Термохимические и газодинамические процессы при производстве стального проката с антикоррозионным покрытием
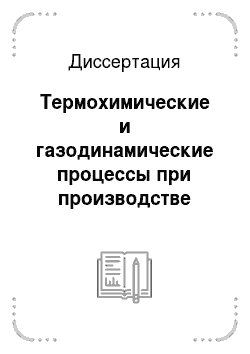
Диссертация
В конце 80-х годов в мире насчитывалось около 220 агрегатов цинкования, включая агрегаты комбинированного типа (позволяющие наносить алюмоцинковое и алюминивое покрытие). В СССР на 1991 г. действовало четыре агрегата цинкования полосы АНГЦ (НЛМК, ЧерМК, ЖданМК им. Ильича, ММК) и один агрегат алюмоцинкования АНГА-1700 ЧерМК. Проектировалось строительство комбинированных агрегатов алюмоцинкования… Читать ещё >
Содержание
- 1. СОВРЕМЕННЫЕ СПОСОБЫ И ТЕХНОЛОГИЯ ПРОИЗВОДСТВА СТАЛЬНОГО ПРОКАТА С АНТИКОРРОЗИОННЫМИ ПОКРЫТИЯМИ
- 1. 1. Коррозионные характеристики покрытий
- 1. 2. Высокопроизводительные агрегаты горячего цинкования и алюмоцинкования стальной полосы
- 1. 3. Производство стальной проволоки с антикоррозионным покрытием
- 1. 4. Антикоррозионные покрытия труб и уголков
- 1. 5. Основные операции при обработке стального проката перед нанесением покрытий и последующей термообработке
- 1. б
- Выводы и задачи исследований
- 2. ЭКСПЕРИМЕНТАЛЬНЫЕ ИССЛЕДОВАНИЯ ТЕРМОХИМИЧЕСКИХ ПРОЦЕССОВ НА СТАЛЬНОЙ ПОВЕРХНОСТИ
- 2. 1. Особенности взаимодействия стальной поверхности с атмосферой продуктов сгорания топлива
- 2. 2. Метод лазерной интерферометрии в исследовании термохимических процессов на стальной поверхности
- 2. 2. 1. Состав оборудования и принцип работы установки лазерного интерферометра
- 2. 2. 2. Методика расчета толщины оксидной пленки и ее оптических характеристик
- 2. 2. 3. Экспериментальные значения оптических параметров пленки
- 2. 3. Исследование окислительно-восстановительных процессов при ТХО стальной поверхности
- 2. 3. 1. Условия и параметры скоростного нагрева
- 2. 3. 2. Термодинамические условия окисления стали в продуктах сгорания топлива
- 2. 3. 3. Характеристики окислительно-восстановительного нагрева сталей различных марок при термохимической обработке
- 2. 3. 4. Термохимическая обработка проката при наличии сероводорода в отопительном газе
- 2. 3. 5. Основные кинетические параметры окислительновосстановительного процесса
- 2. 4. Термическая очистка поверхности стального проката
- 2. 4. 1. Общая характеристика загрязнений
- 2. 4. 2. Кинетические закономерности термической очистки
- 2. 4. 3. Оптимизация процесса термической очистки в протяжной печи
- 3. 1. Термодинамические условия окисления с зародышеобразованием
- 3. 2. Особенность зародышеобразования в твердой фазе
- 3. 3. Инкубационный период зародышеобразования
- 3. 4. Кинетика роста оксидов в неизотермических условиях нагрева
- 4. 1. Экспериментальный стенд алюмоцинкования полосы
- 4. 2. Анализ- качества наносимого покрытия
- 4. 3. Влияние газовых и температурных режимов
- 4. 4. Сажеобразование на поверхности полосы
- 4. 5. Исследование режимов ускоренного охлаждения и отпуска полосы с покрытием
- 4. 6. Термодиффузионный отжиг оцинкованной полосы
- 4. 6. 1. Общая характеристика и экспериментальное определение параметров процесса
- 4. 6. 2. Кинетическое описание диффузионного отжига
- 5. 1. Термохимическая обработка труб перед нанесением покрытия
- 5. 2. 0. собенности ТХО уголков при нанесении покрытий
