Методы изготовления втулки
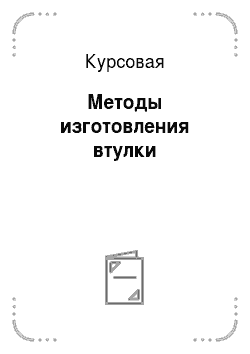
Серийное производство характеризуется ограниченной номенклатурой изделий, изготовляемых периодически повторяющимися партиями. При серийном производстве используются универсальные станки оснащенные специальными приспособлениями, специализированные станки, предназначенные для выполнения типовых операций. Главным видом оборудования являются станки с ЧПУ. Технологическая оснастка так же применяется… Читать ещё >
Методы изготовления втулки (реферат, курсовая, диплом, контрольная)
МИНИСТЕРСТВО ОБРАЗОВАНИЯ РОССИЙСКОЙ ФЕДЕРАЦИИ НОВОСИБИРСКИЙ ГОСУДАРСТВЕННЫЙ ТЕХНИЧЕСКИЙ УНИВЕРСИТЕТ Кафедра машиностроения
Расчетно-графическая работа
По дисциплине: «Прогрессивные производственные
технологии".
Вариант 010.
Выполнила: студентка 5 курса
Шмидт А.А.
Проверил: Никитин Ю.В.
г. Бердск, 20 010 г.
1. Описание детали
1.1 Материал детали и его свойства
1.2 Анализ технологичности детали
1.3 Определение типа производства и размера партии
1.3 Отнесение детали к типовой группировке
2. Выбор вида и метода получения заготовки
3. Определение припусков и размеров заготовки
4. Проектирование маршрута обработки детали
5. Режимы резанья
6. Выбор инструмента и оборудования
7. Разработка лазерного упрочнения
8. Проектирование операции ультразвукового деформирования
9. Расчет технологической себестоимости
10. Список использованных источников
1. Описание детали
Втулка — деталь машины, механизма, прибора цилиндрической или конической формы (с осевой симметрией), имеющая осевое отверстие, в которое входит сопрягаемая деталь.
1.1 Материал детали и его свойства
Втулка изготовлена из стали — 65 Г ГОСТ 4543–71
Сталь 65 Г ГОСТ 4543–71 Сталь качественная легированная.
Это сталь конструкционная, рессорно-пружинная.
Химический состав:
C | Si | Mn | Ni | S | P | Cr | Cu | |
0.62−0.7 | 0.17−0.37 | 0.9−1.2 | до 0.25 | до 0.035 | до 0.035 | до 0.25 | до 0.2 | |
Температура ковки:
Начала 1250, конца 780−760. Охлаждение заготовок на воздухе.
Технологические свойства стали 65Г
Свариваемость: | не применяется для сварных конструкций. | |
Флокеночувствительность: | малочувствительна. | |
Склонность к отпускной хрупкости: | склонна. | |
Обрабатываемость резаниемв закаленном и отпущенном состоянии б.ст. = 0,80. тв.спл. = 0,85, KB = 820 МПа Kпри НВ 240 и Плотностьпри 20 °C — 7,81×10ікг/мі.
Модуль нормальной упругости при 20 °C — 215 Гпа.
Удельная теплоемкость при 20−100°С — 490 Дж/(кг· °С)
Механические свойства
Термообработка, состояние поставки | Сечение, мм | s0,2, МПа | sB, МПа | d5, % | y, % | HRCэ | |
Сталь категорий: 3,3А, 3Б, 3 В, 3 Г, 4,4А, 4Б. Закалка 830 °C, масло, отпуск 470 °C. | Образцы | ||||||
Листы нормализованные и горячекатаные | |||||||
Закалка 800−820 °С, масло. Отпуск 340−380 °С, воздух. | 44−49 | ||||||
Закалка 790−820 °С, масло. Отпуск 550−580 °С, воздух. | 30−35 | ||||||
Механические свойства при повышенных температурах
(Закалка 830 °C, масло. Отпуск 350 °C.)
испытания, °C | s0,2, МПа | sB, МПа | d5, % | y, % | |
Механические свойства в зависимости от температуры отпуска
(Закалка 830 °C, масло.)
t отпуска, °С | s0,2, МПа | sB, МПа | d5, % | y, % | KCU, Дж/м2 | HRCэ | |
теплоемкость | теплопроводность | t. плав. | AC1 | м | |||||||||||
43,8 | 43,8 | 30,2 | 23,9 | — 465 | 0.271 | ||||||||||
Назначение:
Рессоры, пружины и другие детали, от которых требуется повышенные прочностные и упругие свойства, износостойкость; детали, работающие в условиях трения при наличии высоких статических и вибрационных нагрузок.
Таким образом, выбор материала для данной детали оправдан.
ПО чертежу детали видно, что форма отверстий позволяет :
— обрабатывать их напроход с одной двух сторон.
— есть свободный доступ инструмента к обрабатываемым поверхностям
— нет глухих отверстий.
— имеется паз.
1.2 Анализ технологичности детали
Деталь типа " втулка" представляет собой теловращение и является частью механизма станка.
Основными исполнительными поверхностями являются:
1) Наружная цилиндрическая поверхность 80с11
2) Наружная цилиндрическая поверхность 40e7
3) Поверхность центрального отверстия
4) Плоская поверхность (паз)
Самые высокие требования по точности по 7 квалитету 40e7 предъявляются наружной цилиндрической поверхности диаметром 40, что предполагает применение для получения этой поверхности чистовых и отделочных методов обработки:
· Тонкое точение
· Шлифование Требования к центральному отверстию могут быть обеспечены применением:
· Сверление
· Развертывание Наличие паза требует применения специальных приспособлений.
Резьбовая поверхность М 24 может быть изготовлена с помощью метчиков.
Минимальные требования шероховатости предъявлены к наружной цилиндрической поверхности 40e7. Они могут быть обеспечены применением упрочняющей отделочной обработке. (Обработка шаром, ультразвуковое ППД) Требования к остальным поверхностям могут быть получены обычными методами обработки.
Требования по твердости к поверхности В HRC 52…54 могут быть выполнены применением поверхностной закалки (ТВЧ) или с помощью лазера.
Количественная оценка технологичности производится расчетом ряда показателей, характеризующих отдельные свойства.
Коэффициент точности обработки детали:
Кто=(ni· ITi)/ N,
где ni — число поверхностей одного квалитета ITi, N — общее число поверхностей с нормируемой точностью.
Кто=(2*10)+(1*7)+(1*11)/4=9,5
Таким образом, точность обработки детали нормальная.
