Разработка на основе метода конечных элементов модели и способа управления траекторией рабочего движения инструмента при фрезеровании сложнопрофильных деталей: на примере лопаток компрессора ГТД
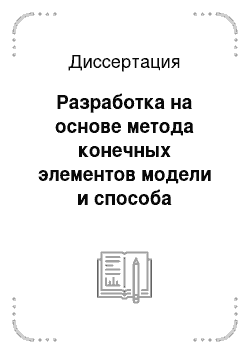
Диссертация
Изучение работ по теории резания также показало актуальность проведенных автором исследований по изучению влияния углов наклона и атаки на величину деформаций и перемещений участков фрезеруемой заготовки. Разработанная конечно-элементная модель процесса фрезерной обработки учитывает режимы резания, геометрию инструмента, характеристики материала заготовки, съем припуска и позволяет рассчитывать… Читать ещё >
Содержание
- УСЛОВНЫЕ ОБОЗНАЧЕНИЯ
- 1. СОСТОЯНИЕ ВОПРОСА. РАЗРАБОТКА МОДЕЛИ КОНЦЕВОГО ФРЕЗЕРОВАНИЯ, УЧИТЫВАЮЩЕЙ ПРОСТРАНСТВЕННЫЕ ИСКАЖЕНИЯ СЛОЖНОПРОФИЛЬНОЙ ДЕТАЛИ ОТ СИЛ РЕЗАНИЯ
- 1. 1. Значение фрезерных работ при лезвийной обработке лопаток ГТД
- 1. 2. Технологические особенности изготовления лопаток компрессора ГТД
- 1. 3. Погрешности, возникающие в процессе фрезерной обработки лопатки компрессора ГТД
- 1. 3. 1. Погрешность, обусловленная деформацией детали от сил резания
- 1. 3. 2. Погрешность, обусловленная деформацией детали от сил закрепления
- 1. 3. 3. Погрешность из-за вибраций, возникающих в процессе обработки
- 1. 4. Анализ ранее выполненных работ по теоретическому и экспериментальному определению напряженно-деформированного состояния обрабатываемой детали и моделированию лезвийной обработки с помощью МКЭ
- 1. 4. 1. Обзор работ, посвященных моделированию процессов лезвийной обработки
- 1. 4. 2. Некоторые особенности моделирования процессов лезвийной обработки с помощью МКЭ
- 1. 4. 3. Достоверность конечно-элементной модели резания
- 1. 4. 4. Обзор работ по расчету напряженно-деформированного состояния в зоне резания аналитическими и эмпирическими методами
- 1. 5. Концепция автоматизированной системы на основе МКЭ для обработки деталей ГТД гипа «лопатка» и ее место в технологической подготовке производства
- 1. 6. Выводы по главе 1. Цели и задачи исследования
- 2. МАТЕМАТИЧЕСКАЯ МОДЕЛЬ ОПРЕДЕЛЕНИЯ НАПРЯЖЕННО-ДЕФОРМИРОВАННОГО СОСТОЯНИЯ ОБРАБАТЫВАЕМОЙ ДЕТАЛИ И СИЛ РЕЗАНИЯ ПРИ КОНЦЕВОМ ФРЕЗЕРОВАНИИ
- 2. 1. Допущения, принятые в данной работе
- 2. 2. Математическое обеспечение расчета напряженно-деформированного состояния концевого фрезерования заготовки
- 2. 3. Описание поведения материала за пределами упругости
- 2. 4. Реализация механизма разделения материала
- 2. 5. Модель режущего инструмента, применяемая в расчете
- 2. 6. Моделирование движения инструмента при многоосевой обработке
- 2. 7. Моделирование контактного взаимодействия инструмента и заготовки
- 2. 8. Определение сил резания
- 2. 9. Теоретическая реализация метода компенсации неравномерного удаления припуска при фрезерной обработке на основе конечно-элементной модели фрезерования