- 5. 3. Алюмоцинкование малоуглеродистой стальной проволоки
- 5. 4. Интенсификация процесса ТХО с применением кипящего слоя
- 5. 4. 1. Статистические характеристики взаимодействия твердой фазы с поверхностями в кипящем слое
- 5. 4. 2. Термическая очистка поверхности проволоки в установках с кипящим слоем
- 6. 1. Исследование гравитационного течения пленок жидкости
- 6. 2. Взаимодействие симметричных газовых струй с плоской поверхностью
- 6. 3. Формирования покрытия из жидкометаллической пленки газовыми струями
- 6. 4. Оптимизация параметров воздушного «ножа» и структура
- 7. 1. Освоение режимов производства проката с алюминиевым покрытием на АНГА-1700 ЧерМК
- 7. 2. 0. тработка режимов ТХО при выпуске опытной партии проката с покрытием типа «Гальфан» на агрегате цинкования ММК
- 7. 3. Отработка газовых и температурных режимов на агрегате цинкования проволоки АГЦП-2 на Ревдинском ММЗ
Список литературы
- Липухин Ю.В., Гринберг Д. Л. Производство эффективных видов оцинкованной стали.-М.: Металлургия, 1987, 167 с.
- Бродов А.А., Соколова Т. В., Степанова Н. В. Состояние производства и рынок листовой стали и жести с покрытиями.// Сталь, 1996, N5, с. 67−71 .
- Парамонов В.А. Некоторые проблемы развития производства листового проката с покрытиями в России и странах СНГ.// Международная конференция «Черная металлургия России и стран СНГ в 21 в». -М.: 1994, Т.5, с. 5−19.
- Тенденции развития производства листовой стали с цинкоалюминиевыми покрытиями.// Инст."Черметинформация". М.: 1990, вып. 1(358), 14 с.
- Проскуркин Е.В., Коряка H.A. Новые виды защитных покрытий из цинка и его сплавов с алюминием.//Черметинформация. М.: 1990, 37 с.
- Мухамедшина Н.М., Салтыков М. И. Производство стальной проволоки и ленты с цинкалюминиевым покрытием. // Черная металлургия. М.: 1990, вып. 1. (1089), с.29−36.
- Проскуркин Е.П., Попович В. А., Мороз А. Т. Цинкование. Справочник.-М: Металлургия, 1988, 527 с.
- Новые виды покрытий из сплавов цинка с алюминием и способы их нанесения на металлопрокат и трубы./Проскуркин Е.В., Митников И. Е., Ткач В. И. и др.// Сталь, 1993, № 1, с.52−56.
- Okamoto, А и др.//Nippon Kokan Technical Report-overseas. 1972, № 12, p. 1−9.
- Pierson M. An optimum galvanizing furnace.// Jornal of Metals. 1971, № 12, p.26−30.
- Физико химические основы горячего свинцевания стали / Ухов В. Ф., Карамышев Е. П., Парамонов В. А. и др.-М.: Наука, 1977, 208 с.
- Бербенев В.И. Сжигание газа в печах безокислительного и малоокислительного нагрева. -Л.: Недра, 1988, 185 с.
- Окисление и обезуглероживание стали./Ващенко А.И., Зеньковский А. Г., Лифшиц А. Е. и др. -М.: Металлургия, 1972 335 с.
- Смирнов Н.С., Простаков М. Е., Липкин Я. Н. Очистка поверхности стали. М: Металлургия, 1978, 230 с.
- Попель С.И. Поверхностные явления в расплавах,— М.: Металлургия, 1994, 432 с.
- Миссол В. Поверхностная энергия раздела фаз в металлах.-М.- Металлургия, 1978, 176 с.
- Hirose Y., TogawaH., Sumiga J.//Tetsu to Hagane. 1982, V.68,№>16, p.2551−2560.
- Butler J., Beam D., Hawkins J. The development of air coating control for continuons strip galvanizing.// .Iron and Steel Eng. 1970, V.47,M 2, p, 77−86.
