Повышение эксплуатационных свойств деталей из стали 30ХГСН2А имплантацией ионов меди и свинца
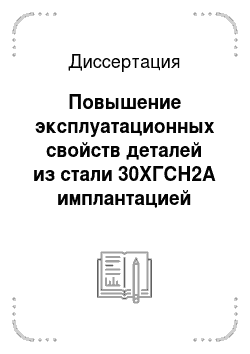
Диссертация
Анализ литературы, а также последние достижения в машиностроении, свидетельствуют о том, что наиболее перспективными методами повышения ресурса высоконагруженных деталей машин являются вакуумные ионно-плазменные технологии высоких энергий. Обработка поверхности металлов и сплавов ионными пучками существенно изменяет физико-механические, химические свойства и структуру поверхностного слоя… Читать ещё >
Содержание
- Глава 1. МЕТОДЫ СОЗДАНИЯ СЛОЕВ С ЗАДАННЫМИ СВОЙСТВАМИ НА ДЕТАЛЯХ ВЫСОКОНАГРУЖЕННЫХ ШАРНИРНЫХ СОЕДИНЕНИЙ
- 1. 1. Беспилотные летальные аппараты — современный этап развития авиационной техники
- 1. 2. Обзор современных методов создания антифрикционных покрытий
- 1. 3. Особенности повышения эксплуатационных свойств поверхностного слоя стальных деталей методом ионной имплантации
- 1. 4. Обоснование выбора сорта ионов для имплантации
- 1. 5. Цель и задачи исследований
- Глава 2. МАТЕРИАЛЫ И МЕТОДЫ ПРОВЕДЕНИЯ ИССЛЕДОВАНИЙ
- 2. 1. Химический состав и свойства стали 30ХГСН2А
- 2. 2. Оборудование для ионной имплантации
- 2. 3. Методы механических испытаний
- 2. 3. 1. Испытание образцов на растяжение
- 2. 3. 2. Испытания образцов на усталость
- 2. 4. Образцы и оборудование для испытаний на износ
- 2. 5. Металлографический анализ имплантированных слоев
- 2. 6. Растровая электронная микроскопия
- 2. 7. ОЖЕ-электронная спектроскопия
- 2. 8. Методика исследования профилей распределения имплантированных ионов методом вторичной ионной масс-спектрометрии
- 2. 9. Рентгеноструктурный анализ методом скользящего пучка
- 2. 10. Измерение микротвердости поверхностных слоев
- 2. 11. Коррозионные испытания
- Глава 3. ВЛИЯНИЕ ИМПЛАНТАЦИИ ИОНОВ МЕДИ И СВИНЦА НА СТРУКТУРУ И СВОЙСТВА СТАЛИ 30ХГСН2А
- 3. 1. Влияние последовательности имплантирования ионов меди и свинца на их распределение в имплантированном слое стали 30ХГСН2А
- 3. 2. Оценка содержания имплантированных металлов в поверхностном слое стали 30ХГСН2А
- 3. 3. Механические свойства образцов стали 30ХГСН2А после ионной имплантации
- 3. 4. Результаты испытаний образцов стали 30ХГСН2А на усталость
- 3. 5. Исследование топологии поверхности стали 30ХГСН2А до и после облучения
- 3. 6. Исследование микроструктуры имплантированного слоя стали 30ХГСН2А
- 3. 7. Результаты испытаний на износостойкость имплантированных образцов
- 3. 8. Коэффициент трения скольжения имплантированных образцов
- 3. 9. Исследование коррозионной стойкости стали 30ХГСН2А после ионной имплантации
- ВЫВОДЫ К ГЛАВЕ 3
- Глава 4. ОПТИМИЗАЦИЯ ПАРАМЕТРОВ СОВМЕСНОЙ ИМПЛАНТАЦИИ В СТАЛЬ 30ХГСН2А ИОНОВ МЕДИ И СВИНЦА
- 4. 1. Исследование влияния состава сплава меди со свинцом на свойства имплантированных образцов
- 4. 2. Влияние дозы имплантирования монотектического сплава меди со свинцом на свойства стали 30ХГСН2А
- ВЫВОДЫ К ГЛАВЕ 4.'
