Разработка методики проектирования технологических процессов формообразования полых осесимметричных деталей ГТД
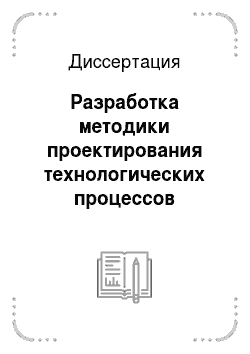
Диссертация
Большинство из этих деталей имеет форму тел вращения (полые осесимметричные оболочки). Основной операцией получения полых оболочек является вытяжка изделия из плоской или трубной заготовки. Эта операция позволяет снизить трудоемкость формообразования, энергетические затраты и получить рациональную форму детали, способствующую максимальному снижению концентрации напряжений, увеличению прочности… Читать ещё >
Содержание
- ПРИНЯТЫЕ ОБОЗНАЧЕНИЯ
- ГЛАВА 1. АНАЛИЗ СОВРЕМЕННОГО СОСТОЯНИЯ ВОПРОСОВ ТЕОРИИ И ПРАКТИКИ ФОРМООБРАЗОВАНИЯ ПОЛЫХ ОСЕСИММЕТРИЧНЫХ ДЕТАЛЕЙ ГТД
- 1. 1. Обзор и анализ литературных данных
- ВЫВОДЫ ПО ГЛАВЕ 1 И ЗАДАЧИ ИССЛЕДОВАНИЯ
- ГЛАВА 2. РАЗРАБОТКА ТЕОРЕТИЧЕСКИХ ОСНОВ ПРОЦЕССА ФОРМООБРАЗОВАНИЯ ПОЛЫХ ДЕТАЛЕЙ ГТД
- 2. 1. Сущность метода, основные допущения
- 2. 2. Определение траекторий движения материальных точек в меридиональных сечениях участков двойной кривизны
- 2. 3. Описание линий тока уравнениями кривых второго порядка
- 2. 3. 1. Описание линий тока уравнениями эллипсов. Определение их параметров
- 2. 3. 2. Описание линий тока уравнениями гиперболы
- 2. 3. 3. Описание линий тока уравнениями параболы
- 2. 4. Определение скоростей движения материальных точек в участке двойной кривизны
- 2. 4. 1. Определение скоростей движения материальных точек с описанием линий тока уравнениями эллипсов
- 2. 4. 2. Определение скоростей движения материальных точек с описанием линий тока уравнениями гиперболы
- 2. 4. 3. Определение скоростей движения материальных точек с описанием линий тока уравнениями параболы
- 2. 5. Определение угловой скорости вращения радиус-вектора в участке двойной кривизны
- 2. 6. Поле скоростей деформаций в участке двойной кривизны
- 2. 6. 1. Определение скоростей деформаций для участка двойной кривизны при описании линий тока уравнениями эллипсов, гиперболы и параболы
- 2. 7. Интенсивность скорости деформации сдвига
- 2. 8. Компоненты тензора деформаций
- ВЫВОДЫ ПО ГЛАВЕ
- ГЛАВА 3. РАЗРАБОТКА МЕТОДИК ОПРЕДЕЛЕНИЯ НАПРЯЖЕННОГО И ДЕФОРМИРОВАННОГО СОСТОЯНИЙ МАТЕРИАЛА ДЛЯ ПРОЦЕССОВ ФОРМООБРАЗОВАНИЯ ДЕТАЛЕЙ ГТД
- 3. 1. Выворот труб
- 3. 1. 1. Деформированное состояние в очаге деформаций. Определение скоростей и скоростей деформаций
- 3. 1. 2. Определение напряжений по границам очага пластической деформации
- 3. 2. Вытяжка. Первая операция
- 3. 2. 1. Деформированное состояние в очаге деформаций. Определение скоростей и скоростей деформаций
- 3. 2. 2. Определение зависимости перемещения кромки фланца заготовки от хода пуансона
- 3. 2. 3. Определение напряжений по границам очага деформации
- 3. 3. Вытяжка. Вторая операция
- 3. 3. 1. Деформированное состояние в очаге деформаций. Определение скоростей и скоростей деформаций
- 3. 3. 2. Определение напряжений по границам очага пластической деформации
- 3. 4. Расчет усилий для формообразования полых осесиммет-ричных заготовок
- 3. 5. Алгоритм расчета напряжений на границе очага пластической деформации
- 3. 1. Выворот труб
