Исследование и разработка эффективной технологии получения элементарной серы из отходящих газов автогенных процессов плавки металлургического сырья
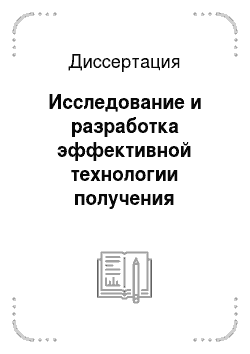
Диссертация
Исследование процесса конденсации серы в газотрубных конденсаторах серы позволили установить, что степень улавливания серы составляет 60−85%. При этом в отходящих газах теряется элементарная сера 15−40%, которую необходимо улавливать в сероуловителях. В этой связи целесообразно использовать жидкофазный метод очистки отходящих газов, который не только позволит проводить дополнительную конверсию… Читать ещё >
Содержание
- ПРЕДИСЛОВИЕ
- 1. АНАЛИТИЧЕСКИЙ ОБЗОР СПОСОБОВ ПОЛУЧЕНИЯ ЭЛЕМЕНТАРНОЙ СЕРЫ ИЗ СЕРНИСТЫХ ГАЗОВ
- 1. 1. Восстановление Б02 твердыми восстановителями
- 1. 2. Восстановление БОг газообразными восстановителями
- 1. 2. 1. Восстановление сернистого ангидрида метаном
- 1. 2. 2. Восстановление сернистого ангидрида сероводородом с получением серы методом Клауса. 1.3. Аппаратурное оформление метанового способа получения серы
- 1. 4. Основные переделы пирометаллургнческого производства и характеристика отходящих газов
- 1. 4. 1. Отражательная плавка
- 1. 4. 2. Плавка во взвешенном состоянии
- 1. 4. 3. Кислородно-факельная плавка
- 1. 4. 4. Плавка Вашокова (ПВ)
- 2. 1. Механизм процесса и термодинамические расчеты с целыо определения необходимой концентрации кислорода в исходном газе для реализации метанового способа получения серы
- 2. 2. Схема лабораторной установки и методика проведения эксперимента
- 2. 3. Результаты лабораторных исследований процесса восстановления
- 3. 1. Описание полупромышленной установки для проведения исследований и отработки технологии высокотемпературного восстановления сернистого ангидрида природным газом
- 3. 2. Подготовка установки к пуску и методика проведения исследований высокотемпературного восстановления БОг природным газом
- 3. 3. Результаты исследований высокотемпературного восстановления БОг природным газом в полупромышленных условиях
- 3. 3. 1. Определение физико-химических условий высокотемпературного восстановления БО: природным газом
- 3. 3. 2. Результаты исследований переработки восстановленного газа, содержащего сероводород и диоксид серы методом Клауса
- 3. 3. 3. Исследование процесса конденсации и улавливания серы из газов
- 4. 1. Расчет состава и количества отходящих газов промышленного комплекса ПВ
- 4. 2. Технологическая схема промышленной установки получения серы (внепечное восстановление SO2)
- 4. 3. Материальный и тепловой балансы высокотемпературного реактора восстановления SO2 природным газом
- 4. 4. Результаты исследований процесса восстановления SO2 на промышленном реакторе
- 5. 1. Высокотемпературное восстановление сернистого ангидрида угольной пылью
- 5. 1. 1. Описание схемы процесса получения серы восстановлением SO в аптейке ПВП (впутрипечное восстановление)
- 5. 1. 2. Технологические показатели процесса
- 5. 2. Высокотемпературное восстановление сернистого ангидрида природным газом
- 5. 2. 1. Схема подачи природного газа в аптейк ПВП
- 5. 2. 2. Исследование температурного режима в аптейке ПВП при восстановлении сернистого газа метаном
- 5. 2. 3. Разработка схемы подачи природного газа для восстановления сернистого ангидрида в аптейке печи взвешенной плавки
- 5. 2. 4. Результаты испытаний восстановления SO2 в аптейке ПВП
