Исходные материалы.
Все про известь
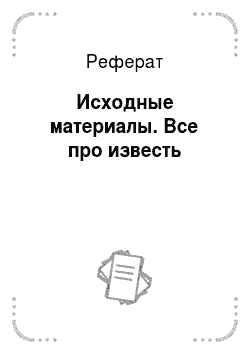
Средняя плотность известняков составляет 2400−2800 кг/м. куб., мела — 1400−2400 кг/м. куб. Влажность известняков колеблется в пределах 3−10%, а мела — 15−25%. Сырьём для производства воздушной извести могут служить не только специально добываемые для этой цели карбонатные породы, но и отходы при добыче известняков для нужд металлургической, химической, строительной и других отраслей… Читать ещё >
Исходные материалы. Все про известь (реферат, курсовая, диплом, контрольная)
Исходными материалами для производства воздушной извести являются многие разновидности известково-магнезиальных карбонатных пород. Все они относятся к осадочным породам. В состав известняков входят углекислый кальций СаСО3 и небольшое количество различных примесей.
Карбонат кальция состоит из 56% СаО и 44% СО2. Он встречается в виде двух минералов — кальцита и аргонита.
Кальцит, или известковый шпат, кристаллизуется в гексагональной системе. Его кристаллы имеют форму ромбоэдров. Истинная плотность кальцита 2,6−2,8г/см. куб., твёрдость по десятибалльной шкале — 3. Кальцит хорошо растворяется при обычной температуре в слабой соляной кислоте с выделением углекислого газа.
Арагонит — менее распространённый минерал, кристаллизуется в ромбической системе. Его истинная плотность 2,9−3 г/см. куб., твёрдость — 3,5−4. При нагревании до 300−400°С арагонит превращается в кальцинит, рассыпаясь в порошок.
Чистые известково-магнезиальные породы — белого цвета, однако они часто бывают окрашены примесями оксидов железа и углистыми примесями. Количество и вид примесей к карбонатным породам, размеры частей примесей, а также равномерность распределения их в основной массе в большей степени отражаются на технологии производства извести, выборе печей для обжига, оптимальной температуре и продолжительности обжига, а также на свойствах получаемого продукта.
Обычно чистые и плотные известняки обжигают при 1100−1250°С. Чем больше карбонатная порода содержит примесей доломита, глины, песка, тем ниже должна быть оптимальная температура обжига для получения мягко обожжённой извести.
Такая известь хорошо гасится водой и даёт тесто с высокими пластичными свойствами.
Примеси гипса нежелательны. При содержании в извести даже около 0,5−1% гипс сильно снижает пластичность известкового теста. Значительно влияют на свойства и железистые примеси, которые уже при 1200 °C и более вызывают образование в процессе обжига легкоплавких эвтектик, способствующих интенсивному росту крупных кристаллов оксида кальция, медленно реагирующих с водой при гашении извести и вызывающих явления, связанные с понятием «пережог».
Физико-механические свойства пород также отражаются на технологии извести. Для обжига в высоких шахтных печах пригодны лишь те породы, которые характеризуются значительной механической прочностью (прочность на сжатие не менее 20−30МПа). Куски породы должны быть однородными, неслоистыми, они не должны рассыпаться и распадаться на более мелкие части во время нагревания, обжига и охлаждения.
Рассыпаться во время обжига склонны крупнокристаллические известняки, состоящие из кристаллов кальцита размером 1−3 мм. Мягкие разновидности известково-магнезиальных пород надо обжигать в печах, в которых материал не подвергается сильному измельчению. Известково-магнезиальные породы в зависимости от их химического состава являются сырьём для производства не только воздушной, но и гидравлической извести, а также портландцемента.
В зависимости от химического состава карбонатные породы делят на семь классов: А, Б, В, Г, Д, Е, Ж.
Из сырья классов, А и Б получают соответственно жирную (пластичную) и тощую маломагнезиальную известь, из сырья классов В и г. — магнезиальную, из сырья классов Д и Е — доломитовую, а из сырья класса Ж — гидравлическую известь. По структуре известняки делят на: кристаллические зернистые мраморовидные, плотные тонкозернистые, оолитовые, известковые туфы, известняки-ракушечники, мел и доломиты.
Мрамор по химическому составу — наиболее чистое сырьё. Однако в связи с высокими декоративными свойствами он используется в качестве отделочного материала, и поэтому в производстве извести, за редким исключением, не применяется. Плотные известняки имеют мелкозернистую кристаллическую структуру, содержат обычно небольшое количество примесей и отличаются высокой прочностью. Их наиболее широко используют для получения извести.
Мел — мягкая рыхлая горная порода, легко рассыпающаяся на мелкие куски. Его обычно обжигают лишь во вращающихся печах, так как при обжиге в шахтных печах он легко крошится, что нарушает процесс обжига.
Известняковый туф отличается ноздреватым строением и большой пористостью. Иногда его используют для производства извести во вращающихся и шахтных печах (в зависимости от прочности).
Известняк-ракушечник состоит из раковин, сцементированных углекислым кальцием. Он представляет собой мало-прочную горную породу, поэтому редко применяется для изготовления извести.
Оолитовый известняк — горная порода, состоящая из отдельных шариков карбоната кальция, сцементированных тем же веществом.
Теоретически доломит состоит из 54,27% СаСО3 и 45,73% MgCO3 или 30,41% СаО, 21,87% MgO и 47,72% СО2. Истинная плотность доломита 2,85−2,95 г/см. куб. доломитовые породы почти нацело слагаются минералом доломитом с тем или иным содержанием глинистых, песчаных, железистых и тому подобных примесей.
Средняя плотность известняков составляет 2400−2800 кг/м. куб., мела — 1400−2400 кг/м. куб. Влажность известняков колеблется в пределах 3−10%, а мела — 15−25%. Сырьём для производства воздушной извести могут служить не только специально добываемые для этой цели карбонатные породы, но и отходы при добыче известняков для нужд металлургической, химической, строительной и других отраслей промышленности. Для этой цели в ряде случаев используют побочные продукты в виде дисперсного карбоната кальция или гидроксида кальция.