Порошковые материалы.
Материаловедение
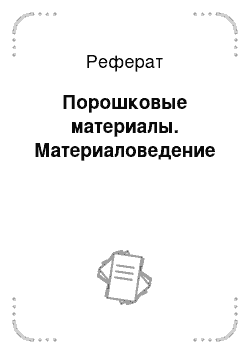
Спекание в электрических печах сопротивления или с индукционным нагревом проводят для повышения прочности предварительно полученных прессованием или прокаткой заготовок. В процессе спекания одновременно протекают такие процессы, как диффузия, восстановление поверхностных окислов, рекристаллизация и др. Температура спекания составляет 0,6—0,9 температуры плавления порошка однокомпонентной системы… Читать ещё >
Порошковые материалы. Материаловедение (реферат, курсовая, диплом, контрольная)
Металлокерамика, или порошковая металлургия, — отрасль технологии, занимающаяся производством металлических порошков с диаметром частиц 0,5—500 мкм и получением из них методом прессования и последующего спекания полуфабрикатов или готовых изделий. Порошки из пластичных и легкоплавких металлов и сплавов получают способами, основанными на раздуве жидкого материала струей воды или газа. Механическим путем (измельчением в шаровых или вибрационных мельницах), как правило, получают порошки из отходов основного производства. Режимы и технология изготовления порошков приведены в специальной справочной литературе.
Основными технологическими свойствами порошков являются текучесть, прессуемость и спекаемость.
Текучесть — способность порошка заполнять форму, которая ухудшается с уменьшением размеров частиц порошка и повышением влажности. Количественной оценкой текучести является скорость [мм*с-1] вытекания порошка через отверстие диаметром 1,5—4,0 мм.
Прессуемость — способность порошка уплотняться под действием внешней нагрузки и не разрушаться за счет сцепления частиц — зависит от пластичности материала частиц, их размеров и формы. Повысить прессуемость можно введением в состав порошка поверхностно-активных веществ.
Спекаемость — прочность сцепления частиц после термической обработки полуфабрикатов или готовых изделий.
Методом порошковой металлургии получают различные сплавы.
- • Пористые сплавы, в которых после окончания обработки сохраняется 10—30% остаточной пористости между частицами порошка.
- • Компактные сплавы, в которых после обработки остаточная пористость не превышает 1—5%.
- • Антифрикционные сплавы (табл. 10.11) изготовляют из порошков как черных, так и цветных металлов с добавками графита, который заполняет поры и является твердой смазкой.
- • Фрикционные сплавы для тормозных устройств с хорошей износостойкостью и высоким коэффициентом трения (см. табл. 10.11). Из этих материалов изготавливаются изделия в форме дисков, колодок, накладок, лент и т. д.
- • Конструкционные материалы. Наиболее часты композиции на основе железа. Марки порошковых сталей — СПХ17Н2, СПН12Х5МЗТ, СПХ23Н18 идр. (СП — сталь порошковая). Детали машин —шестерни, плоские рычаги, храповики, сепараторы подшипников и т. д. из порошковых сталей прессуют практически с окончательными размерами, что дает большой экономический эффект. Возможно создание новых композиций сплавов нестандартного химического состава с новыми свойствами.
- • Керамические твердые сплавы отличают большая твердость и теплостойкость при высокой прочности: ВК (WC + Со), ТК (WoTiC + Со), ТТК (WC + TiC + ТаС + Со). Наиболее распространены марки: ВК6, ВК20 (6,2% Со), ТЗОК6 (30% TiC, 6% Со), ТТ8К6 (TiC + ТаС — 8%, Со — 6%). Применение твердых сплавов в виде наплавок на режущую кромку инструмента позволяет повысить стойкость инструмента.
- • Сплавы с особыми свойствами. Электротехнические материалы из сплавов систем Al — Ni — Си, А1 — Со — Ni — Си используют для изготовления контактов, сердечников, индукционных катушек и т. д. Магнитно-мягкие изделия получают из порошков системы Fe — Ni, ферромагнитные материалы (постоянные магниты) — из порошков системы Al — Ni — Со.
- • Метод порошковой металлургии может быть рекомендован и для изготовления деталей простой формы (цилиндр, конус, зубчатые колеса), малой массы и небольших размеров, поверхность которых не должна иметь внутренних полостей, выемок и т. д.
Химический состав и механические свойства некоторых антифрикционных и фрикционных порошковых материалов
Марка материала. | Содержание элемента, %. | Механические свойства. | |||||
Fe. | графит. | Си. | Sn. | другие. | ав, кге • мм2 | нв | |
Антифрикционные материалы на железной основе*. | |||||||
ЖГр-1. | 1,0. | 10−18. | 50−100. | ||||
ЖГр-3. | 3,0. | 50−120. | |||||
ЖГр-7. | 7,0. | 20−35. | 50−125. | ||||
ЖГр-2Д2,5. | 95,5. | 2,0. | 2,5 сульфидов. | 20−30. | 50−125. | ||
ЖГр-2Д10. | 88,2. | 1,8. | 10 сульфидов. | —. | —. | ||
Антифрикционные материалы на медной основе**. | |||||||
БрОГрЮ-2. | 10−18. | 18−40. | |||||
БрОГр8−4. | 10−18. | 18−40. | |||||
Свинцовая бронза. | 7−72. | 0−15. | 10,5−30 РЬ. | 25−30. | 5−6. | ||
Фрикционные материалы. | |||||||
ФМК-11. | Остальное. | 6 барита; 5 В4С; 3 FeS. | 3,5−4,5. | 65−110. | |||
М КВ-50. | Остальное. | 5 SiC; 3 асбеста; 5 барита. | 3−4. | 80−120. | |||
МК-5. | Остальное. | 8 РЬ. | —. | 25−40. |
* Коэффициент трения по стали всухую и со смазкой 0,07—0,09. Железографит используют при рабочем давлении не более 100— 150 кгс/см2 и температуре 80—100 X. Структура железографита — перлит.