- 5. 3. Определение температурного режима стадии «горячего» катализа после замены восстановителя SO2 пылевидного угля на природный
- 5. 4. Методика определения запыленности восстановленного газа, содержащего серу
- 6. 1. Результаты лабораторных исследований с целью определения физико-химических условий проведения процесса
- 6. 2. Проведение исследований каталитического восстановления SO2 природным газом в полупромышленных условиях в горизонтальном реакторе. щ 6.2.1. Методика проведения эксперимента
- 6. 2. 2. Результаты эксперимента и обсуждение опытных данных
- 6. 3. Результаты полупромышленных исследований процесса каталитического восстановления сернистого ангидрида природным газом в вертикальном реакторе с горизонтальным слоем катализатора
- 6. 4. Технологическая схема каталитического восстановления БОг
- 6. 5. Технологический расчет опытно-промышленного каталитического реактора
- 6. 6. Восстановление БОг конверсированным газом с получением элементарной серы
- 6. 6. 1. Получение конверсированного газа в полупромышленных условиях
- 6. 6. 2. Восстановление БОг конверсированным газом в каталитическом реакторе
- 7. 1. Жидкофазные способы очистки отходящих газов
- 7. 2. Результаты лабораторных исследований взаимодействия Нг8 и БОг в воде
- 7. 3. Результаты исследований процесса доочистки сернистых газов методом жидкофазной конверсии на полупромышленной установке
Список литературы
- Tarasov A.V., Paretsky V.M., Mechev V.V., Autogtnous Smelting of Sul-Щ phide Concentrates, Transactions of the Technical University of Koshitse, 1. sue of
- Rechansk Science Publishing Company Vol. 2, special issue, Cambridge, 1992, 47−56.
- Tarasov A.V., Bystrov V.P., Smelting of Nickel Ores and Concentrates Using Vanyukov Process, Extractive Metallurgy of Copper, Nickel and Cobalt, Pro-1 ceeding of the Paul E. Queneau International Symposium Vol. I, Fundamental
- Aspekts, Denver, 1993, 659−666.
- Сигедин B.H., Аранович В. Л., Довченко B.A., Руденко Б. И., Хасанов А. С. // Цветные металлы. 1999. — № 4. — С. 36−39.
- Вашоков А.В., Быстров В. П. и др. Плавка в жидкой ванне. М.: Металлургия, 1988.
- Бабаджан А.А., Мальцев Б. В. Производство черновой меди. Свердловск, Металлургиздат, 1961.
- Еремин О.Г., Добросельская Н. П. Способы улавливания и утилизации слабоконцентрированных сернистых газов. М., ЦНИИНЦМ. — 1971. — 96 с.
- Еремин О.Г., Добросельская Н. П. Способы очистки металлургических газов при производстве серной кислоты. -М., ЦНИИЦМ. 1972. — 95 с.
- Васильев Б.Г., Отвагина М. И. Технология серной кислоты. М., Химия. — 1985. — 385 с.
- Филатова Н.С., Чертков Б. А., Еремин О. Г. Промышленность минеральных удобрений и серной кислоты. Реферативная информация, выпуск 5. -М., 1974.-С. 15−18.
- Боресков Г. К., Матрос Ю. Ш., Алентов П. Н., Еремин О. Г. и др. Не*стационарный способ производства серной кислоты из отходящих металлур-ф' гических газов. // Цветные металлы. 1984. — № 2. — С. 28−31.
- Yeremin J.G., Tarasov A.V. Removal of Sulfur dioxide from low-concentration off-gases. Proceedings of the Sulfur 2000 International conference,
- San-Francisco USA, 0ct-2000, pp. 373−382.
- Еремин О.Г., Андрианова 3.B., Иванов И., Балашова Г. Ф. Исследование абсорбции SO? суспензией окиси цинка. // Исследования в области производства серной кислоты. Тр. НИУИФ, выпуск 225. С. 205−210.
