Повышение эффективности электроплазменной обработки путем интенсификации газодинамического воздействия и разработки нового оборудования
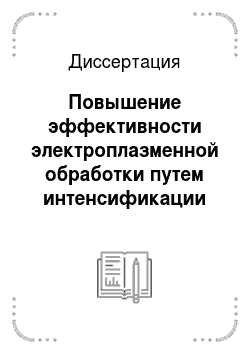
Диссертация
Одним из перспективных источников концентрированных потоков энергии является низкотемпературная плазма, генерируемая электродуговыми плазмотронами, которые получили широкое применение в металлообрабатывающем производстве /3, 6/. В ряде случаев, применительно к определенным технологическим процессам, использование плазменных методов обработки имеет существенные преимущества перед, например… Читать ещё >
Содержание
- ПЕРЕЧЕНЬ СОКРАЩЕНИЙ И УСЛОВНЫХ ОБОЗНАЧЕНИЙ
- Глава 1. АНАЛИЗ СОСТОЯНИЯ ПРОБЛЕМЫ И ПОСТАНОВКА ЗАДАЧ ИССЛЕДОВАНИЯ
- 1. 1. Методы и особенности обработки на основе использования концентрированных потоков энергии
- 1. 2. Плазменная резка и упрочнение поверхности и их недостатки
- 1. 3. Технологическое оборудование плазменно-дуговой обработки
- 1. 4. Формулировка цели и задач исследования
- Глава 2. ТЕОРЕТИЧЕСКОЕ ИССЛЕДОВАНИЕ ВОЗМОЖНОСТЕЙ ПОВЫШЕНИЯ ЭФФЕКТИВНОСТИ ЭЛЕКТРОПЛАЗМЕННОЙ ОБРАБОТКИ
- 2. 1. Повышение эффективности электроплазменной обработки и обоснование возможности увеличения ресурса работы плазмотронов
- 2. 2. Интегральный анализ параметров дугового разряда при повышенных напряжении и расходе газа
- 2. 3. Численное моделирование процесса генерации низкотемпературной плазмы при интенсивном газодинамическом воздействии
- 2. 4. Определение влияния режимов обработки на параметры в зоне взаимодействия потока плазмы с обрабатываемым материалом
- 2. 5. Результаты теоретических исследований
- 2. 6. Выводы
- ГЛАВА 3. ТЕХНОЛОГИЧЕСКОЕ ОБОРУДОВАНИЕ И РЕСУРСНЫЕ ХАРАКТЕРИСТИКИ ПЛАЗМЕННОЙ ОБРАБОТКИ
- 3. 1. Разработка источника электропитания с повышенным напряжением холостого хода
- 3. 2. Разработка генератора низкотемпературной плазмы с высокими вольт-амперным отношением и расходонапряженностью
- 3. 3. Повышение ресурсной стойкости электродов при плазменной резке
- 3. 4. Результаты экспериментальных исследований ресурсных характеристик технологического оборудования
- 3. 5. Выводы
- ГЛАВА 4. ЭКСПЕРИМЕНТАЛЬНОЕ ИССЛЕДОВАНИЕ ТЕОРЕТИЧЕСКИХ РАЗРАБОТОК ПОВЫШЕНИЯ ЭФФЕКТИВНОСТИ ЭЛЕКТРОПЛАЗМЕННОЙ ОБРАБОТКИ
- 4. 1. Плазменно-дуговое термоупрочнение поверхности металлов и сплавов
- 4. 2. Плазменная резка листовой стали
- 4. 3. Зона термического влияния и газонасыщение кромки реза
- 4. 4. Результаты экспериментальных исследований теоретических разработок
- 4. 5. Выводы
- ГЛАВА 5. ПРИМЕНЕНИЕ РЕЗУЛЬТАТОВ ИССЛЕДОВАНИЙ В ПРОМЫШЛЕННЫХ ТЕХНОЛОГИЯХ
- 5. Л. Использование разработок повышения эффективности электроплазменной обработки при создании роботизированного участка плазменной резки с компьютерным управлением
- 5. 2. Экономические аспекты создания роботизированного участка плазменной контурной обрезки автомобильных деталей
- 5. 3. Плазменно-дуговое упрочнение деталей автомобильной техники
- 5. 4. Перспективные направления развития технологии электроплазменной обработки
- 5. 5. Результаты применения исследований в промышленных технологиях на AMO ЗИЛ
- 5. Л. Использование разработок повышения эффективности электроплазменной обработки при создании роботизированного участка плазменной резки с компьютерным управлением
Список литературы
- Рыкалин H.H., Углов A.A. Кокора А. Н. Лазерная обработка материалов. -М.: «Машиностроение», 1975. -296 с.
