Производство чугуна.
Экологическая экспертиза и экологический аудит
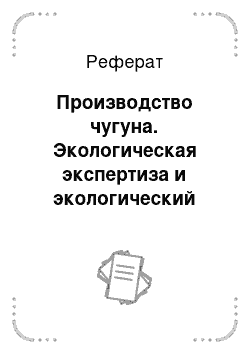
Воздействие на гидросферу. Согласно государственным докладам предприятия черной металлургии потребляют в совокупности около 1700 млн м3 воды в год. При этом до 75% объема ее потребления расходуется на охлаждение металлургических печей, в результате чего вода только нагревается и практически не загрязняется. Еще до 20% воды используется на охлаждение прокатных станов и удаление примесей, причем… Читать ещё >
Производство чугуна. Экологическая экспертиза и экологический аудит (реферат, курсовая, диплом, контрольная)
Чугун — железоуглеродистый сплав, содержащий более 2% углерода. Кроме углерода в чугуне всегда присутствуют кремний (до 4%), марганец (до 2%), а также фосфор и сера. Чугун является основным исходным материалом для получения стали, на это расходуется примерно 80—85% всего получаемого чугуна. Чугун выплавляется из железной руды, агломерата, окатышей и флюсов (на основе известняка) в непрерывно действующих доменных печах.
Доменная печь является шахтной печыо круглого сечения; изнутри выложенной огнеупорной кладкой. Шихта подается в печь сверху через приемную воронку, воздух (дутье) от воздуходувных машин — через воздухонагреватели (в которых он нагревается до 1000— 1200°С) и фурменные приборы, установленные, но окружности горна. Через эти фурмы в доменную печь вводят дополнительное топливо (природный газ, мазут или угольную пыль). Продукты плавки выпускаются в ковши через летки, расположенные в нижней части горна.
Основные химические процессы, протекающие в доменной печи, — это горение топлива и восстановление железа, кремния, марганца и др. элементов. Сопутствующие химические элементы, содержащиеся в руде (медь, мышьяк, фосфор), подобно железу, восстанавливаясь, почти полностью переходят в чугун. Шлак состоит из невосстановившихся оксидов Si02, А1203 и СаО (90−95%), MgO (2−10%), FeO (0,1−0,4%), MnO (0,3—3%), а также S (1,5—2,5%). Непрерывная работа (кампания) доменной печи от задувки до выдувки (остановки на капитальный ремонт) продолжается 5—6, а в некоторых случаях 8—10 лет и более, в течение которых печь один-два раза останавливается на так называемый средний ремонт для замены изношенной огнеупорной кладки.
Производство стали. С момента изобретения стали менялись и совершенствовались способы ее производства. В настоящее время используются три основных способа:
- • кислородно-конвертерный;
- • мартеновский;
- • электросталеплавильный.
В основе всех этих способов лежит окислительный процесс, направленный на снижение содержания в сырье (чугуне) некоторых веществ.
Кислород)to-конвертерный способ. Первое использование кислородноконвертерного способа приходится на пятидесятые годы прошлого столетия. В процессе производства стали чугун продувают в специальной установке — конвертере чистым кислородом. Этот процесс производится без затрат тепла, т. е. без использования топлива. Для того чтобы переработать 1 т чугуна в сталь, требуется около 350 м3 воздуха. Следует отметить, что кислородно-конвертерный способ получения стали является на сегодняшний день наиболее эффективным. Различают кислородно-конвертерные процессы с комбинированной, верхней и нижней поддувкой кислорода, из них самый универсальный — это способ с комбинированной поддувкой.
Подача кислорода в расплав осуществляется через водоохлаждаемую фурму под давлением, окисление чугуна происходит под воздействием дутья. В результате окисления металла выделяется тепло, что способствует снижению содержания примесей и повышению температуры металла. На завершающей стадии процесса происходит так называемое раскисление стали.
Мартеновский способ. В процессе производства стали мартеновским способом используется специальная отражательная печь. Для нагревания стали до нужной температуры (около 2000°С) в печь вводят дополнительное тепло, получаемое за счет сжигания топлива (мазута, природного газа) в струе нагретого воздуха. Обязательным является условие полного сгорания топлива в рабочем пространстве. Особенность мартеновского способа производства стали заключается в том, что количество кислорода, подаваемого в печь, превышает минимально необходимый уровень. Это позволяет создать в печи окислительную атмосферу. Сырье (чугун, железный и стальной лом) загружается в мартеновскую печь, где подвергается плавке в течение 4−6 часов. Добавки в сырье специальных примесей позволяют получать в мартеновских печах специальные сорта сталей.