- ВЫВОДЫ ПО ГЛАВЕ
- ГЛАВА 4. ЭКСПЕРИМЕНТАЛЬНЫЕ ИССЛЕДОВАНИЯ ПРОЦЕССОВ ФОРМООБРАЗОВАНИЯ ПОЛЫХ ОСЕСИММЕТРИЧ-НЫХ ДЕТАЛЕЙ
- 4. 1. Материалы для исследований
- 4. 2. Исследование течения материала в меридиональном сечении участка двойной кривизны заготовки
- 4. 3. Определение напряжений в тороидальных участках заготовки
- 4. 4. Определение сил деформирования для различных операций формообразования полых оболочек
- 4. 4. 1. Определение деформирующих сил при вывороте труб
- 4. 4. 2. Определение деформирующих сил для первой операции вытяжки
- 4. 4. 3. Определение силы деформирования для последующих операций вытяжки
- 4. 5. Исследование механических характеристик деформированного металла
- 4. 5. 1. Исследование остаточных напряжений в заготовках, деформированных по различным схемам
- 4. 5. 2. Усталостные испытания заготовок, деформированных по различным схемам
- 4. 5. 3. Оценка результатов испытаний
- 5. 1. Разработка технологического процесса изготовления деталей типа «Стакан»
- 5. 2. Разработка технологического процесса изготовления деталей с торообразными участками
Список литературы
- Avitzur В. Metal Forming Processes and Analysis. Me Graw Hile Book Company, 1968.-459 p.
- Kobayashi S., Thomsen E.G. Approximate Solutions to a Problem of Press Forming, Trans. ASME, Series B, 81. 1959. -№ 3. — P. 217−227.
- Nine H.D. Drawbead forces in sheet metal forming. «Mech. Sheet Metal forming. Mater. Behav. and Deformation Anal. Proc. Symp., Warren, Mich., 1977. New York London, 1978. — P. 179−207.
- Oehler G. Tifziehen unter besonderer unsymmetrischer und eckiger Teile. «Klepzig Fachber», 1970, 78. № 5. — P. 237−244.
- Аверкиев Ю.А., Аверкиев А. Ю. Технология холодной штамповки. М.: Машиностроение, 1989. — 304 с.
- Алексеев Ю.Н. Вопросы пластического течения металлов. Харьков: Харьковский университет, 1958. — 191 с.
- Антонов Е.А. Исследование напряженного состояния в участках двойной кривизны// Оборудование и прогрессивная технология обработки металлов давлением авиационных материалов: Межвузовский сборник научных трудов. Ярославль, 1984. — С.90−97.
- Антонов Е.А. Разработка теории, процессов и оборудования для холодного формообразования оболочек сложных форм в поле высокого гидростатического давления: Дис.докт. техн. наук: 05.03.05 Защищена 14.11.84- Утв. 24.05.85- ДН № 5 182, — Андропов, 1984.-572 с.
- Антонов Е.А., Новиков В. А. Влияние метода формообразования на усталостную прочность изделий, полученных вытяжкой из листа// Кузнечно-штамповочное производство. 1978. — № 8. — С. 39−40.166
- Ю.Безухов Н. И. Основы теории упругости, пластичности и ползучести. -М.: Высшая школа, 1968.
- Бэкофен В. Процессы деформации. М.: Металлургия, 1977. — 288 с.
- Гелей Ш. Расчеты усилий и энергий при пластической деформации металлов. М.: Металлургиздат, 1958. — 273 с.
- З.Горбунов М. Н. Технология заготовительно-штамповочных работ в производстве самолетов. -М.: Машиностроение, 1981. 224 с.
- Горбунов М.Н. Штамповка деталей из трубчатых заготовок. М.: Машгиз, i960. — 190 с.
- Горбунов М.Н., Попов О. В. Интенсификация процессов холодной штамповки. М.: Машиностроение, 1958. — 267 с.
