Повышение эффективности наборных операций объемной штамповки за счет применения комбинированного процесса высадки и поперечного выдавливания с «бегущим» очагом деформации
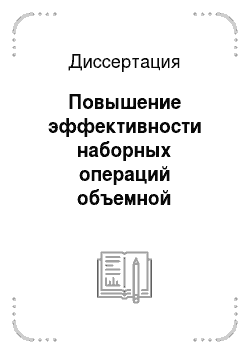
Диссертация
Практическая реализация процесса показала его эффективностьвозможность набора металла при сокращении числа переходов по сравнению с высадкой и уменьшении давления на рабочие элементы штампа по сравнению с выдавливанием. Установлено, что объем набираемого утолщения может быть ограничен только рабочим пространством применяемого оборудования (при использовании воздуха в качестве упругого элемента… Читать ещё >
Содержание
- 1. Состояние вопроса
- 1. 1. Способы получения деталей типа «стержень с утолщением»
- 1. 2. Математические модели силового режима процессов высадки и поперечного выдавливания
- 1. 3. Исследование трения при пластической деформации
- 1. 3. 1. Основные законы и модели трения
- 1. 3. 2. Методы определения коэффициента показателя) трения
- 2. 1. Возникновение «бегущего» очага деформации
- 2. 2. Определение силы комбинированного процесса
- 2. 3. Алгоритм программы расчета силы деформирования
- 2. 4. Результаты расчета силового режима комбинированного процесса
- 2. 5. Определение силового режима на основе метода баланса мощности
- 2. 6. Алгоритм программы расчета силы деформирования по методу баланса мощности)
- 2. 7. Результаты расчета силового режима комбинированного процесса (по методу баланса мощности)
- 3. 1. Материалы, оборудование и аппаратура для проведения экспериментов
- 3. 2. Порядок проведения экспериментов: осадка цилиндрических образцов
- 3. 3. Порядок проведения экспериментов: осадка кольцевых образцов
- 3. 4. Обработка результатов экспериментов и построение кривых текучести (упрочнения) выбранных материалов
- 3. 5. Аппроксимация кривых текучести (упрочнения)
- 3. 6. Результаты исследования контактного трения при деформации выбранных материалов
- 3. 7. Анализ результатов
- 4. 1. Материалы, оборудование и аппаратура для проведения экспериментов
- 4. 2. Результаты исследования течения металла при комбинированном выдавливании с «бегущим» очагом деформации
- 4. 3. Пластичность металла при комбинированном процессе с «бегущим» очагом деформации
- 4. 4. Исследование влияния трения на формоизменение в процессе комбинированного выдавливания с бегущим" очагом деформации
- 4. 5. Исследование макроструктуры полученных изделий
- 5. 1. Гипотезы, основные допущения, принятые при моделировании комбинированного процесса высадки и поперечного выдавливания
- 5. 2. Планирование численного моделирования 148 5.3. Анализ результатов численного моделирования
- 5. 3. 1. Подбор параметров процесса для получения детали, близкой по форме к экспериментальному образцу (схема 1)
- 5. 3. 2. Влияние начального соотношения L/D на течение металла (схема 2)
- 5. 3. 3. Влияние фактора трения на течение металла (схема 3)
- 5. 3. 4. Влияние геометрии заходной воронки на течение металла (схема 4)
- 5. 3. 5. Влияние жесткости пружины на течение металла (схема 5)
- 5. 3. 6. Влияние диаметра исходной заготовки на течение металла (схема 6)
- 5. 4. Основные зависимости, полученные после моделирования процесса по схемам
- 5. 5. Моделирование конусного участка заготовки
- 6. 1. Номенклатура деталей
- 6. 2. Действующий технологический процесс изготовления детали болт
- 6. 3. Штамп для набора утолщения
- 6. 4. Моделирование процесса набора утолщения
- 6. 4. 1. Гипотезы, основные допущения, принятые при моделировании технологии получения заготовки детали болт
- 6. 4. 2. Результаты моделирования
Список литературы
- Абдулаев Ф.С. Разработка и исследование технологического процесса штамповки осесимметричных поковок в закрытых штампах выдавливанием в кольцевую полость. Афтореферат дисс.канд.техн.наук. М.: МВТУ им Баумана, 1979 — 16с.