Коэффициент шероховатости поверхности:
Кш= (ni· Rai)/?N
где ni — число поверхностей одной шероховатости Rai, N — общее число поверхностей с нормируемой шероховатостью.
Кш=(1*0,2)/1=0,2
К шероховатости поверхности данной детали предъявлены высокие требования.
1.3 Определение типа производства и размера партии
Тип производства в значительной мере влияет на все технологические решения и на вид применяемой технологической оснастки. Тип производства определяют предварительно по массе детали. У нас m=1.03 кг, а программа выпуска № =18 000 штук в год. Получается как крупносерийное.
Серийное производство характеризуется ограниченной номенклатурой изделий, изготовляемых периодически повторяющимися партиями. При серийном производстве используются универсальные станки оснащенные специальными приспособлениями, специализированные станки, предназначенные для выполнения типовых операций. Главным видом оборудования являются станки с ЧПУ. Технологическая оснастка так же применяется как универсальная, так и специальная. С увеличением серийности производства применяется все больше специальной оснастки. Операции выполняются в одну установку с ограниченным числом переходов.
1.4 Отнесение детали к типовой группировке
Не смотря на все многообразие машиностроительных деталей производственный опыт позволяет достаточно точно классифицировать их на несколько основных классов, для каждого из которых существует вполне определенный типовой технологический процесс. Поэтому одним из первых этапов проектирования является отнесение оригинальной детали к одному из классов.
Наша деталь относится к классу «Втулка». Она характеризуется соотношением длины 70 мм к среднему диаметру 40 мм., в пределах 0,5< L/D <5. Также для втулок характерно наличие точных наружных и внутренних поверхностей, что наглядно показывает наш чертеж.
2. Выбор вида и метода получения заготовки
Способ получения заготовки определяется прежде всего материалом, из которого изготавливается заготовка, и конфигурацией детали: материал льется или штампуется, можно ли прошить отверстие такого диаметра и такой глубины и т. п. Обязательно учитывается тип производства, т.к. с повышением серийности становится возможным получать более точные и сложные заготовки, обеспечивая и большую экономию металла.
«Заготовка» — полуфабрикат детали, предназначенный для точной механической обработки путем снятия стружки (лишнего металла).
Расчет характеристик заготовок выполняется в специальной программе.
Результаты расчетов представлены ниже.
ПРОТОКОЛ РАСЧЁТА ЗАГОТОВКИ Исходные данные:
Материал детали (код) 2
Масса детали 1,19
Сложность детали 2
Объём производства, шт. 18 000
Число смен 2
Габаритные размеры 70×80×20
РАСЧЁТНЫЕ ДАННЫЕ Тип производства Крупносерийное Такт выпуска, мин 14
Размер партии, шт. 10
Вид заготовки (код) Штамповка на гориз.-ковочной машине Масса заготовки, кг 1,4
Коэффициент использования металла 0,85
Стоимость заготовки, руб. 24,7
ПРОТОКОЛ РАСЧЁТА ЗАГОТОВКИ Исходные данные:
Материал детали (код) 2
Масса детали 1,19
Сложность детали 2
Объём производства, шт 18 000
Число смен 2
Габаритные размеры 70×80×20
РАСЧЁТНЫЕ ДАННЫЕ Тип производства Крупносерийное Такт выпуска, мин 14
Размер партии, шт 10
Вид заготовки (код) Пруток горячекатанный
Диаметр и длина прутка. мм 90×73,3
Масса заготовки, кг 3,637 261
Коэффициент использования металла 0,45
Стоимость заготовки, руб. 38,3
ПРОТОКОЛ РАСЧЁТА ЗАГОТОВКИ Исходные данные:
Материал детали (код) 2
Масса детали 1,19
Сложность детали 2
Объём производства, шт. 18 000
Число смен 2
Габаритные размеры 70×80×20
РАСЧЁТНЫЕ ДАННЫЕ Тип производства Крупносерийное Такт выпуска, мин 14
Размер партии, шт 10
Вид заготовки (код) Штамповка на прессах (без прошивки отв.)
Масса заготовки, кг 1,35
Коэффициент использования металла 0,8
Стоимость заготовки, руб 13
Наилучшее использование материала имеет заготовка — Штамповка на прессах со стоимостью 13 руб.
3. Определение припусков и размеров заготовки
Так как, в качестве заготовки выбрана штамповка на прессах без прошивки отверстий, то необходимо, назначить припуски и определить размеры только для наружных размеров. Таким образом, необходимо рассчитать припуски на наружные цилиндрические поверхности диаметром 80 и 40 и торцевые поверхности длиной 70 мм и 50 мм.
«Припуск» — слой металла, который необходимо удалить для получения поверхности детали.
Припуск Zd — далется на весь диаметр.
Припуск Zl — припуск на сторону.
Величина припуска для заготовок может быть определена по следующим формулам:
Zd= D0,4· L0,05/ IT0,45 Zl= D0,3· L0,05
где Zd — припуск на наибольший диаметр детали, мм;
Zl — припуск на общую длину детали, мм;
D — наибольший диаметр детали, мм;
L — длина детали, мм;
IT — квалитет размера на диаметр детали D (6,7,…10).
D=80 мм.
L=70 мм
Zl= 800,3· 700,05 .=4,60 мм. Припуск на общую длину.
Zd= 800,4· 700,05/110,45 =2,43 Припуск на наибольший диаметр.
Рассчитываем величина припуска на диаметр заготовки
Z=0.15· D0,5·m0.22·KТ·Kсл
гдеD — размер, на который рассчитывается припуск, мм;
m — масса штамповки в кг;
KТ — коэффициент точности штамповки (KТ=1,0 штамповка I класса — точная; KТ=1,35 штамповка II класса — менее точная);
Z80=0.15· 800,5·(1,03*1,6)0.22·*1*1=1,50 мм.
Z40=0.15400,5· (1,03*1,6)0.22·*1*1=1,05 мм.
Получаем величину диаметра припусков заготовки:
80+(1,5*2)=83 мм.
40+(1,05*2)=42,10 мм.
Рассчитываем величину припуска на стороны заготовки:
Z=0.15· D0,5·m0.22·KТ·Kсл
гдеD — размер, на который рассчитывается припуск, мм;
m — масса штамповки в кг;
KТ — коэффициент точности штамповки (KТ=1,0 штамповка I класса — точная; KТ=1,35 штамповка II класса — менее точная);
Kсл — коэффициент сложности (Kсл=1 штамповка простая, Kсл=1,1 штамповка средней сложности, Kсл=1,3 штамповка высокой сложности).