- Гофман, Закс. Введение в теорию пластичности для инженеров. М.: Машгиз, 1957. — 159 с.
- Григоровский Н.И. Модели для исследования напряжений из оптически нечувствительного прозрачного материала с вклейками из материала ЭД6-М Заводская лаборатория, 1958. — № 11. — С. 9−14.
- Громов Н.П. Теория обработки металлов давлением. М.: Металлургия, 1978.-360 с.
- Губкин С.И. Пластическая деформация металлов. М.: Металлургия, 1961.-Т. 1,2,3.
- Гун Г. Я. Теоретические основы обработки металлов давлением. М.: Металлургия, 1980. — 456 с.
- Давиденков H.H. Измерение остаточных напряжений в трубах// Журнал технической физики. 1931. — Вып.1. — Т.1. — С. 115−119.
- Данилин P.A., Огородников В. П., Зацепин С. Б. Определение силовых параметров и предельной деформации при штамповке вытяжкой-выдавливанием// Кузнечно-штамповочное производство. 1990. — № 5-С. 19−22.167
- Евстигнеев М.И., Подзей A.B., Сулима A.M. Технология производства двигателей летательных аппаратов М.: Машиностроение, 1982 — 264 с.
- Евстратов В.А. Теория обработки металлов давлением. Харьков: Харьковский государственный университет, 1981.
- Евстратов В.А., Торяник В. В., Левченко В. Н. Анализ процесса вытяжки// Кузнечно-штамповочное производство 1996. — № 4. — С. 19−23.
- Ершов В.И., Глазков В. И., Каширин М. Ф., Ковалев А. Д. Штамповка торов и патрубков из труб// Кузнечно-штамповочное производство. -1979.-№ 11.- С.21−22.
- Ершов В.И., Глазков М. И., Каширин М. Ф. Совершенствование формоизменяющих операций листовой штамповки. М.: Машиностроение, 1990.-312с.: Ил.
- Жарков В.А. Кинематика течения фланца заготовки// Известия вузов. -Машиностроение, 1975.-№ 11.-С. 141−146.29.3айков М. А. Влияние схемы напряженного состояния на сопротивление металла пластической деформации. Свердловск: Металлургиздат, 1954.-326с.
- ЗО.Звороно Б. П. Использование закона течения при анализе процессов листовой штамповки// Кузнечно-штамповочное производство. 1966. -№ 11.-С. 22−26.
- Зубцов М.Е. Листовая штамповка Л.: Машиностроение, 1980. — 432 е.: Ил.
- Изготовление деталей из листов и профилей при серийном производстве/ А. Н. Громова, В. И. Завьялова, В. К. Коробов. М.: Оборонгиз, 1960.-344 с.
- Изготовление основных деталей авиадвигателей/ Евстигнеев М. И., Морозов И. А., Подзей И. В и др. М.: Машиностроение, 1972. — 478 с.168
- Илюшин A.A. Некоторые вопросы теории пластического течения. М.: АН СССР, 1958.-311 с.
- Исаченков Е.И. Контактное трение и смазка при обработке металлов давлением. М.: Машиностроение, 1978. — 208 с.
- Исаченков Е.И. Основные направления повышения эффективности и качества листовой и объемной штамповки// Качество и эффективность при листовой и объемной штамповке: Материалы семинара. М.: МДНТИ, 1977.-С. 3−8.
- Качанов J1.M. Основы теории пластичности. М.: Наука, 1969. — 420 с.
- Каюшин В.А., Ренне И. П. Выворот концов труб с последующей отбортовкой// Кузнечно-штамповочное производство. 1983. — № 4. -С. 22−25.
- Каюшин В.А., Ренне И. П. Исследование отбортовки концов труб непрерывной раздачей жестким пуансоном без применения матрицы// Кузнечно-штамповочное производство. 1982. — № 2. — С. 23−24.
- Киучи, Авицур. Анализ пластического течения через клиновые суживающиеся матрицы// Конструирование и технология машиностроения. -М.: ИЛ, 1980. -№ 2. С. 213−221.
