Определение допусков основных видов соединений и решение размерных цепей
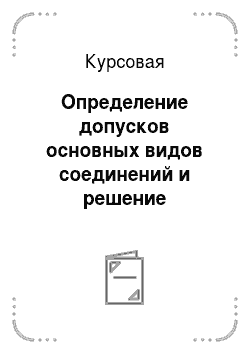
Принимаем предельные отклонения составляющих звеньев равными допуску на изготовление. Знак предельных отклонений назначаем для увеличивающих (охватывающих) размеров — как для основного отверстия (знак «+»), а для уменьшающих (охватываемых) размеров — как для основного вала (знак «-»). В соответствии с исходными данными выбрать посадки для соединения внутреннего кольца подшипника с валом… Читать ещё >
Определение допусков основных видов соединений и решение размерных цепей (реферат, курсовая, диплом, контрольная)
Курсовая работа
по дисциплине: Машиностроение
«Определение допусков основных видов соединений и решение размерных цепей»
допуск соединение размерная цепь Задание № 1. Расчет предельных размеров элементов гладкого цилиндрического соединения и калибров Задание № 2. Определение допусков и предельных размеров шпоночного соединения Задание № 3. Определение допусков и предельных размеров шлицевого соединения Задание № 4. Выбор посадки подшипника качения на вал и в корпус Задание № 5. Определение предельных размеров деталей резьбового соединения Задание № 6. Расчет сборочных размерных цепей
Задание № 1. Расчет предельных размеров элементов гладкого цилиндрического соединения и калибров
Цель работы
1. Усвоить основные понятия и термины, а также научиться определять предельные размеры, зазоры (натяги) и допуски.
2. Приобрести навыки пользования стандартами для определения предельных отклонений.
3. Научиться правильно оформлять чертежи с обозначением посадок, допусков и предельных отклонений.
4. Освоить методику расчета предельных калибров для контроля гладких цилиндрических соединений.
Расчет гладкого цилиндрического соединения
Исходные данные:
Ш80 — посадка с зазором в системе вала.
Ш80 — переходная посадка в системе вала.
Ш80 — посадка с натягом в системе вала.
Расчет для посадки с натягом Ш80 в системе вала
По ГОСТ 25 347–82 определим предельные отклонения отверстия и вала:
ES=-0,037 (мм) | es=0(мм) | |
EI=-0,091 (мм) | ei=-0,035 (мм) | |
Расчет для посадки с зазором Ш80 в системе вала
По ГОСТ 25 347–82 определим предельные отклонения отверстия и вала:
ES=+0,126 (мм) | es=0(мм) | |
EI=0,072 (мм) | ei=-0,035 (мм) | |
Расчет для переходной посадки Ш80 в системе вала
1. По ГОСТ 25 347–82 определим предельные отклонения отверстия и вала:
ES=+0,027 (мм) | es=0(мм) | |
EI=-0,027 (мм) | ei=-0,035 (мм) | |
2. Вычислим предельные размеры отверстия и вала:
Dmax=D+ES=80+0,027=80,027 (мм)
Dmin=D+EI=80−0,027=79,973 (мм);
dmax=D+es=80 (мм);
dmin=D+ei=80−0,035=79,965 (мм).
3. Определим величину допуска отверстия и вала:
TD=Dmax-Dmin=80,027−79,973=0,054 (мм);
Td= dmaxdmin=80−79,965=0,035 (мм).
4. Найдем величину наибольшего предельного зазора, натяга и допуска посадки:
Smax= Dmaxdmin=80,027−79,965=0,062 (мм);
Nmax= dmaxDmin=80−79,973=0,027 (мм);
T (S, N)=| Smax |+| Nmax |=0,062+0,027=0,089 (мм).
5. Так как посадка переходная, то определим вероятность получения зазоров и натягов в соединении, а также вероятные их величины.
Для заданной посадки Ш80 зазор может быть в пределах от 0 до 62 мкм, натяг — от 0 до 27 мкм. Допуск посадки составляет 89 мкм.
