад, 5 — тележка, 6 — приемный стол, 7 — стол для поддонов, 8 — поддоны для отходов, 9 — технологическое оборудование
Такая схема обеспечивает гибкость в управлении передачей заготовок с оборудования при наличии контроля их размеров. В тележке также перемещаются пустые поддоны для отходов. Для складирования поддонов предназначен специальный стол. Изделия в таре подаются на приемный стол, откуда автоматическим штабелером загружаются в свободные ячейки склада.
Число транспортных связей можно уменьшить путем рациональной компоновки накопителей в зоне расположения технологического оборудования. За счет раздельного применения складов заготовок и изделий упрощаются грузопотоки обрабатываемых деталей. Благодаря размещению инструментального склада и системы контроля вблизи технологического оборудования сокращается объем транспортировки инструмента и оснастки. Отходы передаются в централизованную систему удаления отходов, которая может быть независимой от транспортных средств.
Для повышения надежности работы гибкого автоматизированного производства сборки АТНС могут включать несколько видов накопителей или складов и несколько типов транспорта. Так, на рис. 2.27 представлена компоновка ГАП сборки, имеющая склад комплектации заготовок и хранения собранных изделий, а также локальные накопители, приближенные к технологическому оборудованию или встроенные в него.

Рис. 2.27 Компоновка с использованием склада, локальных накопителей и двух типов транспорта:
- 1 — скюд комплектации заготовок и хранения собранных изделий,
- 2 — локальные накопители, 3 — подвесной робот; 4, 5 — технологическое оборудование, 6 — автоматическая тележка; 7 — заготовка
Накопители предназначены для создания страховых или технологических заделов и снабжены устройствами автоматической загрузки. Межоперационные перегрузки выполняются подвесным роботом, а связь между модулями сборки и складом комплектующих изделий осуществляется автоматической тележкой.
Экономия производственных площадей достигается при объемной компоновке ячеек ГАП. При кратковременном хранении миниатюрных и легких изделий радиопромышленности в спутниках с фиксацией экономичны подвесные накопители.
Состав технических средств АНТС включает основные и вспомогательные средства (рис. 2.28).
со
со.

Рис. 2.28. Состав технических средств АНТС
К основному оборудованию АТНС относятся конвейеры, транспортные роботы, устройства пневмои гидротранспорта, склады, стеллажи, штабелеры, ПР, а также ЭВМ, микропроцессоры, датчики и пульты управления.
К вспомогательному оборудованию АТНС относятся ориентаторы, адресователи, толкатели, сбрасыватели, накопители, подъемные и поворотно-координатные столы, подъемники, вибробункеры, перегрузочные тележки, питатели и тара.
Каждое из перечисленных технических средств АТНС подразделяется на различные типы в зависимости от назначения. Классификация основных типов конвейеров дана на рис. 2.29.

Рис. 2.29. Классификация основных типов конвейеров
Ленточные, пластинчатые и роликовые конвейеры обеспечивают высокую надежность транспортных связей. Они дешевы и просты в исполнении. Для транспортирования отходов используют скребковые, пластинчатые и винтовые конвейеры. Скребковые конвейеры позволяют повысить эффективность выполнения операции транспортировки за счет одновременного измельчения отходов неподвижными ножами, зубья которых направлены против хода тягового органа под углом. После этого отходы передвигаются скребками к концевому участку конвейера, где проваливаются в приемные конвейеры через множество различных отверстий, расположенных в шахматном порядке, что позволяет сортировать отходы по фракциям.
В АТНС применяются монорельсовые дороги (монорельсы), выполняемые в виде подвесных дорог и обслуживающие межцеховые и внутрицеховые грузопотоки. Их преимуществавысокая экономичность, большой диапазон скоростей, возможности сокращения производственных площадей, автоматического адресования и использования программного управления.
По сложности схемы дорог подразделяются на элементарные, простые и сложные. Элементарная схема не имеет ответвлений, простая схема имеет до пяти стрелочных переводов, а сложная схема может иметь множество стрелочных переводов, поворотных кругов и межэтажных подъемников. Максимальная грузоподъемность монорельсовых дорог достигает 20 т.
Монорельс можно крепить непосредственно к несущим частям производственных зданий, применяя промежуточные балки. Существуют гибкая и жесткая формы подвесных путей. Гибкая форма позволяет балке свободно поворачиваться и смещаться. Управление подвижным составом монорельса включает операции по переводу стрелок, изменению скорости движения, остановы и согласование с работой накопительных и передаточных устройств.
К недостаткам монорельсовых дорог, так же, как и конвейеров, можно отнести сложность изменения длины и направления трассы, перехода на большую грузоподъемность и достижения высокой точности позиционирования.
Важную роль в создании АТНС играют транспортные роботы. Они являются гибким средством реализации межучастковых и межоперационных связей. Преимущества транспортных роботов заключаются в малых габаритах, большом диапазоне регулирования производительности, автономности и возможности освобождения проездов после окончания работы для других видов транспорта.
На рис. 2.30 показана классификация транспортных роботов.
со
о>

