Сопряженные плазменно-электрохимические процессы, протекающие при получении покрытий на легких конструкционных материалах
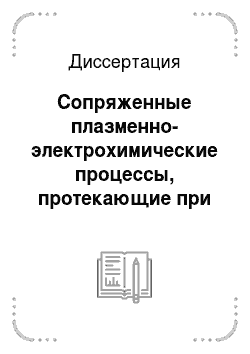
Защитные покрытия, формируемые на поверхности алюминиевых и магниевых сплавов при реализации плазменных микроразрядов на поверхности рабочего электрода, находящегося в электролите, нашли применение в качестве функциональных покрытий, в том числе износостойких и антикоррозионных. В последние годы исследуется возможность применения покрытий, получаемых при наличии плазменных микроразрядов… Читать ещё >
Содержание
- ЧАСТЬ 1. ЛИТЕРАТУРНЫЙ ОБЗОР
- Глава I. Механизм протекания процесса плазменно-электролитического оксидирования (ПЭО) легких конструкционных сплавов
- 1. 1. Основные представления о кинетике и механизме роста покрытий на легких конструкционных сплавах при проведении процесса ПЭО
1.2 О гипотетических механизмах образования высокотемпературных модификаций оксида алюминия в покрытии при проведении процесса ПЭО в щелочных водных растворах с небольшим (до 20 г/л) содержанием ТЖС или эквивалентного содержания силиката щелочного металла.
1.3 Экспериментальное доказательство необходимости нагрева металлической основы для интенсивного образования высокотемпературной модификации оксида алюминия (а-АЬОз) во внутреннем слое покрытия.
Глава II. Влияние катодной составляющей тока на кинетику роста покрытий, формируемых при проведении процесса ПЭО на поверхности алюминиевых сплавов.
II. 1 Гипотетические механизмы влияния катодной составляющей тока на кинетику роста покрытий на алюминиевых сплавах.
II.2 Механизм влияния катодной составляющей тока на кинетику роста покрытий при проведении ПЭО алюминиевых сплавов, разработанный сотрудниками кафедры защиты металлов и технологии поверхности НИТУ «МИСиС».
Глава III. Методы получения антикоррозионных покрытий на основе аморфного диоксида кремния способом ПТХО на изделиях, в том числе крупногабаритных.
III. 1 Технологические режимы и механизм получения антикоррозионных покрытий на основе аморфного диоксида кремния способом ПТХО на алюминиевых сплавах.
Ш. 2 Опубликованные способы ПТХО крупногабаритных изделий.
Список литературы
- Neil W., Wick R. Effect of various polyvalent metal anion addition to an alkaline magnesium anodizing bath // Electrochem. Soc. 1957. V. 104. № 6. P. 356−359.
- Neill W. The preparation of cadmium niobate by an anodoc spark reaction //J. Electrochem. Soc. 1958. V. 105. № 9. P. 544−547.
- Gruss L.L., Neill W. Anodic Spark Reaction Products in Aluminate, Tungstate and Silicate Solutions // Electrochem. Technol. 1963. V. 1. № 9−1. P.283−287.
- Neill W., Gruss L.L. Anodic film growth by anion deposition in aluminate, oungstate and phosphate solutions // J. Electrochem. Soc. 1963. V. 110. № 8. P. 853−855.
- Neill W., Gruss L.L., Husted D.G. The anodic synthesis of CdS films // J. Electrochem. Soc. 1965. V. 112. № 7. P. 713−715.
- Pat. 2 778 789 US. Cr 22 process / Mc Neil W.- 1957.
- Pat. 2 753 952 US. HAE process / Mc Neil W.- 1957.
- Pat. 3 293 158 US (CI. 204−56). Anodic spark reaction process and articles / McNeil W., Cruss L.L.- 1966.
- A.C. 526 961 СССР (H 01G 9/24). Способ формовки анодов электрических конденсаторов / Г. А. Марков, Г. В. Маркова (СССР) — опубл. в Бюл. № 32. 1976.
- Ю.Николаев А. В., Марков Г. А., Пещевицкий Б. Н. Новое явление в электролизе // Изв. СО АН СССР. Сер. хим. наук. 1977. Вып. 5. С. 32−33.
- А.С. 926 083 (С 25 D 9/06). Способ электролитического нанесения силикатных покрытий / Г. А. Марков, Б. С. Гизатуллин, И. В. Рычажкова (СССР) — опубл. в Бюл. № 17. 1982.
