Оптимизация режимов резания при обработке на станках с ЧПУ с целью повышения точности размеров и формы деталей в процессе точения
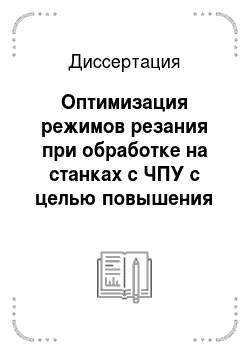
Диссертация
Результаты производственных и лабораторных испытаний подтвердили работоспособность и высокую экономическую эффективность практического использования вышеуказанной автоматизированной системы. Данная автоматизированная система («PRECISION») позволяет значительно повысить технико-экономическую эффективность и общую рентабельность машиностроительного производства без дополнительных трудовых… Читать ещё >
Содержание
- ПЕРЕЧЕНЬ УСЛОВНЫХ ОБОЗНАЧЕНИЙ
- ГЛАВА 1. СОСТОЯНИЕ ВОПРОСА
- 1. 1. Состояние вопроса аналитического определения технологических условий, обеспечивающих заданную точность обработки при точении материалов на станках с ЧПУ
- 1. 1. 1. Анализ и методы исследований погрешностей обработки при точении материалов
- 1. 1. 2. Определение суммарной погрешности токарной обработки деталей на станках с ЧПУ
- 1. 1. 3. Влияние технологических условий на погрешность токарной обработки, предопределяемой недостаточной жесткостью технологической системы СПИЗ
- 1. 1. 4. Влияние технологических условий на погрешность токарной обработки, предопределяемой температурными деформациями элементов технологической системы СПИЗ
- 1. 1. 5. Влияние технологических условий на погрешность токарной обработки, предопределяемой размерным износом резца
- 1. 2. Цель и задачи исследований
- 1. 1. Состояние вопроса аналитического определения технологических условий, обеспечивающих заданную точность обработки при точении материалов на станках с ЧПУ
- ГЛАВА 2. РАЗРАБОТКА МАТЕМАТИЧЕСКОЙ МОДЕЛИ СУММАРНОЙ ПОГРЕШНОСТИ ОБРАБОТКИ НА ТОКАРНЫХ СТАНКАХ С ЧПУ
- 2. 1. Определение погрешности при токарной обработке заготовок, предопределяемой недостаточной жесткостью технологической системы СПИЗ
- 2. 1. 1. Определение коэффициента динамичности технологической системы СПИЗ
- 2. 1. 2. Определение радиальной составляющей силы резания
- 2. 1. 3. Определение статической жесткости технологической системы СПИЗ
- 2. 2. Определение погрешности заготовки, предопределяемой износом режущего инструмента при точении материалов
- 2. 3. Теоретико-экспериментальное определение погрешности формы заготовки, предопределяемой ее температурными деформациями при токарной обработке
- 2. 4. Определение погрешности заготовки, предопределяемой температурными деформациями режущего инструмента
- 2. 5. Погрешности обработки характерные для станков с ЧПУ
- 2. 5. 1. Расчетное определение погрешности позиционирования режущего инструмента
- 2. 5. 2. Расчетное определение погрешности смены режущего инструмента в револьверной головке
- 2. 6. Математическая модель суммарной погрешности обработки на токарных станках с ЧПУ
- 2. 1. Определение погрешности при токарной обработке заготовок, предопределяемой недостаточной жесткостью технологической системы СПИЗ
- Выводы по главе 2
- ГЛАВА 3. МЕТОДОЛОГИЯ ПОВЫШЕНИЯ ТОЧНОСТИ ФОРМЫ ИЗГОТАВЛИВАЕМЫХ ДЕТАЛЕЙ ПУТЕМ ДИНАМИЧЕСКОЙ ОПТИМИЗАЦИИ РЕЖИМОВ РЕЗАНИЯ ПРИ ПРОГРАММИРОВАНИИ ТОКАРНЫХ СТАНКОВ С ЧПУ
- 3. 1. Обеспечение точности токарной обработки заготовки на стадии ТПП
- 3. 2. Обеспечение точности формы заготовки при токарной обработке на станках с ЧПУ
- 3. 3. Технологические ограничения, накладываемые на анализируемый процесс резания и учитываемые автоматизированной системой «PRECISION»
- 3. 3. 1. Определение характеристик шероховатости поверхностного слоя формируемого при точении материалов
- 3. 3. 2. Определение коэффициента запаса динамической устойчивости процесса точения
- 3. 3. 3. Определение хрупкой прочности режущей кромки инструмента
- 4. 1. Результаты проведения лабораторных испытаний
- 4. 2. Результаты проведения производственных испытаний
- 4. 3. Апробация системы «PRECISION» на конкретных деталях в производственных условиях ОАО «РМ»
Список литературы
- Система автоматизированного проектирования. В 9-ти книгах. Кн.6. Автоматизация конструкторского и технологического проектирования: Учебное пособие для вузов/ Н. М. Капустин, Г. Н. Васильев- Под ред. И. П. Норенкова. М.: Высшая школа, 1986. — 191 с.
