Литая износостойкая сталь и режимы ее обработки для изготовления деталей шестеренных дозировочных насосов вискозного производства
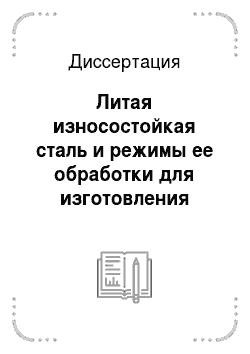
Диссертация
Исследования влияния температуры нагрева под закалку в интервале температур от 1323°К до 1423°К позволили сделать вывод, что с повышением температуры нагрева коррозионная стойкость увеличивается более, чем на порядок. Полученные результаты связаны с превращениями, охватывающими количественные изменения структурных составлящих стали: мартенсита, аустенита и карбидов. После закалки с 1338°К в стали… Читать ещё >
Содержание
- ГЛАВА I. ОБЗОР СОСТОЯНИЯ ВОПРОСА И ЗАДАЧИ ИССЛЕДОВАНИЙ
- 1. 1. Требования к шестеренным дозировочным насосам
- 1. 2. Коррозионная стойкость и износостойкость материалов, применяемых для изготовления шестеренных дозировочных насосов. .II
- 1. 3. Влияние систем легирования на коррозионную стойкость, износостойкость.и.механические свойства сталей
- 1. 4. Влияние режимов финишных операций механической обработки на долговечность рабочих поверхностей деталей насосов
- 1. 5. О перспективности использования литейной технологии для производства деталей. шестеренных дозировочных, насосов
- ВЫВОДЫ
- ГЛАВА II. МЕТОДЫ ИЗСЛВДОВАШЙ
- 2. 1. Методы коррозионных исследований
- 2. 2. Методы исследований износостойкости. разрабатываемых сталей
- 2. 3. Методы определения износостойкости. насосов типа 1ШШ-0,6ИЗ и ПНШ-ЗИЗ
- 2. 4. Методы металлографических исследований
- 2. 5. Методы исследований фазового состава. литой стали
- 2. 6. Методы исследования структуры тонкого. поверхностного слоя литой стали
- 2. 7. Методика проведения исследований свойств литой стали после многократного переплава
- ГЛАВА III. РАЗРАБОТКА. ИЗНОСОСТОЙКОЙ И
- КОРРОЗЙОННОС ТОЙКОЙ СТАЛИ И
- ИССЛЕДОВАНИЕ ЕЕ СВОЙСТВ
- 3. 1. Сравнительные данные по износостойкости и коррозионной стойкости сталей на основе легированных дополнительным элементом
- 3. 2. Исследование влияния режимов закалки разработанной стали 6СК17М2НД на изменение коррозионной стойкости, твердости, структуры
- 3. 3. Исследование влияния отпуска на свойства стали 6СК17М2ЕИ
- ВЫВОДЫ
- ГЛАВА 1. У ИССЛЕДОВАНИЕ ВЛИЯНИЯ ФШЭДШОЙ ОБРАБОТКИ СТАЛИ 60П7М2НД НА
- ЭКСПЛУАТАЦЮШШЕ СВОЙСТВА В
- СОЛЯНОКИСЛОЙ СРБЗДЕ
- 4. 1. Исследование влияния режимов шлифования на коррозионную стойкость сталей 60Х17М2ЩТ и 95X18. .. П
- 4. 2. Исследование влияния режимов шлифования и доводки на структуру и свойства приповерхностного. слоя сталей 6СК17М2ВД и 95К
- 4. 3. Влияние финишных операций механической обработки на коррозионную стойкость и износостойкость в солянокислой среде
- ВЫВОДЫ
- ГЛАВА. У ИССЛЕДОВАНИЕ ХИМИЧЕСКОЙ И СТРУКТУШОЙ СТАБИЛЬНОСТИ СТАЛИ 60Н7М2НП, ИСПОЛЬЗОВАННОЙ ПШ ИЗГОТОВЛЕНИИ ШЕСТЕРЕННЫХ ДОЗИРОВОЧНЫХ НАСОСОВ, В ПРОЦЕССЕ МНОГОКРАТНОГО ПЕРЕПЛАВА
- ВЫВОДЫ
- ГЛАВА 71. ОПЫТНО-ПРОМЫШЛЕННОЕ ИСПЫТАНИЕ ШЕСТЕРЕННЫХ ДОЗИРОВОЧНЫХ НАСОСОВ, ИЗГОТОВЛЕННЫХ ИЗ
- ЛИТОЙ СТАЛИ 60Х17М2ВД
- ВЫВОДЫ
Список литературы
- Геллер Ю.А. Инструментальные стали. — М.: Металлургия, 1968. — 568 с.