Z70=0.15· 700,5·(1,03*1,6)0.22·*1*1=1,40 мм.
Z50=0.15· 500,5·(1,03*1,6)0.22·*1*1=1,18 мм.
Получаем величину сторон припусков заготовки:
70+1,4+1,4=72,8 мм.
50+(1,4−1,18)=50,22 мм Составляем эскиз заготовки
4. Проектирование маршрута обработки детали
— разработка маршрутов обработки отдельных поверхностей.
Наружная цилиндрическая поверхность 40e7, с длиной 50 мм, с
диаметр заготовки 42,10 мм.
Ш Обтачивание (75%) 0,75*1,05=0,79 мм Д1=40,22+(2*0,16)=40,54 мм.
Ш Шлифование предварительное (15%) 0,15*1,05=0,16 мм Д2=40+(2*0,11)=40,22 мм Ш Шлифование чистовое (10%) 0,10*1,05=0,11 мм Дз=Дд=40мм Ультразвуковое ППД позволяет снизить
Наружная цилиндрическая поверхность 80с11, с длиной 20 мм, с
Диаметр заготовки=83 мм.
Ш Обтачивание предварительное (80%) 0,8*1,5=1,2 мм.
Д1=80+(2*0,3) =80,06 мм.
Ш Обтачивание чистовое (20%) 0,2*1,5=0,3 мм.
Дз=Дд=80мм Наружная цилиндрическая поверхность d 38, с длиной 5 мм, с
Ш Обтачивание однократное Дз=Дд=38 мм Центральное отверстие, с длиной 70 мм, с
Ш Сверление Z1св =Дсв/|2=19,6/2=9,8 мм Д1=Д2−2Z2=20- (2*0,2)=19,6 мм Ш Развертывание (максимальный припуск=0,2 мм), Z1=0,2 мм.
Дз=Дд=20 мм Резьба в центральном отверстии М24
Ш Сверление (рассверливание) Zсв.=Д/2=21/2=10,5 мм Ш Нарезание резьбы метчиком Д св=Др-1,2*Sрез.=21-(1,2*2,5)=21 мм.
Z= (Др-дсв)/2=(21−21)/2=1,5 мм.
Др=Дд=24
Поверхность паза, с длиной 80 мм, с
Фрезерование черновое (75%) 0,75*14=10,5 мм
Z2=12,6−2,1=10,5 мм.
Фрезерование получистое (15%) 0,15*14=2,1 мм
Z2=14−1,4=12,6 мм.
Фрезерование чистовое (10%) 0,10*14=1,4 мм
Составление общего маршрута обработки детали.
Сначала делается черновая обработка всех поверхностей, потом предварительная, чистовая, тонкая и отделочная.
005 Вертикально сверлильная.
Тип станкавертикально-сверлильный.
Сверлить отверстие диаметром 19,6 мм на длину 70 мм.
Глубина резания t=Z=Дсв|2=9,8 мм.
Развертывать отверстие диаметром 20 мм на дину 70 мм.
Глубина резания t=Z=0,2 мм.
010 Токарная Тип станкатокарно-револьверный.
Точить однократно диаметром 40,54 на длину 50 мм.
Глубина резания t=Z=0,79 мм.
Точить диаметр 80,06 мм на длину 20
Глубина резания t=Z=1,2 мм
Точить канавку диаметром 38 мм, шириной 5 мм,
Lк обработки=(40−38)/2=1 мм.
Глубина резания t=Z=5 мм
015 Токарная Тип станкатокарно-револьверный.
Точить диаметр 80 мм на длину 20
Глубина резания t=Z=0,3 мм или 1,5
020 Шлифование Тип станкакругло-шлифовочный Шлифовать предварительно диаметр 40,22 длиной 50 мм Глубина резания t=Z=0,16 мм
025 Токарная Тип станкатокарно-револьверный.
Рассверлить отверстие под резьбу диаметр 21 мм, длиной 30 мм Глубина резания t=Z=(Др-Дсв)/2=(21−20)/2=0,5 мм
Нарезать резьбу метчиком на длину 30 мм Глубина резания t=Z=1,5 мм
030 Фрезерная Тип станкагоризонтально-фрезерный Фрезеровать паз диаметром 10,5 мм на длину 80 мм Глубина резания t=Z=10,5 мм
035 Фрезерная Тип станкагоризонтально-фрезерный Фрезеровать паз диаметром 12,6 мм на длину 80 мм Глубина резания t=Z=2,1 мм
040 Фрезерная Тип станка — горизонтально-фрезерный Фрезеровать паз диаметром 14 мм на длину 80 мм Глубина резания t=Z=1,4 мм
045 термическая Тип станкалазерно-технологический комплекс Закалить поверхность В лучом лазера до НRС 52…54 на длину 45 мм. (50−5)
050 Шлифовальная
Тип станка-кругло-шлифовальный Шлифовать поверхность диаметром 40, длиной 50 мм Глубина резания t=Z=0,11 мм
065 отделочная Тип станка — токарно-винторезный с комплексом ультразвукового оборудования Обрабатывать поверхность В до
5. Режимы резанья
Операция № 1 «Вертикально-сверлильная»
Проводим сверление поверхности центрального отверстия Rа 6.3 до 19,6 мм
Проводим развертывание поверхности центрального отверстия до 20 мм.
Операция " 2 «Токарная»
Проводим черновое обтачивание поверхности до 40,54 мм.
Обтачивание однократное поверхности до 80,06 мм
Черновое обтачивание канавки до 38 мм.
Операция № 3 «Токарная»
Проводим чистовое обтачивание поверхности до 80,00 мм.
Операция № 4 «Шлифовальная»
Проводим шлифование предварительное наружной поверхности до 40,22 мм.
Операция № 5 «Токарная»
Рассверливание отверстия (фаски) под резьбу до 21 мм.
Нарезание резьбы метчиком.
Операция № 6 «Фрезерная»
Обработка поверхности паза получистовой обработкой до 10.5 мм.
Операция № 7 «Фрезерная»
Обработка поверхности паза чистовой обработкой до 12,6 мм.
Операция № 8 «Фрезерная»
Обработка поверхности паза тонкой обработкой до 14 мм.
Операция № 9 «Шлифовальная»
Проводим шлифование чистовое наружной поверхности до 40,00 мм
Операция № 10 «Отделочная»
Обрабатывать поверхность В до с комплексом ультразвукового оборудования.