- Автоматизированная система проектирования технологических процессов механосборочного производства/ Под ред. Н. М. Капустина. М.: Машиностроение, 1979. — 247 с.
- Капустин Н.М. Разработка технологических процессов обработки ЭВМ. М.: Машиностроение, 1976. — 278 с.
- Горанский Г. К., Бендерова Э. И. Технологическое проектирование в комплексных автоматизированных системах подготовки производства. М.: Машиностроение, 1981. — 455 с.
- Горанский Г. К. Автоматизированные системы технологической подготовки производства: структура, функционирование и перспективы развития в СССР и за рубежом: Обзорная информация/. Минск, БелНИИНТМ, 1989. — Вып. 1.-56 с.
- Горанский Г. К. Методика выбора металлорежущих станков, инструментов и режимов резания в автоматизированных системах технологического проектирования: Обзорная информация/. Минск, БелНИИНТМ, 1990. -Вып.6. — 64с.
- Автоматизированные системы технологической подготовки производства/ Под ред. Г. К. Горанского. М.: Машиностроение, 1976. — 239 с.
- Бойцов В.В. Автоматизация технологической подготовки производства. М.: Машиностроение, 1982. — 320 с.
- Челищев Б.П., Боброва И. В. Автоматизированные системы технологической подготовки производства. М.: Энергия, 1975.- 137с.
- Аверченков В.И. Оптимизация технологических процессов в САПР ТП: Учебно-методическое пособие/ БИТМ. Брянск, 1987.- 108с.177
- Якобе Г. Ю., Якоб Э., Кохан Д. Оптимизация резания. Параметризация способов обработки резанием с использованием технологической оптимизации: Пер. с нем./. М.: Машиностроение, 1981.- 279 с.
- Соломенцев Ю.М., Басин A.M. Оптимизация технологических процессов механической обработки и сборки в условиях серийного производства: Обзор/. М.: НИИМАШ, 1977. — 73 с .
- Павлов В.В. Математическое обеспечение САПР в производстве летательных аппаратов. М.: МФТИ, 1981. — 64 с.
- Великанов K.M., Новожилов В. И. Экономические режимы резания металлов. JL: Машиностроение, 1972. — 119 с.
- Горанский Г. К., Владимиров Е. В., Ламбин J1.H. Автоматизация технического нормирования на металлорежущих станках с помощью ЭВМ. -М.: Машиностроение, 1970. 222 с.
- Игумнов Б.Н. Расчет оптимальных режимов обработки для станков и автоматических линий. М.: Машиностроение, 1974. — 200 с.
- Автоматизированное проектирование оптимальных наладок металлорежущих станков/ A.M. Гильман, Г. В. Гостев, Ю. Б. Егоров и др. М.: Машиностроение, 1984. — 168 с.
- Оптимизация режимов резания на металлорежущих станках/ A.M. Гильман, Л. А. Брахман, Д. И. Батищев и др. М.: Машиностроение, 1972. -188 с.