Электросталеплавильный способ. Данным способом получают сталь высокого качества, процесс выплавки осуществляется в специальных электрических печах. Основной принцип электросталеплавилыюго способа производства стали — использование электроэнергии для нагрева металла. Механизм производства следующий: за счет преобразования электрической энергии в тепловую сырье нагревается до необходимой температуры. Важно отметить, что процесс плавки сопровождается образованием шлаков, причем качество получаемой стали во многом зависит от количества и состава шлаков. Присутствие в процессе производства стали шлаков оказывает весьма благотворное влияние на ее качество, например, позволяет связывать и выводить из нее различные вредные вещества, такие как фосфор.
Прокат стальных изделий самых различных профилей производится на станах горячей и холодной прокатки.
Цветная металлургия. К заводам цветной металлургии относятся цинковые, свинцовые, медные, сернокислотные, никелевые, кобальтовые, глиноземные, электродные, алюминиевые, титановые и магниевые заводы. Однако, прежде чем поступить непосредственно на переплавку, руды цветных металлов подвергаются обогащению на горно-обогатительных фабриках (комбинатах). С целью снижения транспортных расходов эти производства обычно размещаются непосредственно в местах добычи руды. Довольно часто в рудниках добываются полиметаллические руды, содержащие соединения сразу нескольких металлов. С целью увеличения концентрации и разделения ценных компонентов руд, предназначенных для последующей выплавки цветных металлов: меди, цинка, свинца и других осуществляется их обогащение, которое производят флотационным или гравитационным методом. Пустая порода (хвосты) размещаются в отвалах.
Основными и самыми крупнотоннажными производствами цветной металлургии являются предприятия медной и алюминиевой промышленности. Алюминий производят методом рафинирования боксита до оксида алюминия (глинозема) с восстановлением оксида алюминия в электролизерах для отделения металлического алюминия от кислорода.
На территории России предприятия цветной металлургии расположены неравномерно, в основном они находятся в Восточной Сибири, на Урале и Кольском полуострове.
Загрязнение окружающей среды предприятиями цветной и черной металлургии примерно аналогично.
Загрязнение атмосферного воздуха. В рейтинге отраслей промышленности по общему объему валовых выбросов загрязняющих веществ в атмосферу от стационарных источников черная металлургия занимает второе место. Основными загрязняющими веществами в выбросах предприятий черной металлургии являются:
- • оксид углерода (67,5% суммарного выброса в атмосферу);
- • твердые вещества (15,5%);
- • диоксид серы (10,8%);
- • оксид азота (5,4%).
В городах, где расположены крупные предприятия отрасли (Магнитогорск, Новокузнецк и др.), службами экологического мониторинга систематически отмечаются высокие и чрезвычайно высокие уровни загрязнения атмосферного воздуха (от 10 до 150 ПДК), в том числе — веществами первого и второго класса опасности. Первые места по количеству выбросов в атмосферу занимают металлургические комбинаты: Череповецкий (Вологодская область), Магнитогорский (Челябинская область), Новолипецкий (Липецкая область), Качканарский горно-обогатительный комбинат (Свердловская область).
Не менее значимы предприятия цветной металлургии, ежегодно ими выбрасывается в атмосферу около 3 млн т вредных веществ, что составляет примерно 18% всего объема выбросов на территории России от стационарных источников загрязнения. На долю одного только концерна «Норильский никель» приходится 10% валового выброса загрязняющих веществ в атмосферу всей промышленности страны. Лидерами отрасли по размеру валовых выбросов загрязняющих веществ в атмосферу являются, наряду с концерном «Норильский никель» (г. Норильск Красноярского края): комбинат «Южуралникель» (г. Орск Оренбургской области), комбинат «Печенганикель» (г. Никель Мурманской области), комбинат «Североникель» (г. Мончегорск Мурманской области), «Среднеуральский медеплавильный завод» (г. Ревда Свердловской области), «Красноярский алюминиевый завод» (Красноярский край), «Ачинский глиноземный комбинат» (г. Ачинск Красноярского края). Следует отметить, что немалая часть предприятий отрасли расположена в полярной и приполярной зонах, ассимилирующая способность природной среды которых в несколько раз ниже, чем в средних широтах.
В составе выбросов этих предприятий преобладает диоксид серы (около 75% всех выбросов), образующийся при переработке руд и концентратов. К сожалению, на сегодняшний день в России отсутствует действенный экономический механизм, стимулирующий предприятия увеличивать степень очистки своих выбросов в атмосферу. В результате промышленные выбросы предприятиями цветной металлургии на сегодняшний день очищаются от того же диоксида серы менее чем на 25%.