- Шмидт X., Боде Р., Эммерих Г. Тонкий лист с покрытием «Гальванил» для автомобилестроения.//Черные металлы. 1989,№ 3, с.4−10.
- Nishimoto A., Jnacari J, Nakaoka К. Intluence of Alloying Elements in Hot Dip Galvanized High Tensibe Strength Steet Steels on the Adhesion and Jron-Zinc Alloying Rate.// Tutsuto Hagane. 1982, V.6,№ 9, p. 1404−1410.
- Nokado H., Sudo H., Tsukataui J. и др.// Nutsu to Hagane. 1982, V.68,№ 9, p.1397−1403.
- Гусева H.E. Производство листовой стали с покрытием для автомобильной промышленности за рубежом// Черная металлургия. 1983, Вып. 16 (948), с. 11−30.
- Hirose Y., Toawa Н., Sumiya J.// Tetsu to Hagane. 1982, V.68, № 6, p.658−664.
- Иванов А.И., Федорина В. Г. Исследование окислительных свойств продуктов сгорания топлива/./ Изв. Вузов, Черная металлургия, 1984, № 2, с.91−94.
- Пестряев А. Т. Длышников С.Т. Скоростной безокислительный нагрев полосы в продуктах неполного сгорания.// Совершенствование тепловой работы и конструкций металлургических агрегатов. М4М. -М.: Металлургия, 1982, с.52−64.
- Hoffmann ^//Термодинамические условия окисления. НТМ, 1984, 39, № 3, р.67−104.
- Шкляревский И.Н., Шкляревский О. И. Приближенные формулы для коэффициентов отражения и пропускания тонких пденок/Юптика и спектроскопия .1969, Т.27, вып.4, с.654−664.
- Пестряев A.C., Попов Ю. А. Q кинетике окисления стальной полосы при ее нагреве в продуктах сгорания природного газа,//Изв АН СССР, Металлы, 1984, № 4, с. 198−202.
- Золоторев В.М., Морцов В. М., Смирнов Е. В. Оптические постоянные природных и технических сред. Справочник, — Л.: Химия, 1984, 206 с.
- Попов Ю.А. К теории распространения света в слоистых средах.//Журнал прикладной спектроскопии, 1985, Т.68, № 1, с.138−142.
- Попов Ю.А., Пахалуев В. М. Отражательная способность стали с пленкой оксидов.// Изв. АН СССР, Металлы, 1987, № 4, с.45−47.
- Расчет нагревательных термических печей. Справочник. Под ред. Тым®ка В.И. ГусовекийВ.Л. -М.: Металлургия, 1983, 481 с.
- Филиппов С. И. Теория металлургических процессов.-М.:Металлургия, 1967,279 с.
- Казачков Е. А, Расчеты по теории металлургических процессов. -М: Металлургия, 1968, 289 с.4Q. Файнштейн А. И. Исследование электропроводности тонких оксидных пленок на поверхности железа.//Изв.АН СССР, Металлы, 1981, № 5, с. 168−171.
- Окисление металлов. Под ред. ЕенараЖ. -М. Металлургия, 1968, Т 1, 498 с.
- Воронцов Е.С., Забровская В. Ф., Корнеев А. Н. Исследование температурной зависимости скорости роста оксидных пленок на тантале методом интерференционной индикации.//Изв.Вузов, Черная металлургия, 1985, № 2, с. 1−4.
- Кубашевский О., Гапкинс Б. Окисление металлов и сплавов, — М. Металлургия, 1965, с. 428.
- Грибовская И.В., Никулина НО. Кинетика окисления высокодисперсного порошка меди в неизотермических условиях.// РАН, Металлы, 1993, № 6, с, 192−199.
- ШестакЯ. Теория термического анализа. -М.: Мир, 1987, 455 с.
- Бирке Н, Майер Дж, Введение в высокотемпературное окисление метаддов,-М- Металлургия, 1987, 183 с.
- Влияние сероводорода в отопительном газе, на термическую обработку полосы/ Пахалуев В. М. Дишванов В.Л.Дрохина Л. А., Фомин Е. С. и др.// Сталь, 1990, № 3, с.93−95.