- Гуляев А.П. Металловедение. М.: Металлургия, 1977. -646 с.
- Журавлев В.Н., Николаева О. И. Машиностроительные стали. Справочник. 3-е изд. перераб. и доп. — М.: Машиностроение, 1981. — 391 с.
- Лахтин Ю.М., Леонтьева В. П. Материаловедение. М.: Машиностроение, 1972. — 510 с.
- Клшов И.Я. Коррозия химической аппаратуры и коррозион-постойкие материалы. М.: Машиностроение, 1967. — 468 с.
- Бержиани В.М. Исследование влияния некоторых легируюцих элементов на коррозионную стойкость высокомарганцевой нержавеющей стали. Тр. ин-та металлургии АН Груз. ССР, 1962, 13, с. 105−116.
- Износостойкие материалы в химическом машиностроении. Справочник. / Под ред. Ю. М. Виноградова. Машиностроение, Ленинград. отд-ние, 1977. — 256 с.
- Рускол Ю.С., Витер Л. И., БалаКин А.И., Фокин М. Н. Коррозия сплавов титана в Кбнцзнтрированных растворах хлоридов при температуре до 160°. Защита металлов, 1982, т. 18, J2 4, с. 516−519.
- Томашов Н.Д. КоррозионностойКие сплавы и перспективы их развития. Защита металлов., 1981, т. 17, JS I, с. 16−33.
- Рускол Ю.С., Мосолов A.B., Дутикьва Н. И. и др. Отечественный и зарубежный опыт применения оборудования из титана и его сплавов в химической промышленности Обзоры по отдельнымпроизводствам химической промышленности. М., НИИТЭХИМ, 1973, Вып. 49, 70 с.
- Lewis W. Gleekman, Non ferrous Metals. Chemical Engineering, 1970, 77, N22, p 111−118.
- Chem. Process (USA), 1972,35, N3, p16.
- Гэлицкий Б.А., Абелев M.M., Колосова Л. П. и др. Титан и его сплавы в химическом машиностроении. М.: Машгиз, I963.-262C.
- Энциклопедия неорганических материалов. Киев, 1977, т. I, с. 571−575, т. П, с. 394−398.
- Соркин Л.М. упрочнение стали борированием. M.: Машиностроение, 1972. 64 с.
- Самсонов Г. В.,. Эпик А. П. Тугоплавкие шлфытия. М.: Металлургия, 1973. 400, с.
- Акцептованная заявка Jfi 2 260 010 (ФРГ). Опубл. 14.06.73
- Патент № 802 310 (ФРГ) Опубл. 8.02.51.
- Патент Я 875 144 (ФРГ) Опубл. 4.05.53.
- Chemie-Zahnradpumpe fur universellen Einsatz. — Chem.+ Anlag + Verfahren, 1976, NU, s.38.
- Kompakte Pumpe aus Polyacetal.— Vui nach rieht en, Nr. 41/15. Oktober, 1976. s.7.
- Hochverschlei?fester Pumpenwerkstoff. — У Di i.122, 1980, N12, Junif s.490.