При получении алюминия электролизным путем из ванн выделяются газы, содержащие: фтористый водород, оксид углерода, диоксид серы, концентрация которых зависит от типа электролизера, вида анодов, способа загрузки глинозема, режима работы электролизных ванн, состава электролита и т. д. Например, отходящие от печей для спекания электродов газы могут содержать до 1000 мг/м3 углеводородов и до 100 мг/м3 соединений фтора.
На медеплавильных заводах медь выплавляется из первичного сырья (руды, концентратов) и вторичного сырья (латунный, бронзовый лом и т. д.). При выплавке меди из первичного сырья используют обжиговые печи (многоподовые и печи кипящего слоя), шахтные печи, электропечи, печи взвешенной (факельной) плавки на подогретом воздушном дутье и техническом кислороде, отражательные печи, конвертеры. При выплавке меди из вторичного сырья используют шахтные печи и конвертеры.
Воздействие на гидросферу. Согласно государственным докладам предприятия черной металлургии потребляют в совокупности около 1700 млн м3 воды в год. При этом до 75% объема ее потребления расходуется на охлаждение металлургических печей, в результате чего вода только нагревается и практически не загрязняется. Еще до 20% воды используется на охлаждение прокатных станов и удаление примесей, причем в последнем процессе вода не только нагревается, но и загрязняется металлическими взвесями и растворенными веществами. Ежегодно в водоемы предприятиями отрасли сбрасывается около 1 млн м3 сточных вод, из них 85% — загрязненных. По совокупному сбросу загрязненных сточных вод вклад черной металлургии составляет около 7% общего объема сброса в целом по промышленности России.
Среди загрязняющих веществ в сточных водах металлургических производств преобладают взвеси, сульфаты, хлориды, соли железа и прочих тяжелых металлов. Многие металлургические комбинаты не обеспечивают нормативную очистку своих сточных вод. Так, по данным Государственного доклада о состоянии окружающей среды (2006) объем недостаточно очищенных сточных вод составил:
- • ОАО «Новолипецкий металлургический комбинат» — 123,9 млн м3;
- • ОАО «Магнитогорский металлургический комбинат» — 77,63 млн м3;
- • ОАО «Западно-Сибирский металлургический комбинат» — 45,21 млн м3.
По данным государственного экологического мониторинга существенное воздействие предприятия отрасли оказывают также и на состояние подземных вод: например, загрязнение подземных вод Новолипецким металлургическим комбинатом составляло:
- • радонидами — 957 ПДК;
- • цианидами — 308 ПДК;
- • нефтепродуктами — 80 ПДК;
- • фенолами — 50 ПДК.
По характеру использования воды потребители агломерационных фабрик подразделяются на следующие основные группы.
I группа — потребители, применяющие воду для охлаждения оборудования (охлаждение массы, воздухоохлаждение электродвигателей дымососов, охлаждение горна агломерационных машин и др.); для этих потребителей используется условно-чистая вода, которая в производстве только нагревается, не загрязняясь;
II группа — потребители, которые в процессе использования воду нагревают и загрязняют (гидросмыв пыли из газоочистных аппаратов и вентиляционных систем, от гидроуборки помещении и промывки шламонроводов и др.);
III группа — потребители, у которых происходит полная потеря воды (увлажнение шихты в смесительных барабанах, охлаждение возврата, гидрообеспыливание).
В мировой практике имеется два принципиально различных способа уборки пыли на агломерационных фабриках: мокрый — удаление пыли средствами гидротранспорта и сухой — системами пневмотранспорта.
Состав отработавших вод «грязного» цикла агломерационных фабрик зависит от состава шихты и типа применяемой очистки агломерационных газов (сухой или мокрый). Отработавшие воды агломерационных фабрик являются щелочными, поскольку при гидротранспорте пыли происходит выщелачивание извести. Величина pH осветленной воды «грязного» цикла находится в пределах 9—12, содержание взвешенных веществ достигает 15 000 мг/л.
При производстве чугуна наибольшее количество воды расходуется на охлаждение доменных печей и очистку доменного газа, часть воды используется на гидроуборку подбункерных помещений, грануляцию шлака, охлаждение чугуна на разливочных машинах, а также на рудо-размораживающей установке.
Система водоснабжения — оборотная с градирнями для охлаждающей воды, отстойниками для очистки загрязненных вод от иодбункерных помещений, разливочных машин и очистки газа. Осадки обезвоживаются и используются или удаляются в накопитель.
Отработавшие воды доменного производства характеризуются наличием механических примесей до 5 г/л, растворенных веществ в виде гидрооксида кальция — до 9 мг-экв/л.
