Системы машинного зрения
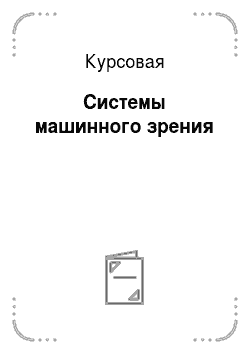
Системы машинного зрения запрограммированы для выполнения узкоспециализированных задач, таких как подсчет объектов на конвейере, чтение серийных номеров или поиск поверхностных дефектов. Польза системы визуальной инспекции на основе машинного зрения заключается в высокой скорости работы с увеличением оборота, возможности 24-часовой работы и точности повторяемых измерений. Так же преимущество… Читать ещё >
Системы машинного зрения (реферат, курсовая, диплом, контрольная)
- ВВЕДЕНИЕ
- 1. ОПИСАНИЕ АСУ
- 1.1 Структурная схема
- 2. ОПИСАНИЕ ПЕРВИЧНЫХ ДАТЧИКОВ
- 2.1 Весоизмерительная ячейка Siwarex R серии BB
- 2.2 Система технического зрения FZM1−350-ECT
- 3. ОПИСАНИЕ МИКРОКОНТРОЛЛЕРА
- 4. ОПИСАНИЕ СИСТЕМЫ ВВОДА-ВЫВОДА
- 4.1 Модульная станция ввода-вывода Simantic ET200S
- 4.2 Сенсорная панель Simantic TP 177B
- 5. ОПИСАНИЕ ОБЪЕКТА УПРАВЛЕНИЯ
- 6. ОПИСАНИЕ ИНТЕРФЕЙСА
- 7. АЛГОРИТМ ОПРОСА ДАТЧИКОВ
- 8. РАСЧЕТ НАДЕЖНОСТИ АСУ
- 9. ПОДГОТОВКА СТАТИЧЕСКИХ ДАННЫХ
- 10. РЕЗУЛЬТАТЫ, ПОЛУЧЕННЫЕ ПРИ ОБРАБОТКЕ ИСХОДНЫХ ДАННЫХ
- ЗАКЛЮЧЕНИЕ
- СПИСОК ЛИТЕРАТУРЫ
Системы машинного зрения запрограммированы для выполнения узкоспециализированных задач, таких как подсчет объектов на конвейере, чтение серийных номеров или поиск поверхностных дефектов. Польза системы визуальной инспекции на основе машинного зрения заключается в высокой скорости работы с увеличением оборота, возможности 24-часовой работы и точности повторяемых измерений. Так же преимущество машин перед людьми заключается в отсутствии утомляемости, болезней или невнимательности. Тем не менее, люди обладают тонким восприятием в течение короткого периода и большей гибкостью в классификации и адаптации к поиску новых дефектов.
Компьютеры не могут «видеть» таким же образом, как это делает человек. Фотокамеры не эквивалентны системе зрения человека, и в то время как люди могут опираться на догадки и предположения, системы машинного зрения должны «видеть» путем изучения отдельных пикселей изображения, обрабатывая их и пытаясь сделать выводы с помощью базы знаний и набора функций таких, как устройство распознавания образов. Хотя некоторые алгоритмы машинного зрения были разработаны, чтобы имитировать зрительное восприятие человека, большое количество уникальных методов были разработаны для обработки изображений и определения соответствующих свойств изображения.
Хотя машинное зрение — процесс применения компьютерного зрения для промышленного применения, полезно перечислить часто использовались аппаратные и программные компоненты. Типовое решение системы машинного зрения включает в себя несколько следующих компонентов:
1. Одна или несколько цифровых или аналоговых камер (черно-белые или цветные) с подходящей оптикой для получения изображений
2. Программное обеспечение для изготовления изображений для обработки. Для аналоговых камер это оцифровщик изображений
3. Процессор (современный ПК c многоядерным процессором или встроенный процессор, например — ЦСП)
4. Программное обеспечение машинного зрения, которое предоставляет инструменты для разработки отдельных приложений программного обеспечения.
5. Оборудование ввода/вывода или каналы связи для доклада о полученных результатах
6. Умная камера: одно устройство, которое включает в себя все вышеперечисленные пункты.