- 2. 10. Характер влияния силы резания на величину прогибов заготовки при многоосевой обработке
- 2. 11. Выводы по главе 2
- 3. ЭКСПЕРИМЕНТАЛЬНАЯ ПРОВЕРКА АДЕКВАТНОСТИ МОДЕЛИРОВАНИЯ ФРЕЗЕРОВАНИЯ И ПРОГРАММНОГО ОБЕСПЕЧЕНИЯ. ЭКСПЕРИМЕНТАЛЬНОЕ ОПРЕДЕЛЕНИЕ ВЛИЯНИЯ УГЛОВ НАКЛОНА И АТАКИ НА ПРОЕКЦИИ СИЛЫ РЕЗАНИЯ
- 3. 1. Методика проведения экспериментов
- 3. 2. Описание хода экспериментов и анализ результатов
- 3. 2. 1. Определение деформаций и напряжений, возникающих в результате фрезерной обработки
- 3. 2. 1. 1. Описание экспериментальной установки и план эксперимента
- 3. 2. 1. 2. Анализ результатов эксперимента
- 3. 2. 2. Определение сил резания
- 3. 2. 2. 1. Описание экспериментальной установки и план эксперимента
- 3. 2. 2. 2. Общий анализ и результаты экспериментов
- 3. 2. 3. Построение расчетной обобщенной кривой по диаграмме растяжения для материала ВТЗ
- 3. 2. 4. Верификация программы
- 3. 2. 1. Определение деформаций и напряжений, возникающих в результате фрезерной обработки
- 3. 3. Выводы по главе 3
- 4. ПРАКТИЧЕСКАЯ РЕАЛИЗАЦИЯ РЕЗУЛЬТАТОВ ИССЛЕДОВАНИЯ
- 4. 1. Применение программного обеспечения на основе метода конечных элементов для моделирования многокоординатного фрезерования сложнопрофильных деталей
- 4. 2. Формирование исходных данных расчета
- 4. 3. Метод уточнения сетки в заданной области
- 4. 4. Проведение расчета
- 4. 5. Компенсация траектории рабочего движения инструмента
- 4. 6. Выводы по главе 4
Список литературы
- А. с. 1 399 074 СССР, МКИ3 В 23 Q 15/12. Способ автоматического управления процессом обработки Текст. / В. Ф. Безъязычный, Т. Д. Кожина, Д.
- A. Туманов (СССР). № 4 091 441/31−08, заявл. 14.07.86 — опубл. 30.05.88, Бюл.20 2 с.
- Безъязычный, В.Ф. Автоматизация технологии изготовления газотурбинных авиационных двигателей Текст./ В. Ф. Безъязычный, В. Н. Крылов,
- B.А. Полетаев и др.- Под ред. В. Ф. Безъязычного и В. Н. Крылова. М.: Машиностроение, 2005. — 560 с.
- Безъязычный, В. Ф. Оптимизация технологических условий механической обработки деталей авиационных двигателей Текст./ В. Ф. Безъязычный, Т. Д. Кожина, А. В. Константинов [и др.]. -М.: Изд-во МАИ, 1993. 184 е.: ил.
- Белиничер, И. Ш. Улучшение качества поверхности при фрезеровании Текст. / И. Ш. Белиничер. М.: Машгиз, 1951
- Борискин, О. Ф. Автоматизированные системы расчета колебаний методом конечных элементов Текст. / О. Ф. Борискин. — Иркутск: Изд-во Иркут. унта, 1984.-188 с.
- Братухин, А. Г. Современные технологии в производстве газотурбинных двигателей Текст./ Под ред. А. Г. Братухина, Г. К. Язова, Б. Е. Карасева. М.: Машиностроение, 1997. — 416 е.: ил.
- Васин, С. А. Резание материалов: Термомеханический подход к системе взаимосвязей при резании Текст./ С. А. Васин, А. С. Верещака, В. С. Кушнер -М.: Изд-во МГТУ им. Н. Э. Баумана, 2001. 448 е.: ил.
