Прочностные расчеты элементов приспособлений
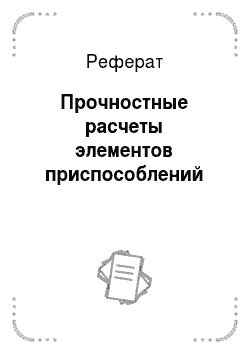
Валы и оси можно рассчитывать на жесткость, но диаметр деталей в этом случае получается больше, чем при расчете на прочность. Расчет на изгибную жесткость состоит из определения углов наклона и прогибов упругой линии осей и валов и сравнения их с допускаемыми значениями. Следует отметить и сложность расчетов деталей на жесткость. Например, расчет валов на жесткость (задача а) при кручении… Читать ещё >
Прочностные расчеты элементов приспособлений (реферат, курсовая, диплом, контрольная)
Расчет деталей приспособлений на прочность решает две задачи: а) проверку на прочность уже существующих деталей путем сравнения фактических напряжений с допускаемыми — это проверочный расчет; б) определение размеров сечений деталей — предварительный проектный расчет.
Расчет на прочность (задача а) детали в виде стержней круглого сечения, нагруженного осевой силой, по допускаемым напряжениям растяжения (сжатия) осуществляется по формуле.

где о — фактическое напряжение растяжения (сжатия), МПа; Р — расчетная осевая сила, Н; (/-диаметр опасного сечения (для резьбового стержня — внутренний диаметр резьбы), мм; [а] - допускаемое напряжение растяжения (сжатия), МПа.
Определение необходимого размера опасного сечения (задача б) для подобного случая можно производить по формуле.

Полученное значение округляется в сторону увеличения до целого или ближайшего стандартного значения. При наличии шпоночного паза в опасном сечении детали полученное расчетом значение d следует увеличить на 5… 10 %.
Расчеты на прочность валов и осей с целью определения их размеров (задача б) можно производить по следующим формулам:
• на изгиб (детали круглого сечения) d = з—г |п. ;
уоиК].
- • на изгиб (детали кольцевого сечения) d = J-7-^-;
- • на кручение d = з|—— ;
У0,2[ткр].
• на изгиб с кручением (детали круглого сечения) d = з/ '^жв ;
I
• на изгиб с кручением (детали кольцевого сечения) d = 3---^-,.
fo, l (l-*04)[a113].
где Мт — изгибающий момент, Н-мм; Мкр — крутящий момент, Н-мм; Мжв — эквивалентный момент, Н-мм; М1КВ = + М^р; [а] - допускаемое напряжение при изгибе, МПа; [ткр] - допускаемое напряжение при кручении, МПа;
ко = dold- отношение внутреннего диаметра вала (оси) do к наружному d.
Необходимо помнить, что оси рассчитываются только на изгиб, так как они не передают крутящего момента.
Валы и оси можно рассчитывать на жесткость, но диаметр деталей в этом случае получается больше, чем при расчете на прочность. Расчет на изгибную жесткость состоит из определения углов наклона и прогибов упругой линии осей и валов и сравнения их с допускаемыми значениями. Следует отметить и сложность расчетов деталей на жесткость. Например, расчет валов на жесткость (задача а) при кручении производится по формуле
где ср — действительный угол закручивания вала, град; [ф] - допускаемый угол закручивания (можно принимать для большинства валов [ф] = 15' на 1 м длины; для менее ответственных валов [ф] принимается до 2°); Мкр — крутящий момент, Н-мм; I — длина скручиваемой части вала, мм; G — модуль упру;
гости при сдвиге, МПа (для стали G = 8−10 МПа); 1р — полярный момент инерции сечения вала, мм4 {jp=nd4/ 32 — для круглого сечения и.
1р = 7 Т?/4/32^ 1 -?(4) _ДЛЯ кольцевого сечения j.
Уточненный расчет валов на прочность в случае возникновения такой необходимости заключается в определении коэффициентов запаса для опасных сечений.
При нагружении соединения силами в плоскости (по поверхности) стыка деталей и в случаях установки штифта без зазора и работы на срез проверочный расчет (задача а) штифта (винта) может осуществляться по формуле.