- Колмогоров В.Л. Напряжение. Деформации. Разрушение. М.: Металлургия, 1970. — 299 с.
- Колмогоров В.Л. Механика обработки металлов давлением. М.: Металлургия, 1986. — 688 с.
- Корн Г., Корн Т. Справочник по математике для научных работников и инженеров. М.: Наука, 1970. — 727 с.
- Крыжный Г. К., Мацукин Ю. Г. Кинематика деформирования заготовки в процессах вытяжки со стационарным полем напряжений/ Импульсная обработка металлов давлением: Сб. Харьков: ХАИ, 1981. — С. 34−38.169
- Малов А.Н. Технология холодной штамповки. М.: Машиностроение, 1969.-568 с.
- Мещерин В.Т. Листовая штамповка (атлас схем).- М.: Машгиз, 1975. -227с.
- Мосин Ф.В. Технология изготовления деталей из труб. М.: Машгиз, 1962.
- Неравномерность деформации при плоском пластическом течении/ И. П. Ренне, Э. А. Иванова, Э. А. Бойко, Ю. М. Филигаров. Тула: Тульский политехнический институт, 1971.-С. 18−31.
- Норицын И.А. Основы расчета процесса вытяжки деталей с фланцем без промежуточных отжигов// Автомобильная и тракторная промышленность. 1954. — № 3. — С. 43−45.
- Норицын И.А. Теоретический анализ процесса вытяжки листового металла// Известия АН СССР, ОТН. 1951. — № 11.
- Овчинников А.Г. Основы теории штамповки выдавливанием на прессах. М.: Машиностроение, 1983. — 300 с.
- Одел, Клаузен. Численное решение задачи глубокой вытяжки// Конструирование и технология машиностроения. М.: ИЛ, 1977. — № 1.-С. 148−151.
- Пат. № 3, 685, 337 США. Глубокая вытяжка/ В. Авицур. 1972.5 4. Пихтовников Р. В. Некоторые вопросы теории однопереходной штамповки-вытяжки// Труды Харьковского авиационного института. -1957. Вып. 17. — С. 64−90.
- Пластическое формоизменение металлов/ Г. Я. Гун, П. И. Полухин, В. П. Полухин и др. М.: Металлургия, 1968. — 458 с.
- Попов Е.А. Общая методика анализа формоизменяющих операций листовой штамповки при осесимметричном деформировании// Основы170теории обработки металлов давлением/ Под ред. М. В. Сторожева. М.: Машгиз, 1957. — С. 369−404.
- Попов Е.А. Основы теории листовой штамповки. М.: Машиностроение, 1977.-278 е.: Ил.
- Попов Е.А. Роль теории в повышении эффективности обработки давлением и качества продукции// Качество и эффективность при листовой штамповке: Материалы семинара. М.: МДНТП, 1977. — С. 9−15.
- Прагер В. Проблемы теории пластичности. М.: Физматгиз, 1958.-193 с.
- Прагер В., Ходж Ф. Г. Теория идеальных пластических тел. М.: ИЛ, 1956.-399 с.
- Общемашиностроительные нормативы времени на холодную штамповку, резку, высадку и обрезку: массовое, крупносерийное, серийное и мелкосерийное производство. -М.: Экономика, 1987 189 с.
- Ренне И.П., Грдилян Г. Л. Реверсивная вытяжка цилиндрических сосудов// Кузнечно-штамповочное производство. 1977. — № 8. — С. 24−29.
- Романовский В.П. Процесс образования и расчет прочности опасного сечения при глубокой вытяжке// Кузнечно-штамповочное производство.- 1968-№ 9. С.5−8.
- Романовский В.П. Справочник по холодной штамповке. Л.: Машиностроение, 1979. — 520 с.
- Северденко В.П. Брак в листовой штамповке. Минск: Наука и техника, 1973. — 168 с.
- Скубачевский Г. С. Авиационные газотурбинные двигатели. Конструкция и расчет деталей. 5-е изд., перераб. и доп. — М.: Машиностроение, 1981. — 550 с.
