Уплотнения подвижных соединений
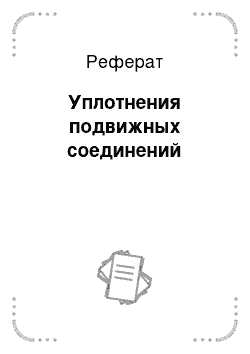
В торцевых уплотнениях герметичность обеспечивается за счет трения между двумя кольцами (рис. 15.2): фиксированным кольцом 2У которое крепится на валу I (рис. 15.2, а) или в корпусе 5 (рис. 15.2, б), и плавающим кольцом 3, которое перемещается вдоль корпуса или вала и прижимается к фиксированному кольцу упругим элементом 4. Торцевые уплотнения длительно обеспечивают высокую герметичность при… Читать ещё >
Уплотнения подвижных соединений (реферат, курсовая, диплом, контрольная)
В контактных уплотнениях герметичность обеспечивается благодаря непосредственному контакту между подвижным и неподвижным элементами соединения. Недостатком контактных уплотнений является наличие трения между контактирующими поверхностями, что приводит к дополнительным энергетическим затратам, а сами поверхности подвергаются нагреву и износу. Наличие трения и износа контактной пары ограничивает долговечность уплотнительных устройств.
Рассмотрим основные типы контактных уплотнений подвижных соединений.
Уплотнения войлочными кольцами (сальниковые).
применяются для герметизации полостей подшипников, работающих на пластичной смазке до скорости v < 8 м/с и температуре Т < 90 °C. Контакт кольца 2 с валом 1 (рис. 15.1, а) обеспечивается путем создания предварительного натяга. Размеры колец из грубошерстного, полугрубошерстного и тонкошерстного технического войлока и проточек для них стандартизированы. Перед установкой в проточку в корпусной детали войлочные кольца пропитываются разогретой смесью из пластичной смазки (85%) и графита. Не рекомендуется применять эти уплотнения при избыточном давлении и повышенной запыленности среды.
Для уменьшения износа колец шейка вала в месте контакта должна иметь Ra < 1,25 мкм при v < 2 м/с и Ra < 0,4 мкм при и < 8 м/с. Поверхность вала должна иметь твердость не менее 45 НКСЭ. Долговечность и эффективность работы уплотнения войлочными кольцами повышаются при установке.

Рис. 15.1.
их в комбинации с другими уплотнениями (щелевыми, лабиринтными). Уплотнения с сальниковой набивкой из графитизированного асбеста способны работать при температурах до 400 °C и давлениях до 10 МПа.
Манжетные уплотнения (рис. 15.1, б) имеют уплотнительное кольцо 3 сложного сечения, изготовленное из упругого материала, с выступающими рабочими элементами, за счет прижатия которых к поверхности сопряженной детали обеспечивается контакт в уплотнении. Манжетные уплотнения применяются в подшипниковых опорах при о < 25…30 м/с и избыточном давлении р = 0,02…0,05 МПа.
В зависимости от условий эксплуатации и сорта смазочного материала манжеты изготавливаются из износостойкой и керосиноводостойкой резины или полимерных материалов. Контакт рабочей кромки манжеты шириной 0,2…0,5 мм с валом 1 обеспечивается созданием предварительного натяга, а также поджатием ее к валу браслетной пружиной 4. Если в полости имеется повышенное давление, уплотнение устанавливается так, чтобы рабочая кромка прижималась к валу давлением уплотняемой среды.
Манжеты для работы в засоренной среде выполняются с дополнительной рабочей кромкой-пыльником 5 (рис. 15.1, в).
Для повышения жесткости корпус манжеты может быть армирован стальным кольцом 6. При избыточном давлении Ар > 0,05 МПа для предотвращения выворачивания манжеты применяется упорная втулка 7 (рис. 15.1, г).
Детали, совершающие возвратно-поступательные движения и имеющие форму тела вращения, уплотняются резиновыми кольцами круглого или овального сечения или манжетой 8 (рис. 15.1, d)t устанавливаемой с предварительным натягом в кольцевую проточку одной из стыкуемых деталей. Благодаря избыточному давлению она дополнительно прижимается к уплотняемым поверхностям.
Эффективность работы манжетного уплотнения повышается последовательной установкой двух манжет на расстоянии.
3…8 мм. Полость между ними заполняется пластичной смазкой. Однако при больших скоростях на контактных поверхностях многоманжетного уплотнения возникают силы трения, вызывающие разогрев и выход из строя уплотнения.
Шероховатость Ra и величину радиального биения А поверхности вала под манжетой назначаются в зависимости от и: при v = 5…10 м/с принимают Ra = 0,66…0,4 мкм, Д = = 0,175…0,1 мм; а при v = 15…20 м/с — Ra = 0,3…0,25 мкм; Д = 0,075…0,04 мм.
Для повышения износостойкости шейки вала твердость ее поверхности должна быть 35…50 HRC3. Отверстие в крышке под манжету выполняется с допуском по Н8 с Ra <2,5 мкм. Для удаления изношенной манжеты в крышке делают два-три демонтажных отверстия диаметром 3…4 мм (рис. 15.1, б).
Долговечность манжетного уплотнения повышается при снижении температуры в месте контакта, что достигается улучшением условий теплоотвода в зоне трения. Простейшие устройства, обеспечивающие теплоотвод в опорах на жидкой смазке, — масляный карман 9 (рис. 15.1, е) или втулка из теплопроводного материала.
В торцевых уплотнениях герметичность обеспечивается за счет трения между двумя кольцами (рис. 15.2): фиксированным кольцом 2У которое крепится на валу I (рис. 15.2, а) или в корпусе 5 (рис. 15.2, б), и плавающим кольцом 3, которое перемещается вдоль корпуса или вала и прижимается к фиксированному кольцу упругим элементом 4. Торцевые уплотнения длительно обеспечивают высокую герметичность при скорости о < 60 м/с и перепаде давлений Ар < 10 МПа. Температурный диапазон −200…+450 °С обеспечивается подбором материалов. Эти уплотнения использовались, например, в российских луноходах.