- А.С. 926 084 (С 25 D 11/02- В 23 Р 1/18). Способ анодирования металлов и их сплавов / Г. А. Марков, Е. К. Шулепко, М. Ф. Жуков (СССР) — опубл. в Бюл. № 17. 1982.
- A.C. 582 894 СССР (В 22 D 15/00). Способ изготовления металлической литейной формы / Ю. А. Караник, Г. А. Марков, В. Ф. Минин и др. (СССР) — опубл. в Бюл. № 45. 1977.
- A.C. 657 908 СССР (B22D 15/00 В22С 9/00). Способ изготовления литейных форм и стержней / Ю. А. Караник, Г. А. Марков, В. Ф. Минин и др. (СССР) — опубл. в Бюл. № 15. 1979.
- Марков Г. А., Терлеева О. П., Шулепко Е. К. Электрохимическое окисление алюминия при катодной поляризации // Изв. СО АН СССР. Сер. хим. наук, 1983. № 7. Вып. 3. С. 31−34.
- Баковец В.В., Поляков О. В., Долговесова И. П. Плазменно-электролитическая анодная обработка металлов. Новосибирск: Наука, 1991. 167 с.
- Черненко В.И., Снежко J1.A., Папанова И. И. Получение покрытий анодно-искровым электролизом / Л.: Химия, 1991. 128 с.
- Гордиенко П.С. Образование покрытий на аноднополяризованных электродах в водных электролитах при потенциалах пробоя и искрения / Владивосток: Дальнаука, 1996. 216 с.
- Гордиенко П.С., Гнеденков C.B. Микродуговое оксидирование титана и его сплавов / Владивосток: Дальнаука, 1997. 186 с.
- Суминов И.В., Эпельфельд A.B., Людин В. Б., Крит Б. Л., Борисов A.M. Микродуговое оксидирование (теория, технология, оборудование) / М.: ЭКОМЕТ, 2005. 368 с.
- Мамаев А.И., Мамаева В. А. Сильнотоковые микроплазменные процессы в растворах электролитов / Новосибирск: Изд-во СО РАН, 2005. 255 с.
- Гнеденков C.B., Хрисанова O.A., Завидная А. Г. Плазменное электролитическое оксидирование металлов и сплавов в тартратсодержащих растворах / Владивосток: Дальнаука, 2008. 144 с.
- Ракоч А.Г., Дуб A.B., Гладкова A.A. Анодирование легких сплавов при различных электрических режимах. Плазменно-электролитическая нанотехнология / М.: Старая Басманная, 2012, 496с. 500 экз. — ISBN 978−5 904 043−82−7.
- Yerokhin A.L., Snisko A.L., Gurevina N.L. Discharge characterization in plasma electrolytic oxidation of aluminium // Journal of Physics D: Applied Physics, 2003. V. 36. P. 2110−2120.
- Слонова А.И., Терлеева О. П. Морфология, структура и фазовый состав микроплазменных покрытий, сформированных на сплаве Al-Cu-Mg // Защита металлов, 2008. Т. 44. № 1. С. 72−83.
- Ракоч А.Г., Гладкова A.A., Ковалев B.JL, Сеферян А. Г. Механизм образования композиционных микродуговых покрытий на алюминиевых сплавах // Коррозия: материалы, защита, 2012. № 11. С. 31−35.
- Томашов Н.Д., Заливалов Ф. П., Тюкина М. Н. Толстослойное анодирование алюминия и его сплавов / М.: Машиностроение, 1968. 220 с.
- Томашов Н.Д., Заливалов Ф. П. Некоторые закономерности толстослойного анодирования алюминия и его сплавов. Сб. «Анодная защита металлов». М.: Машиностроение, 1964. С. 183−185.
- Аверьянов Е.Е. Справочник по анодированию / М.: Машиностроение, 1988. 224 с.
- Магурова Ю.В., Тимошенко A.B. Влияние катодной составляющей на процесс микроплазменного оксидирования сплавов алюминия переменным током // Защита металлов, 1995. Т. 31. № 4. С. 414−418.
- Тимошенко A.B., Магурова Ю. В. Микроплазменное оксидирование сплавов системы Al Cu // Защита металлов, 1995. Т. 31. № 5. С. 523−531.