Считаем, что рассеивание размеров отверстия и вала, а также зазоров (натягов) подчиняется закону нормального распределения, и допуск деталей равен полю рассеивания, т. е. T=6у.
Учитывая принятые условия, получим:
(мкм); (мкм).
Среднее квадратическое отклонение для распределения зазоров и натягов в посадке:
(мкм).
Dm=(Dmax+ Dmin)/2=(80,027+79,973)/2=80 (мм);
dm=(dmax+ dmin)/2=(80+79,965)/2=79,983 (мм);
При средних значениях размеров отверстия Dm и вала dm получаем зазор S:
S= Dmdm=80−79,983=0,017 (мм)=17 (мкм).
Вычислим вероятность того, что значения зазора находятся в пределах от 0 до 17 мкм, т. е. найдем площадь, ограниченную линией симметрии кривой Гаусса и ординатой, расположенной в 17 мкм от линии симметрии.
Вероятность получения зазора определим с помощью интегральной функции вероятности Ф (z) — функции Лапласа, где z — предел интегрирования, Пользуясь таблицей значений интегралов Ф (z), находим Ф (z)= Ф (2,27)=0,4394.
Вероятность получения зазоров в соединении: 0,5+0,4394=0., 9394 или 93,94%.
Вероятность получения натягов: 1−0,9394=0,0606 или 6,06%.
Вероятный зазор равен: -17+3 =-17+3· 11=16 мкм.
Вероятный натяг равен: -17−3=-17−3· 11=-50 мкм.
6. Вычислим предельные и исполнительные размеры гладких рабочих калибров для контроля годности отверстия D=80 мм и допуском Js8, а также вала d=80 мм и допуском h7.
6.1. По ГОСТ 24 853–81 определим числовые значения величин, необходимых для расчета калибров:
a) для калибр-пробки H=6 мкм; Z=8 мкм; Y=8 мкм;
b) для калибр-скобы H1=6 мкм; Z1=5 мкм; Y1=4 мкм.
6.2. В соответствии с вышеприведенными формулами определяем предельные размеры калибров:
a) калибр-пробка:
ПРmax=Dmin+Z+H/2=79,973+0,008+0,003=79,984 (мм);
ПРmin=Dmin+Z-H/2=79,973+0,008−0,003=79,978 (мм);
ПРИЗН=Dmin-Y=79,973−0,008=79,965 (мм);
НЕmax=Dmax+H/2=80,027+0,003=80,03 (мм);
НЕmin=Dmax-H/2=80,027−0,003=80,024 (мм).
b) калибр-скоба:
ПРmax=dmax-Z1+H½=80−0,005+0,003=79,998 (мм);
ПРmin=dmax-Z1-H½=80−0,005−0,003=79,992 (мм);
ПРИЗН =dmax+Y1=80+0,004=80,004 (мм);
НЕmax=dmin+H½=79,965+0,003=79,968 (мм);
НЕmin=dmin-H½=79,965−0,003=79,962 (мм).
6.3. Определим исполнительные размеры калибров:
a) калибр-пробка:
ПРИСП =79,984−0,006 (мм);
НЕИСП =80,03−0,006 (мм).
b) калибр-скоба:
ПРИСП =79,992+0,006 (мм); НЕИСП =79,962+0,006 (мм).
Задание № 2. Определение допусков и предельных размеров шпоночного соединения
Цель работы
В соответствии с заданным типом шпоночного соединения определить допуски и предельные размеры всех элементов соединения, а также представить схему расположения полей допусков по ширине шпонки и сборочный чертеж шпоночного соединения.
Расчет шпоночного соединения
Шпонка призматическая, исполнение В, соединение свободное. Диаметр вала — 30 мм, длина шпонки — 50 мм.
1. Определим номинальные размеры элементов шпоночного соединения по ГОСТ 23 360–78: b=8 мм; h=7 мм; t1=4,0 мм; t2=3,3 мм; (d-t1)=26 мм; (d+t2)=33,3 мм.