7. Очень специализированные источники света (светодиоды, люминесцентные и галогенные лампы и т. д.)
8. Специфичные приложения программного обеспечения для обработки изображений и обнаружения соответствующих свойств.
9. Датчик для синхронизации частей обнаружения (часто оптический или магнитный датчик) для захвата и обработки изображений.
10. Приводы определенной формы используемые для сортировки или отбрасывания бракованных деталей.
Датчик синхронизации определяет, когда деталь, которая часто движется по конвейеру, находится в положении, подлежащем инспекции. Датчик запускает камеру, чтобы сделать снимок детали, когда она проходит под камерой и часто синхронизируется с импульсом освещения, чтобы сделать четкое изображение. Освещение, используемое для подсветки деталей предназначено для выделения особенностей, представляющих интерес, и скрытия или сведения к минимуму появление особенностей, которые не представляют интереса (например, тени или отражения). Для этой цели часто используются светодиодные панели подходящих размеров и расположения.
Изображение с камеры попадает в захватчик кадров или в память компьютера в системах, где захватчик кадров не используется. Захватчик кадров — это устройство оцифровки (как часть умной камеры или в виде отдельной платы в компьютере), которое преобразует выходные данные с камеры в цифровой формат (как правило, это двумерный массив чисел, соответствующих уровню интенсивности света определенной точки в области зрения, называемых пикселями) и размещает изображения в памяти компьютера, так чтобы оно могло быть обработано с помощью программного обеспечения для машинного зрения.
Программное обеспечение, как правило, совершает несколько шагов для обработки изображений. Часто изображение для начала обрабатывается с целью уменьшения шума или конвертации множества оттенков серого в простое сочетание черного и белого (бинаризации). После первоначальной обработки программа будет считать, производить измерения и/или определять объекты, размеры, дефекты и другие характеристики изображения. В качестве последнего шага, программа пропускает или забраковывает деталь в соответствии с заданными критериям. Если деталь идет с браком, программное обеспечение подает сигнал механическому устройству для отклонения детали; другой вариант развития событий, система может остановить производственную линию и предупредить человека работника для решения этой проблемы и сообщить, что привело к неудаче.
Хотя большинство систем машинного зрения полагаются на «черно-белые» камеры, использование цветных камер становится все более распространенным явлением. Кроме того, все чаще системы машинного зрения используют цифровые камеры прямого подключения, а не камеры с отдельным захватчиком кадров, что сокращает расходы и упрощает систему.
«Умные» камеры со встроенными процессорами, захватывают все большую долю рынка машинного зрения. Использование встроенных (и часто оптимизированных) процессоров устраняет необходимость в карте захватчика кадров и во внешнем компьютере, что позволяет снизить стоимость и сложность системы, обеспечивая вычислительную мощность для каждой камеры. «Умные» камеры, как правило, дешевле, чем системы, состоящих из камеры, питания и/или внешнего компьютера, в то время как повышение мощности встроенного процессора и ЦСП часто позволяет достигнуть сопоставимой или более высокой производительности и больших возможностей, чем обычные ПК-системы.
1. ОПИСАНИЕ АСУ
1.1 Структурная схема
На рисунке 1 представлена структурная схема автоматической системы управления промышленным роботом.
Рисунок 1 — Схема АСУ
Рисунок 2 — Структурная схема АСУ Управление производственной подсистемой реализовано на базе SCADA-системы WinCC компании Siemens и промышленных контроллеров Simatic S7-315 °F, станций распределённого ввода/вывода ET200S, сенсорных дисплеев TP177B. Также здесь используются элементы системы безопасности Safety Integrated на основе световых барьеров и средств сигнализации.
Объект управления состоит из двух РТК, которые имитируют изготовление деталей и сборку. Первый РТК включает робот-манипулятор, транспортёр с позицией обработки, систему взвешивания Siwarex, магазин для хранения заготовок, готовых и бракованных деталей. Второй РТК состоит из пневматического сборочного центра, поворотного стола, транспортёра, системы взвешивания Siwarex и робота-манипулятора. Два МР перемещают модели заготовок и готовых деталей между РТК. Система управления МР через беспроводной интерфейс интегрирована с системой WinCC и системой технического зрения.