- Глава 5. ИМПЛАНТАЦИЯ ИОНОВ МОНОТЕКТИЧЕСКОГО СПЛАВА МЕДЬ — СВИНЕЦ В ДЕТАЛИ ЛЕТАТЕЛЬНЫХ АППАРАТОВ
- 5. 1. Промышленное опробование деталей, подвергнутых ионной имплантации
- 5. 2. Анализ результатов испытаний
- 5. 3. Совершенствование оборудования для ионной имплантации
- ВЫВОДЫ К ГЛАВЕ 5
Список литературы
- Шехтер С.Я. Наплавка металлов./ С .Я. Шехтер, A.M. Резницкий — М.: Машиностроение, 1982 72 с.
- Колганов JI.A. Сварочные работы: Сварка, резка, пайка, наплавка: учебное пособие. / JI.A. Колганов. — М: Дашков и К, 2008. 408 с.
- Бойко Н.И. Ресурсосберегающие технологии повышения качества поверхностных слоев деталей машин: учебное пособие для студентов вузов железнодорожного транспорта./Н.И. Бойко. — М: Маршрут, 2006. — 197 с.
- Зарембо Е.Г. Сварочное производство : учеб. пособие для студентов вузов ж.-д. трансп. / Е. Г. Зарембо. — М.: Маршрут, 2005. —237 с.
- Хромченко Ф.А. Сварочные технологии при ремонтных работах: справочник. / Ф. А. Хромченко. — М.: Интермет Инжиниринг, 2005. — 415 с.
- Корчагин КБ. Технологии повышения износостойкости и восстановления деталей с использованием источников высокотемпературного нагрева: учеб. пособие. / И. Б. Корчагин. Воронеж: Воронежский гос. техн. ун-т, 2005. — 146 с.
- Наплавка износостойких сплавов на прессовые штампы и инструмент для горячего деформирования сталей: монография / Г. Н. Соколов, В. И. Лысак. Федеральное агентство по образованию, Волгоградский гос. технический ун-т Волгоград: Политехник, 2005. — 283 с.
- Кортес А. Р. Сварка, резка, пайка металлов: / А. Р. Кортес. — М.: Аделант, 2003. —190 с.
- Соколов Г. Н. Износ и легирование наплавленного металла: учеб. пособие. / Г. Н. Соколов. Волгоград: Волгогр. гос. техн. ун-т, 2003. — 91 с.
- Чернышов Г. Г. Сварочное дело: Сварка и резка металлов: учебник. / Г. Г. Чернышов. -М.: Академия, 2003. 493 с.
- Сварочные работы: Учеб. пособие для студентов образоват. учреждений сред. проф. образования, обучающихся по специальностям строит, профиля / В. А. Чебан. — Ростов н/Д: Феникс, 2003. — 415 с.
- Комельков В.Н., Стулов В. В. Наплавка металлов: учеб. пособие./ В. Н. Комельков, В. В. Стулов. Комсомольск-на-Амуре: Комсомол.-на Амуре гос. техн. ун-т, 2002. — 97 с.
- Соколов Г. Н. Способы наплавки и плакирования металлов: учеб. пособие. / Г. Н. Соколов. — Волгоград: Волгогр. гос. техн. ун-т, 2002. — 80 с.
- Теория и практика нанесения защитных покрытии / П. А. Витязь, B.C. Ивашко, А. Ф. Ильющенко и др. — Минск.: Беларуская наука, 1998. — 583 с.
- Наплавка деталей машин: учеб. пособие / М. Р. Николаенко, Л.Д. Кузнецов- Брян. ин-т трансп. Машиностроения. Брянск: БИТМ, 1995. — 132 с.