- Козлов В.А. Температурно-силовые характеристики процесса резания и их теоретико-экспериментальное определение: Учебное пособие / РГАТА. Рыбинск, 1997. — Ч. 1, 2. — 449 с.
- Макаров А.Д. Износ и стойкость инструментов. М.: Машиностроение, 1966.- 264 с.
- Макаров А.Д. Оптимизация процессов резания. М.: Машиностроение, 1976.- 278 с.178
- Макаров А.Д., Мухин B.C., Шустер Л. Ш. Износ инструмента, качество и долговечность деталей из авиационных материалов. Уфа: УАИ, 1974. — 372 с.
- Смазочно-охлаждающие технологические средства для обработки металлов резанием: Справочник/ Под общей ред. С. Г. Энтелиса, Э.М. Берли-нера. 2-е изд., перераб. и доп./ - М.: Машиностроение, 1995. — 495 с.
- Резников Н.И., Жарков И. Г., Зайцев В. М. и др. Производительная обработка нержавеющих и жаропрочных материалов/ Под ред. Н. И. Резникова. М.: Машгиз, 1960. — 200 с.
- Аршинов В.А., Алексеев Г. А. Резание металлов и режущий инструмент. М.: Машиностроение, 1967. — 440 с.
- Филоненко С.Н. Резание металлов. Киев, Техника, 1975.- 237с.
- Богородский Е.С. Влияние масштабного фактора деталей на рациональные условия эксплуатации режущего инструмента// Высокопроизводительный режущий инструмент: Сб. науч. тр./.- М.: Машгиз, 1973. с. 167−174.
- Х.К. Дей Секер, Д. К. Пэл Силы резания при тонком растачивании чугунных втулок. Jn Journal of the Institution of Engineers (Jndia), 1976, v.56, N 5, p.220−225.
- Филоненко C.H., Гончар Ю. Н. Зависимость величины тангенциальной силы резания от диаметра обработки // Станки и инструмент. 1962. -N7.-c.30.
- Макаров А.Д., Танатаров P.A. Зависимость размерного износа резцов от диаметра расточки// Станки и инструмент. 1964. — N6. — с.28−29.
- Макаров А.Д., Волгарев J1.H. Влияние диаметра и жесткости заготовки на износ резцов и чистоту обработанной поверхности// Тезисы докладов ВНТК «Жесткость в машиностроении"/ БИТМ. Брянск, 1971. — с.226−230.
- Подураев В.Н., Суворов A.A., Елизаров А. И. Зависимость процесса резания от кривизны обрабатываемой поверхности// Известия вузов. Машиностроение. 1975. — N9. — с. 165−167.179
- Жарков И.Г. Вибрации при обработке лезвийным инструментом. -Л.: Машиностроение, 1986. 184 с.
- Высоцкий Ю.И., Хает Г. Л. Определение стойкости резцов с учетом вибраций системы СПИД// Резание и инструмент: Респ. меж-вед. сб. науч. тр./ ХГУ. Харьков, Вища школа, 1979.- Вып. 22. — с.19−25.
- Бармин Б.П. Вибрации и режимы резания. М.: Машиностроение, 1972. — 72 с.
- Балакшин B.C. Основы технологии машиностроения. М.: Машиностроение, 1969. — 72 с.
- Корсаков B.C. Точность механической обработки. М.: Машгиз, 1961.-379 с.
- Соколовский А.П. Расчеты точности обработки на металлорежущих станках. М.: Машгиз, 1952. — 288 с.
- Соколовский А.П. Научные основы технологии машиностроения. -М.: Машгиз, 1955. 515 с.
- Маталин A.A. Технология механической обработки. Л.: Машиностроение, 1977. — 462 с.
- Колев К.С. Точность обработки и режимы резания. М.: Машиностроение, 1968. — 131 с.
- Колев К.С. Технология машиностроения. М.: Высшая школа, 1977. — 256 с.
- Медведев Д.Д. Точность обработки в мелкосерийном производстве. М.: Машиностроение, 1973. — 119 с.