- Обработка концентрированными потоками энергии технологии нового поколения / Курочкин Ю. В. // Экономика и организация промышленного производства. 1987. — № 7 — Н.: «Наука». — С. 8−20.
- Жуков М.ФЫ., Смоляков В. Я., Урюков Б. А. Электродуговые нагреватели газа (плазмотроны). М.: Наука. 1973. — 263 с.
- Плазменная обработка поверхности. Под ред. Ю. В. Курочкина. Н.:Наука. 1990. — 183 с.
- Ширшов Н.Г., Котиков В. Н. Плазменная резка. Л.: «Машиностроение», 1987.-197 с.
- Резников А.Н., Шатерин М. А., Кунин B.C. Обработка металлов с плазменным нагревом. М.: «Машиностроение», 1986. — 230 с.
- Григорьянц А.Г. Основы лазерной обработки материалов. М.: «Машиностроение», 1999. 299 с.
- Андрияхин В.М., Фишкис М. М. Лазеры и перспектива их применения в автомобилестроении. М.: НИИТАвтопром, 1980. 63 с.
- Кебнер Г. Промышленное применение лазеров. М.: «Машиностроение», 1988.-279 с.
- Рыкалин H.H., Углов A.A., Зуев И. В., Кокора А. Н. Лазерная и электронно-лучевая обработка материалов. М.: «Магшиностроение»., 1985.-489 с.
- И. Рыкалин H.H., Зуев И. В., Углов A.A. Основы электронно-лучевой обработки материалов. М.: «Машиностроение», 1978. -240 с.
- Иевлев В.М., Коротеев A.C. Вывод в атмосферу и исследование мощных стационарных электронных пучков. Известия АН СССР. сер. Энергетика и транспорт. № 3, 1981. — С. 3−13.
- Воинов С.С., Шур Е.А., Крапошин B.C., Косырев Ф. К. Физика и технология обработки поверхности металлов. JL: 1984. 129 с.
- Демин Ю.А., Курочкин Ю. В., Курочкин H.A. Высокоресурсные технологии плазменно-дуговой обработки. Международный научный симпозиум «Новые материалы, упрочняющие технологии и покрытия». -М.: МГТУ «МАМИ», 2000. С.56−58.
- Быховский Д.Г. Плазменная резка. Режущая дуга и энергетическое оборудование. Л.: «Машиностроение», 1972. — 183 с.
- Болотов A.B., Шепель Г. А. Электро-технологические установки. М.: «Высшая школа», 1988. — 335 с.
- Вайнерман А.Е., Шоршоров М. Х., Веселков В. Д., Новосадов B.C. Плазменная наплавка металлов. Л.: «Машиностроение», 1969. — 190 с.
- Кудинов В.В., Бобров Г. В. Нанесение покрытий напылением. Теория, технология и оборудование. М.: «Металлургия», 1992. — 430 с.
- Курочкин Ю.В., Муханов Г. Н., Григорьев А. Н., Седунов В. К., Юрасов С. А. Плазменное поверхностное упрочнение высокопрочных чугунов. // -Изв. Сиб. Отд. АН СССР. сер. техн. наук, № 18, вып. 5. 1988. С.138−142.
- Фильченко Д.Н., Диженин В. А. Плазменная резка с использованием водяной подушки. // Сварочное производство. 1982. № 10. С. 28.
- Васильев К.В., Никифоров Н. И. О факторах, определяющих ширину плазменно-дугового реза. // Сварочное производство. 1977. № 6. С. 40−42.