- Садиленко А.К., Амелин А. Г., Илларионов В. В., Воротников А. Г. Окисление сернистого ангидрида в отходящих газах ТЭЦ. // Исследования вф области производства серной кислоты. Тр. НИУИФ, выпуск 225. С. 143 149.
- Тарасов A.B., Еремин О. Г. Анализ зарубежного опыта по очистке газов от сернокислотного тумана при производстве серной кислоты. // Цветные металлы. 2002. — № 5. — С. 40−43.
- Тарасов A.B. Развитие технологий в цветной металлургии России. // Цветные металлы. 2001. — № 6. — С. 70−75.
- Грунвальд В.Р. Технология газовой серы. М., Химия. — 1992. — 272с.
- Менковский М.А., Яворский В. Т. Технология серы. М., Химия. -1985.-326 с.
- Князев М.В. Расширение использования печи Ванюкова в техноло-^ гни металлургического производства. // Цветные металлы. 2000. — № 6. — С.31.32.
- Еремин О.Г., Еремина Г. А. О получении серы из отходящих металлургических газов. // Цветные металлы. 2000. — № 3.- С. 26−28.
- Авдеева А.В. Получение серы из газов. -М., 1977.
- Розенкноп З.П. Извлечение двуокиси серы из газов. Госхимиздат, 1952.
- Справочник сернокислотчика. -М.: Химия. 1971.
- Murden К.В. Paper present at AIME annual Meeting, San Francisca, Feb. 1972.
- Вилесов Н.Г. Очистка выбросных газов. Изд. Техника, Киев, 1971.
- Еремина Г. А. Канд. дис. НИУИФ. -М., 1969.
- Авербух Т.Д., Бакина Н. П. и др. Хим. промышленность № 10, 1968, с. 2и№ 3, 1971, с. 200.
- Sulphur. 1965. — N 58. — 9−14.
- Юшкевич Н.Ф., Каржавин В. А. ЖХП. 15. — 9. — 719. — 1926.
- Юшкевич Н.Ф., Каржавин В. А. ЖХП. -8.-2.- 109.- 1931.
- Амирова С.А. Канд. дис. УНИХИМ. Свердловск, 1951.
- Юшкевич Н.Ф., Каржавин В. А. ЖХП. -8.-1.-3.-1931.
- Юшкевич Н.Ф., Каржавин В. А. ЖХП. 12, 6, 474, 1926- 13, 7, 559, 1926.
- Applebey М., Journal of the Soc. of Chem. Ind., 56, 5, 139T, 1937.
- Описание технологии получения элементарной серы из обжиговых газов (по материалам ПНР). Перевод Гипроцветмета, М., 1958.
- Хиросэ Кадзутое, Коге Катаку дзасси, 63, 6, 906−911. 1960.
- Roesner G. Пат. ФРГ 936 505.15.12.55
- King R.A. Ind. Eng. Chem. 42, 11, 2241, 1950.
- Advances in extractive metallurgy and refining edited by M.J. Jones. The Institution of Mining and Metallurgy, London, 1972, p. 529−548.
- Sulphur, 1971, N96, p. 16.
- Metals Weeb, 1972, March, 20, p. 3.
- Юшкевич Н.Ф., Каржавин В. А., Авдеева А. В. ЖХП, 9, 3, 17, 1932.
- Юшкевич Н.Ф., Каржавин В. А., Авдеева A.B. и др. ЖХП, 11, 2, 33, 1934.
- Юшкевич Н.Ф., Каржавин В. А., Авдеева A.B. и др. ЖХП, 10, 8, 50,1933.
- Авдеева A.B. ЖХП, 15, 1077, 1937.
- Walker S. Ind and Eng. Chem. 38, 9, 906, 1946.
- Кушнир C.B. Канд. дне. Львов, 1956.
- Baccaredds М. la Chimica е L’Industria, 41,4,277,1959.
- Назаров И.И., Каверзнева Е. Д. Журнал ВХО 1,101, 1956.