2. Определим допуски непосадочных размеров по ГОСТ 23 360–78:
— высота шпонки h=7h11=7−0,090 мм;
— глубина паза вала t1=4,0+0,2 мм;
— глубина паза втулки t2=3,3+0,2 мм;
— (d-t1)=26−0,2 мм;
— (d+t2)=33,3+0,2 мм;
— длина шпонки l=50h14=50−0,74 мм;
— длина паза вала под шпонку l1=50H15=50+1,2 мм.
3. Определим допуски на посадочные размеры элементов шпоночного соединения по ширине шпонки b по ГОСТ 23 360–78:
— ширина шпонки 8h9=8−0,036 мм;
— ширина паза вала 8H9=8+0,036 мм;
— ширина паза втулки 8D10=6 мм.
Задание № 3. Определение допусков и предельных размеров шлицевого соединения
Цель работы
Для прямобочного шлицевого соединения с заданным числом зубьев, номинальными размерами и характером соединения выбрать способ центрирования.
Определить допуски и предельные размеры всех элементов соединения. Построить схему расположения полей допусков, посадок и представить чертеж шлицевого соединения.
Расчет прямобочного шлицевого соединения
1. Исходные данные: неподвижное шлицевое соединение с номинальными размерами 8*36*42.
2. По ГОСТ 1139–80 находим размер b=7мм, d1=33,5 мм. В данном случае целесообразно выбрать центрирование по наружному диаметру D. Посадки выбираем по ГОСТ 1139–80:
— для размера D — ;
— для размера b — ;
— для размера d (не центрирующий диаметр) — .
Обозначение шлицевого соединения:
D — 6*28*34*7.
3. По ГОСТ 25 347–82 определим предельные отклонения диаметров:
— отверстие 42H7=42+0,025;
— отверстие 36H11=36+0,160;
— вал 42f7=42;
— ширина впадины втулки 7F8=7;
— ширина зуба вала 7f8=7.
Задание № 4. Выбор посадки подшипника качения на вал и в корпус
Цель работы
В соответствии с исходными данными выбрать посадки для соединения внутреннего кольца подшипника с валом и наружного кольца с корпусом. Представить схемы расположения полей допусков деталей соединения, а также чертежи посадочных поверхностей вала, корпуса и сборочного узла.
Выбор посадки подшипника качения
1. Исходные данные:
— условное обозначение подшипника — 317;
— класс точности — 6;
— радиальная нагрузка Fr=2000 Н.
Внутреннее кольцо испытывает местное нагружение, наружное кольцо — циркуляционное. Режим работы — перегрузка до 150%.
2. По условному обозначению подшипника качения определим его основные размеры (ГОСТ 8338−75):
— диаметр отверстия внутреннего кольца d=85 мм;
— диаметр наружного кольца D=180 мм;
— ширина подшипника B=41 мм;
— радиус закругления фаски r=4 мм;
— рабочая ширина посадочного места b=B-2· r=41−2·4=33 мм.
3. По ГОСТ 520–89 определим предельные отклонения на изготовление колец подшипника:
— для d=85 (внутреннее кольцо) ES=0; EI=-15 мкм;
— для D=180 (наружное кольцо) es=0; ei=-20 мкм.
4. Выбираем посадку циркуляционно нагруженного внутреннего кольца подшипника по интенсивности радиальной нагрузки PR на посадочную поверхность вала, которую рассчитываем по формуле:
где k1 — при перегрузке до 150% k1=1;
k2 — вал сплошной, k2=1;
k3 — подшипник однорядный без осевой нагрузки на опору, k3=1.
Тогда
кН/м.
Такой интенсивности радиальной нагрузки соответствует допуск вала jS6.
Для наружного кольца подшипника, испытывающего циркуляционное нагружение, по ГОСТ 3325–55 назначаем допуск посадочной поверхности отверстия в корпусе H6.
5. Определим предельные отклонения размеров вала и отверстия корпуса по ГОСТ 25 347–82:
— для вала Ш85 jS6 es=+0,011 мм; ei=-0,011 мм;
— для отверстия корпуса Ш180 H6 ES=+0,025 мм; EI=0.