- Черняк Р.В. Тепловые характеристики плазменной дуги при обдуве воздушно-углебводородной смесью. // Автоматическая сварка. 1982. № 10.-С. 20−14.
- Осетник A.A. Состав граничной структуры кромок теплового реза и влияние его на свойства сварных соединений. // тр. ЦНИИТС. 1971. № 109.-С. 19−22.
- Тапченко М.А., Черняк В. Н. Плазменная пакетная резка тонколистовых сталей. // Сварочное производство. 1980. № 8. С 32−34.
- Сучикава Садахино. Резка плазменной дугой алюминиевых сплавов и ее влияние на сварные соединения. // Кэ’икиндзоку есэцу. 1971. Т.98. № 2. -С.75−85.
- Шапиро И.С. Плазменно-дуговая резка алюминиевых сплавов и нержавеющих сталей больших толщин. // Сварочное производство. 1969. 1 10.-С.25−27.
- Vanschem W. Derhtutiqe Stand der Plasmatechnik mit Anwendunqsleispielen. //Sehiff and Hafen. 1980. 1 1.- P. 84−90.
- Oqilvie G.J., Oqilvie I.M. A heat treatment process usinq the tunqsten-inert qas arc. Metals Forum, 1979, V. 2. № 1. — p. 34−39.
- Муханов Г. Н., Просолов B.C., Юрасов С. А., Седунов В. К. Лазерное и плазменное упрочнение чугунов. // Действие электромагнитных полей на пластичность и прочность металлов и сплавов: Тез. докл., г. Юрмала, 1987, -С.211.
- Roqqen R. Durcissement superficiel par plasma desaciers an carbone et des fonttes. Revue de Metallurqie, 1979, V. 76, 1 7, 532−537.
- Reinke F.H. Local electric arc remeltinq process for the qeneration of wear-resistans white iron layers camshatts and cam followers. Electrowarme Int, 1981, 39,1 6, 315−321, 292, 296.
- Чачин В.Н., Бондаренко Л. И., Горшунов В. П. Плазменное термоупрочнение металлических поверхностей. Технология и организация производства. 1982, № 2. — С.42−43.
- Чачин В.Н., Бондаренко Л. И., Горшунов В. П., Дианов В. В. Исследование процесса плазменного поверхностного термоупрочнения. Технология и организация производства. 1982, 1 4. С.48−49.
- Ishida Т. Local meltinq of nodular cast iron by plasma arc. Journal of materials science, 1983,1 4, 2−5.
- Линник В.А., Онегина A.K., Андреев А. И., Алдаркин Х.Х., Синайский
- B.М., Григоренко Л. П. Поверхностное упрочнение сталей методом плазменной закалки. МиТОМ, 1983, № 4. — С.2−5.
- Андреев А.И., Алдаркин Х. Х., Казачков В. А., Агранат А. Р. Технология и организация угольного машиностроения. НТРС ЦНИЭИУголь. 1982, № 3/57. С.3−4.
- Ставрев Д.С., Ников Н. Я. Упрочнение серых чугунов при поверхностном отбеле низкотемпературной плазмой. МиТОМ. 1985, № 4. — С. 15−18.
- Кобяков О.С., Гинзбург Е. Г., Шляхтенко Н. Я. Зонное упрочнение поверхности стальных деталей. Машиностроение. 1984, 1 9. — С.101−105.
- Heck К.Н. Einflusse auf die Harts-chichtdicke beim Nockenwellen-Umschmels-harten. Werkstat und Betrieb, 1985, 118,1 5, 294−296.
- Кулагин И.Д., Борисов А. П., Краснов Ю. И. Поверхностное упрочнение деталей дуговым разрядом. // Теория и практика газотермического нанесения покрытий: Тез. докл., г. Дмитров. 1985, т.4.
- Поверхностная закалка зонным оплавлением. Информэлектро. Электротехника. Серия: Технология электротехнического производства. Электротерния. 1981, № 2. — С. 9−10.
