Определение допусков и посадок в различных системах
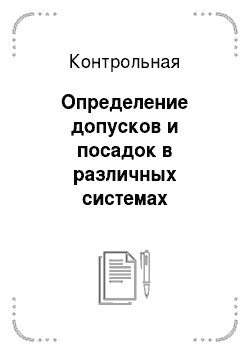
Ec (А?зам)= ?Ec (Аi ув) — ?Ec (Аi ум)=(+0.037+0.031)-(-0.0125*2−0.037)=+0.130 мм Полученное поле допуска замыкающего звена не соответствует исходному полю допуска, А? исх, но принимается в качестве базового. Полученные допуски на размеры составляющих звеньев должны удовлетворять выражению: ТА ??? ТА i. Отсюда, при сравнении ТА? = 0,300 мм с? ТА i = 0,260 мм можно заключить, что размерная цепь… Читать ещё >
Определение допусков и посадок в различных системах (реферат, курсовая, диплом, контрольная)
посадка допуск квалитет точности Целью данной расчетно-графической работы является закрепление теоретических знаний и практических навыков, необходимых при расчете допусков, посадок, квалитетов точности для узлов и деталей машин.
Для выполнения работы необходимо научиться пользоваться справочной литературой, стандартами, используемыми при производстве измерений деталей машин.
Предметом изучения в данной работе являются: гладкие цилиндрические соединения, подшипники качения и размерные цепи.
Задание № 1
1. Записать условное и числовое значение посадки в виде дроби;
2. Определить систему, в которой выполняется сопряжение, тип посадки, квалитет точности исполнения деталей" .
3. По таблицам СТ СЭВ 144−75 определить предельные отклонения размеров вала и отверстия, допуски на изготовление.
4. Рассчитать наибольшие, наименьшие и средние зазоры или натяги, допуски посадок с проверкой результата по допускам на размеры отверстия и вала;
5. В произвольно выбранном масштабе построить схемы полей допусков деталей и привести основные характеристики сопряжений.
6. Вычертить эскизы деталей с обозначениями допусков на изготовление.
Решение
1.1 Расчет посадки с зазором Условное обозначение заданного гладкого цилиндрического соединения O 3 H11/d11.
Данное соединение выполняется в системе отверстия (так как основное отклонение H относится к отверстию). Исходя из данных таблицы 1.16, 1.27, 1.28 [1], определяем, что указанное соединение формируется по посадке с зазором (так как поле допуска вала d11 располагается ниже нулевой линии), а поле допуска отверстия находится выше поля допуска вала.
Предельное отклонение размеров:
отверстия O 3 H11, EI = 0; ЕS = +75 мкм вала O 3 d11, ei = -105 мкм; es = -30 мкм Предельные размеры и допуски на изготовление:
отверстия D max = D + ES =3,0 + 0,075 = 3,075 мм
D min = D + EI = 3,0- 0 = 3,0 мм
TD = D max — D min = 3,075- 3,0 = 0,075 мм вала d max = d + es =3,0 — 0,030 = 2,970 мм
d min = d + ei = 3,0 — 0,105= 2,895 мм
Td = d max — d min = 2,970 — 2,895= 0,075 мм Величины предельных зазоров
S max = D max — d min = 3,075 — 2,895 = 0,180 мм
S min = D min — d max = 3,0 — 2,970 =0,030 мм Средний зазор S m = (S max + S min) / 2 = (0,180 + 0,030) / 2 = 0,105 мм Допуски посадки Т s = S max — S min = 0,180 — 0,030 = 0,150 мм или Т s = TD + Td = 0,075 + 0,075 = 0,150 мм По полученным данным строим схему расположения полей допусков гладкого цилиндрического соединения:
Рис. 1 Основные характеристики сопряжения O 3 H11 / d11 (посадка с зазором).а) схема расположения полей допусков
1.2 Расчет посадки с натягом Условные обозначения соединения O250 S7 / h6
Данное сопряжение выполняется в системе вала (так как основное отклонение h относится к валу). По данным, изложенным в материалах [1], определяем, что соединение выполняется по посадке с натягом, так как поле допуска отверстия S7 находится ниже поля допуска вала h6.