- Базров Б.М. Технологические основы проектирования самоподна-лаживающихся станков. М.: Машиностроение, 1978. — 216 с.180
- Точность обработки, заготовки и припуски в машиностроении/ Ко-силова А.Г. и др. М.: Машиностроение, 1976. — 588 с.
- Силин С.С. Установление критериальных зависимостей при резании металлов на основе изучения тепловых явлений // Тепловые явления и обрабатываемость резанием авиационных материалов: Сб. науч. тр./ МАТИ. -М.: Мвшиностроение, 1966. -Вып. 64. с. 102−138.
- Кован В.М. Основы технологии машиностроения. М.: Машгиз, 1959. — 172 с.
- Проников A.C. Технологическая надежность станков. М.: Машиностроение, 1971. -215 с.
- Проников А. С, Основные вопросы надежности и долговечности машин. М.: Машиностроение, 1969. — 256 с.
- Трощецкий С.П. Расчеты точности обработки на металлорежущих станках. М.: Машиностроение, 1964. — 203 с.
- Обеспечение точности технологического процесса механической обработки/ Безъязычный В. Ф., Силин С. С. и др. Учебное пособие, Ярославль, ЯПИ, 1979. 68 с.
- Безъязычный В.Ф., Чистяков Ю. П. Расчетное определение технологической погрешности обработки лезвийным инструментом// Расчет режимов резания на основе общих закономерностей процессов резания: Сб. науч. тр./ЯПИ. Ярославль, 1982. — 162 с.
- Смолин JI.C. Расчет оптимальных режимов резания при точении с учетом заданной точности и жесткости системы СПИД. Автореферат кан-дитатской диссертации, КуАИ, 1973.
- Справочник технолога-машиностоителя / под ред. Косиловой А. Г., Мещерякова P.C. М.: Машиностроение, 1972. — 694 с.
- Гжиров Р.И., Серебреницкий П. П. Программирование обработки на станках с ЧПУ. Справочник. -JI.: Машиностроение. Ленингр. отделение, 1990.-588 с.181
- Грачев Л.Н., Гиндин Д. Е. Автоматизированные участки для точной размерной обработки деталей. М.: Машиностроение, 1981. — 240 с.
- Соломенцев Ю.М., Сосонькин В. Л. Управление гибкими производственными системами. М.: Машиностроение, 1988. — 352 с.
- Адаптивное управление технологическими процессами/ Ю. М. Соломенцев, В. Г. Митрофанов, С. П. Протопопов и др. М.: Машиностроение, 1980. — 536 с.
- Станки с программным управлением. Справочник. М.: Машиностроение, 1975. — 288 с.
- Программное управление станками и промышленными роботами/ В. Л. Косавский, Ю. Г. Козырев, А. Н. Ковшов и др. М.: Высшая школа, 1989.- 722 с.
- Марголит Р.Б. Наладка станков с программным управлением. М.: Машиностроение, 1983. — 253 с.
- Молчанов Г. Н. Повышение эффективности обработки на станках с ЧПУ. М.: Машиностроение, 1979. — 204 с.
- Старков В.К. Обработка резанием. Управление стабильностью и качеством в автоматизированном производстве.- М.: Машиностроение, 1989.- 296 с.
- Аршанский М.М., Щербаков В. П. Вибродиагностика и управление точностью обработки на металлорежущих станках. М.: Машиностроение, 1988.- 136 с.
- Невельсон М.С. Автоматическое управление точностью обработки на металлорежущих станках. Л.: Машиностроение, 1982. — 184 с.
- Шарин Ю.С. Обработка деталей на станках с ЧПУ. М.: Машиностроение, 1983. — 117 с.
- Ратмиров В.А., Чурин И. Н., Шмутер С. Л. Повышение точности и производительности станков с программным управлением. М.: Машиностроение, 1970. — 343 с.182
- Оптимизация технологических условий механической обработки деталей авиационных двигателей/ В. Ф. Безъязычный, Т. Д. Кожина и др. М.: МАИ, 1993.- 184 с.