- Siller W. Ind. Eng. Chem. 40, 1227, 1948.
- Doumani Т. Пат. США, 2, 361, 825, 1941.
- Gvvelins Handbuch der anorg. Chem. Schwefer A. L. ief 2, 224, B. Lief, 1, 263, 1953.
- F. de Jann, Пат. Франции, 854 116, 1940.
- Чопорев Н.П., Самчук А. И. Хим. промышленность, 8, 468, 1958.
- Kulesar J., Knoble P., Srabo Z. Studia, Univ Babes Bobjai Chem. 3, 4, 207, 1958.
- Авдеева A.B., Боресков Г. К. Хим. промышленность, 4, 1, 1945.
- Preda М. Пат. Бельгии, 630, 584, 1963.
- Thumm W. Пат. ФРГ, 1 051 258, 1959.
- Chem Eng. 67
- Вилесов Н.Г., Лекае В. М., Кузнецов Ю.П. XimI4Ha промисловють, № 1,5, 1964.
- Fleming T.F., TittG.C. Ind. Engng. Chem., N 11,2249, 1950.
- Cam T.J., Tererbaugh A.D. J. Chem. Eng. Data 9, N 3, 455, 1964.
- Авербух Т.Д., Апахов H.A., Майдурова О. В., Бакина Н. П. и др. Хим. Щ} промышленность, № 4, 281, 1962.
- Sulphur N 49 (1963), N 50, 73 (1963).
- Вилесов Н.Г. Хим. технология, 1978, с. 63−64.
- Вилесов Н.Г. Хим. технология, 1979, 3, с. 3−5.
- Еремин О.Г. Меньше загрязнений больше серы. // Наука России. -Щ 1997.-№ 3.-С. 13−15.
- Пусько А.Г., Тарасова B.C. // Цветная металлургия. 1970. — № 2. -С. 252−28.
- CullonJ.T. Пат. США 3 615 231, 1971.
- Wroght S.P. Sulphur, N 100, 72−75, 1972.
- Шахтахтинский Г. Б. и др. Азерб. хим. журн. 1967, № 2, с. 107−110.
- Шахтахтинский Г. Б. и др. Исследования в области неорг. и хим. химии. Баку, 1971, 2-я часть, с. 67−99.
- Авербух Т.Д., Бакина Н. П., Алпатова JI.B. Хим. пром., 1971, № 3, с. 200−203.
- Еремина Г. А. и др. A.c. № 825 133 СССР. 1981.
- Вилесов Н.Г., Горбатых Г. А. Хим. пром. Украины, 2, 16, 1966.
- Горбатых Г. А., Терентьев Д. Ф., Вилесов Н. Г. Сб. техн. и эком, ин-форм., вып. 3, 102,1967.
- Вилесов Н.Г., Горбатых Г. А. Хим. пром, 3, 118, 1966.
- Еремина Г. А., Пашкина Я. А., Дубинский В. М. и др. Промышленная и санитарная очистка газов, № 5, 1978, с. 18−20.
- Еремина Г. А., Зальцман С. Я. и др. Науч. тр. Гинцветмета, 1987, с. 1522.
- Гольд С.М. Промышленная и санитарная очистка газов. 1983, № 4, с. 16−18.
- Pascal 1 Н. Sulphur, 1982, 160, N 5.
- Kinzie Н. Пат. США 4 147 763, 1979.
- Crotnendaal W. Пат. Великобритании 2 143 225, 1985. ф 84. Philipp А. Пат. Франции 2 373 324, 1976.
- Dypin Т. Int. Sulphur, 82, Conf. London, Vol. 1, 1982, с. 241−253.
- Mohtodi H.F. Chem. React. Eng. 1974, c. 612−625.
- Хитати И. Пат. Японии 58−153 519, 1983.
- Dapin Т. Пат. Франции 2 501 532, 1982.• 89. Hass R. Пат. США 4 432 961, 1984.