Рис. 15.2.
Фиксированные кольца обычно выполняются из хромистых сталей 20Х, 40Х, 30X13, 40X13, 95X18 с твердостью.
50. .60 HRC3 или твердых неметаллических материалов (керамики, силицированного графита). Плавающие кольца делают из бронзы (БрОФЮ-1, БрОЦС6−6-3), углеграфита или полимерных материалов (фторопласта-4).
Кольца из материала с большей поверхностной твердостью делаются на 2…4 мм шире колец из мягкого материала. В противном случае врезание твердого материала в мягкий делает невозможным относительное перемещение колец в радиальном направлении. Ширина поверхности контакта колец b (рис. 15.2, а) выбирается в зависимости от d: при d = = 10…20 мм Ъ = 2…3 мм, а при d = 80…150 мм Ъ = 4…7 мм. Шероховатость поверхностей трения должна быть не более Ra = 0,16 мкм. Контактные поверхности колец притираются на плите с пастой, неплоскостность допускается не более.
1. .2 мкм. При v > 20 м/с для исключения влияния центробежных сил на упругий элемент фиксированное кольцо вместе с упругим элементом выполняется неподвижным. Для уменьшения дисбаланса вращающиеся детали изготавливаются из легких материалов. В качестве упругих элементов применяются винтовые пружины, сильфоны и мембраны, которые одновременно выполняют роль вспомогательных уплотнений. Уплотнения с мембранами и сильфонами широко используются в ТНА ЖРД (рис. 15.2, в). Здесь между валом 1 и корпусом 5 поставлеРис. 15.3 но торцевое уплотнение, со.

стоящее из подвижной вращающейся втулки 2, графитового плавающего кольца 3, сильфона 6 и пружины 7. Для снижения давления в полости 8 перед торцевым уплотнением на втулке 2 имеются спиральные канавки 10 и щелевое уплотнение 9.
Для уплотнения подшипниковых узлов при любой смазке и v < 5 м/с могут быть использованы фасонные шайбы (рис. 15.3). Толщина шайб в зависимости от их размера составляет 0,3…0,5 мм. Фиксация шайбы осуществляется гайкой. Шайбы применяются для уплотнения подшипников с жесткой фиксацией наружного (рис. 15.3, а) и внутреннего (рис. 15.3, б) колец. Самоустанавливающиеся подшипники с большими осевыми зазорами уплотнять фасонными шайбами не рекомендуется из-за возможности нарушения контакта между шайбой и обоймой подшипника. Размеры шайб выбираются в зависимости от размеров подшипника.
Уплотнение упругими металлическими кольцами применяется при постоянном перепаде давлений между разделяемыми полостями. Разрезные кольца 1 устанавливаются в проточки на уплотняемых деталях (валах или штоках 3) (рис. 15.4, а). К поверхности стакана 2 кольца прижимаются силами упругости, а постоянный контакт торцев кольца и проточки обеспечивается перепадом давлений.
Кольца изготавливаются из высокосортного серого чугуна (АЧС-1) или из высокооловянистой бронзы (БрОЦС6−6-3), втулки и стаканы — из цементируемой стали. Твердость торцов канавок 56 НИСЭ, внутренней поверхности стакана — 52 НКСЭ. Шероховатость контактирующих поверхностей кольца и проточки Ra < 0,63 мкм; кольца и стакана Ra < < 1,25 мкм. Непараллельность стенок канавки и их неперпендикулярность к оси вала должны быть не больше 0,05 мм.
В авиационной технике для упругих колец с D = = 30…150 мм рекомендуются следующие размеры: =
= 1…1,5 мм; 82 = 0,4…2,0 мм; 83 = 0,05…0,15 мм; Ъ = = 2…3 мм; h = 2,5b.