- Локальное оплавление износостойкого ледебуритного поверхностного слоя на деталях из чугуна. Э.И. НИИНАвтопром: Технология автомобилестроения. 1981, № 5.
- Патент ФРГ № 3 302 415 МКИ С21Д9/30. Способ упрочнения поверхности чугунных деталей электродуговым оплавлением с последующей закалкой.
- Патент ФРГ № 2 825 579 МКИ С21Д9/30. Способ закалки методом переплава кулачкового вала тормозного двигателя и устройство для его осуществления.
- Патент США № 4 243 724 МКИ С21Д9/30. Упрочнение поверхности кулачковых валов.
- Патент Великобритания № 2 042 594 МКИ С21Д9/30. Упрочнение поверхности кулачковых валов.
- Патент Франция № 2 522 687 МКИ С21Д1/09. Установка для закалки кулачковых валов.
- Патент США № 4 312 685 МКИ С21Д9/30. Способ закалки с переплавом поверхности вращающегося вокруг своей оси вращения изделия.
- Балашов Б.Ф. Азотирование как метод повышения прочности деталей машин. В сб.: Повышение усталостной прочности деталей машин поверхностной обработкой. М.: Машиз, 1952. — С.71.
- Технология термообработки в 1990 году. Metal Proqr., 1984, 126, № 4, 59−61,63−64, 67, 69, 70.
- Тенденции в области термообработки. Navama-qaina 2000: Maqaina herramienta е. ins. prod., 1984, № 100, 111−115.
- Кулагин И.Д., Николаев A.B. О плотности тока в анодном пятне. -ФиХОМ, 1969. -С.3−9.
- Колонина Л.И., Смоляков В. Я. Вращательное движение приэлектродных участков и особенности расположения столба дуги в плазмотроне с вихревой газовой стабилизацией. ПМФТ, 1965, № 3, — С.80−84.
- Деграф Э.Д., Мусолин В. Н., Каирбаев Г. К. Баланс энергии в контрагированной анодном пятне при наличии приэлектродных струй. // Генераторы низкотемпературной плазмы: Тез.докл., г. Новосибирск, 1980, т.2.
- Черняк Р.В. Тепловые характеристики плазменной дуги при обдуве воздушно-углеводородной смесью. Автоматическая сварка, 1982, № 10. — С.10−14.
- Курочкин Ю.В., Муханов С. Н. Применение плазмотронов для термического упрочнения. Пост, семин. «Физико-технологические проблемы поверхности металлов», Тез. докл., г. Алма-Ата, 1987. С.24−28.
- Быховский Д.Г., Медведев, А .Я. и др. Плазменная технология (опыт, разработка, внедрение): Л.: Лениздат. 1989. — С. 150.
- Курочкин Ю.В., Демин Ю. Н., Зверев A.A. Режимы работы технологических плазмотронов с высоким вольт-амперным отношением и большим ресу4рсом работы электродов. // Химическое и нефтегазовое машиностроение. 2001. № 6. С.9−14.
- Зверев A.A. Резонансный источник питания. // Описание изобретения к патенту РФ. Бюл. № 35 RU 2 070 733. 1994.
- Курочкин Ю.В., Курочкин H.A., Зверев A.A. Высокоресурсный режим работы технологических плазмотронов. Сборник научных трудов МГИУ. 2001.-С. 34−38.
- Киселев В.Н. Плазмотроны для ручной и механизированной плазменной обработки. // Плазменные методы обработки металлов. — Л: ЛДНТП, 1989. -С. 97−100.
- Григайтис Ю.П., Амбразявичус А. Б. Обобщенная зависимость пульсаций мощности дуги от рабочих параметров ЭДП. Тез. докл. 9 Всесоюз. Конф. По генераторам низкотемпературной плазмы. Г. Фрунзе. 1983. С. 102−105.
- Вадяницкий O.A., Курочкин Ю. В. Генераторы плазмы жидких рабочих тел. Тез.докл. Всесоюз. конф. Электрические поля и прочность материалов. г. Юрмала, 1987. С.67−70.