Предельное отклонение размеров:
отверстия O 250 S7, EI = -190 мкм; ЕS = -138 мкм вала O 250 h6, es = 0; ei = -32 мкм Предельные размеры и допуски на изготовление:
отверстия D max = D + ES = 250,0−0,138=249,862 мм
D min = D + EI = 250,0−0,190=249,810 мм
TD = D max — D min = 249,862 — 249,810 =0,052 мм вала d max = d + es = 250,0+0=250,0 мм
d min = d + ei =250,0−0,032=249,968 мм
Td = d max — d min = 250,0 — 249,968 =0,032 мм Величины предельных натягов:
N max = d max — D min = 250,0 — 249,810 =0,190 мм
N min = d min — D max = 249,968 — 249,862 = 0,106 мм
Средний натяг N m = (N max + N min) / 2 =(0,190 +0,106) / 2 = 0,148 мм Допуски посадки Т N = N max -N min = 0,190 -0,106 =0,084 мм или Т N = TD + Td = 0,052 +0,032 =0,084 мм По полученным данным строим схему расположения полей допусков гладкого цилиндрического соединения Рис. 2 Основные характеристики сопряжения O 250 S7 / h6 (посадка с натягом).а). схема расположения полей допусков
1.3 Расчет посадки переходной Условное обозначение соединения O24 M6 / h5.
Данное сопряжение выполняется в системе вала (т.к. h — основное отклонение вала) по 6 квалитету для отверстия и по 5 квалитету для вала. По данным, изложенным в материале[1], определяем, что соединение выполняется по переходной посадке, т.к. поле допуска вала h5 относится к группе переходных посадок.
Предельные отклонения размеров:
отверстия O 24 M6, ES = - 4 мкм; EI = -17 мкм вала O 24 h5 es = 0; ei = -9 мкм Предельные размеры и допуски на изготовление отверстия D max = D +ES = 24,0−0,004=23,996 мм
D min = D + EI = 24,0−0,017=23,983 мм
TD = D max — D min = 23,996 — 23,983 =0,013 мм
— вала d max = d + es = 24,0 + 0=24,0 мм
d min = d + ei = 24,0−0,009 = 23,991 мм
Td = d max — d min =24,0−23,991 =0,009 мм Величины предельных зазоров и натягов:
S max = D max — d min = 23,996 — 23,991 =0,005 мм
N max = d max — D min = 24,0 — 23,983 =0,017 мм Средний натяг N c = e c — E c
где e c = (es + ei) / 2 = (0 — 0,009) / 2 = -0,0045 мм = -4,5 мкм
E c = (ES + EI) / 2 = (-0,004 -0,017) / 2 = -0,0105 мм = -10,5 мкм Отсюда N c = -0,0045+0,0105= +0,0060 мм Допуск посадки:
T N (T S) = N max — N min = N max — (- S max) = 0,017 — (-0,005)=0,022 мм
или T N (T S) = TD + Td = 0,013 + 0,009 = 0,022 мм По полученным данным строим схему расположения полей допусков соединения:
Рис. 3 Основные характеристики сопряжения O 24 M6 / h5 (посадка переходная) а). схема расположения полей допусков
Расчет посадок для подшипников качения
Для подшипника качения, работающего в опоре вала редуктора необходимо установить параметры сопряжения с деталями редуктора. Для этого требуется:
1. По материалам ГОСТ 3325– — 55 и СТ СЭВ 773 — 77, изложенным в технической литературе [2, 3], определить вид нагружения наружного и внутреннего колец подшипника и вычертить соответствующие схемы нагружения;
2. Для кольца, имеющего циркуляционное нагружение, рассчитать интенсивность нагрузки на посадочную поверхность детали редуктора. По полученным, а также исходным данным, определить квалитеты сопрягаемых деталей (вала и отверстия в корпусе редуктора) и назначить посадки для обоих колец подшипника;
3. Рассчитать предельные размеры посадочных поверхностей вала и отверстия в корпусе редуктора, а также обоих колец;
4. Рассчитать допуски размеров и посадок соответствующих поверхностей, определить зазоры или натяги в соединениях;
5. Вычертить эскизы полей допусков полученных сопряжений с нанесением основных характеристик;
6. Произвести проверку подшипника на наличие рабочего зазора; при необходимости произвести корректировку по посадке соответствующего кольца.
Решение
Определить посадку наружного и внутреннего колец подшипника в корпус и на вал редуктора при следующих данных (см. рис.1):
— диаметр наружного кольца D = 215 мм
— диаметр внутреннего кольца d = 120 мм
— ширина подшипника B = 40 мм
— класс точности подшипника 0
— радиальные реакции в опорах R 1 = R 2 = R = 35 кН
— характер нагрузки с сильными толчками. Перегрузка до 300%
В соответствии с условиями работы подшипника в качестве опоры вала в редуктора определяем, что вращающееся вместе с валом внутреннего кольца подшипника испытывает при постоянно направленной радиальной нагрузке R1 циркуляционное нагружение, а наружное кольцо, не вращающееся относительно радиальной нагрузки, испытывает местное нагружение.