- Ройтер В.А., Голодей Г. И. Введение в теорию кинетики и катализа. Киев, Наукова думка, 1971.
- Алхазов Т.Г. А.с. 825 131 СССР, 5 и 16, 1981.
- Теснер П.А. Газовая промышленность, 1983, № 4, с. 12−13.
- Георгиев Богомил Петров и др. Пат. НРБ 10 080, 1962. tft 94. Рейган С. А., Буралова А. И. Хим. пром., 1, 20, 1963.
- Swinarski A., Wronkowski С. Przem. Chem. 41,6, 306, 1962.
- Gamson В., Elkins R. Chem. Eng., Progr., 49, 4, 1953.
- Maurice W. Пат. ФРГ 1 198 333, 1966.
- Ball W. Chem. Canada, 18, 11, 45, 1966.
- Pannetier G. Chimie Indust., 79, 2, 150, 1958.
- Wet E.J. Advances in Petroleum Chemistry and Refining, 6, 315, 466, 1962.
- Stull D., Ind. Eng. Chem. 41,9, 1968, 1949.
- Бродский Ю.Н. ЖХП, 3, 11, 1965.
- Munro A., Masdin E., Br. Chem. Eng., 12, 3,369, 1967.
- Muddarris Al. Пат. США 4 309 402, 1982.
- Dunning, Пат. США 2 760 848, 1956.
- Duecker, Пат. США 2 767 062, 1956.
- Hunt et al. Пат. США 3 702 884, 1972.
- Kunkel et al. Пат. США 4 035 476, 1977.
- Paskall H. Sulphur, 160, May/June, 1982.
- Some factors affecting the performance of Claus sulphur recovery plants. Sulphur, 115, Non/Dec. 1974.
- Gamson B.W. and Elkins R.H. Chem. Eng. Progr. V. 49, N 4, Apr. 1953,. p. 203.
- Goar B.G. Hydrocarbon Processing. July 1974, p. 129−132.
- Sulphur 112, May/June 1974, p. 54−55.
- Pearson M.J. Hydrocarbon Processing. Feb. 1973, p. 81−85.
- Burns R.A., Lippert R.B., Kerr R.K. Hydrocarbon Processing, November 1974, p. 181−186.
- Technical Bulletin 107. Claus catalyst tests Western Research d Development Ltd, Calgary, Alta.
- Conser R.E. The Oil and Gas Journal, 1, Apr., 1974, p. 67−70.
- Sulphur 110, Jan/Fed. 1974, p. 34−35.
- Sulphur 111, March/Apr. 1974, p. 44−53.
- Sulphur 97, November/December. 1971, p. 47
- Sulphur 101, July/August. 1972, p. 26−28.
- Fleming E. Fitt C. Ind. Eng. Chem., 1953, N 42, p. 2249−2256.
- Mining Engineering, 9, 1970, т. 2, p, 24.
- Mining Congress Journal, 1972, v. 58, N 8, p. 6.
- Вилесов Н.Г., Зальцман С.JI., Еремин О. Г. Получение серы из отходящих газов жидкофазными способами. -М.: ЦНИИНЦМ. 1979. 66 с.
- Раит Дж. Б. Sulphur, 1972, 5, 6.
- Хантер В.Д., Мицнер А.В. Engineering and Mining Jorn., июнь 1973, с. 117−120.
- Еремина Г. А., Менковский Г. А., Добросельская Н. П. Получение элементарной серы из металлургических газов за рубежом. М.-.ЦНИИНЦМ. — 1981.-38 с.
- Манн Е.Л. Electrical Word, ноябрь 1, 1972.
- Chem. Age International, 1972, v. 102, N2782, p. 11, 18.
- Cullom J.T. Пат. США, 1971.
- Skill Min. Rev. 1975, 64, N 26, c. 8.
- World Mining, 1972, April, 74.
- Hunter W.D., Jamesp, WRIGHT. Chemical Engineering. October 2, 1972.