- Толстое И.А., Семиколенных М. Н., Баскаков Л. В. Износостойкие наплавочные материалы и высокопроизводительные их способы их обработки. / И. А. Толстов, М. Н. Семиколенных, Л. В. Баскаков М.: Машиностроение, 1992. — 220 с.
- Толстов И.А., Короткое В. А. Справочник по наплавке. / И. А. Толстов, В. А. Коротков — Челябинск: Металлургия: Челяб. отд-ние, 1990. — 381 с.
- Маслов В.И. Сварочные работы: Учеб. для нач. проф. образования. — 2-е изд., стереотип. / В. И. Маслов. М.: ИРПО- Изд. центр «Академия», 2000.-240 с.
- Корншович С.А. Сварка и наплавка металлов при ремонте машин в сельском хозяйстве: учеб. пособие для вузов. / С. А. Корнилович. — Омск: Изд-во Омского гос. аграр. ун-та, 1997. 197 с.
- Хасуй А., Моригаки О. Наплавка и напыление пер. с яп. В. Н. Попова.- под ред. B.C. Степина, Н. Г. Шестеркина. М.: Машиностроение, 1985.-240 с.
- Пузряков А.Ф. Теоретические основы технологии плазменного напыления: учебное пособие для студентов высших учебных заведений. / А. Ф. Пузряков. -М.: Изд-во МГТУ им. Н. Э. Баумана, 2008. 375 с.
- Людаговский A.B. Газотермическое напыление покрытий: учеб. пособие. / A.B. Людаговский. — М.: Российский гос. открытый технический ун-т путей сообщ., 2006. — 43 с.
- Барвинок В.А. Плазма в технологии, надежность, ресурс. / В. А. Барвинок. М.: Наука и технологии, 2005. — 316 с.
- Бобров Г. В., Ильин A.A. Нанесение неорганических покрытий. Теория, технология, оборудование: учеб. пособие. / Г. В. Бобров, A.A. Ильин. М.: Интермет Инжиниринг, 2004. — 623 с,
- Поляк М.С. Технология упрочнения. Технологические методы упрочнения. В 2 т. / М. С. Поляк. СКРИПТ, Машиностроение, 1995. — Т.1 -832 с. Т2 — 668 с.
- Никитин М.М. Технология и оборудование вакуумного напыления. / М. М. Никитин. М. Металлургия, 1992. — 110 с.
- Кудинов В.В., Бобров Г. В. Нанесение покрытий напылением. Теория, технология и оборудование. / В. В. Кудинов, Г. В. Бобров М.: Металлургия, 1992. — 432 с.
- Лясников В.Н. Плазменное напыление / В. Н. Лясников, А. Ф. Большаков, B.C. Емельянов. Саратов: Изд-во Сарат. ун-та, 1992. — 235 с.
- Соснин H.A., Тополянский П. А., Вичик Б. Л. Плазменные покрытия: (Технология и оборудование) / H.A. Соснин, П. А. Тополянский, Б. Л. Вичик. — СПб.: ДНТП, 1992.-25 с.
- Газотермическое напыление: Под общей ред. Л. Х. Балдаева. М.: Маркет ДС, 2007. 166 с.
- Козырь A.B., Глабец Т. В., Верхотуров А. Д. Жаростойкость и коррозионная стойкость сталей после электроискрового легирования / A.B. Козырь, Т. В. Глабец, А. Д. Верхотуров. Благовещенск: изд-во АмГУ, 2006. -286 с.
- Ншоленко C.B., Верхотуров А. Д. Новые электродные материалы для электроискрового легирования. /C.B. Николенко, А. Д. Верхотуров.-Владивосток: Дальнаука, 2005.-217 с.
