Исследование технологических особенностей производства деформированием двухкомпонентных автомобильных колес из алюминиевых сплавов
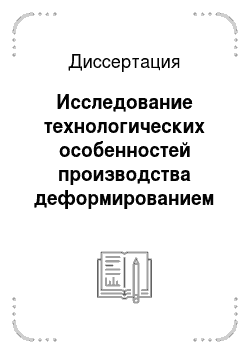
Диссертация
Осадка предварительно прессованных заготовок размером D3 к L3 = 150 к 230 мм с получением поковки диаметром ~ 340 мм и высотой 40 мм при toc = 420 — 400 °C => штамповка в два перехода при такой же температуре и смазке: смесь графита с маслом ВАПОР-Т (1:2). При окончательной штамповке детали расчетная величина усилия не должна превышать 80% предельного усилия пресса,. А конструкция штампа должна… Читать ещё >
Содержание
- Страница
- Глава 1. Современное состояние производства дисков автомобильных колес из алюминиевых сплавов
- 1. 1. Способы получения дисков из легких сплавов методами пластической деформации
- 1. 2. Основные тенденции развития процессов
- 1. 3. Задачи повышения эффективности производства
- 1. 4. Выводы
- Глава 2. Разработка конструкции, выбор материала, оборудования и методы экспериментальных исследований процессов пластического формоизменения деталей двухкомпонентных колес .,
- 2. 1. Разработка конструкции двухкомпонентного колеса
- 2. 2. Выбор материала колес
- 2. 3. Оборудование
- 2. 3. 1. Выплавка исходного металла
- 2. 3. 2. Прессовое оборудование для предварительной деформации
- 2. 3. 3. Штамповочное оборудование
- 2. 4. Исследование параметров деформации изделий
- 2. 5. Выводы
- Глава 3. Исследование и разработка технологических режимов производства ступицы
- 3. 1. Исследование, разработка режимов деформации
- 3. 2. Расчет усилий штамповки
- 3. 3. Основная технологическая схема
- 3. 4. Механическая обработка дисков
- 3. 5. Исследование качества изделий
- 3. 6. Выводы
- Глава 4. Исследование основных технологических операций процесса раскатки обода колеса
- 4. 1. Оборудование и средства осуществления процесса
- 4. 2. Ротационная раскатка обода
- 4. 2. 1. Исходные положения
- 4. 2. 2. Программное обеспечение
- 4. 2. 3. Расчет размеров заготовки
- 4. 2. 4. Дефекты при ротационной раскатке
- 4. 3. Основные технологические и сборочные операции
- 4. 4. Исследования свойств, структуры, другие испытания
- 4. 5. Выводы
- Глава 5. Разработка промышленной технологии производства и оценка надежности при эксплуатации двухкомпонентных колес
- 5. 1. Разработка технологического процесса
- 5. 2. Схема исследования и действующие нагрузки
- 5. 3. Расчет нагрузок для схемы нагружения
- 5. 4. Расчет нагрузок для схемы нагружения
- 5. 5. Построение расчетной модели
- 5. 6. Анализ результатов моделирования
- 5. 7. Выводы
- 5. 8. Перспективы развития процесса
Список литературы
- Мельников В.В., Белов В. Д. Особенности изготовления дисков автомобильных колес из силумина литьем под низким давлением // Литейное производство, 1994, № 4, с. 21 23.
- Каковин В.М., Никонов Е. В. Способ изготовления кольцевых поковок // АС 1 780 913 А1, бюллетень изобретений, № 46, 1992. Каковин В. М., Никонов Е. В. Способ изготовления кольцевых поковок // Патент 95 100 874, бюллетень изобретений, № 31, 1996.
- Aluminium + Automobile. Lect. Intern. Simp. (Dusseldorf, 1980), p. 18/1, Dusseldorf, Ali-Veri (1981)/
- Spath W. Automobiltechn. Z, 88, № 10, s*. 557 (1986).
- Karida M.A. Eifert C.T. SAE Techn. Pap. Ser, # 841 694, p. 1 (19 840.
- Справочник по алюминиевым сплавам, ВИЛС, 1978.
- Изобретено колесо // Автомобильная промышленность США, 1996, № 4/5, с. 30−31.
- KS6161 алюминиевый сплав для автомобильных колес, имеющий высокую прочность // Nakai Manabu, Hirano Masakazu // Кобэ сейко гихо = Коте Steel Eng. Repts, 1992, 42, № 26 с. 134 — Япон.// Реф.: РЖ Металлургия, 1992, 10И433.
- Изготовление автомобильных колес из легких сплавов // Zerres Eberhard // Maschinenmarkt 1994 — 100, № 45, с. 8 — Нем.