- Леонидова М.Н., Шварцман Д. А., Шульц Л. А. Физико-химические основы взаимодействия металла с контролируемыми атмосферами.-М. '.Металлургия, 1980, 263 с.
- Дамаск А., Дине Дж. Точные дефекты в металлах. -М.Мир, 1966, 191 с.
- Карабасов Ю.С., Чижиков В. М. Физико-химия восстановления железа из оксидов. -М. Металлургия, 1986, 200 с.
- Беняковский М.А., Гринберг Д. Л. Производство оцинкованного листа.-М.: Металлургия, 1973, 256 с.
- Грудев А.П., Тилик В. Т. Технологическая смазки в прокатном производстве.-М.: Металлургия. 1975. 365 с.
- Демидов П.Г.ДПандыба В.А., Щеглов П. П. Горение и свойства горючих веществ. -М.: Химия, 1973, 247 с.
- Основы практической теории горения. Под ред. Померанцева В. В. -Д.: Энергоатомиздат, 1986, 312 с.
- Иванов. А.В., Гурсеев A.A. Особенности окисления нефтяных масел в тонком слое на поверхности металла././ ХТТМ, 1993, № 10, с.8−11.
- Климов А.К., Баранов В. А. Новый подход к изучению процесса окисления синтетических смазочных масел// ХТТМ, 1995, № 5, с. 18−20.
- Сборник задач по теории горения. Уч. пособие под ред. Померанцева В. В. -Д.- Энергоатомиздат, 1983, 152 с.
- Телегин А.С., Швыдкий В. С., Ярошенко Ю. Г. Тепло-и массоперенос . -М.- Металлургия, 1995, 400 с.
- A.C.15 148.QQ.(СССР) Способ термохимической обработки стальной полосы./Пахалуев В.М., Пишванов В. Л., Фомин Е. С. 15.10.89. Бюл. N38.
- Эффективность термической очистки поверхности стальной полосы в продуктах сгорания газового топлива./Пахалуев В.М., Пишванов В. Л., Крохина Л. А. и др. Теплотехническое обеспечение основных металлургических производств.-М.: Металлургия, 1990, с.91−94.
- Архаров В.И., Борисов Е. С. Q структуре гематита во внешнем слое окалины.//Физика металлов и металловедение, 1956, ТЗ, вып. З, с.444−449.
- Гурский Д.И., Зеленкин В. А. Структура и кинетика взаимодействия металла с окисляющими средами.- Минск.: НИТ, 1982, с.27−53.
- Russell К. Кинетика зародышеобпазования по границам зерна./'/Acta Metallurgies 1969, VI7, № 8, p.1123−1131.
- Франчук В.И., Лариков Л. Н., Максименко Е. А. Исследование кинетики зарождения интерметаддидных фаз Fe Sn // Металлофизика и новейшие технологии. 1996, Т 18,№ 5, с.30−36.
- Горбачев В А, Шаврин C.B. Зародышеобразование в процессах восстановления окислов, — М.: Наука, 1985, 134 с.
- Бокштейн Б, С Диффузия в металлах, -М,-Металлурги>1978>246 с,
- Пинес Е.Я., Гумен Н. М., Падуе Л. П. К вопросу о влиянии всестороннего давления на эффекты диффузии в системах Cu-Nl, Si-Ni //Физика металлов и металловедение, 1968, Т 25, Вып.2, с.314−325.
- Богданов Н.М.ДСоверда В.П., Скрипов В. П. Зарождение и рост кристаллов в аморфных слоях воды, тяжелой воды и органических веществ.//Термодинамические свойства метастабильных систем и кинетика фазовых превращений. УНЦ АН СССР, Сведловск, 1985, с.30−34.
- Данков Н.Д. К теории начальных стадий фазовых превращений (образование поверхностных пленок).//Доклады АН СССР, 1946, Т 51, № 6, с.449−452.
