Свойства компонентов композитов на основе алюминиевой матрицы
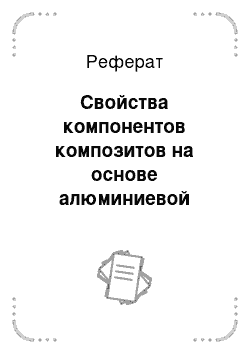
Применение боралюминия по сравнению с титановыми сплавами дает снижение массы на 30…40%, обеспечивая более высокую длительную и усталостную прочность при нагреве до 500 °C. Еще более эффективно применение боралюминия в авиационной и космической технике. Его использование для изготовления крупных деталей для ракет «Атлас», космических кораблей «Аполлон», «Шаттл» позволило уменьшить их массу… Читать ещё >
Свойства компонентов композитов на основе алюминиевой матрицы (реферат, курсовая, диплом, контрольная)
со
?С*
Таблица 2.16.
Тип волокна. | Плотность р, г/см3 | Предел прочности при растяжении о8, МПа. | Модуль упругости ?, ГПа. | Удельная прочность. (Ууа = 0"/(рZ), км. | Удельная жесткость Еуа = ?/(р?). 103км. | ТКЛРос, ю^к-1 | Максимальная температура. 'та". 'С. |
Матрица из алюминиевого сплава. | 2,63 …6,8. | 250…537. | 69…73. | 2,5. | 11…13. | ||
С. | 2,1…2,3. | 850/70. | 360/35. | 1,0…3,6. | |||
В | 2,6. | 1 800/330. | 250/140. | 6,0. | |||
SiC. | 2,85…2,9. | 1 600/350. | 230/140. | 6,1. | |||
В SiC. | 2,7… 2,8. | 1 400/320. | 220/180. | —. | —. | —. | |
А1203 | 3,4. | 260/140. | — | — |
Примечание. В числителе даны продольные значения прочностных характеристик, в знаменателе — поперечные.
Параметр | Магниевые сплавы. | Материал армирующих волокон. | ||
С. | В. | А1203 | ||
Плотность р, г/см3 | СО оо. | 1,9… 1,95. | 2,15. | 2,5 …2,9. |
Предел прочности при растяжении ав, МПа. | 200…280. | |||
Модуль упругости ?*, ГПа. | 43 …45. | |||
Условный предел прочности на растяжение о^, км. | 15,5. | 115*. | ||
Удельная жесткость ?ул, 103 км. | 2,5. | 23*. | ||
ТКЛРа, Ю-^К-'. | 14… 15. | * ; | ; | ; |
Максимальная температура W, «С. | —. | 300…320. | —. | —. |
* Проектируемые значения свойств.
на основе титановой матрицы представляет большие трудности. Недостатком этого вида композитов является также высокая реакционная способность титановой матрицы. Свойства металлических композитов на основе титановой матрицы приведены в табл. 2.18.
Прочность и модуль упругости, а также сопротивление материалов удару для однонаправленных композиционных материалов на основе алюминия, магния и титана повышаются по мере увеличения в композиции объемного содержания волокон.
Для очень высоких температур, например в камерах сгорания реактивных двигателей, используют системы, содержащие молибденовую и вольфрамовую проволоку в матрицах из титана и суперсплавов.
Наибольшей прочностью при температуре 1093 °C обладает проволока из сплава W— Re— Hf— С: ов = 2,2 ГПа, что в несколько раз больше прочности никелевых или кобальтовых суперсплавов при такой же температуре.
Большие перспективы открываются с развитием процессов объемного армирования металлических композитов. В частности, для металлических композитов объемное армирование дает существенный выигрыш в ударной вязкости. Система А1203/А1 трех;
Параметр | Титановые сплавы. | Материал армирующих волокон. | ||
В. | SiC. | В SiC. | ||
Плотность р, г/см3 | 4,5. | 3,3…3,5. | 3,8…4,0. | 3,7… 3,9. |
Предел прочности при растяжении ав, МПа. | 500… 1 200. | 1 500/550. | 1 720/650. | 1 400/550. |
Модуль упругости Еу ГПа. | 250/200. | 290/200. | ||
Удельная прочность °в/(р?), км | ||||
Удельная жесткость Еул> 103 км. | 2,6. | 6,5. | 7,5. | 7,5. |
ТКЛРа, Ю^К-'. | —. | —. | 4,5…5,7. | |
Максимальная температура /тах, «С. | —. |
Примечание. В числителе даны продольные значения прочностных характеристик, в знаменателе — поперечные.