- Жуков М.Ф., Анынаков A.C., Курочкин Ю. В. и др. Электродуговые генераторы с межэлектродными вставками. Н.: Наука, 1981. С. 230.
- Электродуговая газовая горелка на водяном паре. Патент РФ. № 1 731 020, 1993.
- Жуков М.Ф., Урюков Б. А. и др. Теория технической электродуговой плазмы. Н.: Наука, 1987. С. 290.
- Осинцев В.Г., Курочкин Ю. В., Григорьев А. Н. и др. Ресурсная стойкость электродов при воздушно-плазменной резке. // Изв. Сиб. отд. Академии наук СССР. Сер. техн. наук. 1987, № 15, вып. 4. С.61−64.
- Доброленский В.А., Желтобрюх Н. Д. Опыт внедрения плазменной резки на машинах с программным управлением. // Опыт промышленного применения плазменных видов обработки металлов. Л.: ЛДНТП, 1989. -С. 42−51.
- Белопольских И.П. Источники питания радиоустройств. // М.: «Энергия». 1971.-С.92.
- Дандарон Г. Н., Урбах Э. К., Мишне И. И. Эрозия анода в плазмотронах с осевой подачей газа. Тез. докл. 9 Всесоюз. конф. по генераторам низкотемпературной плазмы. 1983, г. Фрунзе. С. 180−181.
- Жиенбеков Г. Р. Влияние охлаждения составного термохимического катода на его эрозионную стойкость. Тез. докл. 9 Всесоюз. конф. По генераторам низкотемпературной плазмы. 1983, г. Фрунзе. С. 156−157.
- Курочкин Ю.В., Пустогаров A.B. Исследование плазмотронов с подачей рабочего тела через пористую межэлектронную вставку. В сб.: Экспериментальные исследования плазмотронов / под ред. М. Ф. Жукова. М.: «Наука», 1977. — С. 82−92.
- Варгефтик Н.В. Справочник по теплофизическим свойствам газов и жидкостей. -М.: «Наука», 1972. С. 720.
- Годунов С.К., Рябенький B.C. Разностные схемы. М.: «Наука», 1977. С. 430.
- Гудмен Т. Применение интегральных методов в нелинейных задачах нестационарного теплообмена. В кн.: Проблемы теплообмена. М.: «Атомиздат», 1967. — С. 41−96.
- Dkumbis R., Maqin P., Barbezat G. Laser treatment of Materials. Ed. Mordike Barry., Oberulsel: Informationsqes. Verl., 1984.479 p.
- Любина T.M., Мельников Г. Н. и др. Межэлектродные вставки из пенокерамики. Физика и химия обработки материалов. № 2,1981. С. 128−132.
- Жуков М.Ф., Анынаков A.C., Дандарон Т. Н. Эрозия электродов. В кн.: Приэлектродные процессы и эрозия электродов плазмотронов. // Новосибирск. «Наука». 1977. — С. 123−148.
- Курочкин H.A., Шляпин А. Д. Технологические аспекты плазменной резки стальных листовых заготовок. Межвузовский сборник научных трудов. //Москва. «МГИУ». 1999.
- Демин Ю.Н., Зверев A.A., Курочкин Ю. В., Курочкин H.A. Высокоресурсные режимы работы технологических плазматронов с повышенным вольт-амперным отношением. Сборник научных трудов МГИУ. 2001. С.48−51.
- Демин Ю.Н., Курочкин Ю. В., Курочкин H.A., Попов В. Б. Роботизированный участок плазменной резки с компьютерным управлением. Сборник научных трудов МГИУ. 2001. С.52−53.
- Демин Ю.Н., Курочкин Ю. В., Курочкин H.A. Высокоресурсные технологии плазменно-дуговой обработки. Международный научный симпозиум «Новые материалы, упрочняющие технологии и покрытия» М. МГТУ «НАМИ» 2000. С.55−77.
- Демин Ю.Н., Курочкин Ю. В., Курочкин H.A., Зверев A.A. Модификация свойств поверхности деталей из чугуна высокоскоростной закалкой из жидкого состояния. Межвузовский сборник научных трудов. М., МГИУ., 2001., С.274−277.