- Stainless steel alloy has improved corrosion resistance. Eng. Mater, and Bes., 1979,23, N1, p. 24−25.
- Ш1 nW (Hardenuble Stainless Steel) Alloy Digest, 1969, Nov.
- Металловедение и термическая обработка стали. Справочник. /Под редакцией Бернштейна М. П. и Рахштадта А. Г. 2-е изд., перераб. и доп. М.: Металлургиздат, 1962, т. П, с. 755−1656.
- Материалы в машиностроении. Выбор и применение: Справочник в пяти томах /Под общ. ред. И. В. Кудрявцева. Том 3 специальные стали и сплавы. /Под ред. Ф. Ф. Химушина. М.: Машиностроение, 1968. — 446с.
- Томашов Н.Д. Теория коррозии и защита металлов. М.: АН СССР, I960. — 591с.
- Коррозия. Справочник. /Под ред. Л. Л. Шрайера, пер. с англ. М.: Металлургия, 1981. — 632с.
- Бабаков A.A., Приданцев М. В. Коррозионностойкие стали и сплавы. М.: Металлургия, 1971. — 320с.
- Вот A., Coutsouradis D. Entwicklung von verschlei? —• und korrosionsbestandigen Legierungen fur den Einsatz in wa? rigen Medien -Molybdan Dienst, 1972, N80, April, s. 10−11.
- Томашов Н.Д., Чернова Г. П. Коррозия и коррозионностойкие сплавы. М.: Металлургия, 1973. — 232с.
- Бидуля П.Н. Технология стальных отливок. М.: Металлург-издат, 196I. — 352с.
- Томашов Н.Д., Маркова О. Н., Чернова Г. П. Влияние легирующих элементов на анодное растворение нержавеющих сталей в средах, содержащих хлор-ионы. В кн.: Коррозия и защита конструкционных сплавов. — М.: Наука, с. 3−26.
- Калуткин И.И., Шаповалов Э. Т., Устименко М. Ю., Беляева В. А. Питтинговая коррозия сплава типа ХН 40МДБ с различным содержанием молибдена. Защита металлов, 1981, т. 17, гё 5, с.553−555.
- Чернова Г. П., Чигиринская Л. А., Томашов Н. Д. Исследование влияния азота, палладия, молибдена на коррозионное и электрохимическое поведение хромоникелевых сталей в разбавленнойсоляной кислоте. Защита металлов, 1980, т. 16, с. 3−7.
- Томашов Н.Д., ГолованенКО С.А., Ульянин Е. А., и др. Коррозионные и механические свойства высокохромистых ферритных сталей повышенной чистоты, легированных молибденом и палладием. -Защита металлов, 1980, т. 16, JS 2, с. I05-III.
- Тодт Ф. Коррозия и защита от коррозии. Москва, Ленинград.: Химия, 1966. — 848 с.
- Каховский А.И. Сварка высоколегированных сталей. -Киев.: Техника, 1975. 376 с.
- Еременко A.C., Щесно Л. П., Тарабан А. Й., Северина Л. С. Влияние легирования азотом на свойства особонизКоуглеродистых нержавещих сталей. Физико-химическая механика материалов, 1975, т. II, J6 6, с. 62−66.
- Шапиро М.Б., Бернштейн М. Л., Барсукова И. М. Влияние азота на стойкость стали Tima 03XI9AT3HI0 против меж^ристал-литной Коррозии. Металловедение и термическая обработка металлов, 1984, Я' I, с. 45−47.
- Лузина О.И., Фрейман Л. И., Фельдгандлер Э. Г., и др. Исследование питтинговой Коррозии сталей 04Х25Н5М2 й 04Х25Н5М2 в хлоридных растворах. Защита металлов, 1979, т. 15,'"$ 5, с. 545−551.
- ГлазКова С.А., Шапиро М. Б. Об устойчивости хромоникеле-вой стали типа 18−12- Мо к локальной коррозии в хлоридных растворах. Защита металлов, 1979, т. 15, $ 3, с. 320−324.
