Исследование наследственного влияния металлургических факторов на процессы структурообразования сталей при термической обработке тяжелонагруженных деталей автомобиля
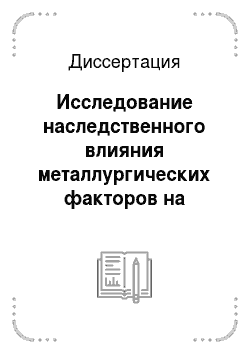
Диссертация
Впервые на термокинетической диаграмме превращения переохлажденного аустенита цементуемых легированных сталей выявлена зона формирования строченных структур, положение которой определяется температурно-скоростными параметрами стадии принудительного охлаждения стали после аустенитизации при изотермическом отжиге. Установлено, что явлением структурной полосчатости в стали можно управлять при… Читать ещё >
Содержание
- 1. Структурное состояние сплавов — основа служебных и технологических свойств металла
- 1. 1. Анализ методов подготовки структуры и свойств стали для механической обработки заготовок лезвийным инструментом
- 1. 1. 1. Микролегирование — основополагающий фактор улучшения обрабатываемости резанием конструкционных сталей
- 1. 1. 2. Термическая обработка — эффективный и наиболее рациональный метод подготовки структуры стали для качественной обработки резанием
- 1. 2. Анализ методов структурообразования стали для повышения и управления физико-механическими и специальными свойствами для обеспечения высокой работоспособности изделий
- 1. 2. 1. Управление структурообразованием стали на стадии закалки при термической обработке
- 1. 2. 2. Управление структурообразованием стали на стадии пластического деформирования изделий
- 1. 2. 3. Управление свойствами поверхностного слоя деталей при упрочнении
- 1. 3. Наследственность строения и свойств в стальных изделиях деталей машин
- 1. 1. Анализ методов подготовки структуры и свойств стали для механической обработки заготовок лезвийным инструментом
- Выводы по главе и задачи исследования
- 2. Теоретическое обоснование параметров тепловой обработки стальных заготовок, способов контроля свойств закалочных сред и методов формирования служебных свойств стали
- 2. 1. Основы выбора и теоретическое обоснование условий охлаждения заготовок при изотермическом отжиге
- 2. 2. Разработка и обоснование нового способа определения охлаждающей способности закалочных сред
- 2. 3. Исследование формирования служебных свойств металла в системе его преобразования в деталь
- Выводы по главе
- 3. Методы формирования структуры и свойств стальных заготовок для повышения их обрабатываемости резанием на автоматических линиях
- 3. 1. Исследование обрабатываемости стальных заготовок на операциях резания
- 3. 2. Исследование закономерности структурообразования стали и разработка унифицированного способа термической обработки
- Выводы по главе
- 4. Технологические аспекты комплексного исследования при разработке новых закалочных сред
- 4. 1. Исследования физико-химических и теплофизических свойств закалочных сред
- 4. 2. Влияние содержания полимера в растворе на закаливаемость, прокаливаемость и деформацию стали
- 4. 3. Исследование влияния скорости охлаждения при закалке на механические свойства улучшаемых сталей
- 4. 4. Влияние концентрации полимера в растворе на трещино-образование стали при закалке
- 4. 5. Мероприятия по внедрению и эксплуатации закалочных сред на основе водорастворимых полимеров
- Выводы по главе
- 5. Материалы и ресурсосберегающие технологии упрочнения сплавов для достижения высоких эксплуатационных свойств изделий
- 5. 1. Номографический метод выбора параметров термомеханической обработки
- 5. 2. Качество поверхности и упрочненного слоя — основное звено повышения долговечности деталей
- 5. 3. Технологические направления повышения геометрической точности зубчатых колес
- 5. 3. 1. Влияние предварительной термической обработки на деформацию стали при химико-термической обработке
- 5. 3. 2. Влияние технологии ХТО на геометрическую точность цементованных шестерен
- 5. 4. Разработка новых составов порошкообразных смесей для борирования изделий
- Выводы по главе
Список литературы
- A.c. 1 099 622 СССР. МКИ3 G01N 25/00. Способ определения охлаждающей способности закалочных сред./ Астащенко В. И., Янцен Г. И. и др.-№ 3 488 516/22/02 заявл. 26.08.82.
- A.c. 1 625 587 СССР, МКИ3 С23 С 87о. Состав для борирования стальных изделий. / Шибаков В. Г., Астащенко В. И., и др.- № 4 605 177/02- заявл. 14.11.88.
- A.c. 1 694 691 СССР, МКИ3 С23С 8/70. Состав для борирования отливок из стали./ Астащенко В. И., Янцен Г. И., и др.-№ 475 098/02- заявл. 26.07.89.- опубл. 30.11.91, Бюл. № 44с.