- Медведев Д.Д. Автоматизированное управление процессом обработки резанием. М.: Машиностроение, 1980. — 143 с.
- Силин С.С. Теория подобия в приложении к технологии машиностроения: Учебное пособие/ЯПИ. Ярославль, 1989. — 108 с.
- Козлов В.А. Прогнозирование точности обработки и характеристик качества поверхностного слоя при точении материалов/ РГАТА. Рыбинск, 1998, — 110с. Деп. в ВИНИТИ 16.10.98, № 1435-В98.
- Козлов В.А. Аналитическое определение критического износа режущих инструментов/ РГАТА. Рыбинск, 1998. — 40 с. Деп. в ВИНИТИ 12.05.98, № 1434-В98
- Трусов В.В., Козлов В. А. Взаимосвязь между значениями износа режущего инструмента по задней поверхности и радиальном направлении/ РАТИ. Рыбинск, 1986. — 32 с. Деп. в ВНИИТЭМР (№ 5мш -86).
- Базров Б.М., Балакшин В. С., Баранчукова И. М. Адаптивное управление станками. М.: Машиностроение, 1973.- 688с.
- Кутателадзе С.С., Борищанский В. М. Справочник по теплопередаче. -М.: Госэнергоиздат, 1959.- 352с.
- Арнольд JI.B., Михайловский Г. А., Селиверстов В. М. Техническая термодинамика и теплопередача.- М.: Высшая школа, 1979.- 446с.
- Михеев М.А., Михеева И. М. Основы теплопередачи. М.: Энергия, 1977.- 343с.
- Резников А.Н. Теплообмен при резании и охлаждении инструментов. М.: Машгиз, 1963. — 200с.
- Резников А.Н. Теплофизика резания. М.: Машиностроение, 1969. -288с.
- Справочник по машиностроительным материалам/ Под ред. Г. И. Погодина Алексеева, т. 1 — М.: Машгиз, 1959. — 908с.182
- Резников А.Н. Теплофизика процессов механической обработки материалов. -М.: Машиностроение, 1981. 279с.
- Силин С.С. Применение метода подобия для определения обрабатываемости резанием современных материалов// Новые методы определения обрабатываемости метериалов резанием и шлифованием: Сб. науч. тр./ЯПИ. Ярославль, 1975. — Вып. З — С. 5. .34.
- Силин С.С. Метод подобия при резании материалов. М.: Машиностроение, 1979. — 152с.
- Силин С.С., Козлов В. А. К вопросу теоретического расчета сил резания// Производительная обработка и технологическая надежность деталей машин: Сб. науч. тр./ЯПИ. Ярославль, 1977. — Вып.6. С. 25.36.
- Козлов В.А., БелецкийД.В. Аналитическое определение длины упруго-пластического контакта стружки с передней поверхностью режущих инструментов// Вестник верхневолжского отделения АТН РФ: Сб. науч. тр./ РГАТА. Рыбинск, 1998.-Вып.З.-С. 104−113.
- Козлов В.А., Мартюшина Н. Ф. Применение метода факторного планирования экспериментов для решения теоретических задач механической обработки материалов. Деп. рукопись № 20 мш 85 (ВНИИТЭМП), -16с.
- Малов А.Н. Общетехнический справочник. М.: Машиностроение, 1971. -464с.
- Безъязычный В.Ф., Чистяков Ю. П. Расчетное определение технологической погрешности обработки лезвийным инструментом// Расчет режимов на основе общих закономерностей процесса резания: Сб. науч. тр. /ЯПИ, -Ярославль, 1982.-Вып. 10. С. 51.63.
- Смазочно-охлаждающие технологические средства для обработки металлов резанием: Справочник/ Под общей ред. С. Г. Энтелиса, Э.М. Берли-нера. -2-е изд., перераб. и доп./- М.: Машиностроение, 1995. 495с.
- Резников А.Н. Теплообмен при резании и охлаждении инструментов. М.: Машиностроение, 1963. 200с.183
- Решетов Х. А, Смирнов В. Э. Влияние тепловых деформаций на точность токарной обработки // Станки и инструмент.-1952.-№ 1.