- Мулин Ю.И., Верхотуров А. Д. Электроискровое легирование рабочих поверхностей инструментов и деталей машин электродными материалами, полученными из минерального сырья. / Ю. И. Мулин, А. Д. Верхотуров. — Владивосток: Дальнаука, 1999 — 108 с.
- Бабенко Э.Г., Верхотуров АД. Особенности формирования покрытий на металлах методом электроискрового легирования. / Э. Г. Бабенко, А. Д. Верхотуров. Владивосток: Дальнаука, 1998.- 88 с.
- Верхотуров А.Д. Физико-химические основы процесса электроискрового легирования металлических поверхностей. /А.Д. Верхотуров-Владивосток: Дальнаука, 1992 — 173 с.
- Черненко В.И., Снежко Л. А., Папанова И. И. Получение покрытий анодно-искровым электролизом / В. И. Черненко, Л. А. Снежко, И. И. Папанова. — Л.: Химия: Ленингр. отд-ние, 1991. — 126 с.
- Верхотуров А.Д. Физико-химические основы эрозии материалов при электроискровом легировании / А. Д. Верхотуров. — Владивосток: ДВО АН СССР, 1991.-65 с.
- Лазаренко Б.Р., Михайлов В. В., Гитлевич А. Е. Лазерное воздействие на покрытия, полученные методом электроискрового легирования. // Электронная обработка материалов.— 1978. № 3. — С.24−25.
- Гурьянов Г. В. Антифрикционные и износостойкие электрохимические покрытия. / Г. В. Гурьянов. — Брянск: БГИТА, 2006. 115 с.
- Верхотуров АД. Формирование поверхностного слоя металлов при электроискровом легировании./ А. Д. Верхотуров. Владивосток: Дальнаука, 1995.-323 с.
- Верхотуров А.Д., Бабенко Э.ГТвердость легированного слоя после электроискрового легирования металлических поверхностей- Препринт / А. Д. Верхотуров, Э: Г. Бабенко Институт машиноведения и металлургии ДВО АН СССР. Владивосток. 1991. — 53 с.
- Ионная имплантация: Сб. ст. / Под ред. Дж. К. Хирвонена- пер. с англ. И. Я. Бокшицкого и др. — М.: Металлургия, 1985 125 с.
- Ионная имплантация / X. Рассел, И. Руге- перевод с нем. В. В. Климова, В. Н. Пальянова. -М.: Наука, 1983. 288 с.
- Комаров Ф.Ф. Ионная имплантация в «металлы / Ф. Ф. Комаров. — М.: Металлургия, 1990.-290 с.
- Эффекты дальнодействия в ионно-имплантированных металлических материалах / А. Н. Диденко — отв. ред. Ю.Р. Колобов- — Томск: Изд-во науч.-техн. лит., 2004 (Томск -. Тип. М-Принт). 213 с.
- Быковский Ю.А., Неволин В. Н., Фоминский В. Ю. Ионная и лазерная имплантация металлических материалов / Ю. А. Быковский, В. Н. Неволин, В. Ю. Фоминский. М.: Энергоатомиздат, 1991. — 302 с.
- Марголин В.И., Тупик В. А. Основы нанотехнологии. Электронная литография и ионная имплантация: учеб. пособие / В. И. Марголин, В. А. Тупик.- СПб.: ЛЭТИ, 2000. 144 с.
- Брюхов В.В. Повышение стойкости инструмента методом ионной имплантации. /В.В. Брюхов. Томск: Изд-во науч.-технлит., 2003. — 211 с.
- Барашенков И. С. Новые профессии тяжелых металлов. /И.С. Барашенков. М.: Атомиздат, 1977. — 120с.
- Белый КМ. Образование химических соединений при ионной бомбардировке тонких пленок переходных металлов Cr, Ni, Mo // Физика и химия обработки металлов. 1979- № 1- С.48−53.