- Тимошенко A.B., Опара Б. К., Ковалев А. Ф. Микродуговое оксидирование сплава Д16Т на переменном токе в щелочном электролите // Защита металлов, 1991. Т. 27. № 3. С. 417−424.
- Тимошенко A.B., Опара Б. К., Магурова Ю. В. Влияние наложенного переменного тока на состав и свойства оксидных покрытий, сформированных в микроплазменном режиме на сплаве Д16 // Защита металлов, 1994. Т. 30. № 1. С. 32−38.
- Руднев B.C. Рост анодных оксидных слоев в условиях действия электрических разрядов // Защита металлов, 2007. Т. 43. № 3. С. 296−302.
- Matykina Е., Arrabal R., Mohamed A., Skeldon P., Thompson G.E. Plasma electrolytic oxidation of pre anodized aluminium. // Corros.Sei., 2009. V. 51. P. 2897−2905.
- Руднев B.C., Гордиенко П. С., Курносова, А Т., Овсянникова А. А. Влияния электролита на результат микродугового оксидирования алюминиевых сплавов // Защита металлов, 1991. Т. 27. № 1. С. 106−1011.
- Рамазанов Ж.М., Мамаев А. И. Получение износостойких функциональных оксидных покрытий на сплавах алюминия методом микродугового оксидирования // Физика и химия обработки материалов, 2002. № 2. С. 67−69.
- Михеев А.Е., Терехин H.A., Стацура В. В., Голенкова A.A. Технологические возможности микродугового оксидирования алюминиевых сплавов // Вестник машиностроения, 2003. № 2. С. 56−63.
- Федоров В.А., Белозеров В. В., Великосельская И. Д., Булычев С. И. Состав и структура поверхностного слоя на сплавах алюминия, получаемого при микродуговом оксидировании // Физика и химия обработки материалов, 1988. № 4. С. 92−97.
- Sundararajan G., Rama Krishna L. Mechanisms underlying the formation of thick alumina coatings through the MAO coating technology // Surface and Coatings Technology, 2003. V. 167. P. 269−277.
- Tillous E.K., Toll-Duchanoy T., Bauer-Grosse E. Microstructure and 3Dmicrotomographic characterization of porosity of MAO surface layers formed on aluminium and 2214-T6 alloy // Surface and Coatings Technology, 2009. Vol. 203. № 13. P. 1850−1855.
- Wenbin Xue, Zhiwei Deng, Ruyi Chen, Tonghe Zhang. Growth regularity of ceramic coatings formed by microarc oxidation on Al-Cu-Mg alloy // Thin Solid Films, 2000. № 372. P. 114−117.
- Ковалев В.Л. Кинетика и механизм образования композиционных микродуговых покрытий на алюминиевых сплавах. Автореф. дисс.. канд. хим. наук. М., 2012. 24 с.
- Богута Д.Л., Руднев B.C., Терлеева О. П. Влияние переменной поляризации на характеристики микроплазменных слоев, формируемых из полифосфатных электролитов // Журнал прикладной химии, 2005. Т. 78. Вып. 2. С. 253−259.
- Богута Д.Л., Руднев В. В., Гордиенко П. С. Влияние формы тока на состав и характеристики получаемых анодно-искровых покрытий // Защита металлов, 2004. Т. 40. № 3. С. 299−303.
- Беспалова О.В., Борисов A.M., Мичурина В. П. и др. Изучение микродугового оксидирования и наполнения МДО-покрытий на алюминиевых сплавах с использованием спектрометрии ЯОР протонов // Физика и химия обработки материалов, 2003. № 1. С. 66−70.
- Pat. US 6 264 817. Method for microplasma oxidation of valve metals and their alloys / Timoshenko A.V., Rakoch. A.G.- 24.07.2001.
- Красноярский В.В. Подземная коррозия металлов и методы борьбы с ней. М.: Высшая школа, 1962. 216 с.
- Жук Н. П. Курс теории коррозии и защиты металлов. Учебное пособие для вузов. 2-е изд. М.: ООО ТИД «Альянс», 2006. 472 с.
- Жук Н. П. Курс теории коррозии и защиты металлов. М.: Металлургия, 1968. 407 с.
- Улиг Г. Г., Реви Р. У. Коррозия и борьба с ней. Введение в коррозионную науку и технику: Пер. с англ. / Под ред. А. М. Сухотина. Л.: Химия, 1989. — Пер. изд., США, 1985. 456 с.