- Вивденко, Ю. Н. Метод прогнозирования точности обработки нежестких деталей ГТД с учетом сил в технологических системах Текст./ Вивденко Ю. Н.,
- Карасев А. В.// Поверхность: Технологические аспекты прочности деталей/ Уфим. Гос. Авиац. Техн. ун-т. Уфа, 1996. — С. 113−118.
- Вивденко, Ю. Н. Технологические системы производства деталей наукоемкой техники Текст. / Ю. Н. Вивденко. М.: Машиностроение, 2006. — 559 е.: ил.
- Виноградов, Ю. В. Моделирование процесса резания металла методом конечных элементов Текст.: автореф. дис. .канд. техн. наук/ Виноградов Ю. В. -Тула, 2004. 19 с.
- Волошин, Д. А. Повышение эффективности процесса фрезерования концевыми фрезами на основе оптимизации траекторий формообразующих движений в пространстве состояний Текст.: дис. .канд. техн. наук/ Волошин Д. А. -Ростов-на-Дону: ДГТУ, 2003. 154 с.
- Гультяев, А. К. Matlab 5.2. Имитационное моделирование в среде Windows: Практическое пособие Текст. / А. К. Гультяев. — СПб.: КОРОНА принт, 1999. 288 с
- Гурин, В. Д. Исследование силовых параметров при фрезеровании концевыми фрезами для диагностирования их состояния Текст. / В. Д. Гурин, С. Н. Григорьев // Вестник машиностроения. 2005. — № 9. — С. 19−22.
- Денисов, С. Ю. Автоматизация технологической подготовки производства на ОАО «НПО „Сатурн“ Текст. / С. Ю. Денисов // Наука-производству: Материалы научно-практической конференции. Рыбинск: РГАТА, 2006.-С. 69−74.
- Дмитриев, А. М. Надежность метода конечных элементов Текст. / А. М. Дмитриев, A. JI. Воронцов // Справочник. Инженерный журнал. 2004. — № 6. -С. 13−22.
- Дьяконов, В, П. Matlab 6: Учебный курс Текст. / В. П. Дьяконов. -СПб.: Питер, 2001. 592 е.: ил.
- Емельянов, Ю. В. Повышение эффективности токарной обработки сложнопрофильных деталей на станках с ЧПУ путем назначения функционально функционально изменяемого режима резания Текст.: дис. .канд. техн. наук/ Емельянов Ю. В. Рыбинск: РГАТА, 2003. — 169 с.
- Ермаков, Ю. М. Комплексные способы эффективной обработки резанием: Библиотека технолога Текст. / Ю. М. Ермаков. М.: Машиностроение, 2003.-272 е.: ил.
- Жеманюк, П. Формообразование сложнопрофильных поверхностей моноколес высокоскоростным фрезерованием Текст. / П. Жеманюк, В. Мозговой [и др.] // Газотурбинные технологии. 2003. — № 5. — С. 18−21.
- Завод турбинных лопаток: Интеррос Электронный ресурс. Новости компаний от 09.07.2002. Режим доступа: www.interros.ru/news, свободный. — Загл. с экрана. Яз. рус., англ.
- Залога, В. А. О выборе уравнения состояния обрабатываемого материала для моделирования процесса резания методом конечных элементов Текст. / В. А. Залога, Д. В. Криворучко, С. Н. Хвостик // Вюник СумДУ. 2006. — № 12. — С. 101 115.
- Зенкевич, О. Метод конечных элементов в технике Текст. / О. Зенкевич: Пер. с англ. М.: Мир, 1975. — 544 е., ил.
- Зорев, Н. Н. Вопросы механики процесса резания металлов Текст. / Н. Н. Зорев. -М.: Машгиз, 1956.
- Ионов, В. Н. Динамика разрушения деформируемого тела Текст. / В. Н. Ионов, В. В. Селиванов. — М.: Машиностроение, 1987. 272 е., ил.