6. Выбор инструмента и оборудования
Операция № 05
Для обработки центрального отверстия Ш 20Н10, длиной 70 мм выбираем следующую модель станка:
Вид операции: Вертикально-сверлильный Модель станка: Вертикально-сверлильный 2Н125
Техническая характеристика | 2Н125 | |
Наибольший диаметр сверления по стали, мм | ||
Расстояние от центра шпинделя до направл. Б, мм | ||
Расстояние от торца шпинделя до стола В, мм | 5−700 | |
Кол-во ступеней частоты вращения шпинделя | ||
Наиб. и наим. частота вращения шпинделя | 45−2000 | |
Наиб. перемещение шпинделя, мм | ||
Конус Морзе шпинделя А | ||
Число ступеней подач | ||
Предел подач шпинделя, мм/об | 0,1−1,6 | |
Размеры стола, мм | 400×450 | |
Размер паза Г, мм | ||
Шаг пазов д, мм | ||
Мощность эл.двигат., кВт | 2,2 | |
Габариты станка в плане, мм | 1130×850 | |
Сверло цилиндрический хвостовик (ГОСТ 10 902−77) Ш20−189,98
(кол-во переточек -10),.
Развертка слесарная ГОСТ 7722–77 Ш20-129,80
(кол-во переточек -1)
Патрон сверлильный -600 руб
Стоимость инструмента: 919, 6
Стоимость станка: 55 000.00 руб.
Операция № 010
Для обработки наружной цилиндрической поверхности 40,54, длиной 50 мм выбираем следующую модель станка Вид операции: «Токарная»
Модель станка: Токарно-револьверный 1Е325
Техническая характеристика | 1Е325 | |
Наибольший диаметр обработки прутка, мм | ||
Наибольший диаметр обработки над станиной, мм | ||
Наибольший диаметр обработки над суппортом, мм | ||
Наибольшая длина обрабат. заготовки, мм | ||
Расстояние от шпинделя до револ. головки, мм | 107−400 | |
Кол-во ступеней частоты вращения шпинделя | ||
Наиб. и наим. частота вращения шпинделя | 80−3150 | |
Подача револьверного суппорта, мм/об | 0,05−1,3 | |
Кол-во ступеней подач револьверного суппорта | ||
Поперечная подача, мм/об | 0,05−1,3 | |
Мощность эл.двигат., кВт | ||
Габариты станка, мм | 3915×925 | |
Проходной резец — ГОСТ 18 879–73 -53,10
(кол-во переточек -3)
отрезной резец ГОСТ 18 880–73 (Т5К10)- 53,10
(кол-во переточек -3)
Токарный патрон-8800 руб.
Стоимость инструмента-8906,20 -
Стоимость станка:90 000 руб.
Операция № 015
Для обработки наружной цилиндрической поверхности 80с11, длиной 20 мм глубиной резанья 1,5 мм выбираем следующую модель станка Вид операции: «Токарная»
Модель станка: Токарно-револьверный 1Е325
Техническая характеристика | 1Е325 | |
Наибольший диаметр обработки прутка, мм | ||
Наибольший диаметр обработки над станиной, мм | ||
Наибольший диаметр обработки над суппортом, мм | ||
Наибольшая длина обрабат. заготовки, мм | ||
Расстояние от шпинделя до револ. головки, мм | 107−400 | |
Кол-во ступеней частоты вращения шпинделя | ||
Наиб. и наим. частота вращения шпинделя | 80−3150 | |
Подача револьверного суппорта, мм/об | 0,05−1,3 | |
Кол-во ступеней подач револьверного суппорта | ||
Поперечная подача, мм/об | 0,05−1,3 | |
Мощность эл.двигат., кВт | ||
Габариты станка, мм | 3915×925 | |
отрезной резец ГОСТ 18 880–73 (Т5К10)- 53,10
(кол-во переточек -3)
Токарный патрон-8800 руб.
Стоимость инструмента-8906,20 -
Стоимость станка: 90 000 руб.
Операция № 020
Для обработки наружной цилиндрической поверхности 40е7, длиной 50 мм, глубиной резанья 0,16 выбираем следующую модель станка Вид операции: «Шлифовальная»
Модель станка: Кругло-шлифовальный
Техническая характеристика | 3М150 | |
Наиб.диаметр обраб. заготовки, мм | ||
Наиб. длина обраб заготовки, мм | ||
Рекоменд. диаметр наруж. шлифования, мм | 10−45 | |
Наиб. длина наружного шлифования, мм | ||
Наиб. размеры шлиф. круга DxB, мм | 400×40 | |
Частота вращения шпинд. шлиф. бабки, об/мин | 2350; 1670 | |
Частота вращения шпинделя изделия (Б/ст), об/мин | 100−1000 | |
Скорость перемещения стола (бесступенч.), м/мин | 0,2−4 | |
Поперечная подача шлиф. бабки на одно дел. лимба, мм | 0,002 | |
Непрерывн. подача врезного шлиф. (б/ст), мм/мин | 0,05−0,5 | |
Мощность эл.двигат., кВт | ||
Габариты станка, мм | 2500×2220 | |
Патрон токарный-8800
Стоимость инструмента: 8800 руб.
Стоимость станка:380 000 руб.
Операция № 025
Для данной операции выбираем следующую модель станка Вид операции: «Токарная»
Модель станка: Токарно-револьверный 1Е325
Техническая характеристика | 1Е325 | |
Наибольший диаметр обработки прутка, мм | ||
Наибольший диаметр обработки над станиной, мм | ||
Наибольший диаметр обработки над суппортом, мм | ||
Наибольшая длина обрабат. заготовки, мм | ||
Расстояние от шпинделя до револ. головки, мм | 107−400 | |
Кол-во ступеней частоты вращения шпинделя | ||
Наиб. и наим. частота вращения шпинделя | 80−3150 | |
Подача револьверного суппорта, мм/об | 0,05−1,3 | |
Кол-во ступеней подач револьверного суппорта | ||
Поперечная подача, мм/об | 0,05−1,3 | |
Мощность эл.двигат., кВт | ||
Габариты станка, мм | 3915×925 | |
Патрон сверлильный-600 руб.
Метчики для трубной цилиндрической, дюймовой и трубной конической резьбы (ст. У12) резьба Ѕ=194,70
Стоимость инструмента-794,70 руб ;
Стоимость станка: 90 000 руб.