- Медовар Б. И. СварКа жаропрочных аустенитных сталей и сплавов. М.: Машиностроение, 1966. — 430 с.
- Кипцел А.Б., Руссел ФрэнКс ВысоКохрошютые нержавеющие и жароупорные стали. М.: Металлургиздат, 1945. — 473 с.
- Циммерман Р., Рюнтер К., Металлургия и материаловедение:
- Справ, изд. Пер. с нем. /Под. ред. П. И. Полухина и М. Л. Бернштейна.-М.: Металлургия, 1982. 480 с.
- Ажогин Ф.Ф. Коррозионное растрескивание и защита высокопрочных сталей. ГЛ.: Металлургия, 1974. — 256 с.
- Пйповалов Э.Т., Ульянин Е. А., Казакова Г. В. и др. Влияние кремния, меди и кобальта на коррозионное растрескивание и питтинговую коррозию стали 03XI8H30. Физико-химическая механика материалов, 1983, т. 19, J6 5, с. 48−52.
- Шлугер М.А., Ажогин Ф. Ф., Ефимов Е. А. Коррозия и защита металлов. М.: Металлургия, 1981. — 216 с*
- Тавадзе Л.Ф., Гольдштейн Я. Е., Асатиани Г. Н. и др. Влияние содержания меди на технологические и служебные свойства высоколегированных аустенитных сталей. Металловедение и коррозия металлов, 1980, с. 23−28.
- Дроздов Ю.Н., Арчегов В. Г., Смирнов В. И. Противозадщрная стойкость трущихся тел. М.: Наука, 1981. — 140 с.
- Askwith 1С. The basis mechanisms of wear Surfac J, mo, 11, N4,p. 2−6
- Котречко A.A., Саткей Б. Проблемы трения и изнашивания, 1980, JS 18, с. 57−62.
- Miyoshi Kazuhisa, Buckley Donald H ¦ The friction and wear of metals and binaru aiioys in contact With an abrasive grit of single -crustai siiicon carbide ASLE Trans, 1980,23, N4-, p, V 60-у 69. discuss, p 469
- Костецкий Б.И., Носовский И. Г., Караулов А. К. и др. Поверхностная прочность материалов при трении /Под общ. ред.
- Б.И. КостецКого. Киев.: Техника, 1976. — 296 с.
- Трение, изнашивание и смазКа: СггравочниК. /Под ред. И.В. КрагельсКого и В. В. Алисина. М.: Машиностроение, Кн. I, 1978. — 440 с.
- Круман Б.Б., Крупицына В. А. Коррозионно-механичесКий износ оборудования. М.: Машиностроение, 1968. — 104 с.
- Влияние среды на взаимодействие твердых тел при трении: Тез. доКл. Всесоюзн. научно-техн. Конф. Днепропетровск, 1981, 245 с.
- Боуден Ф.П., Тейбор Д. Трение и смазка твердых тел. /Пер. с англ. под ред. И.В. КрагельсКого. М.: Машиностроение, 1968. — 542 с.
- Лазарев Г. Е., Харламова Т. Л., ВерейКин В.И. Электрохимические и антифрикционные характеристики пары трения. Защита металлов, 1980, т. 16, $ 4, с. 464г-466.
- Лазарев Г. Е. Износостойкость материалов при трении в Коррозионно-аКтивных средах. Химическое и нефтяное машиностроение, 1974, i? 7, с. 38−39.
- МачевсКая P.A., ТурКовсКая A.B. Влияние трения на потенциал стали в растворах с различными значениями pH. Журнал прикладной химии, 1975, т. 38, В 2, с. 335−341.
- ЖуК н.П. Курс теории Коррозии и защиты металлов. М.: Металлургия, 1976. — 472 с.
- Марковский Е.А. О структурной и химической стабильности отливок^ работающих на износ в агрессивных средах. Литейное производство, 1979, с. 27−29.