- Кабалдин, Ю. Г. Адаптивное управление технологическими системами механообработки на основе искусственного интеллекта Текст. / Ю. Г. Кабалдин, С. В. Серый, С. В. Биленко//Вестник машиностроения. 2004. — № 6. — С. 46−48.
- Кабалдин, Ю. Г. Управление динамическими свойствами технологических систем на основе нейросетевых моделей Текст. / Ю. Г. Кабалдин, С. В. Биленко, Н. А. Сердцев//Вестник машиностроения.-2002. № 7. — С. 38−41.
- Кондратов, А. П. Современные техпроцессы, оборудование и оснастка в механообработке деталей и узлов Текст. / А. П. Кондратов // Наука -производству: Материалы научно-практической конференции. — Рыбинск: РГАТА, 2006.-С. 162- 165.
- Косилова, А. Г. Точность обработки, заготовки и припуска в машиностроении Текст./ А. Г. Косилова, Р. К. Мещеряков, М. А. Калинин. М.: Машиностроение, 1976. 288 с.
- Крымов, В. В. Производство лопаток газотурбинных двигателей Текст./ В. В. Крымов, Ю. С. Елисеев, К. И. Зудин. М.: Машиностроение/ Машиностроение-Полет, 2002. 376 е., ил.
- Лицов, А. Е. Разработка расчетного метода определения технологических условий концевого фрезерования маложестких сложнопрофильных деталей с учетом их деформаций Текст.: дис. .канд. техн. наук/ Лицов А. Е. Рыбинск: РГАТА, 2005.- 185 с.
- Лоладзе, Т. Н. Стружкообразование при резании материалов Текст. / Т. Н. Лоладзе. М.: Машгиз, 1952. — 200 с.
- Малннин, Н. Н. Прикладная теория пластичности и ползучести Текст. / Н. Н. Малинин. — 2-е изд. перераб. и доп. М., „Машиностроение“, 1975. 400 е., ил.
- Марчук, Г. И. Методы вычислительной математики Текст. / Г. И. Марчук. -М.: Наука, 1977.
- Норри, Д. Введение в метод конечных элементов Текст. / Д. Норри, Ж. де Фриз: Пер. с англ. -М.: Мир, 1981. 304 е., ил.
- Ольхов, В. Е. Применение метода конечных элементов для САПР режущего инструмента с целью выбора геометрии токарных резцов Текст.: дис. .канд. техн. наук/ Ольхов В. Е. -Горький: ГПИ, 1987. 347 с.
- Остафьев, В. А. Расчет динамической прочности режущего инструмента Текст. / В. А. Остафьев. М.: Машиностроение, 1979. — 168 с.
- Остафьев, В. А. Физические основы процесса резания металлов Текст. / В. А. • Остафьев, И. П. Стабин, В. А. Румбешта и др. Киев: Вища школа, 1976. — 136 с.
- Панасенко, В. Особенности обработки деталей авиационных ГТД на станках с ЧПУ Текст. / В. Панасенко, С. Петров // Вестник двигателестроения. — 2005.-№ 1.-С. 138−144.
- Пашков, С. В. Численное моделирование фрагментации толстостенных цилиндрических оболочек при взрывном нагружении Текст.: дис. .канд. техн. наук/ Пашков С. В. Томск: ТГУ, 2000. — 120 с.
- Писаренко, Г. С. Деформирование и прочность материалов при сложном напряженном состоянии Текст. / Г. С. Писаренко, А. А. Лебедев. Киев: „Наукова думка“, 1976. — 416 с.
- Полетаев, В. А. Технологические базы лопаток компрессора газотурбинных двигателей Текст. / В. А. Полетаев // Справочник. Инженерный журнал.-2004. № 10.-С. 20−24.
- Полухин, П. И. Сопротивление пластической деформации металлов и сплавов Текст. / П. И. Полухин, Г. Я. Гун, А. М. Галкин. Справочник. М, „Металлургия“, 1983, с. 352.
- Пудов, А. В. Оптимизация режимов резания при обработке на станках с ЧПУ с целью повышения точности размеров и формы деталей в процессе точения Текст.: дис. .канд. техн. наук/ Пудов А. В. Рыбинск: РГАТА, 2000. — 186 с.