- Павлов А.В., Павлов П. В., Зорин Е. И., Тетельбаум Д. И. Взаимодействие атомных частиц с твердыми телами./ А. В. Павлов, П. В. Павлов, Е. И. Зорин, Д. И. Тетельбаум. Киев, 1974. — Т. 1. — С. 114−116.
- Deep ion implantation: Advantages and current problems: Invited talk delivered at the II Intern, symp. «Ion implantation a. other application of ions a. electrons», June 16−19, 1998, Kazimierz Dolny, Poland / B. Slowinski Dubna., 1998
- Ионная имплантация: перспективы и альтернативы / В. В. Титов М. -М.: Металлургия, 1997. 155 с.
- Хайнер Р., Руге И. Ионная имплантация. / Р. Хайнер, И. Руге М.: Наука, 1983.-360 с.
- Резников JI.A. Повышение эксплутационных характеристик деталей машин и металлорежущего инструмента методом ионной имплантации. / JI.A. Резников- М.: Машиностроение. 1990. 215 с.
- Аброян А. К, Титов А. К Физические основы электронной и ионной технологии./ А. И. Аброян, А. И. Титов. — М.: Высш. Школа, 1984. — 320 с.
- Распыление твердых тел ионной бомбардировкой. Физическое распыление одноэлементных твердых тел. Пер. с англ./ Под ред. Р. Бериша.-М.: Мир, 1984. 336 е., ил.
- Распыление твердых тел ионной бомбардировкой. Вып. II. Распыление сплавов и соединений, распыление под действием электронов и нейтронов, рельеф поверхности. Пер. с англ./ Под ред. Р. Бериша. — М.: Мир, 1986.-448 е., ил.
- Распыление твердых тел ионной бомбардировкой. Вып. П1 Характеристики распыленных частиц, применения в технике: Пер. с англ./ Под ред. Р. Бериша, К. Виттмака. М.: Мир, 1998. — 551 е., ил.
- Гусева М.И. Технологические аспекты ионной имплантации в металлах. // Металлы.-1993.~№ 3- С.141−149.
- Комаров Ф.Ф., Кумахов М. А., Темкин М. М. Пространственное распределение энергии, выделенное в каскаде атомных столкновений в твердых телах./ Ф. Ф. Комаров, М. А. Кумахов, М. М. Темкин. — М.: Энергоатомиздат.1985 — 284 с.
- Распределение пробегов ускоренных ионов/ Ф. Ф. Комаров, М. А. Кумахов, М. М. Темкин, Т. И. Жукова. Препринт ИАЭ им. И. В. Курчатова, № 3332/11, М. 1980.-68 с.
- Шаркеев Ю.П., Колупаева С. Н., Гирсова Н. В., Вихорь Н. В., Фортуна C.B., Попов U.E., Козлов Э. В. Эффект дальнодействия в металлах при ионной имплантации // Металлы. 1998. — № 1. — С.109 — 115.
- Белый A.B. Применение ионного легирования для повышения эксплуатационных характеристик деталей машин и оборудования. /A.B. Белый-Минск, 1985.-45с.
- Комаров Ф.Ф., Новиков А. П., Буренков А. Ф. Ионная имплантация./ Ф. Ф. Комаров, А. П. Новиков, А. Ф. Буренков. — Минск, 1994. 303 с.
- Диденко А.Н., Лигачев А. Е., Куракин И. Б. Воздействие пучков заряженных частиц на поверхность металлов и сплавов/ А. Н. Диденко, А. Е. Лигачев, И. Б. Куракин. -М.: Энергоатомиздат, 1987. 184 с.
- Deamaley G. II Mater. Sei. Eng. 1985. V. 69. P. 139−147.
- Раджабов Т.Д., Багдасарян A.C. Особенности имплантации инструментальных сталей.// Поверхность —1986 — № 11С. 104−111.
- Dimigen H., Kobs К., Leutenecker R. e.a.//Mater. Sei. Eng. 1985. V. 69. p. 181−190.