Рис. 2.30. Классификация транспортных роботов
Все транспортные роботы делятся на напольные, вертикального перемещения и подвесные. Напольные транспортные роботы могут быть рельсовыми и безрельсовыми, а подвесные — монорельсовыми, консольно-крановыми и портальными. Роботы вертикального перемещения могут быть с дискретным и непрерывным движением.
В АТНС Г АП широко применяются напольные безрельсовые автоматические тележки, которые могут быть грузонесущими и тянущими. К последним относятся тягачи и буксиры с прицепами. Безрельсовые грузонесущие автоматические тележки имеют широкие возможности за счет простоты создания новых транспортных путей и оснащения их устройствами автоматизации погрузочно-разгрузочных операций, указанных в классификации. Транспортные роботы можно оборудовать подъемными, подъемно-поворотными столами и выдвижными штангами для подъема и фиксации на нужной высоте поддонов с грузами или кассет с заготовками.
В корпусе автоматической тележки монтируются электроприводы движения и поворота, питающиеся от аккумулятора, и устройство управления движением и подъемом на основе бортовой ЭВМ, устройство маршрутослежения, например оптоэлектронного типа, и датчики контроля за состоянием узлов. Для обеспечения безопасности эксплуатации применяется механическая система отключения привода от дуги безопасности, срабатывающая в случае прикосновения к препятствию. Отсчет пройденного пути производится с помощью датчика, работающего от колеса тележки. Информацию о маршруте движения тележка получает на станциях останова, размещенных у склада и технологического оборудования, посредством оптоэлектронной системы обмена информацией без электрического контакта. Маршрутослежение осуществляется по светоотражающей полосе, проведенной вдоль трассы движения. Тележка в автоматическом режиме может подходить к станции подзаряда аккумуляторов после окончания работы.
На рис. 2.31 приведена конструкция тележки с манипулятором, выполняющим погрузочные и разгрузочные операции.

Рис. 2.31. Вариант исполнения тележки с манипулятором:
- 1 — мобильная платформа, 2 — манипулятор, 3 — захватное устройство,
- 4 — детали
Робот имеет устройство, предназначенное для захвата спутников с деталями и установки их на приемные столы. Управление тележками производится от бортовой ЭВМ. Оптоэлектронная система маршрутослежения может состоять из световых маяков, расположенных в требуемой последовательности на потолке производственного помещения, и датчиков на приборах с зарядовой связью, установленных на роботе. Тележка во время движения ориентируется на световые маяки или на специальные метки на технологическом оборудовании, предназначенные для точного позиционирования тележки относительно него. Модульность конструкций тележки и робота позволяет компоновать различные модификации их сочетаний.
Безрельсовый автоматический транспорт может использоваться в технологических поточных линиях сборки, когда заготовка на тележке по ходу движения оснащается узлами и деталями вплоть до выхода готового изделия. В производстве миниатюрных и легких изделий радиопромышленности несколько автоматических тележек с автоматическим адресованием могут обслуживать подвесную транспортную систему. При этом пространственная компоновка трассы включает в себя горизонтальные и вертикальные участки, а также площадки стрелочных переходов. В пределах каждого этапа трасса образует замкнутую кольцевую линию, движение по которой осуществляется в одном направлении. На каждом этаже межэтажных участков трассы имеются поворотные устройства для замыкания внутриэтажного контура трассы и подвода тележек на вертикальные треки в зависимости от адреса.
Фрагмент компоновки АТНС с тремя транспортными роботами показан на рис. 2.32.