- Hunter W.D., Michener AAV. Eng. Min. J. 174, June 1973, 117−120.
- Henderson J.M. Mining Congress Journal, 1973, v. 59, N 3, p. 59−62.
- Еремин О.Г., Еремина Г. A., Менковский M.A. Хим. промышленность 6, 1986, с. 352−353.
- Добросельская Н.П., Еремина Г. А. Цветная металлургия, 1973, № 15, с. 31−33.
- Sulphur, 100, 1972, с. 72−75.
- Пат. США 4 141 962, кл. 423−571.
- Fechner J. Пат. США 4 117 101, 1978.
- Allied Chem. Corp. Пат. США 3 865 927, 1975.
- Henricus J.A. Пат. США 3 495 941, 1980.
- Alliol Chem. Corp. Пат. США 375 551, 1973.
- Canadien Chem. process, 1971, N 2, p. 25.
- Quarm, Mining Magazin, Apr., 1972, v. 130, N 4.
- Chem. Eng., 1972, v. 79, N 22, p. 50−51.
- Еремин О.Г., Филатова H.C., Явор В. И. Основные направления научно-исследовательских работ Гинцветмета в области утилизации серы. // Цветные металлы. 1987. — № 7. — С. 20−23.
- Tarasov A.V., Yeremin O.G., Yeremina G.A. Sulfur production from exhaust gases from non-ferrous autogenous smelting processes // Nickel-Cobalt 97. International Symposium: Proceedings. Sudbury, Ontario, Canada (Aug. 1997). -Vol. III. P. 285−292.
- Tarasov A.V., Yeremin O.G. Production of sulfur from metallurgical offgases of autogenous processes. // Clean-Technology. Third Millennium Challenge International Mining and Environment Congress: Proceeding. Lima. Peru (Jul. 1999).-P. 225−231.
- Еремин О.Г., Еремина Г. А. Утилизация серы из отходящих газов цветной металлургии. // Цветные металлы. 1996. — № 4. — С. 21−23.
- Еремин О.Г., Калнин Е. И., Садыков В. И., Еремина Г. А., Ковган П. А. Получение элементарной серы из металлургических газов. // Сб. науч. тр. Гинцветмета № 47. М., 1979. — С. 202−207.
- Tarasov A.V., Yeremin O.G. Recovery of Elemental sulfur from smelter gases. // Proceedings of the Sulfur 2000 International Conference. San-Francisco, USA, (Oct. 2000). — P. 319−324.
- Tarasov A.V., Yeremin O.G. Catalytic reduction of metallurgical sulfur dioxide: a feasible alternative to smelter acid production. // Proceedings of the Sulfur 2002 International Conference. Vienna, Austria, (Oct. 2002).
- Ушаков К.И., Еремин О. Г., Калнин Е. И. и др. Переработка сернистых газов метановым способом с получением элементарной серы. // Цветные металлы. 1980. — № 2. — С. 34−37.
- Еремин О.Г., Дубинский В. М., Бонн В. А. и др. Исследование каталитического способа восстановления сернистого ангидрида метаном при переработке отходящих сернистых газов металлургических производств. // Сб. науч. тр. Гинцветмета. М., 1981. — С. 25−27.
- Tarasov A.V., Yeremin O.G. Improvement of technology for sulfur recovery from metallurgical gas. // Proceedings of the Sulfur 2003 International Conference. Banff, Canada, (Nov. 2003). — P. 223−227.
- Абрамов Н.П., Еремин О. Г., Барышев A.A., Зальцман C.JI., Кужель Б. И. Опыт освоения производства серы из отходящих газов печей взвешенной плавки на НГМК. // Цветные металлы. 1987. — № 7. — С. 26−28.
- Ушаков К.И., Еремин О. Г., Макаров Д. Ф. Разработка и внедрение метанового способа получения серы из отходящих металлургических газов. // Цветные металлы. 1982. — № 7. — С. 23−28.
