Разработка и исследование методов радиографического контроля глубины дефектов сварных соединений
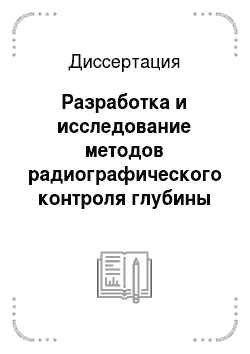
Диссертация
Актуальность работы. Среди продукции предприятий машиностроения большой объем занимают сварные металлоконструкции, в том числе для изготовления машин, работающих в тяжелых и опасных условиях. Такие машины подлежат особому контролю Госгортехнадзора России, Госатомнадзора России и других государственных органов как на стадии изготовления, так и при эксплуатации. Неисправность этих машин может… Читать ещё >
Содержание
- 1. Определение параметров дефектов сварного шва по результатам радиографического контроля (литобзор)
- 1. 1. Дефекты сварного шва
- 1. 1. 1. Причины образования дефектов сварного шва
- 1. 1. 2. Влияние дефектов на работоспособность сварных металлоконструкций
- 1. 2. Радиационный контроль в промышленности
- 1. 2. 1. Радиационный контроль как метод дефектоскопии
- 1. 2. 2. Формирование радиационного изображения
- 1. 2. 3. Влияние различных факторов на выявляемость дефектов сварного шва при радиографическом контроле
- 1. 2. 4. Определение размеров дефектов при радиографическом контроле
- 1. 2. 4. 1. Необходимость определения глубины дефектов
- 1. 2. 4. 2. Существующие методы определения глубины дефектов
- 1. 2. 4. 3. Влияние рассеянного излучения на формирование изображения дефектов
- 1. 1. Дефекты сварного шва
- 1. 3. Цель и задачи диссертационной работы
- 2. 1. Существующие способы расчета глубины дефекта
- 2. 1. 1. Способы расчета, основанные на законе ослабления излучения
- 2. 1. 2. Расчет глубины дефекта с использованием экспериментальных данных
- 2. 1. 3. Связь между размерами дефекта и нерезкостью
- 2. 2. Предложенный метод расчета глубины дефекта
- 2. 2. 1. Анализ влияния ширины дефекта на контраст его изображения
- 2. 2. 2. Расчет характеристик широкого дефекта
- 2. 2. 3. Расчет характеристик узкого дефекта
- 2. 2. 4. Обоснование условий экспериментальной проверки предложенного метода расчета глубины дефекта
- 2. 2. 4. 1. Выбор объекта исследования
- 2. 2. 4. 2. Состав экспериментального комплекса
- 2. 2. 4. 3. Имитаторы непроваров
- 3. 1. Основные соотношения для расчета погрешностей измерений
- 3. 2. Расчет глубины дефекта
- 3. 3. Расчет глубины непровара в корне шва
- 3. 4. Расчет глубины непровара по сечению сварного шва
- 3. 5. Исследование нерезкости как функции глубины дефекта
- 4. 1. Расчет глубины реальных непроваров в корне сварного шва
- 4. 2. Расчет глубины реальных непроваров по сечению сварного шва
- 4. 3. Апробация предложенной методики на дефектах типа газовых пор и шлаковых включений
- 4. 4. Исследование глубины залегания дефектов сварного шва
- 4. 4. 1. Влияние глубины залегания дефекта на расчет его размеров в направлении просвечивания
- 4. 4. 2. Предложенный метод определения глубины залегания малоконтрастного дефекта
- 4. 5. Оценка экономической эффективности от внедрения предложенной методики расчета глубины дефекта
Список литературы
- Еремин К.И. Остаточный ресурс циклически нагруженных металлоконструкций с трещиноподобными дефектами. Дис. на соискание ученой степени доктора техн.наук. Магнитогорск, 1995. -454 с.
- Круль К. Оценка работоспособности металлоконструкций строительных машин с дефектами. Дис. на соискание ученой степени доктора техн.наук. М., 1999 г. — 289 с.