В сталелитейном производстве вода расходуется в основном на охлаждение металлургических агрегатов. Эти расходы воды несколько возросли в связи с применением кислородного дутья, а также с использованием в качестве топлива природного газа. За последнее время удельный расход воды на выплавку стали несколько увеличился из-за повсеместного применения мокрой очистки выбросов сталеплавильных агрегатов (мартеновских и электросталеплавильных печей, а также конвертеров).
Система водоснабжения мартеновских и электросталеплавильных печей — оборотная с градирнями (сооружениями для охлаждения воды). Водоснабжение газоочистных установок также оборотное с очисткой загрязненной отработавшей воды в отстойниках.
Основными факторами, влияющими на формирование и состав отработавших вод, являются технологические особенности выплавки стали, состав шихты, удельный расход воды на очистку газа и др. Концентрация взвешенных веществ в отработавших водах колеблется в широких пределах: от 200 до 18 000 мг/л. В процессе мокрой очистки газов в сточные воды переходят, наряду с механическими примесями, растворимые химические вещества. Последние представлены как «кислыми» компонентами (сульфатами, фторидами, хлоридами и др.), так и щелочами (в основном известью). Баланс кислотных и щелочных компонентов наблюдается редко; чаще всего имеется избыток той или иной группы загрязнений, что в условиях оборотного водоснабжения требует проведения нейтрализации отработанных вод.
При прокатке металла используется техническая очищенная вода для охлаждения подшипников, а также для охлаждения режущих устройств (пил и ножниц) и др. В процессе холодной прокатки техническая вода используется также для приготовления травильных растворов, промывки металла после травления, приготовления эмульсии для прокатных станов, на нужды машинных залов и охлаждение нагревательных устройств.
При холодной прокатке металла оборотная техническая вода в травильных отделениях загрязняется травильными растворами, содержащими кислоты и (или) щелочи. Эта вода подвергается нейтрализации, после чего сбрасывается в шламонакопители или используется в системах оборотного водоснабжения. Отработавшая вода «грязных» циклов прокатных станов подвергается очистке от окалины и масла в отстойниках.
В табл. 2.7 приведен состав сточных вод типичного металлургического завода.
Согласно данным экомониторинга по сбросам загрязненных сточных вод, вклад объектов цветной металлургии составляет 6% общего объема сбросов всей промышленностью. Основная часть жидких отходов предприятий цветной металлургии представлена различного рода водными растворами (рудничные воды, промышленные сточные воды, условно чистые воды, хозяйственно-бытовые воды). Наибольший ущерб окружающей среде наносится при сбросе в открытые водоемы промышленных сточных вод металлургических заводов и рудообогатительных фабрик.
Состав сточных вод металлургического завода.
Показатель. | Единица измерения. | Сточные воды. | |
до очистки. | после очистки в пруду-осветлителе. | ||
Взвешенные вещества. | мг/л. | 100−5000. | 6−24. |
Нефтепродукты. | мг/л. | 60−100. | 2−4. |
Цвет. | ; | Желто-бурый. | Слабобурый. |
Запах. | ; | Шлама и нефти. | Без запаха. |
Жесткость общая. | мг-экв/л. | 0,8−1,6. | До 2,4. |
Щелочность. | мг-экв/л. | 1,1−4,5. | 1−2,1. |
Сухой остаток. | мг/л. | 240−700. | 290−526. |
Сточные воды предприятий цветной металлургии имеют сложный химический состав и высокую степень загрязнения высокотоксичными веществами, что определяется как разнообразием перерабатываемого сырья, так и многостадийностыо производственных процессов и широким ассортиментом применяемых реактивов и материалов. В наибольшей степени сточные воды предприятий цветной металлургии загрязнены минеральными веществами, флотореагентами (веществами, используемыми при флотационном обогащении металлических руд, большинство которых токсично — такими, как ксантогенаты, нефтепродукты и др.), солями тяжелых металлов (меди, свинца цинка, никеля и т. д.), мышьяком, фтором, ртутью, сурьмой, сульфатами, хлоридами и т. д.
В результате в водоемах, принимающих сбросы предприятий цветной металлургии, отмечаются высокие уровни загрязнения природных вод. Например, сбросы «Горно-металлургической компании „Норильский никель“» создают в водоеме 22-кратное превышение ПДК по содержанию нефтепродуктов, 467-кратное — по соединениям меди. В результате деятельности предприятий золотодобывающей промышленности, а также многочисленных старательских артелей, расположенных в северных (Бодайбинском и Мамско-Чуйском) районах Магаданской области, в поверхностные водные объекты поступают значительные объемы взвесей.