Системы технического зрения и взвешивания позволяют имитировать функционирование производственной подсистемы анализа качества выпускаемых изделий. Результаты передаются в систему SAP ERP, где определяется и анализируется эффективность производства.
2. ОПИСАНИЕ ПЕРВИЧНЫХ ДАТЧИКОВ
В рассматриваемой АСУ датчиками являются весоизмерительная ячейка SIWAREX R серии ВВ и система технического зрения FZM1−350-ECT.
2.1 Весоизмерительная ячейка SIWAREX R серии ВВ
Весоизмерительная ячейка на базе гибкого стержня, для эксплуатации в небольших резервуарах и платформенных весах. Измерительный элемент представляет собой двойную изгибную полосу из нержавеющей стали, на которой расположены 4 расширительных измерительных полоски (DMS).
DMS установлены таким образом, что две из них работают на растяжение, а две других на сплющивание.
За счет воздействия нагрузки на измерительном направлении пружинное тело и связанные с ним DMS эластично деформируются. При этом вырабатывается измерительное напряжение пропорциональное нагрузке.
Таблица 1
Технические характеристики весоизмерительной ячейки SIWAREX R серии ВВ
Ном. нагрузка/макс. нагрузка Емакс | 10/20/50/100/200/350 кг | |
Напряжение питания | 5 … 15 В | |
Входное сопротивление Re | 460Щ±50Щ | |
Выходное сопротивление Ra | 350Щ±3,5Щ | |
Время наработки на отказ | 20 000 ч | |
Время наработки на отказ | 350 000 ч | |
2.2 Система технического зрения FZM1−350-ECT
Технологии обработки изображений оптимизированы для решения задач позиционирования. Позиционирование объектов по форме: разделение скрепленных объектов, обнаружение частично скрытых объектов, компенсация скругленных или поврежденных кромок, проверка царапин и дефектов, обнаружение загрязненных или перекрывающихся объектов, проверка повреждений кромок и углов.
Таблица 2
Технические характеристики системы технического зрения FZM1−350-ECT
Типы используемых камер | Высокоскоростные цифровые камеры с автофокусом | |
Интерфейс | RS-232C, Ethernet 100BASE-TX/10BASE-T, USB (1.1 и 2.0) | |
Интерфейс видео выхода | аналоговый RGB одноканальный видео-выход (1024×768) | |
Напряжение питания | 20.4. 26.4 В | |
Время наработки на отказ | 50 000 ч | |
3. ОПИСАНИЕ МИКРОКОНТРОЛЛЕРА
В данной АСУ используется микроконтроллер Simantic S7-300 °F. Программируемый контроллер для построения распределенных систем автоматики безопасности. В этом микроконтроллере применяется CPU 315F-2DP с встроенными функциями автоматики безопасности и интерфейсом PROFIBUS DP, поддерживающим профиль PROFIsafe, реализованы стандартные функции управления с функциями автоматики.
микроконтроллер модульный зрение весоизмерительный
Таблица 3
Технические характеристики микроконтроллера Simantic S7-300 °F CPU 315−2DP
Память | Встроенная RAM 128 Кбайт | |
Минимальное время выполнения операций | логических операций — 0,1 мкс операций со словами — 0,2 мкс арифметических операций с фиксированной/плавающей точкой — 2,0/3,0 мкс | |
Интерфейс | RS 485, Industrial Ethernet | |
Соединитель | 9-полюсное гнездо соединителя D-типа | |
Потребляемый ток | 200мА/=15…30В | |
Время наработки на отказ | 100 000 ч | |
4. ОПИСАНИЕ СИСТЕМЫ ВВОДА-ВЫВОДА
Системы ввода вывода представлены модульной станцией ввода-вывода Simantic ET200S и человеко-машиным интерфейсом реализованным с помощью сенсорной панели Simantic PT 177B.
4.1 Модульная станция ввода-вывода Simantic ET200S
Станции ET200S используются для построения систем распределенного ввода-вывода программируемых контроллеров SIMATIC S7−300/ S7−400/ WinAC/ C7, базирующихся на промышленных сетях PROFIBUS DP или PROFINET IO.