- Еремин О.Г., Менковский M.А., Явор В. И. Разработка и внедрение прогрессивных методов утилизации богатых сернистых газов с получением серной кислоты и серы. // Цветная металлургия. 1983. — № 10. — С. 19−20.
- Еремин О.Г., Филатова Н. С., Бонн В. А. Полупромышленные испытания метанового способа получения серы при переработке влажных газов. // Тез. докл. II Всесоюзного совещания. Баку, 1984. — С. 27.
- Еремин О.Г., Филатова Н. С., Берман И. Ф. Результаты исследований по совершенствованию производства серы и серной кислоты из отходящих металлургических газов. // Цветная металлургия. 1984. — № 5. — С. 49−51.
- Еремин О.Г., Макаров Д. Ф., Абрамов Н. П. и др. Высокотемпературное восстановление сернистого ангидрида природным газом с получением элементарной серы. // Цветные металлы. 1990. — № 11. — С. 36−38.
- Еремин О.Г., Менковский М. А., Явор В. И. Разработка и внедрение прогрессивных методов утилизации богатых сернистых газов с получением серной кислоты и серы. // Химическая промышленность. 1986. — № 6. — С. 352−353.
- Еремин О.Г., Макаров Д. Ф. и др. Получение серы метановым способом из газов автогенной плавки. // Цветные металлы. 1992. — № 5. — С.10−12.
- Еремин О.Г., Макаров Д. Ф. и др. Об утилизации серы из отходящих газов цветной металлургии. // Цветные металлы. 1994. — № 5. — С. 25−27.
- Еремин О.Г., Кужель Б. И., Барышев A.A. и др. Пути совершенствования производства серы из отходящих газов печей взвешенной плавки Но
- Щ рильского горно-металлургического комбината. // Сб. науч. тр. Гинцветмета.-М., 1987.-С. 50−53.
- Мечев В.В., Абрамов Н. П., Соколов O.K., Еремин О. Г. и др. Разработка и освоение технологии получения серы из отходящих газов металлургических производств. // Цветные металлы. 1989. — № 7. — С. 69−72.
- Tarasov A.V., Yeremin O.G. Installation of sulfur granulation at the As. *t*1 trakhan gas refinery (Russia). // Proceedings of the Sulfur 2003 International
- Conference. Banff, Canada, (Nov. 2003). — P. 243−245.
- Боресков Г. К., Матрос Ю. Ш., Алентов П. Н., Еремин О. Г. и др. Нестационарный способ производства серной кислоты из отходящих металлургических газов. // Цветные металлы. 1984. — № 2. — С. 28−31.
- Иванов A.B., Ким И.А., Явор В. И., Еремин О. Г., Иванова И. Д. Состояние и задачи полной утилизации диоксида серы на АГМК. // Цветные металлы. 1987. — № 7. — С. 23−26.
- Еремин О.Г., Филатова Н. С., Савченко С. И. Утилизация отходящих сернистых газов металлургических производств с получением элементарной серы. // Нестационарные процессы в катализе: Тез. докл. III Всесоюзной конференции. Новосибирск, 1985.-С. 16.
- Еремин О.Г., Макаров Д. Ф. Разработка и освоение процесса получения серы из газов автогенных процессов. // Тез. докл. I Всесоюзной научно-технической конференции. М., 1988. — С. 40.
- A.c. 1 058 876 Способ получения элементарной серы. / Еремин О. Г., Менковский М. А., Филатова Н. С., Васина О. Д. Заявл. 02.02.1982 (ДСП).
- A.c. 1 157 013 Способ конверсии ЗОг-содержащих газов. / Еремин * О.Г., Зальцман СЛ. и др. Заявл. 04.06.1979.
- A.c. 1 528 723 Способ управления процессом восстановления сернистых газов металлургического производства. / Еремин О. Г., Филатов A.B.,
- Абрамов Н.П., Макаров Д. Ф., Розенберг Ж. И. и др. Заявл. 19.11.1987- Зарегистрировано 15.08.89.
