Повышение рабочего ресурса элементов теплосилового оборудования электростанций с учетом макроповреждаемости металла
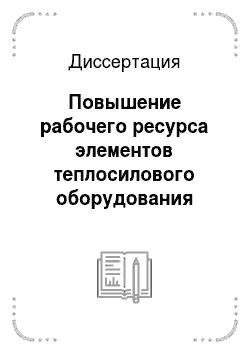
Диссертация
На основе современных физико-механических представлений о механизме формирования и развития разрушения материалов предложены модели кинетики усталостного разрушения в металле, ускоренного воздействием на него жидкой коррозионной среды. Разработанные модели развития коррозионно-усталостных трещин в металле, основанные на принципе снижения свободной энергии активации атомов, а также на механизмах… Читать ещё >
Содержание
- Глава 1. Подходы к определению ресурса и оценке сопротивления разрушению энергетического оборудования с учётом макроповреждённости металла (состояние вопроса)
- 1. 1. Состояние и повреждаемость основных элементов длительно эксплуатируемого тепломеханического оборудования ТЭС
- 1. 1. 1. Котлоагрегаты
- 1. 1. 2. Станционные трубопроводы
- 1. 1. 3. Сосуды, работающие под давлением
- 1. 1. 4. Паровые турбины
- 1. 2. Хрупкое и квазихрупкое разрушение материалов — критерии тре-щиностойкости
- 1. 3. Циклическая трещиностойкость материалов
- 1. 4. Рост трещин в стали при механическом нагружении и воздействии водной среды (коррозионно-механическая трещиностойкость)
- 1. 4. 1. Специфика исследований кинетики усталостного разрушения сталей в условиях воздействия водных сред повышенных параметров
- 1. 4. 2. Анализ особенностей влияния водных сред на характеристики трещиностойкости сталей энергооборудования
- 1. 5. Развитие трещин в теплоустойчивых сталях при длительной статической нагрузке в условиях ползучести
- 1. 6. Основные принципы расчётной оценки долговечности элементов энергооборудования с учётом стадии развития трещиноподобных дефектов
- 1. 7. Выводы по главе 1. Цель и задачи исследования
- 1. 1. Состояние и повреждаемость основных элементов длительно эксплуатируемого тепломеханического оборудования ТЭС
- Глава 2. Моделирование процесса развития трещин в металле
- 2. 1. Модель развития усталостной трещины в металле с учётом воздействия жидкой среды (на базе кинетической модели Екобори)
- 2. 2. Модель кинетики коррозионно-усталостного разрушения металла по механизму анодного растворения
- 2. 3. Модель развития коррозионно-усталостной трещины по катодному механизму охрупчивания металла
- 2. 4. Феноменологическая модель развития трещины в металле при высокотемпературной ползучести
- 2. 5. Выводы по главе 2
- Глава 3. Материал, испытательное оборудование, методика исследований
- 3. 1. Материал и его свойства, образцы
- 3. 1. 1. Исследуемый материал
- 3. 1. 2. Образцы для испытаний
- 3. 2. Испытательное оборудование и технические средства измерений
- 3. 2. 1. Испытания на статическую и циклическую трещиностойкости металла в среде лабораторного воздуха
- 3. 2. 2. Испытания на коррозионно-циклическую и коррозионно-статическую трещиностойкость металла в жидкой среде
- 3. 2. 3. Испытания на трещиностойкость металла при статической нагрузке в условиях ползучести
- 3. 3. Методика проведения исследований
- 3. 3. 1. Испытания на статическую и циклическую трещиностойкости металла в среде лабораторного воздуха
- 3. 3. 2. Испытания на коррозионно-циклическую трещиностойкость
- 3. 3. 3. Испытания на статическую трещиностойкость в условиях высокотемпературной ползучести
- 3. 4. Выводы по главе 3
- 3. 1. Материал и его свойства, образцы
- Глава 4. Статическая и циклическая трещиностойкость материалов
- 4. 1. Статическая трещиностойкость (вязкость разрушения)
- 4. 2. Цикличекая трещиностойкость
- 4. 2. 1. Влияние на циклическую трещиностойкость геометрии образца и асимметрии нагружения
- 4. 2. 2. Влияние температуры испытаний и состояния металла на циклическую трещиностойкость
- 4. 3. Выводы по главе 4
- Глава 5. Исследования кинетики развития трещин в металле при нагруже-нии и воздействии активной водной среды