- В центре внимания автомобильной промышленности производство деталей из алюминия // Metallurgia- 1993 60, № 11, с. 376 — Англ. Реф.: РЖ Металлургия, 1995, 1Д148.
- Использование алюминия в автомобильных конструкциях // Advanced Materials and Processes 1996 — V. 149, № 5, P. 29 -30. Реф.: Технология легких сплавов, 1997, № 1, с. 68 — 69.
- Южная Корея: потребность в алюминии для изготовления ободов автомобильных колес возрастает // Aluminium -1991 67, № 9, с. 842 — 843. -Нем. Реф.: РЖ Металлургия, 1992, 2Г13.
- Автоматическая обработка алюминиевых колес // Tool/ and Prod 1994 -59, № 11, с. 25. — Англ. Реф.: РЖ Технология машиностроения, 1994, 10Б176.
- Способ изготовления автомобильных колес: Заявка 680 794 ЕПВ: МКИ В 21 D-53/30- Опубл. 8.11.95. Реф.: РЖ Технология машиностроения, 1997, ЗВ74П.
- Термообработка деталей автомобильного назначения, выполненных из высокопрочных легких сплавов // Е. Morbitzer || Aluminium 1995 — Т. 71, № 4, с. 438−439.
- Термическая обработка и механические свойства алюминиевого литейного сплава А356 // Takaai Tetsuya, Nakayama Yoshihiro, Koga Masaaki и др. // Met. Abstr. Lighf Metals and Alloys, Vol. 27. (1993 1994) — Osaka, 1994-c. 130-Англ. Реф.: 1996, 1И517.
- Степанский Л.Г. Расчеты процессов обработки металлов давление // М., Машиностроение, 1979, 213 с.
- Шофман J1.A. Основы расчета процессов штамповки и прессования // М, Машгиз, 1961, 340 с.
- Сторожев М.В., Попов Е. А. Теория обработки металлов давлением // М., Машиностроение, 1979, 215 с. i Tokado К., Fukudo A. Biger Aluminium Forgings by Koba. American Machinist, Juby, 1984, p/ 99 — 103.
- Barbazanges J. Hes nou veces possibilites offertes par d’Interforge Annales des mimes, Jan vur, 1979, p. 55 — 62.
- Браславский В.М. Технология обкатки крупных деталей роликами // Машиностроение, М., 1966, 158 с.
- Изготовление обечаек ротационной вытяжкой на станках типа СРГ, производственная инструкция, НИАТ, 1990, 32 с.
- Проектирование технологических процессов автоматизированной ротационной вытяжки на токарных станках, оснащение ЧПУ // Руководящий технологический материал, НИАТ, 1988, 56 с. Ansys user’s manual for revision 5.3. T 1−4. 1995.
- Зенкевич О. Метод конечных элементов в технике. Пер. с англ. Под. ред. Б. Е. Победри // М., Мир, 1975, 541 с.
- Бидерман В.Л. Механика тонкостенных конструкций // М., Машиностроение, 1977, 488 с.127
- Цукерберг С.М. и др. Пневматические шины. // М., Химия, 1973, 264 с. Корнев М. В. Батурин А.И. Оценка напряженно-деформированного состояния двухкомпонентного алюминиевого автомобильного колеса // Технология легких сплавов, № 3, 2000 г., с. 31 36.
- СИСТЕМА СЕРТИФИКАЦИИ ГОСТ Р ГР С СТ АН ДАРТ Р О С С И ИеЕШГИ ФИ КАТЮООШЕТеТВ и я
- СТВУЕТ ТРЕБОВ^ЙЯМ' НОРМАТИВНЫ^ Й®-0511 ж&г-.-.•>•*.-.?-г.'' *. • -. к- ¦ код ТН ВЭД СНГ: рсковская обл.^г. Ступ и н о, ул.' Л р и ста н ци о н н ая, 19, РФ уу:-' ^
- КАТ вь1д^^^ у .¦-.¦•¦¦/'¦•¦¦¦'. -
- Генеральный директор ЗАО «СМК"1. Щ/ / / А.В.Степанов
- Технический акт промышленного внедрения
- Работа выполнялась по разработанным технологиям производства рмической обработки.
- На основании протокола испытаний № 17−00 от 19.04.2000 г. на ко) 5. х1 ЗН2 органом по сертификации ИЦ-НИЦИАМТ выдан сертифи-зоответствия № РОСС RU. MT25.B01859.
- Мы всегда готовы идти навстречу пожеланиям ¦ заказчика. Для заказа колес, не указанных в каталоге, м ,