- Алиев И.С. Технологические процессы холодного поперечного выдавливания. // Кузнечно-штамповочное производство. Обработка материалов давлением. 1988, № 6 — стр. 1 — 4.
- Алиев И.С., Лобанов А. И., Борисов Р. С., Савчинский И. Г. Исследование штампов с разъемными матрицами для процессов поперечного выдавливания. // Кузнечно-штамповочное производство. Обработка материалов давлением. 2004, № 8 — стр. 21 — 26.
- Богатов А.А., Мижирицкий О. И., Смирнов С. В. Ресурс пластичности металлов при обработке давлением. М.: Металлургия, 1984 — с. 144
- Брейтуэйт Е.Р. Твердые смазочные материалы и антифрикционные покрытия (пер. с англ. С. Клюшнева: Под ред. В.Сфиницына. М.: Химия, 1967−320 с.
- Быков П.А. Исследование холодного поперечного выдавливания осесимметричных деталей: Автореферат дисс.канд.техн.наук. М.: Мосстанкин, 1980 — 20с.
- Ганаго О.А., Момзиков Ю. Г., Ватулин И. К., Сергеев Ю. Н., Субич В. Н., Степанов Б. А. Штамповка поковок шестерен в закрытом штампе с использованием активного действия сил трения. // Кузнечно-штамповочное производство. 1981, № 6 — стр. 27 — 28.
- Гневашев Д.А., Петров П. А., Петров М. А. Исследование трения при холодной деформации алюминиевого сплава АМЦ. Кузнечно-штамповочное производство. Обработка материалов давлением. М.: 2005, № 6-стр. 11−13.
- Грайфер А.Х., Однопереходная штамповка на прессах поковок типа стержней с утолщением. // Кузнечно-штамповочное производство. -1972 № 3-стр. 11−13.
- Грудев А.П., Зильберг Ю. В., Тилик В. Т. Трение и смазки при обработке металлов давлением: Справочник. -М.: Металлургия, 1982 -312 с.
- Губкин С.И. Экспериментальные вопросы пластической деформации металлов. М.: ОНТИ, 1934 — вып.1.
- Гуменюк Ю.И., Кузнецов Д. П. Общая и специальная терминология ОМД на примере классификации основных видов процесса выдавливания. // Кузнечно-штамповочное производство. Обработка материалов давлением. 2005, № 2 — стр.26−35.
- Гуяш Г. Штампы с подвижной матрицей для холодного выдавливания. // Кузнечно-штамповочное производство. Обработка материалов давлением. 1985, № 3 — стр.11−13.
- Дмитриев A.M., Воронцов A.JI., Аппроксимация кривых упрочнения металлов. // Кузнечно-штамповочное производство. Обработка материалов давлением. -2002, № 6 стр. 16−21.
- Евстифеев В.В. Научное обоснование, обобщение и разработка новых технологий холодной объемной штамповки. Дисс. докт. техн. наук: 05.03.05. Омск, 1993.
- Евстратов В.А. Основы технологии выдавливания и конструирования штампов. М.: МГТУ им. Баумана, 1994 — 422 с.
- Зибель Э. Обработка металлов в пластическом состоянии. М.: Металлургиздат, 1934.
- Исаченков Е.И. Контактное трение и смазки при обработке металлов давлением. М.: Машиностроение, 1978 — 208 с.
- Калпин Ю.Г., Басюк Т. С. Напряжение течения при горячем изотермическом деформировании. // Кузнечно-штамповочное производство. -1990, № 3 стр. 7−9.