- Gunterschulze A., Betz Н. Electrolytic rectifying action // Z. Pfys., 1932. Vol. 78. P. 196−210.
- Гюнтершульце А., Бетц Г. Электролитические конденсаторы / Оборонгиз., 1938. 200 с.
- Ракоч А.Г., Хохлов В. В., Баутин В. А., Лебедева Н. А., Магурова Ю. В., Бардин И. В. Модельные представления о механизме микродугового оксидирования металлических материалов и управление этим процессом // Защита металлов, 2006. Т. 42. № 2. С. 173−184.
- Ракоч А.Г., Магурова Ю. В., Бардин И. В., Эльхаг Г. М., Жаринов П. М., Ковалёв B.JI. Экзотермическое окисление дна каналов микроразрядов при микродуговом оксидировании алюминиевых сплавов // Коррозия: материалы, защита, 2007. № 12. С. 36−40.
- Ракоч А.Г., Дуб А.В., Бардин И. В., Жаринов П. М., Щедрина И. И., Ковалёв B.JI. Влияние катодной составляющей тока на кинетику роста микродуговых покрытий на поверхности алюминиевых сплавов // Коррозия: материалы, защита, 2008. № 11. С. 30−34.
- Klapkiv M. D, Nykyforchyn Н. М, Posuvailo V. Spectral analysis of an electrolytic plasma in tht prjcess of synthesis of aluminium oxide // Mater. Sci., 1994. V. 30. P. 333−344.
- Dunleavy C.S., Golosnoy I.O., Curran J.A. Clyne T.W. Characterisation of discharge events during plasma electrolytic oxidation // Suface & Coatings Tecnology, 2009. V. 203. P. 3410−3419.
- Аверьянов E.E. Плазменное анодирование в радиоэлектронике / М.: Радио и связь, 1983. 80 с.
- Файззулин Ф.Ф., Аверьянов. Е. Е. Анодирование металлов в плазме. Казань: Изд-во КГУ, 1977. 128 с.
- Nie X., Leyland A., Song H.W., Yerokhin A.L., Dowey S.J., Matthews
- A. Thickness effects on the mechanical properties of micro-arc discharge oxide coatings on aluminium alloys 11 Surface and Coatings Technology, 1999. V. 116 119. P. 1055−1060.
- Щедрина И.И. Свойства и скорость образования покрытий на сплаве Д16 при проведении процесса микродугового оксидирования при различных режимах / Автореф. дис.. к.х.н. М., 2011 — 24 с.
- Wenbin Xue, Zhiwei Deng, Ruyi Chen, Tonghe Zhang, Hui Ma. Microstructure and properties of ceramic coatings produced on 2024 aluminum alloy by microarc oxidation // Journal of Materials Science, 2001. № 36. P. 26 152 619.
- R. McPherson, J. Mater. Sci. 8 (1973) 851. Вкниге есть полностью статья.
- Tajima S., Soda M., Mori Т., Baba N. Properties and mechanism of formation of a-alumina (Corundum) film by anodic oxidation of aluminium in bisulphate // Electrochim. Acta, 1959. V. l, P. 205−216
- Чалых Е.Ф. Справочник по углеграфитовым материалам / Л.: Химия, 1974. 206 с.
- Крылов В.Н., Вильк Ю. Н. Углеграфитовые материалы и их применение в химической промышленности / Л.: Химия, 1965. 145 с.
- Химическая энциклопедия / М.: Советская энциклопедия, 1988. Т.1.623 с.
- Бабичев А.П., Бабушкина Н. А., Братковский A.M. и др. Физические величины: Справочник / Под. ред. Григорьева И. С., Е. 3. Мейлихова. М.- Энергоатомиздат, 1991. 1232 с. ISBN 5−283−4 013−5.
- Лившиц Б.Г., Крапошин B.C., Линецкий Я. Л. Физические свойства металлов и сплавов / Под ред. Б. Г. Лившица. М.: Мир, 1982. 447 с.
- Жаринов П.М. Эффективные микроразряды и новые способы нанесения покрытий на изделия из алюминиевых сплавов. Автореф. дис.. к.х.н.-М., 2009−24 с.
- Колотыркин Я.М. Журнал Всесоюзного химического общества им.Д. И. Менделеева. 1975. Т.20, № 1. С. 59−65.
- Колотыркин Я.М. Металл и коррозия / М.: Металлургия, 1985. 88 с.