** Коэффициент трения бронзографита по стали всухую 0,04—0,07 и со смазкой 0,05—0,007.
Процесс приготовления смеси состоит из разделения порошков по размерам частиц (50 мкм и больше), смешивания в специальных устройствах и предварительной обработки. В металлические порошки вводят технологические присадки различного назначения — пластификаторы (парафин, стеарин, олеиновую кислоту и др.), облегчающие процесс прессования и получения заготовки высокого качества; легкоплавкие присадки, улучшающие процесс спекания, и различные летучие вещества для получения деталей с заданной пористостью. Для повышения текучести порошок иногда предварительно гранулируют. Предварительную механическую или термическую обработку (например, отжиг) применяют для повышения технологических свойств порошков.
Способы формообразования заготовок и деталей — прессование (холодное, горячее, гидростатическое) и прокатка.
При холодном прессовании в пресс-форму 2 засыпают определенное количество подготовленного порошка 3 и прессуют пуансоном 1 (рис. 10.13). В процессе прессования увеличивается контакт между частицами, уменьшается пористость, деформируются или разрушаются отдельные частицы. Прочность получаемой заготовки обеспечивается силами механического сцепления частиц порошка, электростатическими силами притяжения и трения. С увеличением давления прессования прочность возрастает. Давление распределяется неравномерно по высоте прессуемой заготовки из-за влияния сил трения порошка о стенки пресс-формы. Это является причиной получения заготовок с различной прочностью и пористостью по высоте. В зависимости от размеров и сложности прессуемых заготовок применяют одно;

Рис. 10.13. Схемы холодного прессования:
а — одностороннее; б — двустороннее и двустороннее прессование. Рабочие детали пресс-форм изготовляют из высоколегированных, инструментальных сталей и твердых сплавов.
Односторонним прессованием (см. рис. 10.13, а) изготовляют заготовки простой формы с отношением высоты к диаметру меньше единицы и заготовки типа втулок с отношением диаметра к толщине стенки меньше трех, вследствие чего обеспечивается равномерная плотность получаемых заготовок. Двусторонним прессованием с нижним пуансоном 4 (см рис. 10.13, б) получают заготовки сложной формы с равномерной плотностью. При извлечении детали из пресс-формы ее размеры увеличиваются. Величина упругого последействия в направлении прессования составляет 0,3—0,5% и 0,1—0,2% — в направлении, перпендикулярном прессованию.
При горячем прессовании технологически совмещаются процессы формообразования заготовки и получения готовой детали из твердых сплавов и специальных жаропрочных материалов спеканием. Недостатками горячего прессования являются низкая производительность, малая стойкость графитовых пресс-форм (4—7 прессовок), необходимость проведения процесса в среде защитных газов.
Гидростатическое прессование без дорогостоящих пресс-форм применяют для получения металлокерамических заготовок, к которым не предъявляют высоких требований по точности. Сущность процесса заключается в том, что порошок, заключенный в эластическую резиновую или металлическую оболочку, подвергают равномерному и всестороннему обжатию в специальных герметизированных камерах. При давлении жидкости до 3000 МПа обеспечивается пол}шение заготовок высокой прочности и плотности.
Прокатка — один из наиболее производительных способов переработки металлокерамических материалов. Прокаткой получают ленты из различных материалов (в том числе и двухслойные) толщиной 0,02—3,0 мм и шириной до 300 мм из различных металлокерамических материалов (пористых, твердосплавных, фрикционных и др.). Применение валков определенной формы позволяет получить прутки различного профиля, в том числе и проволоку диаметром от 0,25 мм до нескольких миллиметров.
Спекание в электрических печах сопротивления или с индукционным нагревом проводят для повышения прочности предварительно полученных прессованием или прокаткой заготовок. В процессе спекания одновременно протекают такие процессы, как диффузия, восстановление поверхностных окислов, рекристаллизация и др. Температура спекания составляет 0,6—0,9 температуры плавления порошка однокомпонентной системы или ниже температуры плавления основного материала для порошков, в состав которых входит несколько компонентов.
Процесс спекания рекомендуется проводить за три этана: I — нагрев до температуры 150—200 °С (удаление влаги); II — нагрев до 0,5 температуры спекания (снятие упругих напряжений и активное сцепление частиц); III — окончательный нагрев до температуры спекания. Время выдержки после достижения температуры спекания по всему сечению составляет 30—90 мин.
Для предотвращения окисления спекают в нейтральных или защитных средах, а для повышения плотности и прочности получаемые заготовки повторно прессуют и спекают. Требуемой точности достигают с помощью отделочных операций. Калибруют заготовки дополнительным прессованием в специальных стальных пресс-формах или продавливанием пруткового материала через калиброванное отверстие. При этом уплотняется поверхностный слой заготовки.
Обработку резанием (точение, сверление, фрезерование, нарезание резьбы и т. д.) применяют в тех случаях, когда прессованием нельзя получить детали заданных размеров и форм. Не рекомендуется применять обычные охлаждающие жидкости, которые, впитываясь в поры, вызывают коррозию. Пропитка маслом пористых заготовок перед обработкой также нежелательна, так как в процессе резания масло вытекает из пор и, нагреваясь, дымит. При обработке резанием используют инструмент, оснащенный пластинками из твердого сплава или алмаза (см. параграф 11.5). Для сохранения пористости при обработке необходимо применять хорошо заточенный и доведенный инструмент.