- Марковский Е.А., КириевсКий Б.А. Влияние легируицих элементов на стабильность состава и структуры поверхностных слоев трущихся сплавов. Проблемы трения и изнашивания. -Киев.: Техника, 1980, вып. 18, с. 24−30.
- ШрКовсКий Е. А. Диффузия углерода в слое металла высокопрочного чутуна, деформированного трением. В сб.: Структураи свойства литых сплавов. Киев.: Изд-во АН УССР, 1962, с. 135−142.
- Марковский Е.А. Основные закономерности, происходящие при изнашивании материалов. В сб.: Литые износостойкие материалы. — Киев.: НауКова думКа, 1969, с. 3−15.
- Webster 0. Mreasing the tougness of the martensiti’M Sireinless Steel AFC 77 by control of reteined mtenite content, ausforming and Strainaging. Trans. Amer. Cos. Metals, 1968, 61, p. 816 -828.
- DiboldScheidl H. Aushartbare chemisch bestandige Stable -Urabt, 1975, 24, N9, s. 458−466.
- Каличак Т.Н., ПохмурсКий В.И., Швед M.M., и др. Усталостная" и Коррозионноусталостная црочность некоторых мартен-ситныХ нержа вещих сталей с 10, хрома. Физико-химическая механик материалов, 1970, т. 6, JS 3, с. ЦЗ-116.
- Chlorimet 3 (Korrosion resistand cast п№ -base allog) ~ Allog Digy 1980/ Nov.
- Михин H.M., Кумяева JT.A., Родионов АЛО. Исследование влияния Коррозионно-аКтивных веществ на изнашивание твердых тел. Трение и износ, 1984, т. 5, $ I, с. 143−148.
- Батраков В. П. Теоретические основы Коррозии и защиты металлов в агрессивных средах. В Кн.: Коррозия и защита металлов. — М.: Оборонгиз, 1962, с. 5−32-
- Карпенко Г. В., Бабей Ю. И., Карпенкь И. В., Гутман Э.М.
- Уйрочнение стали механической обработкой. Киев.: Наумова ДумКа, 1966. — 202 с.
- Хитаришвили М.Г., Бабей Ю. И., Василенко и. И. Влияние миКрогеометрии поверхности и физико-механического состояния поверхностных слоев деталей на их Коррозионное растрескивание.-ФизиКо-химичесКая механик материалов, 1972, J? 4, с. 50−53.
- Бабей 10. И, Сопрунюк н.Г. Защита стали от Коррозионное механического разрушения. Киев.: Техникаt 1981. — 126 с.
- ИванецВ.И., Манжар В. А., Черватюк в.А. СтруКтурно-напряженное состояние поверхности и контактная долговечность стали после шлифования Кругами из сверхтвердых материалов. ФизиКо-химичесКая механик штериалов, 1982, т. 18, № 5, с. II5-II6.
- Маталин A.A. Технологические методы повышения долговечности деталей машин. Киев.: Техника, 1971. — 144 с.
- Шульман П.А., Созин Ю. И., КолесниченКо Н.Ф., Вишневский A.C. качество поверхности, обработанной алмазами. -Киев.: Техника, 1972. 148 с.
- Сагарда A.A., Вальчук Г. И., Делеви В. Г., МишнаевсКий л.П. Состояние поверхностных слоев закаленной стали при алмазном шлифовании.- ФизиКо-химичесДая механик материалов, 1969, т. 5,1. J6 5, с. 577−580.
- Бабей Ю.И. Об аношльном ускорении диффузии цри образовании белых слоев. ФизиКо-химичес^я механик материалов, 1975, т. II, В 4, с. 104−107.
- Бабей Ю. И. Рябов Б.Ф., Голубец В. М., ДядченКо Б.Т., Капарова I.A. 0 природе белых слоев, возникавших в цроцессе некоторых видов обработки стали. ФизиКо-химичесКая механик материалов, 1973, т. 9, JS 4, с. 33−39.