- Томашов Н.Д., Чернова Г. П. Теория коррозии и коррозионностойкие конструкционные сплавы: учебн. пособие для вузов / М.: Металлургия, 1993. 416 с.
- Акимов Г. В. Теория и методы исследования коррозии металлов / М.: Изд- во АН СССР, 1945.350 с.
- Батраков В.П. Коррозия и защита металлов. Труды ВИАМ / М.: Оборонгиз, 1962. С. 8−81.
- Томашов Н.Д. Теория коррозии и защиты металлов / М.: Изд во АН СССР, 1960. 480 с.
- Эванс Ю.Р. Коррозия и окисление металлов / М.: Машгиз, 1962. 856с.
- Скорчеллети В.В. Теоретические основы коррозии металлов. Л.:Химия, 1973. 263 с.
- Розенфельд И.Л. Коррозия и защита металлов / М.: Металлургия, 1970. 448 с.
- Ширяев С.О., Григорьев А. И., Морозов В. В. О некоторых особенностях появления ионов вблизи заряженной поверхности интенсивно испаряющегося электролита // Л.: Журнал технической физики, 2003. Т. 73. Вып. 7. С. 21−27.
- А.С. СССР № 657 908 Способ изготовления литейных форм и стержней / Караник Ю. А., Марков Г. А., Минин В. Ф. и др. опубл. в Бюл. № 15.1979.
- Терлеева О.П., Белеванцев В. И., Марков Г. А., Слонова А. И., Шулепко Е. К. Электрохимический микроплазменный синтез композиционных покрытий на графите / М.: Физика и химия обработки материалов, 2000, № 2. С. 35−39.
- Патент. Электрохимический способ получения покрытий на металлическом изделии / Ракоч А. Г., Дуб A.B., Гладкова A.A., Сеферян А. Г., Ковалев В. Л., Бардин И. В., Баутин В. А. (№ 2 012 113 340/02(20 161), 06.04.2012, положительное решение от 17.12.2012)
- Колачев Б.А., Елагин В. И., Ливанов В. А. Материаловедение и термическая обработка цветных металлов и сплавов / М.: МИСиС, 2001.416 с.
- Альтман М.Б., Абрамцумян С. М., Аристова З.Н и др. Промышленные алюминиевые сплавы: Справочник 2-е изд. / М.: Металлургия, 1984. 528 с.
- Фридляндер И.Н. Алюминиевые деформируемые конструкционные сплавы / М.: Наука, 1979. 208 с.
- Строганов Г. Б., Ротенберг В. А., Гершман Г. Б. Сплавы алюминия с кремнием / М.: Металлургия, 1977. 272 с.
- Ракоч А.Г., Nomine А., Гладкова A.A., Ковалёв В. Л., Бардин И. В. Эффективный режим микродугового оксидирования сплава МЛ5 // Известия ВУЗов. Цветная металлургия, 2012. № 5. С. 9−12.
- Ракоч А.Г., Баутин В. А., Бардин И. В., Ковалев В. Л. Механизмы и кинетические особенности микродугового оксидирования магниевого сплава МЛ5пч в электролитах, содержащих NH4 °F // Коррозия: Материалы, Защита. 2007. № 9. С. 7−13.
- Бардин И.В. Электрохимические режимы микродугового окасидирования алюминиевого и магниевого сплавов в щелочных электролитах // Автореф. дис.. к.х.н. М., 2009 — 24 с.
- Химия: справ, изд. / Шретер В., Лаутеншлегер К.-Х., Бибрак X. и др.: пер. с нем. -М.: Химия, 1989. пер. изд.: ГДР, 1986. 648 с.
- Физико-химические свойства окислов. Справочник / Самсонов Г. В. и др. М.: Металлургия, 1978. 472 с.
- Попова Н.Е. Кинетика формирования оксидных слоев на магнии и его сплавах с алюминием при микродуговом оксидировании / Автореф. дис. к.т.н, Саратов, 2000. — 18 с.
- Takaya М. Luminescence phenomena on anodized coating surface of magnesium alloys //Aluminium, 1989. V. 65. P. 1244−1248.
- Тимонова M.A. Защита от коррозии магниевых сплавов / М.: Металлургия, 1977. 160 с.
- Khaselev О., Weiss D., Yahalom J. Structure and composition of anodic films formed on binary Mg-Al alloys in KOH-aluminate solutions under continuous sparking // Corrosion Science. 2001. V. 43. P. 1295−1307.