Рис. 2.32. Фрагмент компоновки, А ТНС с тремя транспортными роботами:
- 1 — обрабатывающие центры, 2 — транспортер, 3 — приемный стол,
- 4 — штабелер, 3 — автоматический склад, 6 — участок контроля,
- 7 — поворотные столы, 8 — транспортные роботы, 9 — загрузочные транспортеры
С автоматического склада штабелер передает заготовки на приемный стол, где они крепятся на унифицированных палетах. По мере необходимости с помощью транспортера палеты загружаются на один из трех автоматических транспортных напольных роботов, обслуживающих загрузочные транспортеры обрабатывающих центров, и загрузочные поворотные столы других многоцелевых станков с ЧПУ. Готовые изделия передаются транспортным роботом на участок контроля или на следующий участок — участок производства. Для маршрутослежения используется индукционная система. В ней информация о направлении движения, поворотах и остановах передается от управляющей ЭВМ по индукционному кабелю, вдоль которого движется транспортное средство.
Для межоперационного транспортирования изделий можно применять монорельсовые транспортные роботы. Они состоят, как правило, из электротележки, перемещающейся по монорельсу, и установленного на ней ПР. Такие транспортные роботы отличаются от монорельсовых подвесных дорог с тележками автоматического адресования тем, что имеют устройство для манипулирования изделиями и тарой. Это позволяет выполнять различные элементы технологических операций, такие, как ориентация, укладка, перенос и перестановка изделий и тары по программируемой траектории, загрузка и разгрузка подвесок грузонесущих конвейеров, а также загрузка технологического оборудования.
Системы управления транспортно-накопительными системами в общем случае имеют иерархическую структуру обработки информационных потоков, состоящую из нижнего и верхнего уровней.
Нижний уровень системы управления ЛТНС включает локальные устройства автоматизации и управления транспортным оборудованием, штабелерами и транспортными роботами. На этом уровне обеспечивается:
- — управление приводами транспортных систем;
- — точное позиционирование транспорта у рабочего места;
- — останов транспорта при аварийных ситуациях;
- — загрузка и разгрузка накопителей;
- — выработка и передача сигнала для контроля и диагностики.
Верхний уровень системы управления АТНС осуществляет:
- — задание маршрутов движения транспорта (адресование);
- — контроль и диагностику неисправностей;
- — учет движения груза.
К устройствам управления и автоматизации нижнего уровня предъявляются требования полной автоматизации транспортного процесса, сопряжения с системой управления верхнего уровня, адаптируемости к изменению транспортных потоков, модульности построения, высокой надежности устройств автоматики (наработка на отказ не менее 5000 ч), наличия на выходе унифицированного сигнала, контроля правильности работы.
В комплекс технических средств системы управления нижнего уровня обычно входят датчики, предназначенные для определения наличия или отсутствия груза, а также датчики положения транспорта, уровней для накопительных систем, усилий, безопасности и другие измерительные приборы. Использование ЭВМ позволяет реализовать логические функции управления (адресование, блокировку, переключение режимов работы приводов, управление приводами) не аппаратным, а программным путем. ЭВМ обеспечивает связь с верхним уровнем управления и придает системе гибкость и модульность. Связь ЭВМ с датчиками и исполнительными механизмами осуществляется с помощью устройства ввода-вывода.
Система автоматического контроля и диагностики работы АТНС предназначается для обеспечения бесперебойного функционирования оборудования грузопереработки и его эксплуатационной надежности путем оперативного обнаружения критических и аварийных ситуаций. Система контроля и диагностики осуществляет сбор информации о состоянии наиболее ответственных узлов АТНС и элементов системы управления, обрабатывает эту информацию по заданному алгоритму, принимает решения о возможности дальнейшего функционирования составляющих элементов АТНС и выводит информацию о неисправностях на пульт управления и индикации. Система функционирует в режимах диагностирования начального состояния АТНС и систем управления, тестовой диагностики и диагностирования текущего состояния оборудования АТНС.
В режиме диагностирования начального состояния оборудования АТНС и систем управления определяется готовность всего комплекса оборудования к началу работы. В этом режиме производится контроль цепей электропитания и управления, исходного состояния отдельных узлов АТНС, правильности исходных сигналов от датчиков положения и адресации. Диагностирование проводится в начале каждого рабочего дня перед пуском транспортно-накопительного комплекса.
Задачами режима тестовой диагностики являются проверка работоспособности основных составляющих АТНС при воздействии на них тестовых программ, а также профилактическое выявление неисправных узлов системы, параметры которых близки к отказу. Программа включает контроль за прохождением технологических команд на элементы АТНС с измерением уровня ответных сигналов и проверкой последовательности и времени их получения. В результате отработки тестовой программы на пульте оператора высвечиваются номера узлов подсистем, режимы которых не соответствуют задаваемым значениям по критериям работоспособности и прогнозирования. Данная проверка проводится перед началом работы комплекса после диагностики его состояния.
В режиме диагностирования текущего состояния оборудования АТНС контролируется правильность выполнения управляющих программ в наиболее информативных узловых точках. В память диагностического устройства вводится программа, содержащая информацию о заданных состояниях оборудования системы и элементах системы управления, соответствующих каждому шагу управления. В момент перехода к следующему шагу происходит сравнение текущих и заданных параметров с одновременным измерением времени отработки данного шага.