а) Циркуляционное нагружение б) Местное нагружение
Рис 1. Схемы нагружения колец подшипника
Посадку внутреннего кольца определяем по интенсивности нагрузки, рассчитываемой по формуле:
p R = k 1 * k 2 * k 3 *R1/B
где R 1 = R 2 = R = 35 кН — радиальная нагрузка на опору;
k 1 — коэффициент характера нагрузки.
Для нагрузки с сильными толчками принимаем
k 1 =1,8 (табл. П 39,)
k 2 — коэффициент характера конструкции.
Для жесткого корпуса редуктора и сплошного вала принимаем
k 2 = 1,0 (табл. П 40, [ 4 ])
k 3 — коэффициент неравномерности распределения радиальной нагрузки между рядами в подшипниках.
Для однорядных подшипников принимаем
k 3 = 1,0 (табл. П 40,[ 4 ])
p R = ((35 000/40)* 1,8 * 1,0 * 1,0) = 1575 Н / мм
В соответствии с данными табл. 4.92 принимаем для внутреннего кольца подшипника посадку сопряжения с валом, выполненным по полю допуска вала k 6.
Для наружного кольца, испытывающего местное нагружение при динамической перегрузке, принимаем сопряжение отверстием в неразъемном корпусе, выполненным по полю допуска отверстия H7. (табл. 4.89 [2])
Находим предельные отклонения и размеры
а) вала O 120 k 6, где es = + 28 мкм; ei = + 3 мкм. (табл. 1.28 [1])
Отсюда d max = d + es =120,0 + 0,028 = 120,028 мм
d min = d + ei =120,0 + 0,003 =120,003 мм
Td = es — ei = 0,028 — 0,003 = 0,025 мм.
б) отверстия в корпусе O 215 H7, где ES = +46 мкм, EI = 0 (табл. 1.36 [1])
D max = D + ES = 215,0 + 0,046 = 215,046 мм
D min = D + EI = 215,0 +0 = 215,0 мм
TD = ES — EI =0,046 — 0 = 0,046 мм.
Находим предельные отклонения и размеры подшипника.
а) внутреннего кольца O120, класс точности 0, для которого
ES = 0, EI = - 25мкм. (табл. 4.82)
Отсюда D п max = D + ES =120,0 + 0 =120,0 мм
D п min = D + EI =120,0 — 0,025 = 119,975 мм
TD п = D п max — D п min = ES — EI = 0 — (- 25) = 0,025 мм
б) наружнего кольца O 215, класс точности 0, для которого
es = 0, ei = - 30 мкм. (табл. 4.83 [2])
Отсюда d п max = d + es = 215,0 + 0 = 215,0 мм
d п min = d + ei = 215,0 — 0,030 =214,970 мм
Td п = d п max — d п min = es — ei = 0 — (- 30) = 30 мкм = 0,030 мм
Определяем параметры сопряжений
а) внутреннее кольцо подшипника — вал
N max = d max — D п min =120,028 — 119,975 = 0,053 мм
N min = d min — D п max =120,003 — 120,0 = 0,003 мм
T N = N max — N min = 0,053 — 0,003 = 0,050 мм
б) наружное кольцо подшипника — корпус
S max = D max — d п min = 215,046 — 214,970 = 0,076 мм
S min = D min — d п max = 215,0 — 215,0 = 0 мм
T s = S max — S min = 0,076 — 0 = 0,076 мм
По полученным данным строим схему расположения полей допусков деталей с основными характеристиками соединения
Рис. 2. Схема расположения полей допусков подшипникового узла.
Определяем посадочный (рабочий) зазор в подшипнике
Радиальный посадочный зазор в подшипнике после его установки на вал по посадке k6 определяется как g п =g н ср — ?d 1 max ,
где g н ср — средний начальный зазор в подшипнике;
g н ср = 0.5 * (g н max + g н min)
Исходя из данных приложения IX [3], имеем для радиального однорядного
роликого подшипника с цилиндрическим отверстием:
g н max = 115 мкм, g н min = 45 мкм
Отсюда g н ср = 0.5 * (115 + 45) = 80 мкм
?d 1 max — диаметральная деформация беговой дорожки внутреннего кольца после посадки
? d1 max = N эф * (d / d 0),
где N эф = 0,85 * N max — эффективный натяг в посадке
N max = 53 мкм — максимальный натяг в посадке
d = 120 мм — номинальный диаметр внутреннего кольца
d 0 =d + (D — d) / 4 — приведенный диаметр внутреннего кольца
В нашем случае d 0 =120,0 + (215,0 -120,0) / 4 = 143,75 мм
N эф = 0,85 * 53 = 45,05 мкм
?d 1 max = 45,05 * (120,0 / 143,75) = 37,6 мкм
Тогда радиальный посадочный зазор составит
g п = 80,0 — 37,6 = + 42,4 мкм
Из полученных данных следует, что радиальный зазор сохраняется (это необходимо для нормальной работы подшипника). Следовательно, тип подшипника выбран верно.
