Исследование процесса профилирования в валках и совершенствование технологии производства гнутых профилей
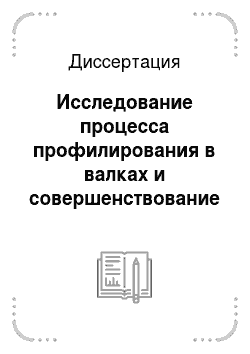
Диссертация
Разработаны алгоритмические способы расчета калибровок рабочих валков профилегибочных станов с разбиением сложного цельного валка на отдельные профильные дисковые элементызаменой двух соседних элементов с одинаковой кривизной образующей на один общийзаменой конусных дисковых элементов на дистанционные втулкизаменой элементов вогнутых поверхностей валка на соответствующие им совокупности конусных… Читать ещё >
Содержание
- Глава 1. Современное состояние вопроса, постановка целей и задач исследования
- 1. 1. Состояние и основные направления исследований процесса профилирования в валках
- 1. 2. Моделирование процесса формообразования гнутых профилей проката и трубной заготовки в валках
- 1. 3. Выводы по главе 1
- 1. 4. Цель и задачи исследования
- Глава 2. Теоретическое исследование процесса формообразования гнутых профилей проката
- 2. 1. Геометрия профилируемой заготовки на участке плавного перехода
- 2. 2. Геометрические параметры продольных и поперечных волокон формуемой полосы
- 2. 3. Необходимые исходные данные
- 2. 4. Гипотезы и допущения
- 2. 5. Формоизменение заготовки в процессе профилирования
- 2. 6. Условия захвата профиля валками клети
- 2. 7. Формоизменение деформируемой заготовки на участке контакта с поверхностью. валков универсальной четырехвалковой клети
- 2. 8. Выводы по главе 2
- Глава 3. Исследования деформированного состояния полосы при производстве гнутых профилей проката
- 3. 1. Аналитический метод определения деформаций металла при производстве гнутых профилей проката на основе теории оболочек
- 3. 2. Экспериментальные исследования пластических деформаций стали в процессе производства гнутых профилей проката
- 3. 3. Выводы по главе 3
- Глава 4. Совершенствование технологии производства гнутых профилей на профилегибочных станах
- 4. 1. Расчет рабочих валков и технологической оснастки для изготовления гнутых профилей проката
- 4. 2. Расчет рациональных параметров процесса профилирования в валках
- 4. 3. Исследование причин возникновения дефектов и совершенствование технологии производства гофрированных гнутых профилей С21×1000×0,6−0,
- 4. 4. Разработка технических параметров профилирования качественных гофрированных гнутых профилей Н57×900×0,55−0,
- 4. 5. Способ производства гофрированных гнутых профилей
- С16,8×1080×0,55−0,
- 4. 6. Мини-станы для производства тонкостенных гнутых профилей проката
- 4. 7. Выводы по главе 4
Список литературы
- Тришевский И.С., Докторов М. Е. Теоретические основы процесса профилирования. -М.: Металлургия, 1980. -288с.
- Рымов В. А., Полухин П. И., Потапов И. Н. Совершенствование производства сварных труб. -М.: Металлургия, 1983. -312с.
- Давыдов В.П., Максаков М. П. Производство гнутых тонкостенных профилей. -М.: Металлургия, 1959. -233с.
- Производство труб электросваркой методом сопротивления / Б. Д. Жуковский, Л. И. Зильберштейн, Я. Е. Осада и др. -М.: Металлургия, 1953. -308с.
- Калибровка валков для производства гнутых профилей проката. Под ред. И. С. Тришевского. Киев: «Техника», 1980. -168с.
- Смирнов-Аляев Г. А., Гун Г. Я. -Изв. вузов. «Черная металлургия», 1962, № 9.
- Смирнов-Аляев Г. А., Гун Г. Я. -Изв. вузов. «Черная металлургия», 1962, № 11.
- Пластическое формоизменение металлов / Г. Я. Гун, П. И. Полухин, В. П. Полухин и др. -М.: Металлургия, 1968. -416с.
- Гун Г. Я., Полухин П. И. Пластическая деформация металлов и сплавов. -М.: Металлургия, 1974.
- Богоявленский К.Н., Григорьев А. К. Обработка металлов давлением. М.-JL: Машиностроение, 1965.
- Докторов М.Е., Олейник Г. В. Исследование процесса пружинения при профилировании // Гнутые профили проката: Отрасл. сб. научн. тр. -Харьков: УкрНИИМет, 1980. -с.10−17.