Операция № 030 «Фрезерная»
Для обработки плоской поверхности (паза) 10,5, длиной 80 мм, глубиной резанья 10,5 выбираем следующую модель станка Вид операции: «Фрезерная»
Модель станка: Горизонтально-фрезерный
Техническая характеристика | 6P80Г | |
Размеры рабочего стола, мм | 800×20 | |
Расстояние от оси шпинд. до стола А, мм | 20−320 | |
Расстояние от вертикаль. направл. до середины стола Б, мм | 180−340 | |
Наиб. перемещение стола продольное, мм | ||
Наиб. перемещение стола поперечн., мм | ||
Наиб. перемещение стола вертикаль., мм | ||
Угол поворота стола, град | ||
Кол-во скоростей шпинделя | ||
Частота вращения шпинделя, об/мин50 | ||
Конец шпинделя по ГОСТ 836–72 | ||
Число ступеней подач стола | ||
Подача стола (продол. и попереч.), мм/мин | 25−1120 | |
Подача стола (вертикальная), мм/мин | 12,5−560 | |
Мощность эл.двигат. главн. движ., кВт | ||
Габариты станка в плане, мм | 1525×1875 | |
Фрезы дисковые 3-х сторонние (ГОСТ 3755 и ГОСТ 9474) 60х14−997,10
(кол-во переточек -4), чисел зубьев-80
Приспособление специальное -7000 руб.
Стоимость инструмента -7997,10
Стоимость станка: 415 000 руб.
Операция № 035 «Фрезерная»
Для обработки плоской поверхности (паза) 12,6, длиной 80 мм, глубиной резанья 2,1 выбираем следующую модель станка Вид операции: «Фрезерная»
Модель станка: Горизонтально-фрезерный
Техническая характеристика | 6P80Г | |
Размеры рабочего стола, мм | 800×20 | |
Расстояние от оси шпинд. до стола А, мм | 20−320 | |
Расстояние от вертикаль. направл. до середины стола Б, мм | 180−340 | |
Наиб. перемещение стола продольное, мм | ||
Наиб. перемещение стола поперечн., мм | ||
Наиб. перемещение стола вертикаль., мм | ||
Угол поворота стола, град | ||
Кол-во скоростей шпинделя | ||
Частота вращения шпинделя, об/мин50 | ||
Конец шпинделя по ГОСТ 836–72 | ||
Число ступеней подач стола | ||
Подача стола (продол. и попереч.), мм/мин | 25−1120 | |
Подача стола (вертикальная), мм/мин | 12,5−560 | |
Мощность эл.двигат. главн. движ., кВт | ||
Габариты станка в плане, мм | 1525×1875 | |
Фрезы дисковые 3-х сторонние (ГОСТ 3755 и ГОСТ 9474) 60х14−997,10
Приспособление специальное -7000 руб.
Стоимость инструмента -7997,10
Стоимость станка: 415 000 руб.
Операция № 040 «Фрезерная»
Для обработки плоской поверхности (паза) 14Н 10, длиной 80 мм, глубиной резанья 1,4 выбираем следующую модель станка Вид операции: «Фрезерная»
Модель станка: Горизонтально-фрезерный
Техническая характеристика | 6P80Г | |
Размеры рабочего стола, мм | 800×20 | |
Расстояние от оси шпинд. до стола А, мм | 20−320 | |
Расстояние от вертикаль. направл. до середины стола Б, мм | 180−340 | |
Наиб. перемещение стола продольное, мм | ||
Наиб. перемещение стола поперечн., мм | ||
Наиб. перемещение стола вертикаль., мм | ||
Угол поворота стола, град | ||
Кол-во скоростей шпинделя | ||
Частота вращения шпинделя, об/мин50 | ||
Конец шпинделя по ГОСТ 836–72 | ||
Число ступеней подач стола | ||
Подача стола (продол. и попереч.), мм/мин | 25−1120 | |
Подача стола (вертикальная), мм/мин | 12,5−560 | |
Мощность эл.двигат. главн. движ., кВт | ||
Габариты станка в плане, мм | 1525×1875 | |
Фрезы дисковые 3-х сторонние (ГОСТ 3755 и ГОСТ 9474) 60х14−997,10
Приспособление специальное -7000 руб.
Стоимость инструмента -7997,10
Стоимость станка: 415 000 руб.
Операция № 050 «Лазерное упрочнение поверхности «В».
Для операции «Лазерное упрочнение» применяем лазерный технологический комплекс Мощность-100 кВт Занимаемая площадь-100 кв.м.
Стоимость комплекса: 1 500 000 руб.
Операция № 055
Для обработки наружной цилиндрической поверхности 40,22, длиной 50 мм, глубиной резанья 0,16 выбираем следующую модель станка Вид операции: «Шлифовальная»
Модель станка: Кругло-шлифовальный
Техническая характеристика | 3М150 | |
Наиб.диаметр обраб. заготовки, мм | ||
Наиб. длина обраб заготовки, мм | ||
Рекоменд. диаметр наруж. шлифования, мм | 10−45 | |
Наиб. длина наружного шлифования, мм | ||
Наиб. размеры шлиф. круга DxB, мм | 400×40 | |
Частота вращения шпинд. шлиф. бабки, об/мин | 2350; 1670 | |
Частота вращения шпинделя изделия (Б/ст), об/мин | 100−1000 | |
Скорость перемещения стола (бесступенч.), м/мин | 0,2−4 | |
Поперечная подача шлиф. бабки на одно дел. лимба, мм | 0,002 | |
Непрерывн. подача врезного шлиф. (б/ст), мм/мин | 0,05−0,5 | |
Мощность эл.двигат., кВт | ||
Габариты станка, мм | 2500×2220 | |
Шлифовальный круг-400 руб.
Патрон токарный-8800
Стоимость инструмента: 9200 руб.
Стоимость станка: 380 000 руб.
Операция № 060
Для обработки наружной цилиндрической поверхности 40,22, длиной 50 мм, глубиной резанья 0,16 выбираем следующую модель станка Вид операции: «Шлифовальная»
Модель станка: Кругло-шлифовальный
Техническая характеристика | 3М150 | |
Наиб.диаметр обраб. заготовки, мм | ||
Наиб. длина обраб заготовки, мм | ||
Рекоменд. диаметр наруж. шлифования, мм | 10−45 | |
Наиб. длина наружного шлифования, мм | ||
Наиб. размеры шлиф. круга DxB, мм | 400×40 | |
Частота вращения шпинд. шлиф. бабки, об/мин | 2350; 1670 | |
Частота вращения шпинделя изделия (Б/ст), об/мин | 100−1000 | |
Скорость перемещения стола (бесступенч.), м/мин | 0,2−4 | |
Поперечная подача шлиф. бабки на одно дел. лимба, мм | 0,002 | |
Непрерывн. подача врезного шлиф. (б/ст), мм/мин | 0,05−0,5 | |
Мощность эл.двигат., кВт | ||
Габариты станка, мм | 2500×2220 | |
Шлифовальный круг-400 руб
Патрон токарный-8800
Стоимость инструмента: 9 200 руб.