На заводах цветной металлургии вода в основном расходуется на охлаждение печей, разливочных машин, электролитов, шлаков, деталей машин. Кроме того, вода используется для приготовления технологических растворов, мокрой очистки выбросов, для гидротранспорта шлама и др.
Система водоснабжения применяется преимущественно с оборотом воды. В зависимости от цели использования воды и требований к ее качеству на заводах устраиваются, как правило, три водопроводные сети:
- • хозяйственно-питьевой воды;
- • свежей технической воды;
- • оборотной воды (условно-чистой и загрязненной).
В настоящее время ряд цинковых заводов переходит на замену воды как охладителя цинкового электролита воздухом. С целью сокращения расхода воды печи с кипящим слоем и плавильные печи переводят на испарительное охлаждение.
Соответственно устраиваются следующие канализационные сети:
- • загрязненных производственных сточных вод, поступающих на специализированные очистные сооружения;
- • условно-чистых сточных вод, направляемых на охлаждение в системе оборотного водоснабжения;
- • хозяйственно-бытовых и дождевых стоков, поступающих на общегородские очистные сооружения.
Настоятельной задачей является повсеместный перевод металлургических производств на систему оборотного водоснабжения.
Образование твердых отходов, загрязнение почв. Твердые отходы образуются на всех стадиях производства черной металлургии: агломерационном, доменном, сталеплавильном, горячем прокате, травлении металлов. Основную массу отходов составляют доменные и сталеплавильные шлаки. Шлаки содержат большое количество соединений кремния и оксидов ряда металлов (железа и др.). Состав их разнообразен и тесно связан как с видом сырья, так и с принятой на металлургическом предприятии технологией выплавки металла. Это обстоятельство заметно влияет на свойства шлаков и технологию их переработки.
Главным признаком классификации является химический состав отхода. Шлаки делят на основные (преобладают оксиды щелочных металлов Са и Mg), кислые (преобладают оксиды Si и А1) и нейтральные (амфотерные), в которых соотношение различных типов оксидов примерно одинаково.
Сталеплавильные шлаки содержат заметное количество железа (в металлическом виде до 20% и в виде оксидов до 24%), а также различные оксиды и сульфиды. Масса ежегодно образуемых сталеплавильных шлаков примерно вдвое меньше, чем доменных.
Схожим со шлаками видом отходов является так называемая горелая земля — отработанный продукт литейного производства. Дело в том, что самым распространенным видом литейного производства является литье в песчано-глинистые формы, ранее называемое «литьем в землю». В состав формовочных и стержневых смесей входят в определенном соотношении неорганические (кварцевый песок, глина, жидкое стекло и др.) и органические материалы (опилки, древесная и угольная пыль и др.). Поскольку потребность в смесях велика, практически на любом литейном предприятии значительную часть смесей составляет регенерированная «горелая земля».
Цветная металлургия относится к числу отраслей с наибольшим удельным выходом производственных отходов (на единицу продукции). Значительная часть ныне действующих предприятий цветной металлургии введена в строй в годы индустриализации страны, либо в первые послевоенные годы. Этим объясняется то, что при их проектировании и строительстве не были учтены требования рационального природопользования и снижения негативного воздействия на окружающую среду. В условиях формирования рыночных отношений возможности экологизации промышленного производства существенно сократились.
К настоящему времени в зоне действия рудников, обогатительных фабрик и металлургических заводов отрасли накоплено свыше 5 млрд т вскрышных и вмещающих пород, около 1 млрд т хвостов обогащения и почти 500 млн т металлургических шлаков и шламов. В настоящее время в производство вовлекаются не более 20% вскрышных пород, около 10% отходов обогащения и примерно 40% шлаков. Согласно выполненным оценкам в отвальных хвостах обогащения содержится более 1 млн т меди, 1,2 млн т цинка, более 700 тыс. т никеля и 35 тыс. т кобальта, около 400 тыс. т молибдена. Еще по 1 млн т меди и цинка, 400 тыс. т никеля, 13 тыс. т олова, 84 тыс. т свинца хранят отвалы шлаков металлургического производства, накопленные на территории страны за многие годы.
Неудивительно, что эти «горы» отходов загрязняют почву близлежащих территорий. Так, по данным аэрокосмического мониторинга, область загрязнения почвенных покровов вокруг крупных центров черной и цветной металлургии простирается до расстояний около 60 км. Например, во Владикавказе обнаружен ареал рассеяния тяжелых металлов площадью 40 км2, в пределах которого содержание металлов в почве превышает норму в десять раз.