- Ross R. Handbook of metal treatments and testing, second ed. / Chapman&Hall. Springer-Verlag New York: 1988. P. 592.
- Perrault G.G. Encyclopedia of electrochemistry of the elements V. 8 / M. Dekker. New York: 1973. P. 263.
- Khaselev O., Weiss D., Yahalom J. Anodizing of pure magnesium in KOH-aluminate solutions under sparking // J. Electrochem. Soc., 1999. V. 146. № 5. P. 1757−1761.
- Мровец С., Вербер Т. Современные жаростойкие материалы: Справ. Изд. / Металлургия. 1986. 360 с.
- Чавчанидзе А.Ш. Коррозионностойкие поверхностные твердые растворы: Учебное пособие / М.: МГУПП, 2002. 100 с.
- Кульга Г. Я. Влияние активных добавок на процессы диффузионного насыщения металлов: Дис. канд. тех. наук / М.: МИСиС, 1982. 112с.
- Ракоч А.Г., Жукарева О. В., Фукалова Е. В., Ковалев А. Ф. О механизме влияния фторидов на процесс окисления циркония и его сплава с ниобием на воздухе в широком диапазоне температур // Цветная металлургия. 1996. № 6. С. 56−59.
- Ракоч А.Г., Шкуро В. Г., Замалин Е. Ю., Жукарева О. В., Фукалова Е. В. Процесс высокотемпературного окисления материалов в присутствии активаторов и пассиваторов // Физика и химия обработки материалов. 1996. № 3. С. 113−116.
- Гельд П.В., Цхай В. А., Швейкин Г. П. Влияние Ме-Ме-взаимодействий на структурные и термодинамические свойства карбидов, нитридов и окислов металлов IVa и Va подгрупп // Неорганические материалы, 1967. Т. 2. № 10. С. 1835−1841.
- Цхай В.А., Гельд П. В. Влияние экранирования и величины перекрывания d-орбит на некоторые свойства эквиатомных оксидов и карбидов титана, ванадия, ниобия // Журнал структурной химии, 1964. Т. 5. № 2. С. 275−280.
- Тот JI. Карбиды и нитриды переходных металлов / М.: Мир, 1974.294 с.
- Цхай В.А., Гельд П. В. Влияние экранирования на некоторые фазовые и структурные свойства кубических карбидов переходных металлов пятой группы // Журнал физической химии, 1965. Т. 39. № 5. С. 1150−1156.
- Гельд П. В. Цхай В.А. Средние плотности валентных электронов в FeOx, VOx, TiOx // Журнал структурной химии, 1963. Т. 4. № 2. С. 235−244.
- Цхай В. А. Гельд П.В. Статистический расчет распределения атомов и вакансий в оксикарбидах тугоплавких металлов // Журнал физической химии, 1971. Т. 45. № 9. С. 2129−2138.
- Цхай В.А., Гельд П. В. О топографии вакансий в карбидах переходных металлов IV и V групп со структурой NaCl // Журнал структурной химии, 1963. Т. 5. № 2. С. 576−582.
- Попов Ю.А. Теория взаимодействия металлов и сплавов с коррозионно-активной средой / М.: Наука, 1995. 200 с.
- Пат. RU 2 221 077 С1, МКИ: 7 С 23 С 8/12 Способ обработки поверхности металлических материалов / Ракоч А. Г., Хохлов В. В., Костерина М. Л. № 2 003 105 69/02- заявл. 21.02.2003- опубл. 10.01.2004.
- Хохлов В.В., Ракоч А. Г., Костерина М. Л. и др. Коррозия стали 10 в водных растворах NH4 °F и при последующем ее нагреве на воздухе. // Коррозия: материалы, защита, 2004. № 4. С. 2−8.
- Хохлов В.В., Ракоч А. Г., Костерина М. Л. Влияние предварительной обработки стали 10 в насыщенном водном растворе NH4 °F на процесс ее высокотемпературного окисления на воздухе // Защита металлов, 2004. Т. 40. № 3.С. 1−5.
- Воробьева A.M., Уткина E.A., Ходин А. А. Исследование механизма самоорганизации при формировании самоупорядоченной пористой структуры анодного оксида алюминия // Микроэлектроника, 2007. Т.36. № 6. С. 437−445
- Гриднев А.Е. Формирование системы концентраторов поля при образовании анодных оксидов алюминия как результат ударной ионизации // Вестник ВГУ. Серия физика, математика, 2008. № 1. С.11−16.