- Резников, А. Н. Теплофизика процессов механической обработки материалов Тескт. / А. Н. Резников. -М.: Машиностроение, 1981. 279 с. ил.
- Розин, JI. А. Основы метода конечных элементов в теории упругости Текст. / Л. А. Розин. Л., изд-во ЛПИ, 1972.
- Русские ученые основоположники науки о резании металлов. И. А. Тиме, К. А. Зворыкин, Я. Г. Усачев, А. Н. Челюсткин. Жизнь, деятельность и избранные труды Текст.. М., Машгиз, 1952.
- Руководство по металлообработке. Точение. Фрезерование. Сверление. Растачивание. Оснастка: Технический справочник: разработчик АВ Sandvik Coromant. Sweden: АВ Sandvik Coromant, 2005. — 553 с.
- Сегерлинд, Л. Применение метода конечных элементов Текст. / Л. Сегерлинд: Пер. с англ. М.: Мир, 1979. — 393 е., ил.
- Силин, С. С. Аналитическое определение величины сопротивления деформированию при резании металлов Текст. / С. С. Силин, Д. В. Масляков // Вестник машиностроения. 2002. — № 11. — С. 67−69.
- Силин, С. С. Метод подобия при резании материалов Текст. / С. С. Силин. -М.: Машиностроение, 1979. 152 е., ил.
- Скитева, Т. А. Разработка расчетного метода определения технологических условий обработки при торцовом фрезеровании с учетом заданной точности Текст.: дис. .канд. техн. наук/ Скитева Т. А. — Рыбинск: РГАТА, 1997. -226 с.
- Смирнов, Г. В. Методика анализа деформации пера лопатки после обработки с использованием средств компьютерного моделирования Текст. / Г. В.
- Смирнов // Проблемы и перспективы развития двигателестроения: Тр. Ч. 1 Самара: СГАУ, 2003.-С. 351−355.
- Соломенцев, А. М. Адаптивное управление технологическими процессами Текст. / А. М. Соломенцев. -М.: Машиностроение, 1980, 536 с.
- Соломенцев, Ю. М. Моделирование точности при проектировании процессов механической обработки Текст. / Ю. М. Соломенцев, М. Г. Косов, В. Г. Митрофанов. — Обзор М.: НИИмаш, 1984, 56 е., 12 ил. (сер. С-6−3. Технология металлообрабатывающего производства).
- Стерлитамакский станкостроительный завод Электронный ресурс. ОАО Стерлитамак М.Т. Е. Режим доступа: http://www.stanok-mte.ru, свободный. Загл. с экрана. Яз. рус., англ.
- Технология изготовления лопаток турбин авиадвигателей Текст. // ИТО: Инструмент. Технология. Оборудование. 2004. — № 4. — С. 16.
- Уваров, Л.Б. Основные направления развития технологии производства лопаток компрессора ГТД Текст./ JI. Б. Уваров // Справочник. Инженерный журнал -2003. -№ 12.-С. 10−14.
- Уваров, JI. Б. Технология производства лопаток компрессора современных газотурбинных установок Текст./ JI. Б. Уваров. Рыбинск: РГАТА, 2005.-96 с.
- Юркевич, В. В. Повышение точности токарной обработки на основе управления траекториями формообразования Текст. / В. В. Юркевич // Справочник. Инженерный журнал. 2004. — № 2. — С. 14−18.
- Яманнн, А. И. Компьютерно-информационные технологии в двигателестроении Текст. / А. И. Яманин, Ю. В. Голубев, А. В. Жаров [и др.]. -М.: Машиностроение, 2005. 480 е., ил.
- Ящерицын, П. И. Моделирование температурных полей и напряжений в зоне резания металла Текст. / П. И. Ящерицын, С. С. Довнар // Машиностроение: Республ. межведом, научн.-техн. сб. Минск: Вышейшая школа, 1986. — Вып. 11 -С. 3−7.