- 5. 1. Влияние состава коррозионной среды
- 5. 2. Влияние параметров циклического нагружения
- 5. 3. Влияние динамического состояния среды, температуры и состояния металла
- 5. 4. Кинетика трещин в сталях при статической нагрузке и воздействии коррозионной среды
- 5. 5. Исследование электрохимических параметров в вершине трещины и анализ механизмов влияния коррозионной среды на процесс разрушения металла
- 5. 6. Выводы по главе 5
- Глава 6. Кинетика трещин в. теплоустойчивых сталях при высокотемпературной ползучести
- 6. 1. Общие закономерности развития трещин в сталях при ползучести
- 6. 2. Модифицированные зависимости скорости развития трещин ползучести в сталях./
- 6. 3. Выводы по главе 6
- Глава 7. Практическая реализация метода определения живучести элементов энергооборудования
- 7. 1. Базовые кинетические диаграммы трещиностойкости сталей энергооборудования
- 7. 2. Аппроксимация поля напряжений и методы: определения коэффициента интенсивности напряжений в элементах оборудования
- 7. 3. Алгоритм расчёта долговечности элементов конструкций с учётом наличия в них трещиноподобных дефектов (расчёт живучести)
- 7. 4. Примеры практического применения метода определения живучести элементов энергооборудования
- 7. 4. 1. Расчёт живучести барабана котла ТП-9 с трещинами на кромках отверстий питательных труб
- 7. 4. 2. Анализ условий и оценка причин разрушения барабана котла ТГМ-84 в результате гидроиспытаний после проведенного ремонта,
- 7. 4. 3. Расчётная оценка живучести гибов необогреваемых труб котла ТГМ
- 7. 4. 4. Расчётная оценка живучести гибов питательного трубопровода энергоблока 300 МВт
- 7. 4. 5. Расчёт живучести гиба пароперепускной трубы котла
- 7. 4. 6. Анализ процесса разрушения стыкового сварного соединения паропровода ГПП блоков 800 МВт
- 7. 4. 7. Оценка живучести узла сопряжения переходного штуцера де-аэрационной колонки с баком корпуса деаэратора повышенного давления
- 7.
- Выводы по главе 7
Список литературы
- Злепко В.Ф., Резинских В. Ф., Штромберг Ю. Ю., Швецова Т. А. Оптимизация системы эксплуатационного контроля и диагностики состояния металла основных элементов энергооборудования // Электрические станции. 1991. — № 6. — С. 59−60.
- Правила устройства и безопасной эксплуатации паровых и водогрейных котлов ПБ 10−574−03. М.: НТЦ «Промышленная безопасность», 2004.-216 с.
- Правила устройства и безопасной эксплуатации трубопроводов пара и горячей воды ПБ 10−573−03. М.: НТЦ «Промышленная безопасность», 2004. — 128 с.
- Правила устройства и безопасной эксплуатации сосудов, работающих под давлением ПБ 03−576−03. М.: НТЦ «Промышленная безопасность», 2003.- 192 с.
- Тумановский А.Г., Резинских В. Ф. Стратегия продления ресурса и технического перевооружения тепловых электростанций // Теплоэнергетика.-2001.-№ 6.-С. 3−10.
- Типовая инструкция по контролю металла и продлению срока службы основных элементов котлов, турбин и трубопроводов тепловых электростанций РД 10−577−03. М.: НТЦ «Промышленная безопасность», 2004. — 127 с.
- Злепко В.Ф., Гринь Е. А., Швецова Т. А. Техническое перевооружение действующих ТЭС с учётом состояния металла // Электрические станции. 2001. — № 7. — С. 12−18.
- Антикайн П.А. Обеспечение надёжной эксплуатации котлов, сосудов и трубопроводов после исчерпания проектного срока службы // Теплоэнергетика. 1996. — № 12. — С. 2−7.
- Карзов Г. П., Леонов В. П., Тимофеев Б. Т. Сварные сосуды высокого давления (прочность и долговечность). Л.: Машиностроение, 1982. — 267 е.
- Антикайн П.А. Металлы и расчёт на прочность котлов и трубопроводов. М.: Энергия, 1980. — 440 с.
- Махутов H.A. Прочность и безопасность. Фундаментальные и прикладные исследования. Новосибирск: Наука, 2008. — 528 с.
- Резинских В.Ф., Гринь Е. А., Букин Ю. А. Эксплуатационная надёжность и перспективы продления эксплуатации тепломеханического оборудования Сургутской ГРЭС-2 //Электрические станции. -2005. -№ 3. С. 11−15.