- Калпин Ю.Г., Петров М. А., Петров П. А. Разработка нового способа получения детали типа «стержень с утолщением». // Известия ТулГУ. Серия. Механика деформируемого твердого тела и обработка металлов давлением. Тула: ТулГУ, вып.2, 2005 — стр. 50−56.
- Калпин Ю.Г., Петров М. А., Петров П.А. Experimental and numerical investigation of transverse extrusion of «rod with flange» parts. Computer Methods in Materials, Science (KomPlasTech'2007), V.7 (2007) № 3, 347 351.
- Калпин Ю.Г., Петров М. А., Петров П. А. Исследование кинематики процесса радиального выдавливания с «бегущим» очагом деформации. // Известия МГТУ «МАМИ». М: МГТУ «МАМИ», № 2(4) 2007 -стр. 164−168.
- Колмогоров B.JI. Напряжение, деформация, разрушение. М.: Металлургия, 1970 — 230 с.
- Лавриненко В.Ю. Разработка методики автоматизированного проектирования процессов высадки поковок типа стержня с шаровой головкой с направленным волокнистым строением: Автореф. дисс.канд.техн.наук: 05.03.05. -М.: МГТУ им. Н. Э. Баумана, 2004.
- Леванов А.Н., Колмогоров В. Л., Буркин С. П., Картак Б. Р., Ашпур Ю. В., Спасский Ю. И. Контактное трение в процессах обработки металлов давлением. М.: Металлургия, 1976 — 416 с.
- Мансуров A.M. Технология горячей штамповки. М.: Машиностроение, 1971 -324 с.
- Напалков А.В. Технология формообразования стержневых деталей со значительными перепадами сечения и фигурными подголовками. // Кузнечно-штамповочное производство. 2006, № 9 — стр. 30−32.
- Несвит С.М., Нюнько О. И. Горизонтально-ковочные машины и их автоматизация. -М.: Машиностроение, 1964 323 с.
- Овчинников А.Г., Грайфер А. Х., Влияние конфигурации формовочного перехода на устойчивость заготовок при высадке. // Кузнечно-штамповочное производство. 1974, № 12 — стр. 3−5.
- Оленин Л.Д. К выбору оптимального варианта получения заготовок под точную объемную штамповку. // Повышение точности и качества при штамповке. М.: МДНТП, 1975 — стр.72−79.
- Оленин Л.Д., Исследование процесса холодного комбинированного выдавливания. Дисс.канд.техн.наук: 05.03.05. -М.: МАМИ, 1967—167с.
- Оленин Л.Д., Расчет технологических переходов и конструирование инструмента для холодного комбинированного выдавливания, // Кузнечно-штамповочное производство. 1972, № 1 — стр. 9−12.
- Охрименко Я.М., Тюрин В. А. Теория процессов ковки. М.: Высшая школа, 1977−295 с.
- Перфилов В.И., Петров П. А., Петров М. А. Исследование трения при горячей изотермической деформации алюминиевого сплава АМгб. // Кузнечно-штамповочное производство. Обработка материалов давлением. 2004, № 3 — с. 15−17.
- Петров П.А., Петров М.А., Experimental and numerical investigation of friction in hot isothermal deformation of aluminium alloy A A3 003. The 8th International ESAFORM Conference on Material Forming, Romania, Cluj-Napoca, 27−29 April, 2005, pp.511−514.
- Петров П.А., Петров M.A. Устройство для исследования сопротивления металлов и сплавов горячей деформации. Патент № 46 582 РФ, МПК G01N 3/28, G01N 3/02.
- Петров П.А., Перфилов В. И., Петров М. А. Исследование трения при горячей изотермической деформации алюминиевого сплава АК 4−1. Кузнечно-штамповочное производство. Обработка материалов давлением. 2004, № 3 — с. 15−17.
- Полухин П.И., Горелик C.C., Воронцов B.K. Физические основы пластической деформации. М.: Металлургия, 1982 — 584 с.