- Abrari, F. Multi-axis milling of flexible parts Text.: A thesis submitted to the School of Graduate Studies in partial fulfillment of the requirements for the degree Doctorate of Philosophy / F. Abrari McMaster University, 1998.
- Altan, T. Determination of workpiece flow stress and friction at the chip-tool contact for high-speed cutting Text. / T. Altan, T. Ozel // Int. Journal of machine Tools & Manufacture-Vol. 40 (2000). P. 133−152.
- Astakhov, V. P. An opening historical note Text. / V. P. Astakhov // Int. J. Machining and Machinability of Materials -Vol. 1 -No. 1 -P. 3−11.
- Baumel, B. Werkstoffgerechte Auslegung und Festigkeitsnachweis fur Verbrennungsmotorkolben aus Mesophasenkohlenstoff Text.: Dissertation Technische Universitat Munchen, Institut fur Werkstoffe und Verarbeitung 2001.
- Behrens, A. Wissen, was ablauft. Finite-Elemente-Simulation gibt Einblick in HSC-Zerspanprozesse Text. / A. Behrens, J. P Wulfsberg, K. Kaiisch // MaschienenMarkt Das IndustrieMagazin — № 46 — 2002 — S. 26−31.
- Dirikolu, M.H. Modelling requirements for computer simulation of metal machining Text. / M.H.Dirikolu, T.H.Childs // Turk. J. Engin. Environ. Sei. 24 (2000) -P. 81−83.
- Halil, B. A comparison of orthogonal cutting data from experiments with three different finite element models Text. / B. Halil, E. Kilic, A. Erman Tekkaya // Int. J. of Machine Tools & Manufacture № 44 (2004) — P. 933−944.
- Iwabe, H. Analysis of surface generating mechanism of ball end mill based on deflection by FEM Text. / Iwabe H., Natori S., Masuda M. // JSME International Journal, Series C, Vol 47, No. 1, 2004, P. 8−13.
- Johanson, K Looking to the future Text. / K. Johanson // Manufacturing Engineering July 2002 — Vol. 129 — No. 1. — P. 89 — 95.
- Kikkava, K. An approach of estimating machining error by heuristic geometrical rule in 5-axis ball-nosed end milling Text. / Kikkava K., Nakamura K., Mizugaki Y. // JSME International Journal Series C — Vol 47 — No. 1 — 2004 — P. 79−84.
- Lijing Xie, M. Sc. Estimation of two-dimensional tool wear based on Finite Element Method Text.: Dissertation zur Erlangung des akademischen Grades eines Doktors der Ingenieurwissenschafien/ M.Sc.Lijing Xie, Universitat Karlsruhe, 2004.
- Ozel, T. Finite element modeling the influence of edge roundness on the stress and temperature fields induced by high-speed machining Text. / T. Ozel, E. Zeren // Int. J. Adv. Manuf. Technologies Springer-Verlag, London, 2006.
- SINUMERIK 840D. Programming Text.: Brochure: AG SIEMENS 04.2004
- SINUMERIK 840D. Tool and Mold making Text.: Brochure: AG SIEMENS 04.2004
- Soo, S. The development of 3D-FEM HSM-milling of Inconel 718 and cutting parameters determination Text. / S. Soo // Journal of Engineering and Manufacturing -Nr. B11 Vol. 218. 2004-p. 1555−1561.
- Suzuki, Y. A stick motion compensation system with a dynamic model Text. / Suzuki Y., Matsubara A., Kakino Y. // JSME International Journal, Series C Vol 47 -No. 1 -2004-P. 168−174.
- Westhoff, B. Modelierungsgrundlagen zur FE-Analyse von HSC-Prozessen Text.: Dissertation Universitat der Bundeswehr — Hamburg 2001.