Расчет размерной цепи
В соответствии с заданным эскизом узла редуктора и номинальными размерами его элементов выполнить проектный расчет размерной цепи методом полной взаимозаменяемости, для чего необходимо:
1. Определить все составляющие звенья размерной цепи во взаимосвязи с заданным исходным (замыкающим) звеном;
2. Построить схему размерной цепи с указанием номинальных размеров звеньев и определить характер составляющих звеньев (увеличивающие, уменьшающие);
3. По способу допусков одного квалитета определить средний квалитет составляющих звеньев размерной цепи;
4. С использованием принципа максимума — минимума по заданным предельным отклонениям исходного звена рассчитать допуски и предельные отклонения размеров составляющих звеньев;
5. Провести проверку полученного результата по уровню допуска на замыкающее звено как суммы допусков составляющих звеньев и сравнение его с заданным допуском. При необходимости произвести корректировку допусков составляющих звеньев и вновь произвести проверку.
Решение Исходные данные:
А 1 = 52 мм, А 2 = 30 мм, А 3 = 3,0 мм, А 4 = 75 ммисходные размеры звеньев.
ES(А ?) = 0 мкм, EI (А ?) = -300мкмпредельные отклонения исходного звена.
Согласно рисунку и исходным данным строим схему размерной цепи узла редуктора.
Исходя из полученной величины, а ср, по таблицам устанавливаем соответствие
а ср = 47 единиц 9 квалитету для размеров составляющих звеньев и допуски на них,
а именно:
А 1 = 52 +0,074 мм, А 2 = 30 +0,062 мм — для увеличивающих звеньев
(охватывающие размеры) и для поля допуска основного отверстия.
А 3 = 3,0 -0,025 мм, А 4 = 75 -0,074 мм — для уменьшающих звеньев
(охватываемые размеры) и для поля допуска основного вала.
По полученным данным выполняем проверочный расчёт цепи :
? ТА i = 0,074 + 0,062 + 2 * 0,025 + 0,074 = 0,260 мм
Определяем предельные и средние величины отклонений поля допуска, А ?зам
Верхнее предельное отклонение:
ES (А ?зам)= ?ES (А i ув) — ?EY (А i ум)=(+0.074+0.062)-(-0.025*2−0.074)=+0.260 мм Нижнее предельное отклонение:
EY (А ?зам)= ?EY (А i ув) — ?ES (А i ум)=(+0+0)-(0+0+0)=0
Координаты Ec середины поля допуска:
Ec (А?зам)= ?Ec (Аi ув) — ?Ec (Аi ум)=(+0.037+0.031)-(-0.0125*2−0.037)=+0.130 мм Полученное поле допуска замыкающего звена не соответствует исходному полю допуска, А ? исх, но принимается в качестве базового. Полученные допуски на размеры составляющих звеньев должны удовлетворять выражению: ТА ?? ? ТА i. Отсюда, при сравнении ТА ? = 0,300 мм с? ТА i = 0,260 мм можно заключить, что размерная цепь решена правильно, а узел редуктора будет работоспособен после сборки и в процессе эксплуатации.
Рис. Схема размерной цепи
Заключение
В результате выполнения данной расчетно-графической работы были закреплены и использованы на практике теоретические положения по дисциплине «Метрология, стандартизация и сертификация». В ходе выполнения работы применялась справочная литература и стандарты.
Выполнение заданий по расчету и анализу допусков, посадок, квалитетов точности, а также определению видов нагружения наружного и внутреннего колец подшипника и расчету составляющих звеньев цепи для узлов и деталей машин позволило на практике закрепить полученные практические навыки и теоретические знания.
Допуски и посадки. Справочник под ред. Мягкова В. Д. и др. (часть 1). — М.: Машиностроение, 1982. — 544 с.
Допуски и посадки. Справочник под ред. Мягкова В. Д. и др. (часть 2). — М.: Машиностроение, 1982. — 448 с.
Зябрева Н.Н. и др. Пособие к решению задач по курсу «Взаимозаменяемость, стандартизация и технические измерения». Учебное пособие для вузов. М.: Высшая школа, 1977. — 204 с.
Козловский Н.С., Ключников В. М. Сборник примеров и задач. — М.: Машиностроение, 1983. — 304 с.
Юдин В. Н. Методические указания по выполнению расчетно-графической работы по дисциплине «Метрология, стандартизация и сертификация». — Коломна: КИ МГОУ, 2001. — 45 с.
6.Якушев А. И. и др. Взаимозаменяемость, стандартизация и технические измерения. — М.: Машиностроение, 1987. — 352 с.