- Thompson G.E. Porous anodic alumina: fabrication, characterization and application // Thin Solid Film., 1997. V. 297. P. 1258.
- Parkhutik V.P., Shershulskii V.I. Theoretical modeling of porous oxide growth on aliminum // J. Phys. D.: Appl. Phys., 1992. V. 25. P. 1258.
- Shimizu К. Electroluminescence of njn destructive electronic avalance // Electrochim. Acta., 1978. V. 23. P. 605.
- Klein N. A theory of localized breakdown in insulating films // Adv. Phys., 1972. V. 21. P. 605.
- Akahori H. Electron microscopic study of growing mechanism of aluminium anodic oxide film // Journal of Electron Microscopy, 1961. V. 10. № 3. P. 175−185.
- Palibroda E. Le mecanisme du developpement de l’oxyde poreux de l’aluminium II. L’oxyde poreux et la tension electrique de la couche barriere // Surface technology, 1984. V. 23. № 4. P. 341−351.
- Palibroda E. Aluminium porous oxide growth-II. On the rate determining step // Electrochimica acta., 1995. V. 40. № 8. P. 1051−1055.
- Palibroda E. Le mecanisme du developpement de l’oxyde poreux de l’aluminium III: Le regime transitoire I (t) a v constante // Surface technology, 1984. V. 23. № 4. P. 353−365.
- Palibroda E. Aluminium porous oxide growth. On the electric conductivity of the barrier layer // Thin solid films, 1995. V. 256. № 1−2. P. 101 105.
- Palibroda E., Farcas T., Lupsan A. A new image of porous aluminium oxide // Materials Science and Engineering B, 1995. V. 32. № 1−2. P. 1−5.
- Одынец JI.JI., Орлов B.M. Анодные оксидные пленки / Л.: Наука, 1990. 200 с.
- Matykina E., Arrabal R., Mohamed A., Skeldon P., Thompson G.E. Plasma electrolytic oxidation of pre anodized aluminium // Corros. Sci., 2009, V.51.P. 2897 -2905.
- Сеферян А.Г. Энергосберегающие комбинированные режимы получения защитных микродуговых покрытий на сплаве Д16 // Автореф. дис.. к.х.н.-М., 2012.-24 с.
- Ракоч А.Г., Сеферян А. Г., Номинэ А. О кинетических особенностях роста покрытия на поверхности сплава Д16 при сменетехнологических режимов анодирования // Коррозия: Материалы, Защита, 2012. № 7. С. 38−46.
- Хла Мо. Оптимизация процесса микродугового оксидирования алюминиевых и магниевых сплавов: Автореф.канд. тех. наук. -М, 2007. 24 с.
- Хохлов В.В., Ракоч А. Г., Хла Мо, Жаринов П.М., Баутин В. А., Бардин И. В. Влияние силиката натрия на механизм роста оксидно-керамических при микродуговом оксидировании алюминиевых сплавов // Коррозия: материалы, защита, 2007. № 1. С. 28−33.
- Снежко J1.A., Тихая Л. С., Удовенко Ю. Э., Черненко В. И. Анодно-искровое осаждение силикатов на переменном токе // Защита металлов, 1991. Т. 27. № 3. С. 425−430.
- ГОСТ 13 078–81. Стекло натриевое жидкое. Технические условия. М., 1981.11, 15 с.
- Дамаскин Б.Б., Петрий O.A., Цирлина Г. А. Электрохимия -2-е изд., испр. и перераб. / М. Химия, КолосС, 2006. 672 с.
- Самсонов Г. В., Эпик А. П. Тугоплавкие покрытия / М.: «Металлургия», 1973. 399 с.
- Эпельфельд A.B., Людин В. Б., Дунькин О. Н., Невская О. С. Характер разряда в системе металл-оксид-электролит при микродуговом оксидировании на переменном токе // Известия АН. Серия Физическая, 2000. Т. 64. № 4. С. 759−762.
- Марков Г. А., Белеванцев В. И., Терлеева О. П., и др. Износостойкость покрытий, нанесенных анодно-катодным микродуговым методом // Трение и износ, 1988. Т. 9. № 2. С. 286−290.
- Слонова А.И., Терлеева О. П., Марков Г. А. О роли состава силикатного электролита в анод но-катодных микродуговых процессах // Защита металлов, 1997. Т. 33. № 2. С. 208−212.