6. По ГОСТ 520–89 определим шероховатость поверхности посадочных мест вала и отверстия корпуса. Для посадочной поверхности вала и отверстия корпуса Ra — не более 1,25 мкм, для торцов заплечиков валов и отверстий корпусов Ra — не более 2,5 мкм.
7. Вычислим допуски формы (овальность и конусообразность) посадочных мест вала и отверстия корпуса.
Для посадочной поверхности вала:
0,5Td=0,5· 0,022=0,011 мм, для посадочной поверхности отверстия корпуса:
0,5TD=0,5· 0,025=0,0125 мм.
8. По ГОСТ 520–89 определим допускаемое торцовое биение заплечиков вала и отверстия корпуса.
— для заплечиков вала Д=0,012 мм;
— для заплечиков отверстия корпуса Д=0,030 мм.
Задание № 5. Определение предельных размеров деталей резьбового соединения
Цель работы
1. Усвоить основные параметры метрической резьбы и их обозначения на чертеже.
2. Приобрести навыки пользования стандартами для определения предельных диаметров болта и гайки и правильно производить их расчет.
3. Научиться оформлять чертежи с обозначением полей допусков и посадок резьбового соединения.
Расчет предельных размеров деталей резьбового соединения
1. Задано резьбовое соединение M24*1 — 6H/6h. По ГОСТ 24 705–81 определим номинальные размеры основных элементов резьбового соединения:
— наружный диаметр болта и гайки d=D=24 мм;
— средний диаметр болта и гайки d2=D2=23,35 мм;
— внутренний диаметр болта и гайки d1=D1=23,918 мм;
— шаг резьбы P=1 мм;
— угол профиля резьбы б=60°.
2. Определим предельные отклонения диаметров болта и гайки резьбы по ГОСТ 16 093–81.
Предельные отклонения болта при допуске 6h:
— для d2, d, d1 верхнее отклонение es=0;
— для d2 нижнее отклонение ei=-125 мкм;
— для d нижнее отклонение ei=-180 мкм;
— для d1 нижнее отклонение не регламентируется.
Предельные отклонения гайки при допуске 6H:
— для D2, D, D1 нижнее отклонение EI=0;
— для D2 верхнее отклонение ES=+170 мкм;
— для D верхнее отклонение не регламентируется;
— для D1 верхнее отклонение ES=+236 мкм.
3. Вычислим предельные размеры болта и гайки:
dmax= d + es = 48+0=24 мм;
dmin= d + ei = 24−0,180=23,820 мм;
d2 max= d2 + es = 23,35+0=23,35 мм;
d2 min= d2 + ei = 23,35−0,125=23,225 мм;
d1 max= d1 + es = 23,918+0=23,918 мм;
d1 min — стандартом не регламентируется;
Dmax — стандартом не регламентируется;
Dmin= D + EI = 24+0=24 мм;
D2 max= D2 + ES = 24,35+0,170=23,520 мм;
D2 min= D2 + EI = 23,35+0=23,35 мм;
D1 max= D1 + ES = 23,918+0,236=24,154 мм;
D1 min= D1 + EI = 23,918+0=23,918 мм.
4. Определим величины зазоров в соединении:
— по наружному диаметру:
Smin= Dmin — dmax= 24−24=0;
— по среднему диаметру:
Smax= D2 max — d2 min= 23,520−23,225=0,295(мм) = 295(мкм);
Smin= D2 min — d2 max= 23,35−23,35=0.
Задание № 6. Расчет сборочных размерных цепей
Цель работы
Выполнить расчет заданной размерной цепи способом допусков одного квалитета двумя методами — максимума-минимума и теоретико-вероятностным.
Расчет сборочной размерной цепи
Вал редуктора установлен на подшипниках качения 6−217. Предельные отклонения на изготовление подшипников качения по ширине принимаем по ГОСТ 520–89 в зависимости от диаметра внутреннего кольца, который в данном случае равен d=85 мм.