мерного армирования поглощает почти такую же энергию удара, как и чистый металл.
Армирование по толщине, обеспечиваемое трехмеоной волокнистой структурой, предотвращает расслоение и ограничивает распространение трещин.
К недостаткам металлических композитов относятся их сравнительно высокая стоимость и сложность изготовления. Их стоимость в настоящее время превосходит стоимость полимерных композитов в несколько раз. Совершенствование технологии позволит снизить себестоимость металлических композитов, а их уникальные свойства делают их незаменимыми в ряде конструкций.
В авиационной и космической технике наиболее широко используют композиты с борными волокнами. Детали из боропластика и бороалюминия применяют такие крупные фирмы США, как «Локхид», «Боинг», «Дженерал Дайнемикс». Из них изготавливают горизонтальные и вертикальные стабилизаторы, рули, элементы хвостового оперения, лонжероны, лопасти винтов, обшивку крыльев и др.
Области использования металлических композитов непрерывно расширяются. Помимо улучшения технических характеристик многих ответственных изделий, использование металлических композитов способно обеспечить уменьшение массы изделий на.
20…30%. Современные А1—Li сплавы имеют этот показатель на уровне 10… 15%.
Применение боралюминия по сравнению с титановыми сплавами дает снижение массы на 30…40%, обеспечивая более высокую длительную и усталостную прочность при нагреве до 500 °C. Еще более эффективно применение боралюминия в авиационной и космической технике. Его использование для изготовления крупных деталей для ракет «Атлас», космических кораблей «Аполлон», «Шаттл» позволило уменьшить их массу на 20…50%. Это, в свою очередь, увеличило полезную нагрузку, а для военных самолетов — дальность полета, объем вооружения и т. д. Снижение полетной массы истребителя F-15 на 6% (около 1 100 кг) приводит к увеличению дальности полета на 15%.
Фирма Toyota (Япония) изготовила металлические композиты для деталей автомобилестроения. Алюминий армировали смесью коротких волокон А1203 и Si02 (диаметр примерно 3 мкм и длина до 10 мкм) в различных соотношениях. С увеличением массовой доли волокон А1203 возрастает прочность и модуль упругости, при росте доли волокон Si02 повышается износостойкость. Этот материал использовали вместо никелевых сплавов для изготовления накладок поршней, что позволило поднять температуру в камере сгорания двигателя и его мощность. За счет увеличения износостойкости поршней пробег автомобиля увеличен до 300 тыс. км.
Производство таких металлических композитов, по мнению японских специалистов, откроет промышленную технологию следующего поколения.
Правильный выбор материалов с целью экономии массы летательных аппаратов играет определяющую роль. Стоимость материала конструкции составляет 40% для военных самолетов, 68% — для коммерческих, 19% — для космических аппаратов, 50% — для орбитального космического корабля типа «Шаттл». В космической технике экономию массы принято оценивать через стоимость вывода 1 кг массы на орбиту с учетом числа запусков. Учитывая, что отношение исходной массы к массе, доставленной на околоземную орбиту, составляет 100: 1, эта величина может составлять до 30 тыс. долл ./кг.
Применение композитов в конструкции космического корабля «Шаттл» позволило снизить массу на 1 402 кг, в том числе за счет боропластика — на 410 кг и боралюминия — на 82 кг. Такая экономия массы позволила уменьшить затраты на вывод корабля на орбиту на несколько миллионов долларов, что заранее окупает затраты на стоимость элементов конструкции из этих материалов.
- 1. Назовите основные этапы технологии получения изделий из керамических материалов.
- 2. Какие виды керамических материалов используются в промышленности?
- 3. В чем преимущества режущего инструмента с пластинами из керамических материалов?
- 4. Какой эффект достигают при изготовлении деталей двигателей из керамических материалов?
- 5. Где используют ударопрочные керамические материалы?
- 6. Какова область применения радиопрозрачных керамических материалов?
- 7. Какой материал называется композиционным?
- 8. Что представляют собой дисперсно-упрочненные, волокнистые и слоистые композиты?
- 9. Что означает слово «синтсгран»? Из чего состоит этот материал?
- 10. Каковы области применения синтеграна?
- 11. Каковы свойства углепластиков и где они используются?
- 12. Что представляют собой органопластики и где их применяют?
- 13. Какова область применения боропластиков?
- 14. Где используют композиты с металлической матрицей?