- Комаров И.М. Тепловые явления при резании // Вестник машиностроения.-1954.-№ 8.
- Морозов И.А. Исследование температурного поля в обрабатываемом материале при резании // Труды московского авиационного института им. С. Ордженикидзе.-Москва, 1956.-Выпуск 70.
- Корсаков B.C. Исследование деформаций деталей машин в процессе их обработки.-Москва:МВТУД950.
- Гостев Г. В. Сопротивление металлов пластическому деформированию в условиях резания// Труды Горьковского политехнического института. Механический и машиностроительный факультеты: Сб. науч. тр./ ГНИ. Горький, 1968. № 4. — С.89−92.
- Гостев Г. В., Моисеев С. И. Силы, усадка стружки и напряжения при резании некоторых технически чистых материалов// Вопросы технологии машиностроения: Сб. науч. тр./ ГПИ. Горький, 1970. Т. 26, № 4. — С. 12−18.
- Армарего И.Д. Обработка металлов резанием. М.: Машиностроение, 1977, 326с.
- Кононов Ю.Е. Исследование износа твердосплавных режущих инструментов при резании металлов методом теории подобия. Сб. научных трудов РАТИ N 7, Ярославль, 1977.
- Силин С.С. Расчет оптимальных режимов на основе изучения процессов резания методами теории подобия // Технология машиностроения: Сб. науч. тр. / ЯПИ. Ярославль, 1968. — Вып. 1. — с.43−64.
- Силин С.С. Метод подобия при резании материалов. М.: Машиностроение, 1979. — 152с.184
- Козлов В.А. Аналитическое определение на ЭВМ оптимальных по размерной стойкости инструмента режимов резания при точении материалов: Учебное пособие / РГATA. Рыбинск, 1997. — 123с.
- Ящерицин П.И., Еременко M.JL, Фельдштейн Е. Э. Теория резания. Физические и тепловые процессы в технологических системах: Учебник для вузов. М.: Высшая школа, 1990. — 512с.
- Кацев П.Г. Статистические методы исследования режущего инструмента. М.: Машиностроение, 1974. — 231с.
- Подураев В.Н. Резание труднообрабатываемых материалов: Учебное пособие для вузов. М.: Высшая школа, 1974. — 587с.
- Макаров А.Д., Шевин Г. А. Исследование некоторых характеристик обрабатываемости при чистовом точении сплава Ал9 // Вопросы оптимального резания металлов: Сб. науч. тр. / УАИ. Уфа, 1972. — вып 29. -с.26−31.
- Трусов В.В., Козлов В. А. Влияние износа режущего инструмента на динамическое состояние технологической системы // Оптимизация операций механической обработки: Сб. науч. тр. / ЯПИ. Ярославль, 1984. -Вып.12. — с.97−100.
- Трусов В.В., Козлов В. А. Расчет жесткости резания (точение): Учебно-методическое пособие. Рыбинск, РГАТА, 1992. — 31с.
- Лоладзе Т.Н. Прочность и износостойкость режущего инструмента. -М.: Машиностроение, 1982. 320с.
- Лоладзе Т.Н. Износ режущего инструмента. М.: Машгиз, 1958.354с.
- Бетанели А.И. Хрупкая прочность режущей части инструмента / ГПИ. Тбилиси, 1969. — 319с.
- Остафьев В.А. Расчет динамической прочности режущего инструмента. М.: Машиностроение, 1979. — 168с.
- Писаренко Г. С., Лебедев A.A. Деформирование и прочность материала при сложном напряженном состоянии. Киев, «Наукова Думка», 1976. -415с.
- Утешев М.Х. Разработка научных основ прочности режущей части инструмента по контактным напряжениям с целью повышения его работоспособности: Автореферат дис. докт. техн. наук. Томск, 1966. — 36с.