- Данков Н.Д., Чураев. Эффект деформации поверхностного слоя металла при окислении.// Доклады АН СССР, 1950, Т 73, № 6, с.1221−1224.7L Горбачев В. А., Шаврин. С .В.Термические напряжения в спеках.-М.: Наука, 1982,74 с,
- Мровец С., Вепбер Т. Современные жаростойкие материалы. Справочник.- М.- Металлургия, 1986, 360 с.
- Франк-Каменецкий Д. А. Диффузия и теплопередача в химической кинетике. -М: Наука, 1967, 491 с.
- Пайдасси Ж. Коррозия металлов (в жидких и газообразных средах).- М.: Металлургия, 1964, с.95−152.
- Пахалуев. В.М., Пишванов В. Л. Особенности термохимической обработки стальной полосы в агрегатах горячего ал ю мин и р о шшя.И Сталь, 1986, JHklO, с.99−102,
- Применение электрохимических датчиков с твердым электролитом для контроля процессов/ Ивонин А. К., Кирнос И. В., Клышников С. Т. и др.//Сталь, 1993, № 3, с. 102−164.
- Jones R., Thomas R. Production of hot dip aluminized steel strip // Prad. and Use Coil-Coated. Strip. Proc. Jut. Conf. Birmingham. — 1981, p. 55 — 63.
- Вашитзуки A. II Tensu to Hagan. 1986, V. 72, № 5, p.439 .
- Заявка 2 537 298 (США). Способ предварительной обработки полосы или листа из недатированной стали т чанесе. ния покрытия путем погружения в расплав, не содержащий флюса Armko Steei2208.1974.
- Заявка 54−8.7359 (Япония). Спосоо регулирования горения в пламенной печи безокислительного отжига Дайдо Токусюко К. К. Опубл. 09.02.1982.
- Патент 4 364 728 (США). Печь непрерывного отжига полосы в линии нанесения цинковых и алюминиевых покрытий Electric Furnace Со. Опубл. 21.12.82.
- Патент Q134143 (Япония). Способ горячего алюминирования полосы Nippon Steel Corpl, Опубл, 13,03,85,
- Линчевский Б.В. Термодинамика и кинетика взаимодействия газов с жидкими металлами. -М.Металлургия, 1986, 220 с.
- Патент 58−2586 (Япония). Устройство для нанесения покрытия из расплава в непрерывных процессах Ниссик Сайтэцу Ки. Опубл. 17.01.83.
- Arnold J., Boston S., Caudiil F. Control of defects by zinc vaporization in the snout.//Int. conf. on zinc and alloys coated steel sheet.(Токио) 1989, p. 130−137.
- Галиханданов Е.А., Хоромайлов В. Г., Шкодин К. К. Расчет равновесий искусственных атмосфер из природного газа со сталью// Изв. АН СССР. -Металлы, 1972, N5, с.92−96.
- Термодинамические свойства индивидуальных веществ. Под ред. Глушко В. П. -М.: АН СССР, 1962, Т 2, 916 с.
- Еаник Я., Ясавски Ф. Развитие производства стальных листов с алюминиево-цинковым покрытием././ Черметинформация. -М.:1982, Вып.8 (132), 19 с.
- Л ар и ко в Л И, Механизм, реактивной диффузии//Металлофизика и новейшие технологии. 1994, Т16, № 9, с. 3−28.
- Заявка 394 050 (Япония). Флюс для нанесения горячих покрытий сплавами системы цинк-алюминий. Кокай Токке Кохо. Опубл. 18.04.91.
- Заявка 55−7602.(Япония). Процесс нанесения покрытий на проволоку Кокай Токке Кохо. Опубл. 01.06.80.
- Новый способ нанесения на проволоку металлических покрытий./Экспресс-информация. Метизное производство. 1990, вып.20, с, 7.
- Дерягин Б.В., Леви С-.Н. Физико-химия нанесения тонких слоев на движущуюся подложку.-М: АН СССР, 1959, 208 с.
- ЛевичВ.Г. Физико-химическая гидродинамика,-М.: Ф-М., 1959, 699 с.
- Баскаков АЛ. Скоростной безокисдительньш нагрев и термическая обработка в кипящем слое,— М.: Металлургия, 1968, 224 с.