Обширный спектр модулей различного назначения позволяет оптимально адаптировать станции ET200S к требованиям решаемой задачи. Интерфейсные модули обеспечивают возможность непосредственного подключения станции к электрическим или оптическим каналам связи PROFIBUS DP, а также электрическим каналам связи Industrial Ethernet, выполнять предварительную обработку данных на уровне станции, обеспечивать поддержку профиля PROFISafe в распределенных системах автоматики безопасности. При работе в системах распределенного ввода-вывода программируемых контроллеров S7−400 обеспечивается поддержка функций «горячей» замены как электронных, так и силовых модулей.
Таблица 4
Технические характеристики модульной станциии ввода-вывода Simantic ET200S
Интерфейс | PROFIBIUS DP, RS 485/- (интерфейсный модуль IM 151−1) | |
Объем данных на телеграмму ввод/вывод | 244/244 | |
Напряжение питания | 24В | |
Время наработки на отказ | 100 000 ч | |
4.2 Сенсорная панель Simantic TP 177B
Сенсорные панели оператора SIMATIC серии 177 предназначены для построения систем человеко-машинного интерфейса и решения задач оперативного управления и мониторинга. Панели могут использоваться с программируемыми контроллерами SIMATIC S7−200/ S7−300/ S7−400, системами компьютерного управления SIMATIC WinAC, программируемыми контроллерами других фирм.
Таблица 5
Технические характеристики сенсорной панели Simantic TP 177B
Интерфейсы | USB, RS 422, PROFIBUS DP, Ethernet | |
Количество обслуживаемых контроллеров | до 4 | |
Время наработки на отказ | 50 000 ч | |
5. ОПИСАНИЕ ОБЪЕКТА УПРАВЛЕНИЯ
Объект управления представлен промышленным роботом Юнимен-3000. Промышленный робот «Юнимен-3000» имеет шесть степеней свободы, из них четыре у руки (перемещение по горизонтали и вертикали, а также поворот относительно двух осей) и две у кисти (качание и захват). Поворот руки может выполняться одновременно с горизонтальным перемещением.
Робот «Юнимен-3000» работает в цилиндрической системе координат. Манипулятор, пульт управления и гидравлический узел смонтированы раздельно.
Большая грузоподъемность робота позволяет использовать его для транспортировки тяжелых деталей и узлов.
Таблица 6
Технические характеристики промышленного робота Юнимен-3000
Максимальная грузоподъемность | 200 кг | |
Масса робота | 1 900 кг | |
Интерфейс | RS 485 | |
Напряжение | 220 В | |
Время наработки на отказ | 150 000 ч | |
6. ОПИСАНИЕ ИНТЕРФЕЙСА
Так как рассматриваема АСУ базируется на промышленном контроллере Simantic компании Siemens AG, то система передачи данных в АСУ основа на открытой промышленной сети PROFIBUS (PROFIBUS DP — профиль протоколов этой сети), разработанной этой же компанией Siemes AG.
На физическом уровне интерфейс представлен электрической сетью с шинной топологией, использующей экранированную витую пару, соответствующую стандарту RS-485.
Так же устройства данной АСУ поддерживают интерфейс Ethernet.
Таблица 7
Технические характеристики протокола PROFIBUS DP
Архитектура | ISO/OSI | |
Тип передачи данных | циклический | |
Интерфейс | RS 485 | |
Таблица 8
Технические характеристики интерфейса RS-485
Стандарт | EIA RS-485 | |
Физическая среда | Витая пара | |
Максимальная скорость передачи | 100Кбит/с — 10 Мбит/с | |
Напряжение | — 7 В до +12 В | |
Тип разъема | не специфицирован | |
7. АЛГОРИТМ ОПРОСА ДАТЧИКОВ
Рисунок 3 — Блок схема алгоритма опроса датчиков
Алгоритм опроса датчиков
1. Подготовка к началу работы.
2. Оператор вводит техническое задание (набор значений управляемых параметров координаты позиционирования x0, y0, z0). Система производит опрос датчиков для получения текущих значений управляемых параметров (x, y, z).