- A.c. 1 549 000 Способ получения серы. / Еремин О. Г., Филатов A.B., Абрамов Н. П., Розенберг Ж. И. и др. Заявл. 27.05.1988- Зарегистрировано0811.89.
- A.c. 1 390 993 Способ получения элементарной серы. / Еремин О. Г., Хагажеев Д. Т., Абрамов Н. П., Розенберг Ж. И. и др. Заявл. 30.04.1987- Зарегистрировано 22.12.87.
- A.c. 1 469 769 Способ управления процессом восстановления сернистого ангидрида в производстве элементарной серы. / Еремин О. Г., Алентов П. Н., Розенберг Ж. И. и др. Заявл. 15.06.1987- Зарегистрировано 15.08.89.
- A.c. 1 769 935 Способ очистки отходящих газов от серы. / Мечев В. В., Еремин О. Г., Филатова Н. С., Калнин Е. И. Заявл. 18.07.1989- Опуб. 23.10.92. — Бюл. № 39.
- A.c. 1 823 218 Реактор для восстановления диоксида серы природным газом. / Еремин О. Г., Абрамов Н. П. и др. Заявл. 23.04.1991- Опуб. 1993. — Бюл. № 23.
- A.c. 1 616 034 Способ получения серы из сернистых газов. / Еремин О. Г., Абрамов Н. П., Барышев A.A., Макаров Д. Ф. Заявл. 11.08.1988- Зарегистрировано 22.08.90.
- A.c. 1 605 485 Способ получения серы. / Мечев В. В., Еремин О. Г., Барышев A.A., Козлов А. Н. и др. Заявл. 08.02.1989- Зарегистрировано0807.90.
- A.c. 1 148 253 Способ получения элементарной серы. / Еремин О. Г., Заславский Г. Ш., Волков В. И., Розенберг Ж. И. и др. Заявл. 18.11.1983.
- A.c. 1 089 895 Способ получения элементарной серы. / Еремин О. Г., Филатов A.B., Хагажеев Д. Т. и др. Заявл. 04.06.1979.
- Пат. 2 072 317 Способ получения элементарной серы. / Еремин О. Г., Зорий З. В., Барышев Л. Л. и др. Заявл. 28.06.1991- Опуб. 27.01.97. — Бюл. № 3.
- Пат. 2 091 297 Способ управления процессом восстановления кислородсодержащих сернистых газов. / Еремин О. Г., Мечев В. В., Орлов В. Н., Барышев А. А. и др. Заявл. 31.07.1990- Опуб. 27.09.97. — Бюл. № 27.
- Пат. 1 983 867 Способ непрерывной плавки сульфидных материалов. / Мечев В. В., Птицын A.M., Еремин О. Г., Калнин Е. И. Заявл. 12.06.1990.
- Пат. 1 754 649 Способ очистки сернистого газа. / Явор В. И., Иванова И. Д., Еремин О. Г. Заявл. 16.10.1990- Опуб. 15.08.92. — Бюл. № 30.
- Еремин О.Г., Менковский М. А., Явор В. И. Разработка и внедрение прогрессивных методов утилизации богатых сернистых газов с получением серной кислоты и серы // Цветная металлургия. 1983. — № 10. — С. 19−20.
- Еремин О.Г., Макаров Д. Ф., Тимошенко М. В. и др. Переработка отходящих сернистых газов металлургических производств с получением элементарной серы // Сб. науч. тр. Гинцветмета. М., 1989. — С. 65−71.
- Tarasov A.V., Yeremin O.G. Experience with new technology for sulphur recovery from flash smelting furnace. // Proceedings of the Sulphur 2004 International Conference. Barcelona, Spain, (Oct. 2004). — P. 193−197.
- Тарасов A.B., Еремин О. Г. Совершенствование технологии получения серы из отходящих металлургических газов. // Цветные металлы. 2004. — № 10.-С. 41−43.