- Семенов Е.И. Технология и оборудование ковки и горячей штамповки. М.: Машиностроение, 1999 — 384 с.
- Семенова Л.П. Холодная объемная штамповка головных частей на заготовках стержневых изделий с заданными эксплуатационными характеристиками: Автореферат дисс.канд.техн.наук: 05.03.05: Тула, 2006, М.: ПроСофт-М, 2005.
- Соловцов С.С., Быков И. А. Изготовление стерженвых деталей с фланцем поперечным выдавливанием. // Технология автомобилестроения. 1988, № 4 — стр.6−9.
- Тарновский И.Я. Формоизменение при пластической обработке металлов. М.: Металлургиздат, 1954 — 534 с.
- Трофимов И.Д., Стоколов В. Е. Оборудование для горячей штамповки с электронагревом. М.: Машиностроение, 1972 — 200 с.
- Фиглин С.З., Калпин Ю. Г., Бойцов В. В., Каплин Ю. И. Изотермическое деформирование металлов. М.: Машиностроение, 1975 — 239 с.
- Фиглин С.З., Бойцов В. В., Калпин Ю. Г. Горячая штамповка и прессование титановых сплавов. М.: Машиностроение, 1975 — 285 с.
- Хензель А., Шпиттель Т. Расчет энергосиловых параметров в процессах обработки металлов давлением. М.: Металлургия, 1982.
- Шварцман Я. О., Копылов-Хейфец С.И. Пути улучшения технологических параметров холодной высадки и объемной штамповки. // Кузнечно-штамповочное производство. 1977, № 6 -стр.36−3 8.
- Шибаков В.Г., Гончаров М. Н., Гончаров С. Н. Особенности разработки технологических процессов формообразования поковок управляемым поперечным выдавливанием. // Кузнечно-штамповочное производство. Обработка материалов давлением. 2006, № 5 — стр. 38−40.
- Billigmann J., Feldmann H.-D. Stauchen und Pressen. Handbuch fflr das Kalt- und Warmmassivumformen von Stahlen und Nichteisenmetallen. -Carl Hanser Verlag Munchen, 1973.
- Burgdorf M. Uber die Ermittlung des Fliesswertes fur Verfahren der Massivumformung durch den Ringstauchversuch. // Ind.-Anz. V.89 (1967) № 39, 15−20.
- F. Fereshteh-Saniee, I. Pillinger, P. Hartley. Friction modelling for the physical simulation of the bulk metal forming processes. // Journal of Materials Processing Technology 153−154 (2004) 151−156.
- Gronostajski Z. The constitutive equations for FEM analysis. // J. Mat.Proc. Techn., V.106 (2000) 40−44.
- Male A.T., Cocroft M.G. Method for the determination of the coefficient of friction of metals under conditions of bulk plastic deformation. //J.Instit. Metals. V.93 (1964)38−46.
- Spur G., Stoferle Th. Handbuch der Fertigungstechnik. Umformen, Band 2, Teil 2. Carl Hanser Verlag Munchen Wien, 1984.
- ГОСТ 25.503−97. Расчеты и испытания на прочность. Методы механических испытаний металлов. Метод испытания на сжатие.
- Конструкция штампового инструмента с подвижной матрицей передана в производство для проработки и для промышленного освоения. от МГТУ «МАМИ» оКФГУП ММПП «Салют"1. ЬЛ», 15-
- Результаты теоретических и экспериментальных исследований, выполненных Петрова М. А. применяются при чтении лекций по курсам «Теория обработки металлов давлением» и «Основы научных исследований».
- Настоящий акт утвержден на заседании кафедры «КиОД» (протокол № 11 от 8 ноября 2007 г.)
- Председатель комиссии: зав. каф., к.т.н., проф. Члены комиссии: д.т.н., проф. к.т.н., доц.1. FT/НЬКИН Н.Ф.
- Филиппов Ю.К./ /Перфилов В.И./