Специальные термические процессы в сварочном производстве
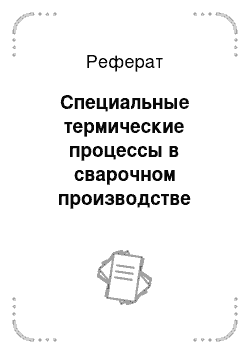
Термическая резка базируется на использовании широкого круга источников теплоты (газовое пламя, плазменная дуга, электронный и лазерный луч). Можно разрезать металлы и сплавы различной толщины (от десятков миллиметров до долей миллиметра), любого химического состава, обеспечивать достаточно высокую точность и чистоту реза. Причем возможно осуществлять непрерывный процесс резки, прошивать… Читать ещё >
Специальные термические процессы в сварочном производстве (реферат, курсовая, диплом, контрольная)
К сварочным процессам помимо процессов соединения относят также термическую сварку, резку, наплавку, напыление и ряд других методов обработки материалов [1, 2, 4, 18, 19].
юо При необходимости сварки стальных деталей некоторых типов в полевых условиях применяют «термиты». Источником теплоты является экзотермическая реакция восстановления оксидов железа алюминием (алюминиевые термиты — смесь 22% алюминия и 78% железной окалины). Зачищенный стык соединяемых деталей заключают в разъемную керамическую форму и засыпают термитной смесью. Термит поджигают фосфорным запалом. В результате реакции образуется оксид алюминия, который расплавляет железо, заполняющее зазор в стыке. Сварку довершают сжатием стыка. Оксид алюминия всплывает в виде шлака.
При соединении стержней и проводов линий электропередач применяют муфельную сварку магниевым термитом (смесь оксидов железа с магнием).Концы деталей вводят в муфту и сдавливают винтовым зажимом.
Термическая резка базируется на использовании широкого круга источников теплоты (газовое пламя, плазменная дуга, электронный и лазерный луч). Можно разрезать металлы и сплавы различной толщины (от десятков миллиметров до долей миллиметра), любого химического состава, обеспечивать достаточно высокую точность и чистоту реза. Причем возможно осуществлять непрерывный процесс резки, прошивать отверстия в заготовках, производить поверхностную резку (снятие слоя металла с заготовки).
Основной разновидностью термической резки является кислородная резка металлов. Она заключается в сжигании металла в струе кислорода и удалении этой струей образующихся оксидов.
Кислородная резка металлов происходит в две стадии: место резки подогревается пламенем газовой горелки до температуры воспламенения металла в струе кислорода; открывается основной «режущий» вентиль кислорода — металл сгорает в струе кислорода.
Плохо режутся чугун, алюминиевые и медные сплавы.
Обычно кислородную резку используют для разрезания металлов толщиной 5—300 мм.
Плазменно-дуговую резку выполняют плазменной дугой и плазменной струей. При резке плазменной дугой металл выплавляется из полости реза направленным потоком плазмы (полностью ионизированного газа), совпадающим с токоведущим столбом создающей его дуги прямого действия. Этим способом можно разрезать толстые листы алюминия и его сплавов (до 80—120 мм), высоколегированную сталь и медные сплавы, т. е. те материалы, которые не годятся для кислородной резки. Плазменной струей, полученной в столбе дугового разряда независимой дуги, разрезают неэлектропроводные материалы (например, керамику), тонкие стальные листы, алюминиевые и медные сплавы, жаропрочные сплавы и т. д. При плазменной резке используют аргон, его смесь с водородом, воздух и другие плазмообразующие газы.
Наплавка — процесс, при котором на поверхность детали наносится слой металла требуемого состава.
Наплавку применяют при ремонте изношенных деталей для восстановления их исходных размеров и для изготовления новых изделий. Масса наплавленного металла обычно не превышает нескольких процентов от общей массы изделия. Проплавление основного металла и перемешивание основного и наплавленного металлов должно быть минимальным для сохранения механических свойств наплавляемого слоя.
Для наплавочных работ создано большое количество различных сплавов, разработано множество марок наплавочных электродов, кроме того, можно применять электроды общего назначения.
Ручная дуговая наплавка металлическими электродами — самый простой и распространенный способ наплавки. Ее выполняют короткой дугой на минимальном токе.
Существует также много других разновидностей наплавки с использованием плазменной дуги, газового пламени, плавящегося электрода в защитном газе, порошковой проволоки и пластинчатого электрода.
При напылении расплавленные по всему объему или по поверхности частицы материала будущего покрытия направляются на поверхность нагретой заготовки. При соударении с поверхностью частица деформируется, обеспечивая хороший физический контакт с деталью. Характер взаимодействия частицы с материалом подложки (детали), последующая кристаллизация частиц определяют качество адгезии покрытия с подложкой. Последующие слои формируются уже за счет связей частиц друг с другом, имеют чешуйчатое строение, и неоднородны.
По мере повышения стоимости объемного легирования и стремления получить требуемые эксплуатационные свойства более экономичным способом (легированием только поверхности изделия) напыление становится все более предпочтительным и перспективным.
Для напыления используют источники тепла: газовое пламя, плазму, ионный нагрев, нагрев в печах, лазер и др.
Наибольшее распространение получили процессы газоплазменного и плазменного напыления. Материал для напыления подается в пламя горелки или плазменную дугу в виде проволоки или порошка, где происходит нагрев и распыление частиц, которые тепловым потоком источника нагрева разгоняются и попадают на поверхность напыляемой детали.
Иной способ формирования покрытий при нагреве в печах. В этом случае нагретая деталь контактирует с материалом покрытия, находящимся в виде порошка или газовой фазы. Получаемое таким методом покрытие имеет высокую адгезию к поверхности детали за счет активных диффузионных процессов, происходящих в период достаточно длительной выдержки в печи при высокой температуре.
Все большее распространение получают ионно-плазменные методы нанесения износостойких и декоративных покрытий.