- Флуктуации коэффициента теплоотдачи и теплообмен пластины с вырезом в псевдоождженном слое /Баскаков А. Д, Лумми А. П., Пахалуев В, М, и др, Деп. ВИНИТИ, 1994, Ш332-В, 22 с.
- Лумми А.П., Баскаков А. П., Пахалуев В. М. Интенсификация внешнего теплообмена при истечении вторичного воздуха в кипящем слое. Деп. ВИНИТИ, 1994, № 1334−8. 8 с.
- Пахалуев В.М. Спектральные характеристики процесса переноса в неоднородных кипящих слоях,//Гидродинамика и теплообмен. -Свердловск, УНЦ АН СССР, 1974, с, 52−56.
- Лумми А.П., Пахалуев В. М. Расчет времени нагрева в кипящем слое деталей с вырезами,// Промышленные печи с кипящим слоем, СЛ. 2.42,-УШТ, Свердловск, 1976, с.22−24.
- Лумми А.П. /Пахалуев В.М., Жигало C.B. Особенности теплообмена тел с вырезами в кипящем слое. Деп. ВИНИТИ, 1980, № 6(104), с. 71.
- Исламов С.Р. Удаление технологической смазки с проволоки в кипящем слое.//Промышленные печи с кипящим слоем. Сб.242. УПИ. Свердловск. 1976. с.115−118.
- Пахалуев В.М., Шейнкман А. Г. Аппаратурный анализ статистических спектров гравитационного течения пленок жидкости.//Теплофизика и термодинамика, УНЦ АН СССР, Свердловск, 1974, с.64−70.
- Пахалуев В.М., Шейнкман А. Г. Исследование статистических характеристик волнового течения пленок жидкости.// ИФЖ, 1974, Т27, № 5. с, 845−849.
- Щеклеин С.Е., Пахалуев В. М., Шейнкман А. Г. Исследование стекающей вниз пленки жидкости высокочастотным емкостным мето.дом.//Гидродинамика и теплообмен в. энергетических установках. УНЦ АН СССР, Свердловск, 1975, с.18−21.
- Пахалуев В.М., Щеклеин С. Е. Энергетические характеристики волнового течения пленок жидкости.// ТОХТД975, Т9, № 5, с.761−763.
- Пахалуев В. М. Державина H.A. Исследование локального теплообмена и трения в условиях пленочного течения жидкостиУ/Теплофизические свойства жидкости и взрывное вскипание. УНЦ АН СССР, Свердловск, 1976, с.98−101.
- Теплообмен турбулентной пленки жидкости с шероховатой поверхностью в условиях свободного стекания/ Ратников Е. Ф., Шейнкман А. Г., Пахалуев В. М. и др.// Теплоэнергетика, 1977,№ 4, с.75−76.
- Дыбан Е.П., Мазур А. И. Теплообмен в окрестности критической точки при натекании турбулизированной струи на преградуУ/Теплофизика и теплотехника, — Киев, 1977, вып.33, с.6−11.
- Пахалуев В. М. Дрохина Л.А. Особенности теплообмена соударяющихся струй с плоской поверхностью между ними. // Тепломассообмен-VI. Минск, 1980, Т1, ч.2, с.167−170.
- Релик Е.У., Кузенков B.K. Измерение турбулентного поверхностного трения с помощью плоских трубок полного напора.//ИФЖ, 1979, Т35, № 6, с.980−981.
- Ellen О., Tu С. Анализ струйного Удаления жидких покрытий.// Теоросновы инженерных расчетов.- 1984, № 4, с. 146−152.
- Thornton J., Graff Н. Аналитическое описание процесса струйного формирования жидкометаллического покрытия на полосе,// Metallurcical Trans.B., 1976, V7B, № 4, р.607−618.
- Пахалуев В.М., Кукушкин В. М., Гринберг Д. Л. Формирование тонкого цинкового покрытия на стальной полосе воздушным «ножом».// Сталь, 1980, № 3, C.2Q7−2Q9.