- Дзельтен Г. П. Определение напряженного состояния и прочности режущей части инструмента с целью выбора ее рациональных параметров: Автореферат дис. докт. техн. наук. Санкт-Петербург, 1996. — 36с.186
- Сенюков В.А., Серов A.B., Рымин A.B. и др. Оптимизация черновой обработки отверстий сверлами с СМП с ограничением по прочности режущей части // Вестник Верхневолжского отделения АТН РФ: Сб. науч. тр. / РГАТА. Рыбинск, 1994. — Вып.1. — с.40−42.
- Справочник конструктора-инструментальщика: Под общей редакцией В. И. Баранчикова. -М.: Машиностроение, 1994. 560с.
- Козлов В.А., Смирнов Ф. В. Автоматизированная система научно-обоснованного выбора оптимальных технико-технологических условий процесса токарной обработки: Монография / РГАТА. — Рыбинск, 1998. 96с.
- Козлов В.А. Комплексная оптимизация токарных операций на основе математического моделирования условий обработки. — «Справочник. Инженерный журнал». 1999. — N 6. — с.6−9.
- Козлов В.А. Повышение эффективности токарной обработки на основе автоматизированного выбора оптимальных условий и режимов резания / РГАТА. Рыбинск, 1998. — 16с. — Деп. в ВИНИТИ N 3024-В98.
- Прогрессивные режущие инструменты и режимы резания металлов: Справочник. В. И. Баранчиков, A.B. Жаринов, Н. Д. Юдина и др.- Под общей редакцией В. И. Баранчикова. М.: Машиностроение. 1990. — 400с.
- Фомин С.Ф. Справочник мастера токарного участка. М.: Машиностроение, 1985. — 240с.
- Михайлов-Михеев П. Б. Справочник по металлическим материалам турбино- и моторостроения. М.: Машгиз, 1961. — 838с.
- Ы2 -0,909 -0,955 -0,2 603 -0,3 885 0,382 -0,3 088 0,2 772 -0,3 549 0,2 082 0,697
- КВ -0,16 581 -0,17 884 -0,24 771 -0,28 964 -0,19 544 -0,44 705 0,27 083 -1,6 687 0,10 787 0,24 141
- И.4 1,9 191 1,9 116 3,2 893 1,96 249 1,74 818 1,81 579 0,72 365 4,26 723 -0,70 253 0,14 103
- Ы5 0,34 730 0,34 503 0,29 975 0,6976 В 0,37 132 0,47 671 -0,24 110 0,32 672 1,23 0,77 537
- И.6 0,2 577 0,1 861 0,1 395 0,6 593 0,3 611 0,5 241 -0,383 0,9 374 0,14 431 0,9 732
- И., кЧ Группа обрабатываемого материала1 2 3 4 5 6 7 8 9 10кО 1,27 520 0,89 774 1,217 1,31 964 1,47 259 1,40 774 0,96 430 1,87 811 0,33 202 0,94 819
- И. -1,33 805 -1,45 339 -1,34 702 -1,45 792 -1,61 111 -1,70 556 -0,93 310 -2,7 289 -1,12 617 -1,21 293
- Ы2 -0,3 342 -0,1 114 -0,1 225 -0,764 -0,1 837 -0,2 497 0,427 0,2 498 0,2 044 -0,811кВ -0,17 318 -0,28 272 -0,23 601 -0,18 849 0,3 335 -0,38 811 0,3 633 -0,59 624 0,10 719 -0,3 239
- Ш 1,3 462 1,90 810 1,8095 В 1,87 946 1,57 051 1,49 789 0,59 260 1,36 421 -1,19 603 -0,16 037