где Р — срезающая сила, Н; d — диаметр штифта (стержня винта), мм; i — число стыков (количество штифтов или винтов) в соединении; [тср] - допускаемое напряжение среза, МПа.
Расчет на прочность шпоночных и шлицевых соединений заключается в сравнении фактически передаваемого крутящего момента с допускаемым моментом из условий прочности шпонок (шлиц).
Расчет на прочность шпоночных соединений (задача а) производится по следующим формулам:
- • на смятие: Мкр < 0,25D/j/ [стсм] (для призматических шпонок);
- • Мкр < 0,5КП11 [асм] (для сегментных шпонок);
- • на срез: Мкр < 0,5Dhl [тсм] (для призматических и сегментных шпонок),
где Мкр — крутящий момент (рассчитывается по передаваемой мощности и частоте вращения вала), Нмм; D — наружный диаметр вала, мм; h — высота призматической шпонки, мм; АТ, — размер выступающей из паза части сегментной шпонки, мм; / - рабочая длина шпонки, мм; [стсм] - допустимые напряжения смятия, МПа.
Проверочный расчет на прочность шлицевых соединений (задача а) может осуществляться по следующим формулам:
• на смятие:
Мкр = 0,5zhli [стсм] (прямобочный профиль);
'У
Л/кр = 0,5/MZ"/7/i|;[aCM] (эвольвентный профиль);
• на срез:
Мкр =0,25z/?/v|/(D + c ()[tcm] (прямобочный и эвольвентный профили),.
где Мкр — крутящий момент, Н мм; z — число шлицев; h — высота поверхности контакта (для прямобочного профиля И = 0,5х (?> - с!) — 2здесь /ш — фаска зуба и паза шпоночного соединения, по СТ СЭВ 188−75 фаска принимается равной 0,3…0,5 мм с допуском 0,2…0,3; для эвольвентных шлицев с центрированием по боковым поверхностям И = /и, с центрированием по наружной цилиндрической поверхности h = 0,9да); D — наружный диаметр вала, мм; с! - внутренний диаметр отверстия, мм; b — ширина шлица, мм; т — модуль эвольвентного соединения, мм; vj/ - коэффициент, учитывающий неравномерность распределения нагрузки по шлицам (|/ принимается равным 0,7…0,8).
При необходимости расчеты на прочность сварных соединений, пружин, подшипников, клиноременных, зубчатых передач и других специфических сборочных единиц и деталей специальных приспособлений следует выполнять с помощью справочных и других литературных источников по сопротивлению материалов.
При значительных силах зажима следует проанализировать кинематическую цепочку передачи усилия, выделить наиболее слабые звенья и произвести их расчет на прочность, срез, иногда на устойчивость. Наиболее часто проверяется прочность на разрыв болтовых соединений, на срез — осей, пальцев, на устойчивость — длинных стержней, тяг, коромысел. Все расчеты выполняются по формулам сопротивления материалов.
Наиболее характерные виды разрушения резьбовых соединений — разрыв стержня болта (винта, шпильки) по резьбе или переходному сечению, срез или смятие витков резьбы, повреждение головки болта (винта).
Стандартизация резьб проведена с условием равной прочности всех элементов соединения. Поэтому можно ограничиваться расчетом по одному, основному критерию — прочности нарезанной части, а размеры винтов, болтов и гаек принимать по таблицам стандарта в зависимости от рассчитанного диаметра резьбы.
Если болт нагружен внешней силой F, то опасным является в данном случае сечение стержня, ослабленное нарезкой. Расчет болта на растяжение ведут по внутреннему диаметру резьбы dy.

где [ар] - допускаемое напряжение при растяжении для материала болта: для болтов из углеродистой стали рекомендуется [0р] = О, 6стш. Так можно прове.

Рис. 3.11. Схема нагружения болта в зажиме прихватом рить прочность рым-болтов, устанавливаемых для подъема тяжелых приспособлений, или соединение штоков пневмо-, гидроприводов с передаточными элементами.
Если болт затягивается с силой F3, как при зажиме детали прихватом (рис. 3.11), то стержень болта не только растягивается продольной силой F3, но и закручивается моментом в резьбе Мр. Прочность таких болтов определяется по эквивалентному напряжению
Здесь ар — напряжение от растяжения, определяемое при F = F3, тк — напряжение от кручения: тк = ]6Л/рДтк/|j; [стр] - допускаемое напряжение: [стр ] = ст)И / АГ3; К3 — требуемый коэффициент запаса прочности болта, принимаемый в зависимости от материала болта, характера нагрузки и диаметра винта.
Расчет для стандартных метрических резьб дает о3=1,Зор. Это позволяет расчет болтов.

Рис. 3.12. Схема для расчетов на срез и смятие оси при совместном их растяжении и кручении заменить расчетом только на растяжение по увеличенной за счет кручения силе Fp. Для метрических резьб Fp = 1,3 F3.
В конструкциях приспособлений часто используется система рычагов для изменения направления и величины силы зажима. Рычаги соединяются между собой в подвижное соединение с помощью осей, пальцев. Такие детали испытывают напряжения среза по сечению, а тонкие элементы рычагов (уши) ;
смятие (рис. 3.12).
Условие прочности поперечного сечения стержня:

где т, [х] - соответственно расчетное и допускаемое напряжения для материала болта на срез: [т] = (0,2…0,3)стш; d-диаметр оси, пальца.
Прочность на смятие проверяется по формуле.

где стсм,[осм] - соответственно расчетное и допускаемое напряжения смятия для материала болта: [асм] = (0,8…1,0)оот; s — наименьшая толщина детали (ушка рычага, стойки и т. и.).