- Исследование процесса струйного регулирования толщины металлического покрытия/ Пахалуев В. М, Крохина Л, А., Шаповалов A.B. идр.//Металлургическая теплотехника. -М. Металлургия, 1981, с.74−76.
- Пахалуев В. М. Дрохина Л.А., Кукушкин В. М. Оптимизация параметров воздушного «ножа» при производстве оцинкованной полосы с минимальной разнотолщинностью покрытия.//Тепдотехнические основы металлургических процессов, -М.: Металлургия, 1984, с.56−58.
- Формирование цинкового покрытия на стальной полосе в агрегатах непрерывного действия / Кукушкин В. М., Попель СИ, Пахалуев В. М. и др.//Сталь, 1980, Ш11, с.992−994
- A.C. 1 079 695.(СССР). Устройство для формирования покрытий из расплава./ Пахалуев В. М. Дрохина Л.А., Кукушкин В. М. и др. Опубл.15.03.84. Еюл. № 10.
- А.С.910 832.(СССР). Устройство для автоматического регулирования толщины покрытия в процессе горячего цинкования./Давыдов В.К., Турубинер Н. Л., Грушко В. А. и др. Опубл. 07.03.82. Бюл. т
- Патент 38.41 557 (США). Автоматическое регулирование толщины покрытия при горячем цинковании рулонного материала N.S.C., Опубл.15,10,74,
- Производство, алюмооцинкованных стальных полос на линии Череповецкого металлургического комбината / Липухин Ю. В. Дишков В.Я., Степанов A.A. и др.// Межд.конф. «Черная металлургия России и стран СНГ в 21 веке».- М.:1994, Т5, с.48−50.
- Лисиенко В.Г., Лобанов В. И. Дитаев Б.И. Теплофизика метшщургилеских процессов. -М.: Металлургия, 1982, 240 с.
- Заявка 41−1078.75 (Япония). Антикоррозионное цинк-алюминиевое покрытие и способ его. получения. Беслем Стил Карп. Опубл. 10.10.78.
- Анализ технологии термической обработки полосы с алюмоцинковым и алюминиевым покрытиями./Пахалуев В.М., Пишванов В. Л., Филиппова И. А. и др.// Сталь, 1989, № 3″ с.97−100,
- Пахалуев В.М., Пишванов В. Л., Кукушкин В. М. Газотермические режимы современной технологии производства проката с покрытиями на основе, цинкозлюминиевого спдава,//Тезисы доклада Всесоюзного Н.-Т. конференции ВНИИМТ Свердловск, 1990, с.86−87.
- Проволока с покрытием Bezinal// Draht., 1993, V4, № 4, р.234 (нем).
- Проблемы коррозионной защиты стальной проволоки покрытиями, нанесенными из расплава/ Буравлев ИБ, Коковихин Ю. И., Почта В Н. и др.// Металлургия и горнорудная промышленность, 1993, № 3, с.42−44.
- Новые виды покрытий из сплавов цинка с алюминием и способы их нанесения на тпубы и проволоку/ Проскуркин Е. В., Ткач В. И., Хаустов Г. И. и др.// Междун.конф. «Черная металлургия России и стран СНГ в 21 в.» М.:1994, Т5, с.50−51.
- Материалы фирмы «Bethlehem Steel». -1981, p. 1−13.
- Современные и перспективные пути развития производства металлопроката и труб с покрытиями из цинка и его сплавов с алюминием.//Отчет по материалам Международного симпозиума под ред. Проскуркина Е. В. -Днепропетровск, 1989, 91 с.
- Снижение разнотолщинности при струйном формировании цинкового покрытия на стальной полосе/Пахалуев В. М. Дрохина Л.А., Кукушкин В. М. и др.// Сталь, 1983, № 4, с.43−46.
- Пестряев. A.C., Фомин Е. С. Пути улучшения работы протяжной печи АГЦ-2У//Сталь, 198.4, № 2, с.89−92.
- Уменьшение обрааования оксидов азота путем нестеохиометрического сжигания газа в методической нагревательной печи / Ашихмин A.A., Каратаев В. Л., Дружинин Г. М. и др.// Сталь, 1996, № 9, с.75−77.