3. Система передает значения управляемых параметров (заданных и текущих) в микроконтроллер.
4. В микроконтроллере на основе разности между значениями управляемых параметров вырабатывается управляющий сигнал g ((x-x0),(y-y0),(z-z0)). Управляющий сигнал поступает в мобильный робот, после получения управляющего сигнала происходит изменение значений управляемых величин (V[g ((x-x0),(y-y0),(z-z0))]).
5. Система опрашивает датчики, для получения текущего значения управляемых параметров.
6. Текущие значения поступают в микроконтроллер, где происходит их сравнения с заданными. Если значения совпадают, то система вырабатывает сигнал прерывания и выводит на экран сообщение о выполнении (пункт 7,8). Если значения не совпадают, то система возвращается к пункту 3.
8. РАСЧЕТ НАДЕЖНОСТИ АСУ
Для расчета надежности предоставления информации составим сводную таблицу всех элементов системы с указанием из времени наработки на отказ.
Таблица 9
Сводная таблица элементов системы
Элементы | Время наработки на отказ, ч | |
SIWAREX R | 350 000 | |
SIMANTIC TP 177B | 50 000 | |
ET200S | 100 000 | |
Simantic S7−300 CPU 315−2DP | 200 000 | |
FZM1−350-ECT | 50 000 | |
Юнимен-3000 | 150 000 | |
Построим кривую надежно предоставления информации. Функция описывающая эту кривую имеет вид:
где, Tn — время наработки на отказ элемента.
.
Рисунок 4 — Кривая надежного предоставления информации
Оценим вероятность надежного предоставления информации в течение 10 000ч. Из графика видно, что значение данной вероятности примерно составляет 52.5%.
Оценим доверительную вероятность для уровня вероятности 0,999
Рисунок 5 — Доверительная вероятность
Время в течение, которого надежность предоставления информации будет выше уровня вероятности 0,999, составляет 15 часов.
9. ПОДГОТОВКА СТАТИЧЕСКИХ ДАННЫХ О ВРЕМЕНИ НАРАБОТКИ И ВРЕМЕНИ ВОССТАНОВЛЕНИЯ КОМПОНЕНТА ССОИ. РАСЧЕТ ОЦЕНКИ СРЕДНЕЙ НАРАБОТКИ НА ОТКАЗ (Т0)
В качестве исходных данных возьмем следующие данные:
Таблица 10
Номера прерываний
Номера прерываний и восстановлений работоспособности ССОИ | |||||||||
Номер документа (i) | Начало работы Конец работы | ||||||||
tН1 | 10.00.00 | 10.31.34 | 11.03.45 | 11.21.11 | 11.45.11 | 12.30.00 | |||
tК1 | 10.21.12 | 10.51.15 | 11.12.54 | 11.41.23 | 12.25.43 | 13.30.00 | |||
tвi | |||||||||
Таблица 11
Время обработки запросов
Номер запроса (i-го) | Обозначение показателя | Номер s-го замера времени обработки i-го запроса Время обработки | |||||||
s | |||||||||
ts (00мин.00с.) | 14.14 | 14.17 | 14.06 | 14.13 | 14.17 | 14.14 | 14.15 | ||
На основании исходных данных (таблица 10), произведем расчет суммарного (общего) времени пребывания системы в работоспособном состоянии:
где N = 6 — суммарное за период испытаний количество прерываний работоспособного функционирования;
thl — момент времени фактического начала работы после наступления
(l-1)-го прерывания;
tkl — момент времени фактического окончания работы при наступлении l-го прерывания.
Переведем время данное в таблице в секунды и подсчитаем ТPi:
tkl — thl=1272 с
tk2 — th2=1181 с
tk3 — th3=549 с
tk4 — th4=1212 с
tk5 — th5=2432 с
tk6 — th6=3600 с
Рассчитаем среднюю наработку на отказ по формуле:
где Tpi — суммарное (общее) время пребывания АИС в работоспособном состоянии;
k — суммарное число отказов.
k=6
Расчет оценки среднего времени восстановления.