- И5 0,22 313 0,32 789 0,63 365 0,49 243 1,2 614 1,4 733 0,25 183 0,11 272 0,74 494 0,37 447
- М.6 0,905 0,3 533 0,110© 0,5 458 0,11 135 0,11 912 0,11 124 0,8 445 0,10 204 0,4 197
- Ш 0,20 731 0,18 259 -0,1 792 0,12 480 0,27 470 0,21 706 -0,23 045 -0,35 801 0,1 175 0,12 369
- И. -1,39 639 -1,48 014 -1,58 543 -1,55 246 -1,41 159 -1,42 399 -1,12 691 -1,59 398 -1,12 254 -1,4 918
- И2 -0,909 -0,955 -0,2 603 -0,3 885 0,382 -0,3 088 0,2 772 -0,4 568 0,2 082 0,697
- ИЗ -0,16 581 -0,17 884 -0,24 771 -0,28 964 -0,19 544 -0,44 705 0,27 083 -0,35 619 0,10 787 0,24 141
- И.4 1,9 191 1,9 116 3,2 893 1,96 249 1,74 818 1,81 579 0,72 365 -0,44 640 -0,70 253 0,141 031. 0,34 730 0,34 503 0,29 975 0,69 763 0,37 132 0,47 671 -0,24 110 -0,45 516 1,23 0,77 537
- KL6 0,2 577 0,1 861 0,1 395 0,6 593 0,3 611 0,5 241 -0,383 -0,8 164 0,14 431 0,9 732 т 0,24 562 0,23 282 0,27 620 0,28 826 0,13 765 0,19 889 -0,8 442 0,54 793 -0,6 813 0,4 632
- И.8 0,87 430 0,84 565 0,32 878 0,36 327 3,3 925 1,25 568 1,52 254 -1,20 081 4,5 454 3,54 009
- И. -1,36 144 -1,45 444 -1,52 748 -1,56 741 -1,56 974 -1,53 283 -1,15 931 -1,84 106 -1,9 230 -1,10 673
- И2 -0,455 -0,597 -0,1 496 -0,1 743 -0,3 167 43,3 147 0,1 063 -0,5 945 0,2 771 0,638
- ЫЗ -0,18 124 -0,16 302 -0,19 897 -0,29 367 -0,19 014 -0,30 161 0,16 504 0,31 508 0,221% 0,14 728
- И4 1,30 270 1,48 496 3,17 143 2,76 527 2,98 091 2,816© 1,26 513 -1,9 212 -1,10 962 -0,17 389
- И5 0,38 847 0,41 842 0,56 130 0,95 321 0,76 974 0,72 028 0,278 -0,52 283 0,88 483 0,60 508
- М.6 0,3 183 0,3 883 0,7 790 0,11 004 0,9 005 0,10 368 0,4 964 -0,8 855 0,12 443 0,7 150кТ7 0,21 895 0,20 832 0,7 814 0,129® 0,14 201 0,3 428 -0,13 595 0,63 361 -0,2 571 0,8 975
- И8 1,5 067 1,4 022 1,8 778 0,82 730 0,99 104 0,87 140 1,21 832 -1,37 935 1,96 512 2,40 435
- Ы. -1,32 677 -1,47 245 -1,45 766 -1,47 698 -1,82 771 -1,87 931 -0,95 216 -2,69 126 -1,14 523 -1,23 199
- Ы2 -0,3 342 -0,1 114 -0,1 225 -0,764 -0,1 837 -0,2 497 0,427 -0,3 968 0,2 044 -0,811
- ИЗ -0,17 318 -0,28 272 -0,23Ю1 -0,18 849 0,3 335 -0,38 811 0,3 633 0,12 966 0,10 719 -0,3 239ш 2,3 462 1,90 810 2,80 953 1,87 946 2,57 052 2,49 789 0,59 203 2,29 457 -1,19 803 -0,16 637
- Ы5 0,22 313 0,32 789 0,63 365 0,49 243 1,2 614 1,4 733 0,25 183 -1,14 267 0,74 494 0,37 447
- И.6 0,905 0,3 533 0,11 062 0,5 458 0,11 135 0,11 912 0,11 124 -0,19 156 0,10 204 0,4 197кГ7 0,20 731 0,18 259 -0,1 792 0,12 480 0,27 470 0,21 706 -0,23 045 0,61 082 0,1 175 0,12 369
- ИВ 1,24 278 1,4 126 1,14 466 2,33 831 3,65 277 3,31 155 1,7 286 -0,54 003 2,9 833 0,88 649