- Выгоде ад И. П. К вопросу о влиянии белого слоя на выносливость углеродистых сталей. ФизиКо-химичесКая механика материалов, 1974, т. Ю, la 5, с. II8-I20.
- ВарпенКо Г. В. Прочность стали в Коррозионной среде.- Москва Киев.: Машгиз, 1963. — 188 с.
- Емелин М.И., Герасименко A.A. Защита машин от Коррозии в условиях эксплуатации. М.: Машиносароение, 1980. — 224 с.
- КарпенКо Г. В. Оптимальные условия для работы m тер наловв активных средах. ФизиКо-химичесКая механика материалов, 1973, т. 9, 1й 2, с. 3−5.
- Томашов Н.Д. Теория Коррозии и защиты металлов. М.: Машгиз, i960. — 177 с.
- Романов В.В. Коррозионное растрескивание металлов. -М.: Машгиз, 1962. 855 с.
- Эванс Ю.Р. Коррозия и окисление металлов. -41.: Машгиз, 1962. 855 с.
- РябченКов A.B., Никифорова В. М. Коррозия и защита металлов в машиностроении. М.: Машгиз, 1959.
- АКимов Г. В. Основы учения о Коррозии и защите металлов.-М.: Металлургиздат, 1946. 463 с.
- Ацебеева А.И., Левин С. З. Ингибиторы коррозии металлов.-М.: Металлургиздат, 1946. 463 с.
- Антропов Л. И. Формальная теория действия органических ингибиторов Коррозии. Защита металлов, 1977, т. 13, вып. 4, с. 387−399.
- Балезин С.А. Об определяющее факторах Коррозии и инги-бирования. Журнал физ. хиглия, 1973, т. 47, Л 12, с. 29 612 964.
- Шеин А.Б., Кузнецов В. В. Исследование Коррозионно-элеКтро химического поведения упруго дефюрм1фО ванной стали в ингибиро-ванной Кислоте. ФизиКо-химичесКая механика материалов, 1983, т. 19, В 15, с. 100−101.
- Вшивцева Л.В., Машаева В. И. Овчинникова Т.М. К вопросу о методике определения водорода в стали. В кн.: Наводорожи-вание металлов. — I.: Изд-во ЛГУ, 1974, с. 14−17.
- Козлов E.H., Антропов Л. И. Использование ингибиторов кислотной коррозии для защиты стали от наводороживания при Катодной поляризации в серной Кислоте. Коррозия и защита метахлов. — Калиниград, 1978, JS 4, с. 49−56.
- СнекКин В.А., Сергеев М. И. Распределение водорода в пружинной стали 65 Г при Катодной поляризации в серной Кислотеи его влияние на микротвердость. Коррозия и защита металлов.-Калининград.: Изд-во Кгу, 1978, вып. 4, с. 31−35.
- Иванов Е.С., Балезин С. А., Иванов С. С. Ингибиторы Кислотной Коррозии и их влияние на механические характеристики высокопрочной стали. Защита металлов, 1980, т. 16, J5 I, с. 8083.
- Гутман Э.М. Механохимия металлов и защита от Коррозии.
- М.: Металлургия, 1974. 231 с.
- Розенфельд И.Л., Жигалова К. А. Ускоренные методы Коррозионных испытаний металлов. М.: Металлургия, 1966. — 344 с.
- Романов Б.В. Методы исследования Коррозии металлов.-М.: Металлургия, 1965. 253 с.
- Жук Н.П. %рс Коррозии и защиты металлов. М.: Металлургия, IS68. — 407 с. 109. коррозия и защита химической аппаратуры: Справочное руководство, т. I /Под редакцией A.M. Сухотина. JT.: Химия, 1969. — 559 с.
- ПО. ТомашовН.Д., ЖукН.П., Титов В. А., Веденеева М. А. Лабораторные работы по Коррозии и защите металлов. М.: Металлургия, 1971. — 279 с.