- Соколов И.И., Гисин П. И. Руководство для сварщиков. Свердловск, Средне-Уральское книжное издательство, 1973
- Троицкий В. А, Радько В. П., Демидко В. Г. Дефекты сварных соединений и средства их обнаружения. Киев: Вища школа, 1983. -144 с.
- Иванов A.B. Прогнозирование качества формирования однопроходного шва при сварке плаящимся электродом в защитных газах на основе математического моделирования: Автореф. дис. на соискание ученой степени канд. техн. наук. М., 1996 — 18 с.
- Гончаров И.А., Пальцевич А. П., Токарев B.C. Влияние водорода в низколегированном металле шва на порообразование при сварке под флюсом // Автоматическая сварка. 2001. — № 7. — С.21−23.
- Головко В.В. Моделирование состава неметаллических включений в металле сварных швов высокопрочных низколегированных сталей // Автоматическая сварка. 2001. — № 5. — С.3−7.
- Куркин С.А., Николаев Г. А. Сварные конструкции. Технология изготовления, механизация, автоматизация и контроль качества в сварочном производстве. М.: Высшая школа, 1991. — 398 с.
- Остсемин A.A., Дильман B.JI. Оценка влияния дефектов и эксплуатационной надежности сварных прямошовных и спирально-шовных труб // Сварочное производство. -2001. -№ 9. С. 6−12.
- Большаков A.M., Левин А. И., Прохоров В. А. Методика установления сочетания причин разрушения резервуаров // Заводская лаборатория. Диагностика материалов. 2001. — № 10. — С. 48−50.
- Махненко В.И., Великоиваненко Е. А., Розынка Г. Ф., Пивторак Н. И. Компьютерное моделирование сварочных процессов как средство прогнозирования дефектов в сварных соединениях // Автоматическая сварка. 1999. — № 12. — С. 10−19
- Сукнев C.B. Учет масштабного эффекта в расчетах на прочность элементов конструкций с концентраторами напряжений // Заводская лаборатория. Диагностика материалов. 2001. — № 10. — С.57−60.
- Чабуркин В.Ф., Канайкин В. А. Оценка опасности дефектов сварных соединений при диагностике газонефтепроводов // Сварочное производство. -2000. № 9. — С. 41−44.
- Конев A.B. Методика оценки несущей способности стальной оболочки магистрального газопровода с дефектами по результатам внутритрубной дефектоскопии: Автореф. дис. на соискание ученой степени канд. техн. наук. Томск, 1998 -28 с.
- Кузьмин В.Р., Прохоров В. А., Афонская Г. П. Оценка несущей способности резервуаров с дефектами // Контроль. Диагностика 2001. — № 8. — С.7−10.
- Тиньгаев А.К., Губайдулин Р. Г., Елсуков Е. И. Совершенствование нормативных требований к качеству сварных соединений стальных конструкций. 4.2 // Сварочное производство. 2000. — № 12. — С.24−28
- Остсемин A.A. Анализ несущей способности действующеготмагистрального нефтепровода при наличии дефектов в продольном сварном шве//Сварочное производство. 1998.-№ 9.-С. 11−15
- Шахматов М.В., Ерофеев В. В., Коваленко В. В. Оценка прочности механически неоднородных сварных соединений с трещиноподобными дефектами в условиях квазимягкого разрушения // Сварочное производство. -2000. № 7. — С.5−9.
- Ерофеев В.В., Шахматов М. В., Остсемин A.A. Влияние дефектов на несущую способность сварных соединений цилиндрических деталей при квазихрупком разрушении // Сварочное производство. 1997. — № 10.-С.10−14
- Ерофеев В.В., Шахматов М. В., Коваленко В. В. Влияние ориентации дефектов на несущую способность сварных соединений, ослабленных мягкими прослойками // Сварочное производство -2000. № 8. — С. 1317
- Клюев В.В. Неразрушающий контроль и диагностика безопасности // Заводская лаборатория. Диагностика материалов. 1998. — № 1. — С. 1628
- Глазков Ю.А., Беда П. И. К вопросу остановки роста катастроф // Надежность и контроль качества. 1998. — № 8. — С.43−48
- Ермолов И.Н., Останин Ю. А. Методы и средства неразрушающего контроля качества. М.: Высшая школа, 1988. — 368 с.