- Модификация системы линейных уравнений в соответствии с заданныминачальными условиями
- Рассмотрим систему четырех уравнений первой степени с четырьмя неизвестными: агх + Ъ^у + сх2 + йха = Вх а2х + Ь2у + с2г + ¿-2а = В2 (П. 1.1)аъх + Ь3у + съг + с1ъа = В3 аАх + Ъ, у + с4г + а = ВА
- В матричной записи система уравнений (П. 1.1) выглядит следующим образом:1. А- X = В, (П. 1.2)1. А =1. Ч Ъх <0 г*? Г41а2 Ь2 С2 й2 х = У В = В2аъ Ъъ г в±а4 К С4 ¿-А- Л 14)
- Предположим, что в матрице-столбце неизвестных X значения х, г известны, а в матрице-столбце известных В значения Вь В3 — неизвестны.
- Преобразуем систему (П. 1.1) в соответствии с предположениемГ1. П. 1.3)
- Запишем (П. 1.3) в матричной форме1. А- X = В,-1 6, 0 Г*Л0 Ь2 0 X = У0 Ьг -1 с1ъ 0 К 0 ка)1. П. 1.4) — а^х схг 11. В2 а7х — с2г- аъх с3г КВ4 — а4х — с4г,
- Уравнение (П. 1.4) является модифицированным.
- Вывод уравнения движения произвольной точки инструмента длямногоосевой обработки
- Рассмотрим точку М (рисунок П. 2.1), находящуюся на высоте Rz и расстоянии г от оси OZ и движущуюся по окружности г. Координаты точки М: х~г ¦ cos
- За 1 оборот центр окружности передвинется по оси ОХ на расстояние: p'SoH 2 • 71
- Тогда координаты точки М определяются1. Ф' ЪОЕx-r- cos ср + -——у = г • sin^-z = Rz 2 • 7Г
- Введем угол атаки а. Повернем систему координат вокруг оси ОУ на угол (рисунок П. 2.2).
- У = V • cos (0, a)-z'= V ¦ sin (©, — a) — x'=F-(cos0, cosa + sin©, -sina) — z'=V-(cos©, -sina-sin©, — cosa)-x'= (r • cos (o + ^ ^0/')cosa + Rz-sina- z'= (r ¦ costf? + ^ + Rz • cosa-1. Y 2 ж 2tz1. У= r • sin
- Введем угол наклона p. Повернем систему координат вокруг оси ОХ на угол р (рисунок П. 2.3).
- У'= V • cos (©, /?)-z"= V • sin (0, — /?) — y'=F-(cos0, -cos^ + smO, — sin/?) — z"=V •(eos©, • sin/?-sin 0, -eos/?) У'= y cos ?3 + z'-sin p- z» = У sin P — z' cos P.
- Сделав соответствующие подстановки, получаемх"= (г • cosg> + ^OB)cosа + Rz • sin a- 2 жу" = г • бш^собр + {{г • соб (р + ^ 5°к)-апа + Лг- собсс) -ьт/З-2л"г" = г • бш Ф • бш р ((г • соб (р +. 8ш, а + Лг ¦ СОБ а) • соб Р2ж1. Рисунок П. 2.3
- Алгоритм определения контактных узлов.1. Описание алгоритма)
- Принцип работы функции состоит в следующем.
- С помощью уравнений главы 2 определяется положение программируемой точки инструмента в системе координат отрезка траектории в данный отрезок времени.
- Если условие принадлежности выполняется, то для данного узла в соответствии с выражениями главы 2 определяются проекции скоростей и ускорения на оси машинной системы координат.
- Алгоритм моделирования отделения материала.
- Затем в таблице элементов ЕЬКТ обнуляются строки с номерами тс! ехс1е1е1. В таблице узлов МЫБТ номеру узла присваивается ноль, если данный узел удален вместе с элементом и не принадлежит больше никакому узлу.
- Корректируется матрица механических свойств в соответствии со скорректированными таблицами узлов и элементов.1. Все элементы
- Таблицы режимов резания к эксперименту по определению напряжений прифрезеровании лопатки компрессора ГТД
- Режимы резания СпинкаПрофиль,