Стоимость станка:380 000 руб.
Операция № 065
Вид операции: «Отделочная»
Модель станка: Токарно-винторезный с комплексом ультразвукового оборудования
Техническая характеристика | ИТ-1М | |
Наиб.диам. об-ки над станиной, мм | ||
Наиб.диам. об-ки над суппортом, мм | ||
Наиб.диам. прутка, проходящего через отв. шпинд., мм | ||
Расстояние между центрами, мм | ||
Шаг нарез. резьбы (метрич), мм | 0,25−112 | |
Кол-во ступеней частоты вращения шпинделя | ||
Наиб. и наим. частота вращения шпинделя | 28−1250 | |
Наиб.перемещение суппорта продоль. | ||
Наиб.перемещение суппорта попереч. | ||
Предел подач продольных, мм/об | 0,05−6,0 | |
Предел подач поперечных, мм/об | 0,025−3,0 | |
Мощность эл.двигат., кВт | ||
Габариты станка, мм | 2165×960 | |
Стоимость: 90 000+70 000=160 000 руб.
Обрабатывать поверхность В до
7. Разработка операции лазерного упрочнения
Исходные данные:
Характеристики источника нагрева:
· d (диаметр луча) — 3,8 мм
· положение оси луча — 2,0
· V луча (скорость перемещения луча) 1, 5 см/с.
Характеристика материала:
Плотность — 7,81 кг./=7810
Предел текучести — 1210;
Температура плавления t — 1500 ;
АС1 — 724
V закалки — 465
НВ = 240
7 5 20 Размер расчетной области (мм).
11 11 11 Размеpность задачи (не более 30 по кажд. коорд.).
2.0 Положение оси луча (мм).
1.5 Скорость перемещения луча (см/с).
9820 Плотность теплового потока (Вт/см**2).
20 Температура детали (град C).
200 Коэффициент теплоотдачи (Вт/м**2/К).
0.10 Относительное количество внутренних итераций.
30 Количество шагов установления.
0.10 Шаг установления ©.
10.00 Точность расчетов (град/с).
Результаты расчета операции лазерного упрочнения поверхности «В».
Построение графика изменения температуры по слоям в процессе нагрева и охлаждения.
t, с. | 0,13 | 0,27 | 0,40 | 0,53 | 0,67 | 0,80 | 0,93 | 1,07 | 1,20 | 1,33 | |||
h = 0 мм | |||||||||||||
h = 0,5 мм | |||||||||||||
Т, °С | h = 1,0 мм | ||||||||||||
h = 1,5 мм | |||||||||||||
h = 2,0 мм | |||||||||||||
h = 2,5 мм | |||||||||||||
АС1,°С = | |||||||||||||
2. Построение графика изменения скорости нагрева/ охлаждения.
t, с. | 0,13 | 0,27 | 0,40 | 0,53 | 0,67 | 0,80 | 0,93 | 1,07 | 1,20 | 1,33 | |||
h = 0 мм | -6559 | -2274 | -754 | -364 | -207 | -130 | -87 | -59 | -32 | ||||
h = 0,5 мм | -2027 | -1473 | -669 | -343 | -199 | -126 | -85 | -58 | -31 | ||||
Т, °С | h = 1,0 мм | -356 | -319 | -217 | -144 | -99 | -70 | -50 | -27 | ||||
h = 1,5 мм | -97 | -173 | -146 | -108 | -79 | -59 | -44 | -24 | |||||
h = 2,0 мм | -66 | -82 | -72 | -59 | -47 | -37 | -21 | ||||||
h = 2,5 мм | -31 | -41 | -40 | -36 | -30 | -18 | |||||||
Vзак,°С= | -465 | -4 | -465 | -465 | -465 | -465 | -465 | -465 | -465 | -465 | -465 | ||
3. Расчет величины упрочненного слоя.
3. Расчет величины упрочненного слоя | |||||||||||||
3.1. Введите номер первого слоя, который не пересекает Ас1 | j = | ||||||||||||
3.2. Введите максимальную температуру слоя, который не пересекает Ас1 | Tj = | ||||||||||||
3.3. Введите максимальную температуру предыдущего слоя | Tj-1 = | ||||||||||||
3.4. Температура | точки Ас1 = | ||||||||||||
3.5. Введите шаг расчетной сетки в мм | Sx2 = | 0,5 | |||||||||||
grad T = | (Tj-1 — Tj)/Sx2 | = ( | — 429 | ) / | 0,5 | = | °C/мм | ||||||
0,147 | 0,73 529 412 | 0,5 | |||||||||||
hупр = | Sx2 | (j — 2) | (Tj-1 — Ас1) / | grad T | = | 0,5712 | мм | ||||||
Вывод:
В результате расчета установили что, требуемый уровень твердости НRC 52…54, обеспечивается при лазерном упрочнении поверхности детали лазером d луча = 3,8 мм;
при скорости перемещения = 1.5 (см/с);
при плотности теплового потока = 9820 (Вт/см**2);
При этом толщина упрочненного слоя составляет — 0,5712 мм.
Алгоритм определения режимов и расчета основного времени при лазерном упрочнении
1. Перевести скорость перемещения луча V в м/мин.
V=1.5 cм/с
V= (1.5*60)/100=0, 9 м/мин.
2. Рассчитать число оборотов детали n = 1000*V /(?*d), где d — диаметр детали,? = 3,14
n=(1000*0.9)/(3.14*40)=7.165
3. Рассчитать величину подачи: S = Kпер * dлуча, где Kпер — коэффициент перекрытия пятен нагрева (принять равным 0,6)
S=3,8*0,6=2,28
4. Рассчитать основное время to = L /(S*n), где L — длина обрабатываемой поверхности
To=50/(2,28*7,165=3,06
8. Проектирование операции ультразвукового деформирования поверхности «В»
Исходные данные:
Амплитуда 0,0007 м.
Диаметр -0,0095 мм Частота колебаний-20 000
Модуль нормальной упругости:
Е = 2,15E+11 Па Коэффициент Пуассона м= 0,271
Амплитуда УЗО = 0,25Гц Диаметр деформации элемента Д = 0,008 м.
Плотность р = 7850(кг/м в кубе) Площадь волновода 0,225 м2
Скорость звука = 5100 м/с НД =3,6E+09Н/м2
Результаты расчета операции ультразвукового деформирования.
1. Построение графика зависимости динамического усилия (Fmax) от статического (Fct).