- Захаров A.A., Зверьков Б. В., Иванов A.A. Анализ повреждений котельных барабанов при малоцикловом нагружении // Материалы к краткосрочному семинару «Малоцикловая усталость сварных конструкций». — Л.: ЛДНТП, 1979.-С. 95−101.
- Партон В.З., Морозов Е. М. Механика упругопластического разрушения. М.: Наука, 1974. — 416 с.
- Черепанов Г. П. Механика хрупкого разрушения. М.: Наука, 1974. -640 с.
- Махутов H.A. Деформационные критерии разрушения и расчет элементов конструкций на прочность. М.: Машиностроение, 1981. — 272с.
- Нотт Дж. Ф. Основы механики разрушения. М.: Металлургия, 1978. -256 с.
- Броек Д. Основы механики разрушения. Пер. с англ. М.: Высшая школа, 1980.-380 с.
- Екобори Т. Физика и механика разрушения и прочности твёрдых тел. -М.: Металлургиздат, 1971. 264 с.
- Качанов JIM. Основы механики разрушения. М.: Наука, 1974. — 311 с.
- Балашов Ю.В., Надцына JI.B., Каминская Е. И., Давлятова JI.B. Исследование металла барабана, разрушившегося при гидроопрессовке // Электрические станции. 1993. — № 12. — С. 15−17.
- Гринь Е.А. Хрупкие разрушения барабанов котлов высокого давления — основные причины и способы предотвращения // Теплоэнергетика, — 2008.-№ 2.-С. 40−45.
- Зорев H.H. Причины повреждения барабанов котлов высокого давления и повышение их надёжности М.: НИИИНФОРМТЯЖМАШ, 1968. -81 с.
- Балашов Ю.В. Повреждения и ремонт котельных барабанов в ФРГ // Энергохозяйство за рубежом. 1984. — № 5. — С. 12−14.
- Cockenzie: brittle fracture failure // Engineering. 1967. — 203. — № 5276. -P. 885−886.
- Wellinger К., Schoch W., Krageloh E. Versuche an einer ausqebauten Kesseltrommel mit Dehnungsmessung //Mitt. d. VGB.-H. 107 (1967).-P. 91−98.
- Hanford R. Analysis of boiler drum failure during hydrostatic testing // Journal of Products Leebility. 1978. — № 1. — P. 59−75.
- Зароченцев Г. Г. О причине появления трещин в барабанах современных котлов // Электрические станции. 1965. — № 5. — С. 41^-2.
- Испытание до разрушения котельного барабана из стали 16ГНМ / Б. В. Зверьков, А. Х. Сигал и др. // Энергомашиностроение. 1970. — № И. -С. 28−30.
- Данюшевский И.А. Исследование деформаций около отверстий на моделях барабана котла // Энергомашиностроение. 1971. — № 2. — С. 43—44.
- Зверьков Б.В., Сигал А. Х. Напряжения в котельном барабане при гидравлическом испытании // Энергомашиностроение. 1972. —№ 6. — С. 11−13.
- Никитин В.И., Кисилёва Е. В. Исследование усталостной прочности котельных сталей в воде, не содержащей кислород // Труды ЦКТИ, вып. 123.-Л., 1974.-С. 43−51.
- Шур Д.М., Ивченко Л. Ф. Экспериментальное исследование прочности крупных сварных сосудов, работающих под давлением // Сварочное производство. 1972. — № 6. — С. 32−34
- Федосов А.И., Иванищев Г. И., Купцова Н. И. Температурные напряжения в барабанах паровых котлов и влияние их на прочность материала барабанов // Проблемы прочности. 1970. — № 5. — С. 76−80.
- Квашнина Е.И. Исследование характера дефектов барабанов котлов высокого давления // Труды ЦНИИТМАШ, вып. 114. М., 1973. — С. 71−74.
- Туляков Г. А. О роли термических напряжений при возникновении и развитии эксплуатационных трещин в барабанах паровых котлов // Теплоэнергетика. 1970. — № 5. — С. 11−13.
- Зорев H.H., Туляков Г. А. О возможности эксплуатации котельных барабанов без выборки трещин из отверстий водоопускных труб // Электрические станции. 1975. -№ 6. — С. 10−11.
- Балашов Ю.В., Шрон Р. З., Надцина Л. В., Щапова В. В. О ресурсе барабанов котлов высокого давления // Электрические станции. 1991. -№ 6. — С. 44−47.46.