- Марков Г. А., Слонова А. И., Терлеева О. П. Химический состав, структура и морфология микроплазменных покрытий // Защита металлов, 1997. Т.33.№ 3. С. 289−294.
- Марков Г. А., Белеванцев В. И., Терлеева О. П. Микродуговое оксидирование//Вестник МГТУ. Сер. Машиностроение, 1992. № 1. С. 34−56.
- Терлеева О.П., Белеванцев В. И., Слонова А. И., Богута Д. Л., Руднев И. С. Сравнительный анализ формирования и некоторых характеристик микроплазменных покрытий на алюминиевом и титановом сплавах // Защита металлов, 2006. Т. 42. № 2. С. 1−8.
- Марков Г. А. Татарчук В.В., Миронова М. К. Микродуговое оксидирование алюминия в концентрированной серной кислоте // Изв. СО АН СССР. Сер. хим. наук, 1983. № 7. Вып. 2. С. 34−37.
- Саакиян Л.С., Эпельфельд A.B., Ефремов А. П. Развитие представлений Г. В. Акимова о поверхностной оксидной пленке и ее влиянии на коррозионно-механическое поведение алюминиевых сплавов // Защита металлов, 2002. Т. 38. № 2. С. 186−191.
- Ракоч Ф.Г., Дуб A.B., Бардин. И.В., Ковалев В. Л. Щедрина И.И., Сеферян А. Г. К вопросу о влиянии комбинированных режимов на предельную толщину микродуговых покрытий // Коррозия, материалы, защита, 2009. №i i. с. 32−36.
- Jaspard-Mecuson F., Czerwiec Т, Henrion G. et al. Tailored aluminium oxide layers by bipolar current adjustment in the plasma electrolytic oxidation (PEO) process // Surf. Coat. Technol., 2007. № 201. P. 8677−8682.
- Терлеева О.П., Уткин B.B., Слонова А. И. Особенности изменений напряжения в сложных токовых режимах микроплазменных процессов // Защита металлов, 1999. Т. 35. № 2. С. 192−195.
- Белов В.Т. О проблемах теории окисления алюминия // Защита металлов, 1992. Т. 28. № 4. С. 643−648.
- Акимов Г. В., Томашов Н. Д., Тюкина М. Н. Механизм анодного окисления алюминия в серной кислоте // «Журнал общей химии». 1942. Т. 12. № 11. С. 12−17.
- Заливалов Ф.П., Тюкина М. Н., Томашов Н. Д. Влияние условий электролиза на формирование и рост анодных оксидных пленок на алюминии. «Журнал физической химии», 1961. Т.35, № 4. С. 879−890.
- Богоявленский А.Ф. О механизмах образования оксидной пленки на алюминии. Сб. «Анодная защита металлов» / М.: Машиностроение, 1964. С. 22−27.
- Одынец Л.Л., Орлов В. М. Анодные оксидные пленки / Л.: Наука, 1990. 200 с.
- Францевич И.Н., Пилянкевич А. Н., Лавренко В. А., Вольфсон А. И. Анодные оксидные покрытия на металлах и анодная защита / Киев: Наукова Думка, 1985. 280 с.
- Синявский B.C., Вальков В. Д., Будов Г. М. Коррозия и защита алюминиевых сплавов / М.: Металлургия, 1979. 224 с.
- Синявский B.C., Вальков В. Д., Калинин В. Д. Коррозия и защита алюминиевых сплавов / М.: Металлургия, 1986. 368 с.
- Dewald J.F. A theory of the kinetics of formation of anode films at high fields // Journal of the Electrochemical Society, 1955. V. 102. № 1. P. 1−6.
- Голубев А.И. Анодное окисление алюминиевых сплавов / М.: Изд. АН СССР, 1961.200 с.
- Голубев А.И., Утянская А. И. Процессы, протекающие на алюминиевых сплавах при анодировании в серной кислоте. Сб. «Размерное травление и анодирование алюминиевых сплавов» // М.: МДНТП, 1959. Вып. 1. 55 с.
- Шрейдер А.В. Оксидирование алюминия и его сплавов / М.: Металлургиздат, 1980. 198 с.
- Тимошенко А.В., Ракоч А. Г., Микаелян А.С, Защита от коррозии. Неметаллические покрытия и жаростойкие материалы / М.: Каравелла. 1997.336 с.