Имеем верхнее отклонение по ширине колец подшипника, равное 0, и нижнее отклонение, равное -200 мкм. Тогда при заданной ширине В=28 мм подшипника 6−217 звенья А4 и А8 имеют размер А4= А8= мм. Остальные составляющие звенья размерной цепи имеют следующие номинальные значения: А1=270 мм; А2=5 мм; А3=25 мм; А5=20 мм; А6=60 мм; А7=102 мм; А9=6 мм; А10=8мм.
Замыкающее звено А0 имеет предельные отклонения: верхнее ES (А0)=+680 мкм; нижнее EI (А0)=+060 мкм.
Предварительно рассчитаем следующие данные:
а) номинальный размер замыкающего звена:
где — сумма номинальных размеров увеличивающих звеньев;
— сумма номинальных размеров уменьшающих звеньев.
(мм);
б) допуск замыкающего звена:
(мкм);
в) среднее отклонение поля допуска замыкающего звена:
(мкм);
г) допуск на ширину колец подшипников качения:
(мкм);
д) среднее отклонение поля допуска 4-го и 8-го звеньев:
(мкм).
Расчет размерной цепи методом максимума-минимума
Решение первой задачи:
1. Рассчитаем допуск составляющих звеньев размерной цепи по способу допусков одного квалитета. Определим единицу допуска составляющих звеньев с учетом их номинального размера.
Рассчитаем среднее число единиц допуска составляющих звеньев цепи с учетом известных допусков ТА4 и ТА8:
где m — общее число звеньев размерной цепи, m=11;
q — число звеньев цепи с известными допусками по условию задачи (звенья 4 и 8), q=2;
ij — единица допуска составляющих звеньев.
По найденному значению аm выберем ближайший квалитет. Для всех звеньев цепи, кроме А1, примем 7-й квалитет. Для А1 (наиболее сложное звено) примем 8-й квалитет. Так как аm не равно значению, а по ГОСТ 25 346–89, то одно из звеньев цепи необходимо выбрать в качестве корректирующего. В данном случае за корректирующее примем звено А3, простое в изготовлении.
Назначим допуск составляющих звеньев с учетом их номинального размера и принятого квалитета по ГОСТ 25 346–89 и занесем в таблицу 1.
Определим допуск корректирующего звена из условия:
где ТА3 — допуск корректирующего звена.
Отсюда
(мкм)
2. Определим предельные отклонения составляющих звеньев цепи.
Принимаем предельные отклонения составляющих звеньев равными допуску на изготовление. Знак предельных отклонений назначаем для увеличивающих (охватывающих) размеров — как для основного отверстия (знак «+»), а для уменьшающих (охватываемых) размеров — как для основного вала (знак «-»).
3. Рассчитаем координату середины поля допуска составляющих звеньев.
Для этого определим среднее отклонение полей допусков составляющих звеньев, кроме корректирующего. Для любого составляющего звена цепи имеем:
.
Определим среднее отклонение поля допуска корректирующего звена А3 из выражения:
.
В итоге получим (мкм).
По найденной величине ЕС (А3) и допуску ТА3 рассчитаем предельные отклонения корректирующего звена:
(мкм)
(мкм)
Таблица 1. Сведения о расчете размерной цепи методом максимума-минимума (способ допусков одного квалитета)
Номер звена | мм | Характер действия на | Первая задача (проектная) | ||||||||
Квалитет | Исполнительный размер, мм | ||||||||||
мкм | |||||||||||
Ув. | 3,23 | 40,5 | — 81 | — 40,5 | 270-0,081 | ||||||
Ув. | 0,73 | — 12 | — 6 | 5-0,012 | |||||||
Ум. | 1,31 | — 180 | — 194 | — 187 | |||||||
Ум. | ; | 11−12 | — 200 | — 100 | 28-0,200 | ||||||
Ум. | 1,31 | 10,5 | — 21 | — 10,5 | 20-0,021 | ||||||
Ум. | 1,86 | — 30 | — 15 | 60-0,030 | |||||||
Ум. | 2,17 | 17,5 | — 35 | — 17,5 | 102-0,035 | ||||||
Ум. | ; | 11−12 | — 200 | — 100 | 28-0,200 | ||||||
Ув. | 0,73 | — 12 | — 6 | 6-0,012 | |||||||
Ум. | 0,9 | 7,5 | +15 | 7,5 | |||||||
Решение второй задачи:
Проверим замыкающее звено размерной цепи по следующим параметрам:
а) соответствие допуска замыкающего звена допускам составляющих звеньев:
(мкм);
б) соответствие среднему отклонению поля допуска замыкающего звена:
(мкм) в) предельные отклонения замыкающего звена:
(мкм);
(мкм);
Проверочный расчет размерной цепи показывает, что проектная задача решена верно.