- Красько А. Г. Красько В.Г., Ивакин А. Н. Рентгенотелевизионные системы интроскопии // Контроль. Диагностика. 1999. — № 5. — С. 3132.
- Чахлов B. JL, Москалев Ю. А., Темник А. К. Система цифровой радиографии для неразрушающего контроля в диапазоне энергий излучения 1 .20 МэВ // Контроль. Диагностика. 2000. — № 9. — С. 2223.
- Москалев Ю.А., Дмитриева A.B., Григорьев C.B. Интроскоп дляГ
- Шуринов В.А. Использование CCD-камер в радиационных электронно-оптических преобразователях // Контроль. Диагностика. 2001. — № 12. -С. 16−19.
- Мамчев Г. В. Оценка точности выполнения наблюдателями метрический операций в стереотелевизионных устройствах отображения радиационных изображений // Техническая диагностика и неразрушающий контроль. 1992. — № 2. — С. 7−15.
- Крутеев A.B. К вопросу оценки выявляемости несплошностей при внедрении рентгенотелевизионного контроля // Контроль. Диагностика. -2001. -№ 12. С.24−28.
- ГОСТ 20 426–82. Контроль неразрушающий. Методы дефектоскопии радиационные. Область применения. Введ. с 01.07.83. — М.: Изд-во стандартов, 1984. — 24 с.
- Приборы для неразрушающего контроля материалов и изделий: Справочник: В 2 книгах / Под ред. В. В. Клюева. М.: Машиностроение, 1986.-Кн. 1 -488 с.
- Вяткин И.В. Оптимизация процесса радиографии на базе импульсного рентгеновского аппарата МИРА-2Д: Автореф. дис. на соискание ученой степени канд.техн.наук. Томск, 1993 — 15 с.
- Багриевич В.П. Исследование и разработка средств автоматизации дефектоскопического комплекса на базе линейного ускорителя электронов: Автореф. дис. на соискание ученой степени канд. техн. наук.-СПб., 1992- 17 с.
- Капустин В.И., Максимова Т. Н., Стасеев В. Г., Фирстов В. Г., Шведов Л. И., Орлов Н. С. Стандартизация радиографического метода контроля // Стандарты и качество 2002. — № 2. — С.27−29.
- Пронин С.Е. Использование рентгеновского аппарата SMART 300 впромышленной дефектоскопии при одностороннем доступе к объекту контроля // Контроль. Диагностика 2001. — № 7. — С.5−8.
- Добромыслов В.А., Косарина Е. И. Номограммы для определения режимов радиографического контроля сварных соединений трубопроводов // Контроль. Диагностика. 2000. — № 4. — С. 11−13.
- Румянцев C.B., Штань A.C., Гольцев В. А. Справочник по радиационным методам неразрушающего контроля. М.: Энергоиздат, 1982.-240 с.
- Добромыслов В.А., Соснин Ф. Р. Формирование изображений дефектов в радиационной дефектоскопии // Контроль. Диагностика. 2000. — № 1. — С.14−17.
- ГОСТ 7512–82. Контроль неразрушающий. Соединения сварные. Радиографический метод. Введ. с 01.01.84. — М.: Изд-во стандартов, 1988.-32 с.
- Зуев В.М. Оценка выявляемости дефектов при радиографическом контроле сварных соединений //Дефектоскопия. -1997. № 12. — С.33−42.
- Зуев В.М. К вопросу оценки выявляемости дефектов при радиографическом контроле сварных соединений // Дефектоскопия. -2001.-№ 3. С.64−74.
- Орлов А.И. Всегда ли нужен контроль качества продукции? // Заводская лаборатория. Диагностика материалов. 1999. — № 11. — С. 51−55
- СТП, А 248−90 Металлоконструкции сварные. Общие технические требования: Утв. 08.08.90: Введ. в действие с 01.01.91. Екатеринбург: ОАО «Уралмаш», 1991. — 80 с.