- Смирнов B.C. Теория обработки металлов давлением. М.: Металлургия, 1973. — 524 с.171
- Расчеты экономической эффективности новой техники: Справочник/ Под общей редакцией К. М. Великанова. 2-е изд., перераб. и доп. — JL: Машиностроение, 1990. -445 с.
- Смирнов-Аляев Г. А. Сопротивление материалов пластическому деформированию. М.: Машиностроение, 1978. — 368 с.
- Соколов И.А., Уральский В. И. Остаточные напряжения и качество металлопродукции. -М.: Металлургия, 1981.
- Соколовский В.В. Теория пластичности М.: Гостехиздат, 1950 — 416 с.
- Справочник по авиационным материалам: Т.2, 4.1/ Под ред. А.Т. Туманова- М.: Машиностроение, 1965. 632 с.
- Степанский Л.Г. О границах очага пластической деформации при выдавливании// Вестник машиностроения. 1963. — № 9. — С. 25−31.
- Степанский Л.Г. Расчеты процессов обработки металлов давлением. -М.: Машиностроение, 1979. 215 с.
- Сторожев М.В., Попов Е. А. Теория обработки металлов давлением. -М.: Машиностроение, 1977. 424 с.
- Теория обработки металлов давлением/ И. Я. Тарновский, A.A. Поздеев, O.A. Ганаго и др. М.: Металлургиздат, 1963. — 289 с.
- Тимощенко В.А. Опыт штамповки полых деталей при малых коэффициентах вытяжки// Кузнечно-штамповочное производство. -1965. -№ 7. -С. 30−31.
- Тиса М. Исследование напряженно-деформированного состояния при глубокой вытяжке с учетом степенной зависимости упрочнения материала// Кузнечно-штамповочное производство 1985. — № 3. — С. 12−14.
- Томленов А.Д. Теория пластических деформаций металлов. М.: Машгиз, 1951.-378 с.
- Томсен Э., Янг Ч., Кобаяши Ш. Механика пластичных деформаций при обработке металлов/ Пер. с англ. Машиностроение, 1969. — 504 с.172
- Третьяков A.B., Зюзин В. И. Механические свойства металлов и сплавов при обработке давлением. 2-е изд. — М.: Металлургия, 1973. — 224 с.
- Унксов Е.П. Инженерная теория пластичности. Методы расчета усилий деформирования. -М.: Машгиз, 1959.
- Установление возможности однооперационной вытяжки контровочных замков ГТД с использованием торцевого подпора: Отчет по теме № 6.1864.5130.431/ НИАТ: Руководитель темы Е. Сизов- Руководитель этапа Е. Антонов. М., 1977. — 219 с.
- Хензель А., Шпиттель Т. Расчет энергосиловых параметров в процессах обработки металлов давлением: Справ, изд./ Пер. с нем. М.: Металлургия, 1982. — 360 с.
- Хилл Р. Математическая теория пластичности. М.: ГИТТЛ, 1956. -273 с.
- Чиченев H.A., Кудрин А. Б., Полухин П. И. Методы исследования процессов обработки металлов давлением. М.: Металлургия, 1977. -312 с.
- Чянь, Кобаяши. Влияние анизотропии и параметров упрочнения на распределение напряжений и деформации при глубокой вытяжке// Конструирование и технология машиностроения М.: ИЛ, 1966 — № 4-С. 117−123.
- Шехтер В.Я. Максимальная скорость деформации при глубокой вытяжке листовых материалов// Кузнечно-штамповочное производство. -1962.-№ 12.-С. 28−30.
- Шехтер В.Я. Перемещения, деформации, скорости и ускорения при глубокой вытяжке из листовых материалов. М.: Оборонгиз, 1951. -С. 13−19.173
- Шляхин А.Н. Расчет напряжений в опасном сечении при вытяжке без утонения цилиндрических деталей// Кузнечно-штамповочное производство. 1995. — № 6. — С. 20−23.
- Шофман JI.A. Основы расчета процессов штамповки и прессования. -М.: Металлургиздат, 1961.-291 с.
- Яблонский A.A., Никифорова В. М. Курс теоретической механики. М.: Высшая школа, 1971. — 424 с.174