Наружный диаметр кольца в свободном состоянии должен быть на 2…3% больше D.
В противном случае в результате трения повышается температура кольца, что приводит к еще большей потере упругости вплоть до выхода уплотнения из строя. При значительных перепадах давления для улучрис. 15.4.
шения работы колец необходимо на поверхность трения подавать уплотняемую жидкость через два-три отверстия диаметром 0,8…1,2 мм.
Для облегчения монтажа уплотнения в стакане выполняются конические расточки под углом, а = 15…30°, максимальный диаметр которых должен быть больше наружного диаметра колец в свободном (несжатом) состоянии. Для повышения эффективности уплотнения устанавливаются несколько колец так, чтобы стыки находились в разных плоскостях. Упругие металлические кольца применяются для уплотнения узлов подшипников редукторов вертолетов и турбовинтовых авиационных двигателей.
Для герметизации полостей с быстровращающимися валами используются уплотнения с плавающими разрезными кольцами, в которых каждое кольцо состоит из нескольких отдельных сегментов, прижимающихся один к другому по торцам браслетной пружиной 5 (рис. 15.4, б). Кольцо от проворачивания удерживается штифтом.
Бесконтактные уплотнительные устройства работают за счет использования сопротивления протеканию уплотняемой среды через узкие щели или каналы с резко изменяющимися проходными сечениями. Они не обеспечивают абсолютной герметичности, а служат для ограничения утечек. Основными преимуществами бесконтактных уплотнений являются повышенная долговечность и надежная работа при любых температурах и скоростях.
По принципу действия бесконтактные уплотнения можно разделить на статические и динамические. В статических уплотнениях (щелевых и лабиринтных) величина утечек зависит только от геометрических характеристик соединения сопряженных элементов. Эффективность динамических уплотнений (спиральных и импеллерных) зависит от геометрии соединения и от относительной скорости вращения сопряженных элементов.
Щелевое уплотнение (рис. 15.5, а) применяется при густой смазке и v < 5 м/с. Эффективность уплотнения зависит от зазора 5 и длины щели L Зазор 5 определяется прогибом вала в месте установки уплотнения, эксцентриситетом поверхностей вала 2 и корпуса 1 по отношению к оси вращения, зазором в подшипниках и т. п. Уменьшение зазора 5 может быть достигнуто нанесением на неподвижную деталь мастики 3, приготовленной на порошкообразном графите.
Щелевые уплотнения выполняются с радиальными (рис. 15.5, а) и осевыми зазорами (рис. 15.5, б). Длина радиальной щели принимается равной 4… 10 мм.
Для уплотнения подшипниковых узлов, работающих на густой и жидкой смазках при Т — 80…400 °С и v < 30 м/с, используются жировые канавки (рис. 15.5, в, г). При сборке канавки заполняются пластичной смазкой. Размеры канавок и величина зазора назначается в зависимости от диаметра вала. Например, при d =* 20…95 мм, г = 1…1,25 мм и 6 = = 0,3…0,4 мм.

Спиральное уплотнение (резьбовое) (рис. 15.5, д) выполняется в виде одноили многозаходной резьбовой нарезки прямоугольного или треугольного профиля. Направление нарезки согласуется с направлением вращения вала. Уплотняемая среда (масло, жидкость, газ) при вращении вала отбрасывается внутрь уплотняемой полости. Спиральное уплотнение можно применять только в нереверсивных механизмах.
Уплотнение подшипниковых узлов при и > 30 м/с обеспечивается радиальными (рис. 15.6, а) или аксиальными (рис. 15.6, б) лабиринтными уплотнениями. В зависимости от числа щелей они могут быть однои многоступенчатыми. При радиальном уплотнении (рис. 15.6, а) допускается осевое смещение втулки 2 относительно крышки опоры 1, поэтому оно применяется для плавающих опор подшипников.
В аксиальном лабиринтном уплотнении (рис. 15.6, б) при неразъемном корпусе 3 используется составная лабиринтная втулка 4. Это уплотнение не применяется при осевых перемещениях вала.
В подшипниковых опорах с жидкой смазкой эффективно работают при вращении вала динамические уплотнения (центробежные), но они теряют свою эффективность при низких скоростях и остановках. Для предотвращения утечек в неработающих механизмах такие уплотнения применяются в комбинации со статическими контактными или бесконтактными уплотнениями.
На рис. 15.7, а показано комбинированное уплотнение узла подшипника редуктора авиационного двигателя, состоящее из маслоотражательного кольца 2 и упругих металлических колец 1. Здесь под действием центробежной силы масло отбрасывается к периферии кольца 2 и стекает в нижнюю.


Рис. 15.7.
часть полости корпуса 4, где имеется канал 3 для его слива. Форма и размеры маслоотражательных колец зависят от диаметра и частоты вращения вала, способа подачи масла и других факторов.
Импеллерное уплотнение (рис. 15.7, б) применяется в комбинации с другими уплотнениями и в качестве основного уплотнительного устройства. Импеллер 5 представляет собой диск, на одной стороне которого имеется несколько радиально направленных лопастей. На валу импеллер устанавливается так, чтобы зона высокого давления уплотняемой жидкости с избыточным давлением Ар находилась с гладкой стороны диска. При вращении импеллера жидкость с него под действием центробежных сил сбрасывается. Высота лопастей h должна быть значительно больше зазора 6 (8 < 1 мм). Правильным подбором всех размеров импеллера можно добиться почти полной герметизации.