- СниП 3.05.05−84. Технологическое оборудование и технологические трубопроводы: Утв. Госстроем СССР 07.05.84: Введ. в действие с 01.01.85. М.: ЦИТП Госстроя СССР, 1988. — 32 с.
- Румянцев C.B. Радиационная дефектоскопия. М.: Атомиздат, 1974.560 с.
- Зуев В.М. Фотометрическая оценка размеров дефектов в направлении просвечивания // Дефектоскопия. -1993. -№ 5. С.87−93.
- Зуев В.М. Оценка размера дефектов малого раскрытия в направлении просвечивания // Дефектоскопия 2000. — № 7. — С.63−68.
- Арефьев М.Г., Каксис Ю. А., Маклашевский В .Я. Разработка алгоритма реконструкции томографического изображения для повышения точности определения дефектов и снижения затрат на проведение контроля // Контроль, Диагностика. 1999. — № 8. — С. 23−27.
- Клюев В.В., Филинов В. Н. О работах МНПО «Спектр» в области рентгеновской компьютерной томографии // Контроль. Диагностика.1999.-№ 5.-С. 35−40.
- Юмашев В.М., Кузелев Н. Р., Маклашевский В .Я. Комплексный радиационный контроль изделий, слоистых и композитных материале в промышленности, авиационной и космической технике // Контроль. Диагностика. 2001. — № 5. — С. 35−36.
- Межуев В.А. и др. Рентгенотелевизионный контроль- сварных швов TBC для ядерных реакторов // В мире неразрушающего контроля.2000.- № 4.-С. 41−43.
- Дмоховский В.В. Основы рентгенотехники. М.: Медгиз, 1960. — 352 с.
- Зуев В.М. Влияние рассеянного излучения на формирование радиографических изображений // Дефектоскопия -1997. -№ 12. С.25−32.
- Соколов B.C. Дефектоскопия материалов. M.-JI.: Государственное энергетическое издательство, 1957. — 240 с.
- Круглова Е.В., Князюк JI.B. Определение размеров дефектов сварных соединений по сканированным рентгеновским снимкам // Дефектоскопия. 2004. — № 1. — С .71 -75.
- Е. Krouglova, L. Knyzuk, V. Kortov: MATHEMATICAL MODELING AT
- ACCOUNT of PARAMETERS of INCOMPLETE FUSION of a WELD, Third International Conference on Mathematical Modeling and Computer Simulation of Material Technologies MMT-2004, Ariel, Israel, 2004, p.2−105 T -2−111.
- Корн Г., Корн Т. Справочник по математике для научных работников и инженеров. М.: Наука, 1970. — 720 с.
- Кассандрова О.Н., Лебедев В. В. Обработка результатов измерений. -М.: Наука, 1970.- 104 с.
- Круглова Е.В., Князюк Л. В., Кортов B.C. Определение размеров непровара по сечению сварного шва при радиографическом контроле // Дефектоскопия. 2005. — № 4. — С. 63−69.
- Соснин Ф.Р. Неразрушающий контроль: Справочник: В 7 т. Под общ. ред. В. В. Клюева. Т. 1: В 2 кн.: Кн.1: Визуальный и измерительныйф контроль. Кн. 2: Радиационный контроль. М.: Машиностроение, 2003.- 560 с.
- Способ определения глубины залегания малоконтрастного дефекта при радиографическом контроле/Л.В. Князюк, Е. В. Круглова. Заявка на изобретение № 2 003 117 860/28- Заявл. 16.06.03- Опубл. 20.02.05. — Бюл. № 5.
- Круглова Е.В. Экономическая эффективность внедрения метода расчета глубины дефекта при радиографическом контроле. //Современные проблемы сварочного производства: сборник тезисов докладов научно-технической конференции. Екатеринбург, 2004. С. 55−56.
- Клюев В.В., Соснин Ф. Р. Современные средства и методы цифровой ^ радиационной дефектоскопии // В мире неразрушающего контроля.2002. = № 4. С.52−56.