- Feller H.G., Klinger R., Benesce W.// Mater. Sei. Eng. 1985. V.69.p. 173−180.
- Павлов П.В., Зорин ЕЖ, Тетелъбаум Д.И. Взаимодействие атомных частиц с твердым телом. / П. В. Павлов, Е. И. Зорин, Д. И. Тетельбаум. — Ч. II. Киев.:1974.- С.114−115.
- Пранявичюс П., Дудонис Ю. Модификация свойств твердых тел ионными пучками./ П. Пранявичюс, Ю. Дудонис. — Вильнюс: «MOKCJIAC», 1980.-242 с.
- Арзамасов Б.Н., Сидорин И. И., Косолапое Г. Ф. Материаловедение./ Б. Н. Арзамасов, И. И. Сидорин, Г. Ф. Косолапов. М.: Машиностроение, 1986.-384 с.
- Овчинников В.В., Козлов ДА., Якушина C.B. Исследование свойств поверхности стали 30ХГСН2А после имплантации ионами меди. // Машиностроение и инженерное образование—2009 —№ 2.—С.7—13.
- Григоров А.И., Елизаров O.A. Ионно-вакуумные износостойкие покрытия. Обзор. НИИМаш, 1979. 48 с.
- Габович МД, Гусева М. И., Юрасова В. Е. Ионная физика и технология. / М. Д. Габович, М. И. Гусева, В.Е. Юрасова- Киев, АН УССР, 1990.-133 с.
- Комаров Ф.Ф., Никифорова Л. Г. Ионно-лучевая модификация металлов./ Ф. Ф. Комаров, Л. Г. Никифорова. Минск: БелВИНИТИ, 199 064 с.
- Пат. 2 152 455 Россия. МКИ С23С 14/48. Способ ионно-лучевой обработки изделий / Б. П. Гриценко, Ю. П. Шаркеев, В. В. Вторушин. Заявлено 31.12.1997- Опубл. 10.07.2000, Бюл. № 19. 8 с.
- Пат. 2 192 502 Россия. МКИ С23С 14/48. Ионно-лучевой способ повышения износостойкости материала изделий / Б. П. Гриценко, В. В. Беспалов. Заявлено 04.12.2000- Опубл. 10.11.2002, Бюл. № 31. 6 с.
- Шаркеев Ю. П. Колупаева C.B. Фирсова Н. В. и др. Эффект дальнодействия в металлах при ионной имплантации. // Металлы—1998 — № 1.-С. 109−115.
- Овчинников В.В., Козлов ДА. Влияние марки бронзы на свойства стали 30ХГСН2А при электроискровом легировании. // Машиностроение и инженерное образование.- 2008.-№ 1-.С.ЗЗ~40.
- Двойные и многокомпонентные системы на основе меди. Справочник. -М.: Наука, 1979.
- Авдеев М.А., Миллер О. Г. Изучение области расслаивания в системе медь-свинец. // Журнал неорганической химии. — 1958. Т.З.— С.921—923.
- Елютин В.П., Костиков В. И., Лысое B.C., Маурах М. Л., МитинB.C., Мозжухин ЕЖ II Высокотемпературные материалы. 4.II. М.: Металлургия, 1973. — 464 с.
- Портной Д.И., Салибеков С. Е., Светлов H.A., Чубарое В. М. Структура и свойства композиционных материалов. — М.: Машиностроение, 1979.-255 с.
- Федорченко И.М., Пугина Л. И. Композиционные спеченные антифрикционные материалы. — Киев: Наук. Думка., 1980. 403 с.
- Порошковая металлургия. Спеченные композиционные материалы. / под ред. В. Шатта. — М.: Металлургия, 1983.
- Якушина C.B., Овчинников В. В., Козлов Д. А., Немое A.C. Влияние имплантирования ионов меди и свинца на свойства стали 30ХГСН2А. // Машиностроение и инженерное образование — 2010 — № 4 — С.38−45.