Рассчитаем среднее время восстановления в работоспособное состояние после отказа:
где k = 5 — число отказов, после которых происходило восстановление во время испытаний;
tbi — время восстановления после j-го отказа.
tb1=622 c
tb2=752 c
tb3=497 c
tb4=228 c
tb5=257 c
Расчет оценки среднего времени реакции ССОИ на получение входного сигнала.
Вычислим среднее время реакции:
где m = 7 — количество замеров времени обработки запросов i-го типа (табл.11.);
tis время обработки входной информации (табл. 11.).
Расчет значения коэффициента готовности ССОИ.
Произведем расчет значения коэффициента готовности:
Расчет оценки вероятности надежного преобразования входной информации.
Вероятность рассчитывается по формуле:
где Toi и Tbi — среднее время наработки на отказ и восстановления после отказа;
Tpeaк.i — среднее время реакции Определение значения доверительной вероятности б для интервала оценивания.
В качестве значения доверительной вероятности б возьмем значение б=0,999 для повышения точности расчетов.
Определение значения доверительной вероятности для интервала оценки Расчет нижней и верхней доверительных границ для показателя наработки на отказ можно произвести по формулам:
где коэффициенты r1(k, a) = 6,68 и r3(k, a) = 0,27 берутся из табл. 1.1. и 1.2. в приложении 1;
Toi= 1707,66 с — оценка б = 0,999 — доверительная вероятность.
Расчет нижней и верхней доверительных границ для показателя времени восстановления работоспособности АИС производится по формулам:
где коэффициенты r1 (k, a) = 6,68 и r3(k, a) = 0,27;
Tbi = 471,2 с — оценка.
Расчет нижней и верхней доверительных границ для показателя коэффициент готовности производится по формулам:
,
,
где с — нижняя доверительная граница для показателя наработки на отказ;
с — верхняя доверительная граница для показателя наработки на отказ;
с — нижняя доверительная граница для показателя времени восстановления работоспособности;
с — верхняя доверительная граница для показателя времени восстановления работоспособности;
Расчет нижней и верхней доверительных границ вероятности надежного представления запрашиваемой выходной информации производится по формулам:
10. РЕЗУЛЬТАТЫ, ПОЛУЧЕННЫЕ ПРИ ОБРАБОТКЕ ИСХОДНЫХ ДАННЫХ
Сведем полученные данные в таблицу.
Таблица 12
Результаты обработки исходных данных.
Среднее время наработки на отказ, с | Среднее время восстановления работоспособности после отказа, с | Коэффициент готовности | Вероятность надежного преобразования запрашиваемой входной информации за время равное 8 часам. | |||||||||
453,06 | 1707,66 | 11 470,16 | 127,22 | 471,2 | 3147,61 | 0,12 | 0,78 | 0.99 | 0,044 | 0.665 | 0,92 | |
ЗАКЛЮЧЕНИЕ
Анализ графика аппаратной части АСУ показывает, что при заданном уровне надежности б=0.999 система находится в работоспособном состоянии течении 16 часов. Что является крайне не высоким показателем. Для повышения времени работы автоматизированной системы управления, необходимо, например, поменять датчики на более надежные. Также, при анализе надежного предоставлении информации в течении 10 000 часов, система показывает невысокую надежность 0,53.
Во второй части данной курсовой работы мы произвели расчет нижней
() и верхней () доверительных границ вероятности надежного представления запрашиваемой выходной информации: они составили 0,044 и 0,92 соответственно. Значит, рассматриваемая нами будет работать надежно, без сбоев в течение заданного промежутка времени.
1. Линаев В. В, Сертификация информационных технологий программных средств и баз данных, Казань, 2010
2. Костогрызов А. И., Петухов А. В., Щербина А. М. Основы оценки, обеспечения и повышения качества выходной информации в АСУ организованного типа, М.: «Вооружение. Политика. Конверсия», 1994.
3. Климов Г. П. Теория вероятности и математическая статистика М.: МГУ, 1983.
4. Вентцель Е. Г. Теория вероятностей, М.: Наука, 2009.
5. Шор Я. Б. Статические методы анализа и контроля качества и надежности, М.: Сов. радио, 1962.
6. www.sta.ru