Fct, Н | |||||||
Fmax, Н | |||||||
2. Построение графика зависимости диаметра отпечатка (dotp) от статического усилия (Fct).
Fct, Н | |||||||
dotp, мм | 0,186 | 0,353 | 0,492 | 0,595 | 0,659 | ||
3. Построение графика зависимости максимальной глубины внедрения деформатора (hmax) от статического усилия (Fct).
Fct, Н | |||||||
hmax, мкм | 0,91 | 3,286 | 6,37 | 9,326 | 11,43 | ||
4. Построение графика изменения динамического усилия (F) в периоде контакта инструмента с деталью (t0 — t2) для режима Q0 = -60°
t0 | tia | tib | tic | tid | t1 | t2 | ||
t, мкc | 3,9 | 7,81 | 11,71 | 15,62 | 19,53 | 27,07 | ||
F, H | ||||||||
Fa | Fb | Fc | Fd | Fmax | ||||
5. Построение графика изменения глубины внедрения деформатора (h) в периоде контакта инструмента с деталью (t0 — t2) для режима Q0 = -60°
t0 | tia | tib | tic | tid | t1=tza | tzb | tzc | t2 = tzb | ||
t, мкc | 3,9 | 7,81 | 11,71 | 15,62 | 19,53 | 22,54 | 24,05 | 27,07 | ||
h, мкм | 2,32 | 5,39 | 8,41 | 10,61 | 11,43 | 11,08 | 10,55 | 8,98 | ||
hia | hib | hic | hid | hmax | ||||||
hza | hzb | hzc | hzb | |||||||
2,45 | 2,1 | 1,57 | ||||||||
Алгоритм определения режимов и расчета основного времени при ультразвуковом упрочнении
1. Определить значение шероховатости поверхности (Rz исх.) перед ультразвуковой обработкой (принять равной шероховатости, получаемой на операции шлифования) Шероховатость поверхности после шлифований перед ультразвуковой обработкой =
;
где hmax — наибольшая глубина внедрения деформатора в поверхностный слой детали.
hупр.- величина упругой деформации в момент наибольшего внедрения деформатора.
2. По графику h = h (t) найти отношение I = hmax / h
3. Найти заданное значение hmax зад. =I * Rz исх.
4. На графике h = h (t) отложить значение hmax зад. и найти, соответствующий ему момент времени tзад.
h мах заданное = 2,04 мкм.
t заданное = 3,95 мкс
5. На графике F = f (t) отложить значение tзад. и найти, соответствующее ему значение динамического усилия Fзад.
Fзад.мах = 225 Н
t заданное = 3,95 мкс.
6. На графике Fmax = f (Fct) отложить значение Fзад. и найти, соответствующее ему значение статического усилия Fct зад.
Fзад.мах = 225 Н
Fct зад.=26Н
7. На графике hmax = f (Fct) отложить значение Fct зад. и найти, соответствующее ему значение максимальной глубины внедрения деформатора hmax пров.
Fct зад.=26Н
hmax пров.=2,0 мкм
8. Найти значение отклонения:(hmax зад. — hmax пров.) / hmax зад.
(2,04−2,04)/2,04=0,0196
9. Сделать вывод об уровне точности определения Fct зад. — если отклонение < 0,1, то точность приемлемая.
Полученный результат свидетельствует о том, что точность определения Fсt приемлема.
10. На графике dotp = f (Fct) отложить значение Fct зад. и найти, соответствующее ему значение диаметра отпечатка dotp зад.
Fct зад.=26Н
dotp зад.=0,28
11. Определить глубину отпечатка, соответсвующую значению шероховатости, заданному на чертеже h = 4*Ra
h=4*0,2=0,8=0,0008мкм.
12. Рассчитать параметр Х по формуле:
13. Рассчитать величину подачи S=2* Х
S=2*0,087=0,174
14. Рассчитать величину скорости обработки V= |S|* f, где f — частота колебаний
V= 0,174*20 000=3480
15. Рассчитать число оборотов детали n = 1000*V /(p*d), где d — диаметр детали, p = 3,14
n = (1000*3480)/(3,14*40)=27 707,10
16. Рассчитать основное время to = L /(S*n), где L — длина обрабатываемой поверхности
To=50/(0,174*27 707,10)=0,0133 мин.
9. Расчет технологической себестоимости
Как видно из предыдущих разделов в основе всех технико-экономических расчетов лежит оценка трудозатрат на выполнение одной или нескольких технологических операций, а иногда и всего технологического процесса. Эти трудозатраты и определяют так называемую технологическую себестоимость.
Технологическая себестоимость операции складывается из следующих элементов:
С= З0 + Эл + Ам + Пр + Ин + Цх, где З0 — заработная плата основных производственных рабочих, руб; Эл — затраты на силовую электроэнергию, руб; Ам — амортизационные отчисления на основное оборудование; Пр — расходы на станочные приспособления; Ин — расходы по эксплуатации режущего инструмента; Цх — прочие цеховые накладные расходы (зарплата наладчиков, обслуживающего персонала, тепло, освещение цеха и т. п.). Прежде чем рассчитать технологическую себестоимость, найдем неизвестные элементы затрат:
Основная заработная плата производственных рабочих за выполнение одной операции:
З0= S * K * t шт / 60, руб, Где: S — часовая тарифная ставка станочника 1-го разряда. руб; S=100 руб/час К — тарифный коэффициент требуемого для операции разряда; К=1
t шт — норма штучного времени на операцию, мин.
В данном проекте принять tшт = Тш-к.
Штучно-калькуляционное время Тш-к = фк tо, где tо— основное время операции.
Рассчитаем норму штучного времени на каждую операцию:
t штучное = t основное *Кt
1.
2.
3.
4.
5.
6.
7.
8.
9.
10.
11.
12.
13.
14.
15.
Рассчитаем основную заработную плату производственных рабочих за выполнение одной операции:
З0= S * K * t шт / 60, руб,
1.
2.
3.
4.
5.
6.
7.
8.
9.
10.
11.
12.
13.
14.
15.
Затраты на силовую электроэнергию.