- ДончуК п.П., КостецКий Б. И. Влияние поверхностных окисных пленок на Коэффициент трения и схватывание некоторых металлов. В сб.: Повышение долговечности литых материалов. -Киев.: ИПЛАН ЗССР, 1969, с. 134−139.
- Ступа В.И. Влияние некоторых конструктивных параметров шестеренного дозировочного насоса химических волокон на величину и неравномерность его производительности.: Автореф.
- Дис.. Канд. техн. наук, — Москва, 1971.
- Приборы и методы физического металловедения. Выпуск j /Под ред. Ф. Вейнберга М.: Мир, 1973. — 427 с.
- БеККерт М., Клеш X. СцравочниК по металло1рафичесКому травлению. Пер. с нем.- М.: Металлургия, 1979. — 336 с.
- ФизиКо-химичесКие методы исследования металлов /Под ред. Н. И. Еремина М.: Мэшгиз, 1950. — 239 с.
- Техника электронной микроскопии: Пер. с англ. М.: Мир, 1965. — 399 с.
- Качанов Н.И., МирКин Л.И. Рентгеноструктурный аналюз:
- Практическое руководство. M.: Машгиз, I960. — 216 с.
- Миркш Л.И. РентгеноструКтурный Контроль машиностроительных материалов: Справочник. М.: Машиностроение, 1979. — 134 с.
- Батуринск^я H.I., КальчуК H.A., Черный В. Г. Определение параметров тонкой кристаллической структуры в поверхностных слоях материала с помощью рентгеновского дифраКтометра. -ЗаводсКая лаборатория, 1982, т. 48, JS 7, с. 38−40.
- Постников В. И. Радиоактивные изотопы в исследовании и автоматизации Контроля за износом, ~ М. — Машиностроение, 1967. 140 с.
- КостецКцй Б-И. Трение cmaife и тгэчос в машинах. -Яиев.: Техник, 1970. 3S6 с.
- Основы научных исследований в литейном производстве /Под общ. ред. А.ЕДривошеева. -г Киев-Донецк.: Вица шКола. Головное езд-во, 1979. 168 с.
- Хартман К, ЛецКий Э., Шефер В. и др. Планирование эксперимента в исследовании технологических процессов. М.: Мир, 1977. — 552 с.
- Туфанов Д. Г. Коррозионная стойкость нержавевдих сталей, сплавов и чистых" металлов. М.: Металлургия, 1982. -352 с.
- АндргаценКо Ф.К., Орехова В. В. Теоретичес1^ электрохимия. Киев.: Вица шКола, 1979. — 167 с. 127.~ДамасКин Б.Б., Петрий O.A. Основы теоретической электрохимии. М.: Высшая шКола, 1978. — 230 с.
- ПиККеринг Ф.Б. физическое металловедение и разработка сталей: Пер. с англ.- М.: Металлургия, 1982. 184 с. 129. курдюмов Г. В. Явление закалки и отпуска стали. М.: Металяургиздат, 1960. — 64 с.
- Коррозия: Сцрав. изд. пер. с англ. /Сод ред. Л.Л.Щрайе-ра. М.: Металлургия, 1981. — 632 с.
- Хоникомб Р. У. К Некоторые механизмы упрочнения легированных сталей. В кн.: Высоколегированные стали: Пер. с англ. /Под ред. А. Г. Рахштадта. — М.: Металлургия, 1969, с. 7−43.
- Томашов Н.Д. Теория коррозии и защиты металлов. М.: Изд-во АН ССОР, 1959. — 592 с.
- Томашов Н.Д., Стрекалов П.В. В кн.: Коррозия и защита конструкционных материалов. — М.: Машгиз, 1961, с. 196 199.
- Цриданцев М.В., Талов Н. П. Левин Ф.Л. Высокопрочные аустенитные стали. М.: Металлургия, 1969. — 248 с.