- Докторов М.Е., Олейник Г. В., Ильюшко В. Н. Экспериментальные исследования процесса пружинения при профилировании // Теория и технология производства гнутых профилей проката: Отрасл. сб. научн. тр. -Харьков: УкрНИИМет, 1982. -с.42−46.
- Расчет жесткости поперечного сечения подгибаемых элементов профиля / В. А. Воблых, Г. В. Олейник, A.B. Павлюк, Н. Г. Попов, С. С. Чумаченко // Производство гнутых профилей проката: Отрасл. сб. научн. тр. -Харьков: УкрНИИМет, 1986. -с.14−19.
- Игнатенко А.П., Хижняков Я. В., Заика С. И. Исследование процесса двухслойной формовки тонкостенных гофрированных профилей //Теория и технология производства гнутых профилей проката: Отрасл. сб. научн. тр. -Харьков: УкрНИИМет, 1982. -с.5−12.
- Осадчий В.А. Конструирование калибров валков для производства гнутых профилей проката с помощью ЭВМ. // Теория и технология процессов пластической деформации: Сб. научн. тр. -М.: Изд-во МИСиС, 1994. -с.117−121.
- Власов В.З. Избранные труды. T.I. М.: Изд. АН СССР, 1962. -528с.
- Власов В.З. Избранные труды. Т.П. М.: Изд. АН СССР, 1963. -507с.
- Коренев Г. В. Тензорное исчисление.-М.: Изд-во МФТИ, 1995.-240.
- Корн Г., Корн Т. Справочник по математике для научных работников и инженеров. -М.: Наука, 1973.-823 с.
- Kiuchi М. CAD system for cold-roll forming. J. Annals of the CIPR, Vol.38/1/1989, pp.283−286.
- H. Suzuki, M. Kiuchi, S. Nakajima, M. Ichiddayama, K. Takada. Experimental investigation on cold-roll forming process. J. Report of The Institute of Industrial Science, The University of Tokyo., Vol.26, 8/1978, pp.291−346.
- U.Oesten: Continuous manufacture of sheet metal sections — j. Technic International- 2/1980- pp 11−17.
- K.Hada, D. Sumitomo, T. Ohsawa: Development of a cross-roll edge-bending method for ERW tube forming- j. Nippon Steel Technical Report- 72/1997- pp.39−46.
- D.Bhattacharyya, P.D. Smith, C.H. Yee, L.F. Collins: The prediction of deformation length in cold-roll forming- Journal of Mechanical Working Technology- 9/1984- pp. 181−191.
- Производство гнутых профилей: Оборудование и технология / И. С. Тришевский, А. Б. Юрченко, B.C. Марьин и др.- Под научн. ред. И. С. Тришевского. -М.: Металлургия, 1982. -384с.
- Чекмарев А. П. Калужский В.Б. Гнутые профили проката. М.: Металлургия, 1974.
- Физические основы пластической деформации. Учебное пособие для вузов / Полухин П. И., Горелик С. С., Воронцов В. К. -М.: Металлургия, 1982. -584с.248
- Колмогоров B. J1. Механика обработки металлов давлением. Учебное пособие для вузов. -М.: Металлургия, 1986. -688с.
- Разработка и освоение технологии производства нового гнутого профиля для тетив пожарных автолестниц. / Колоколов С. В., Клепанда В. В. //Теория и технология производства гнутых профилей проката: Отрасл. сб. научн. тр. -Харьков: УкрНИИМет, 1982. -с.58−64.
- Дьяконов В.П. Справочник по MathCAD PLUS 7.0 PRO -М.: CK Пресс, 1998.-352с, ил.
- MathCAD 6.0 PLUS: Руководство пользователя / Пер. с англ. М.: Филинъ, 1996.-712с.
- Мищенко A.C., Фоменко А. Т. Курс дифференциальной геометрии и топологии. -М.: Изд-во МГУ, 1980. -440с.
- Лысов М.Н. Теория и расчет процессов изготовления деталей методами гибки. —М.: Машиностроение, 1966. -236с.
- Тришевский И. С, Клепанда В. В. Механические свойства гнутых профилей проката. -ML: Металлургия, 1977. -143с.
- P.C. Кинасошвили Сопротивление материалов. -М.: Наука, 1965.-388с.
- Тришевский И. С, Клепанда В. В, Хижняков Я. В. Холодногнутые гофрированные профили проката, Киев, «Техшка», 1967, с.226−246.
- Патент РФ RU № 2 029 645 С1, кл. В 21 D 5/06, 1995.
- Европейский патент Ер N 5 060, кл. В 21 D 5/08, 1980.