По каждой операции определяются отдельно, по следующей формуле:
Эл= (Сэ *Ny **to) / (60* ), руб где Сэ — отпускная цена за кВт силовой электроэнергии, руб = 2,0 рубквт;
Ny — установочная мощность электродвигателей станка, кВт;
— коэффициент загрузки станка по мощности (на черновых операциях 0,8; на чистовых 0,5);
to — основное (машинное) время обработки, мин;
— коэффициент, учитывающий различные потери -0,75
Рассчитаем затраты на силовую энергию :
Рассчитаем расходы на амортизацию оборудования:
Ам
Они определяются по формуле Ам= (So*Кa*t шт-к) / (Fд **•60)
где So — балансовая стоимость оборудования, руб;
Кa — коэффициент амортизационных отчислений, определяющий срок окупаемости оборудования 0,15-основные виды станков);
t шт-к — штучно-калькуляционное время выполнения операции, мин;
Fд — действительный годовой фонд работы оборудования, час (двух сменах работы составляет 4140 час.);
— коэффициент загрузки оборудования (0,8- при серийном производстве).
1.
2.
3.
4.
5.
6.
7.
8.
9.
10.
11.
12.
13.
14.
15.
Рассчитаем расходы на эксплуатацию специальных приспособлений (паз 14H10):
Пр= Sпр*(а+в) / N, руб, где Sпр — стоимость специального приспособления = 7000 руб;
а — коэффициент амортизации (0,3);
в — коэффициент затрат на текущий ремонт (0,1);
N — годовая программа производства деталей. для изготовления которых сделано это приспособлений = 27 000 штук.
Рассчитаем расходы на эксплуатацию режущего инструмента:
где Sи — стоимость режущего инструмента, руб;
n — число допустимых переточек за срок эксплуатации;
Т — период стойкости инструмента между переточками-(50) ;
К-коэффициент затрат на переточки инструмента (1,5);
to — основное машинное время на операцию;
— коэффициент времени резания данным инструментом в составе операции =1(1).
1.
2.
3.
4.
5.
6.
7.
8.
9.
10.
11.
12.
13.
Прочие цеховые расходы.
Определяются общими затратами на содержание цеха и соотносятся с площадью рабочего места, приходящегося на операцию, и времени ее выполнения:
Н= (Sуд.* F*tшт-к) / (60*Fд),
где Sуд — норматив годовых затрат на содержание 1 м2 основной производственной площади цеха, руб/м2; = 5500 руб.
F — площадь, приходящаяся на рабочее место, занимаемое данной операцией, м2;
tшт-к — штучно-калькуляционное время на операцию, мин;
Fд — действительный годовой фонд времени работы оборудования. = 4140ч.
1. Вид операции: Токарно-револьверная (точение).
Модель станка: Токарно — револьверный 1Е325;
Габаритные размеры станка: 3915*925мм.=(3915/1000)*(925/1000) = 3,621
2. Вид операции: Вертикально-сверлильный. (сверление, развертывание)
Модель станка: Вертикально-сверлильный 2Н125
Габаритные размеры станка: 1130×850мм (1130/1000)*(850/1000)=0,96
3.Вид операции «Фрезерная».
Модель станка: Горизонтальнофрезерный 6Р80Г Габаритные размеры станка, (в плане): 1525*1875мм = (1525/1000)*(1875/1000) = 2,860
4.Вид операции «Шлифование»
Модель станка: Кругло — шлифовальный 3М150
Габаритные размеры станка: 2500*2220мм.=(2500/1000)*(2220/1000)=5,55
5. Вид операции «Лазерное упрочнение поверхности
Модель комплекса: «лазер технологический»;
Габаритные размеры станка: (10 000 /1000)*(10 000/1000) -100 .
6.Вид операции: «Ультразвуковая обработка».
Модель станка: Токарно — винторезный ИТ-1М, дополненный ультразвуковым оборудованием.
Габаритные размеры станка: 2165×960мм.=(2165/1000)*(960/1000) = 2,08
Рассчитаем прочие цеховые расходы по операциям:
1.
3.
4.
5.
6.
7.
8.
9.
10.
11.
12.
14.
15.
Находим общую стоимость каждой операции:
Технологическая себестоимость операции складывается из следующих элементов:
С= З0 + Эл + Ам + Пр + Ин + Цх,
№ п/п | Зар.плата | Силовая Эл. энергия | Амортизация | Спец. приспособления | Реж. инструмент | Цеховые расходы | Итого на каждую операцию | |
1,04 | 0,0375 | 0,0276 | 0,013 | 0,273 | 0,013 | 1,4041 | ||
0,758 | 0,017 | 0,02 | 0,013 | 1,36 | 0,0096 | 2,1776 | ||
0,113 | 0,0053 | 0,0049 | 0,196 | 0,02 | 0,005 | 0,3442 | ||
0,09 | 0,0043 | 0,0039 | 0,196 | 0,016 | 0,0043 | 0,3145 | ||
0,113 | 0,0053 | 0,0049 | 0,196 | 0,02 | 0,005 | 0,3442 | ||
0,27 | 0,008 | 0,012 | 0,196 | 0,05 | 0,013 | 0,549 | ||
0,376 | 0,021 | 0,069 | 0,196 | 0,35 | 0,03 | 1,042 | ||
0,553 | 0,019 | 0,10 | 0,196 | 0,51 | 0,041 | 1,419 | ||
0,23 | 0,008 | 0,01 | 0,013 | 0,06 | 0,011 | 0,332 | ||
1,3 | 0,029 | 0,057 | 0,013 | 3,4 | 0,062 | 4,861 | ||
0,127 | 0,0053 | 0,25 | 0,156 | 0,37 | 0,005 | 0,9133 | ||
0,076 | 0,002 | 0,015 | 0,156 | 0,22 | 0,003 | 0,472 | ||
0,053 | 0,0013 | 0,011 | 0,156 | 0,15 | 0,002 | 0,3733 | ||
6,63 | 0,68 | 4,8 | —-; | 8,8 | 20,91 | |||
0,03 | 0,88 | 0,0022 | 1,56 | —; | 0,008 | 1,60 | ||
Всего | 11,759 | 0,8439 | 5,39 | 3,25 | 6,8 | 9,01 | 37,057 | |
Себестоимость детали типа «втулка» составляет = 11,759+0,8439+5,39+3,25+6,8+9,01=37, 057 руб.
Список использованных источников
1.Фетисов Г. П. и др. Материаловедение и технология металлов. М.; Высшая школа; 2000. 637с.
2. Петруха П. Г., Марков А. И., и др. Технология обработки конструкционных материалов. М.: Высшая школа, 1991, 512 с.
3. Дальский А. М. и др. Технология конструкционных материалов. М.; Машиностроение; 1992. 447 с.
4. Волчок И. П. Современные технологии производств. 1−4 часть. — Запорожье, 1996.-120с.
5. Замятин В. К. Технология и оснащение сборочного производства машиноприборостроения: Справочник. — М.:Машиностроение, 1995. — 608 с.