Расчет размерной цепи теоретико-вероятностным методом
Решение первой задачи:
Считаем, что рассеивание отклонений размеров подчиняется закону нормального распределения, а границы их вероятного рассеивания совпадают с границами полей допусков.
1. Установим допуск составляющих звеньев. Для этого определим квадрат единицы допуска i2 составляющих звеньев с учетом их номинального размера, а затем рассчитаем среднее число единиц допуска составляющих звеньев с учетом известных допусков ТА4 и ТА8:
;
.
Установим по найденному значению аm ближайший квалитет. В данном случае для всех звеньев цепи примем 9-й квалитет. Корректирующим будет 3-е звено размерной цепи.
Назначим по ГОСТ 25 346–89 допуск составляющих звеньев размерной цепи с учетом их номинального размера и принятого квалитета.
Определим допуск корректирующего звена, исходя из условия:
;
;
Отсюда ТА3=25 (мкм).
2. Определим предельные отклонения составляющих звеньев, которые принимаем равными допуску для охватывающих размеров, как для основного отверстия (со знаком «+»), а для охватываемых размеров — как для основного вала (со знаком «-»).
3. Рассчитаем среднее отклонение полей допусков составляющих звеньев, которое определим по формуле:
.
Среднее отклонение поля допуска корректирующего звена определим из условия:
.
Отсюда ЕС (А3)=-150 (мкм).
При известных ЕС (А6) и ТА6 рассчитаем предельные отклонения корректирующего звена:
(мкм);
(мкм);
Таблица 2
Сведения о расчете размерной цепи теоретико-вероятностным методом (способ допусков одного квалитета)
Номер звена | мм | Характер действия на | Первая задача (проектная) | ||||||||
Квалитет | Исполнительный размер, мм | ||||||||||
мкм | |||||||||||
Ув. | 10,41 | — 130 | — 65 | 270-0,130 | |||||||
Ув. | 0,53 | — 30 | — 15 | 5-0,030 | |||||||
Ум. | 1,72 | 12,5 | — 137,5 | — 162,5 | — 150 | ||||||
Ум. | ; | 10−11 | — 200 | — 100 | 28-0,200 | ||||||
Ум. | 1,72 | — 52 | — 26 | 20-0,026 | |||||||
Ум. | 3,46 | — 74 | — 37 | 60-0,074 | |||||||
Ум. | 4,71 | 10−11 | — 140 | — 70 | 102-0,140 | ||||||
Ум. | ; | 10−11 | — 200 | — 100 | 28-0,200 | ||||||
Ув. | 0,53 | — 30 | — 15 | 6-0,030 | |||||||
Ум. | 0,81 | +36 | +18 | ||||||||
Решение второй задачи:
Проверим правильность расчета составляющих размеров по следующим параметрам замыкающего звена:
а) допуск замыкающего звена:
б) среднее отклонение поля допуска замыкающего звена:
в) предельные отклонения замыкающего звена:
1. Анурьев В. И. Справочник конструктора-машиностроителя. В 3-х т. — М.: Машиностроение, 1978. Т. 1−3.
2. Мочалов В. Д. Взаимозаменяемость и технические измерения. Метрология, стандартизация и сертификация: учебное пособие/ В. Д. Мочалов, А. А. Погонин, А. Г. Схиртладзе. — Белгород: Изд-во БГТУ, 2006. — 204с.
3. Мягков В. Д. Допуски и посадки: справочник: в 2 ч/В.Д. Мягков, М. А. Палей. — Л.: Машиностроение, 1982;1983.