- A.c. 1 068 508 СССР, МКИ3, С21Д V78. Способ термической обработки заготовок./ Астащенко В. И., Волосов H.H., и др.- № 3 402 738/02- Заявл. 26.02.82- опубл. 23.01.84г, Бюл. № 3.
- A.c. 1 317 942 СССР, МКИ3 С21Д V78. Способ термической обработки заготовок./Янцен Г. И., Астащенко В. И. и др.-№ 3 900 282/22−02- заявл. 24.05.85- опубл. 02.02.87 Бюл. № 2.л о
- A.c. 1 266 226 СССР МКИ С22С /22- Способ газовой цементации стальных изделий/Астащенко В.И., Цуканов A.C., и др.- № 3 781 875- заявл. 16.08.84.
- Анненкова, В.З. Универсальная закалочная среда на основе ПК-2./ Анненкова В. З. и др.// Информационный листок № 82−36. Иркутский ЦПИ- 1981.-№ 82−36−2 с.
- Арзамасцева, Э. А. Градиент температур на поверхности как критерий реальной интенсивности охлаждения при закалке./ Арзамасцева Э. А.// ЭИ «Технология автомобилестроения», 1980.- № 1- с. 23−24.
- Арзамасцева, Э.А. Синтетические закалочные среды на основе полимерных водных растворов./ Арзамасцева Э.А.- М., НИИНавтопром, 1981, 8с.
- Арзамасцева, Э. А. Новый метод определения закаливающей способности среды./ Арзамасцева Э. А.// ЭИ «Технология автомобилестроения»,-1980.-№ 1- с. 23−24.
- Арзамасцева, Э. А. Термообработка как средство повышения обрабатываемости резанием цементуемых и улучшаемых сталей/ Арзамасцева Э. А.//ЭИ «Технология автомобилестроения».- 1980.- № 1- с. 35−39.
- Ассонов, А. Д. Современные методы термической обработки./ Ассонов А. Д.- М., Машиностроение, 1964, 191с.
- Ассонов, А. Д. Технология термической обработки деталей автомобиля./
- Ассонов А. Д.- М., Машгиз, 1958, 264с.
- Астащенко, В.И. Влияние концентрации кипящей закалочной жидкости «ТОСОЛ-К» на трещинообразование в сталях./ Астащенко В. И., Янцен Г. И., Ионкина Н. П. // Автомобильная промышленность- 1981.- № 5- с. 2930.
- Астащенко, В.И. Влияние технологических факторов на геометрическую точность цементованных изделий./ Астащенко В. И., Родькин И. М. // Изв. вузов, Сев. Кавк. регион. Технические науки. — 2005 г. — приложение № 3-с. 66−72.
- Астащенко, В.И. Изучение прокаливаемости сталей в слабых закалочных средах./ Астащенко В. И., Янцен Г. И., и др.//Металловедение и прочность материалов: сб. научных трудов/ Волгоград. полит, ин-т 1982.-с. 100−107.
- Астащенко, В.И. Испытания и контроль жидких закалочных сред./ Астащенко В. И., Янцен Г. И., и др.// Сб. научн. тр./ Волгоградский полит, ин-т- 1983.- с. 89−94.
- Астащенко, В.И. О «пятнистой» цементации стали./ Астащенко В. И., Каргинова Л. А. // МиТОМ- 1982.- № 6- с. 13 -15.
- Астащенко, В. И. О технологичности машиностроительных сталей. // Изв. вузов. Сев.-Кавк. регион. Технические науки. 2005 г.- приложение № 4, -с.42−45
- Астащенко, В.И. Оборудование для предварительной термической обработки./ Астащенко В. И., Волосов H.H., Янцен Г. И. // ЭИ «Передовой производственный опыт в автомобилестроении».- 1979.-№ 5- с. 10−18.
- Астащенко, В.И. Особенности охлаждающих сред применяемых для закалки деталей автомобиля «КамАЗ»./ Астащенко В. И., Ионкина Н. П. и др.//Технология автомобилестроения, 1981.- № 4- с. 26−28.
- Астащенко, В.И. Применение закалочной жидкости «ТОСОЛ-К» для объемной закалки сталей./ Астащенко В. И., Янцен Г. И., Ионкина Н. П. // МиТОМ- 1982.- № 6- с. 5−8.
- Астащенко, В.И. Применение полимерных закалочных сред в автомобилестроении./ Астащенко В. И., Рудницкий Н. М., Устиловский С. Я. М.: НИИНавтопром, 1984.- 55 с.
- Астащенко, В.И. Применение синтетических закалочных сред для закалки деталей автомобиля./ Астащенко В. И., Янцен Г. И. // Технология автомобилестроения- 1982.- № 10- с. 7−10.
- Астащенко, В.И. Повышение качества балки переднего моста автомобиля «КамАЗ»./ Астащенко В. И., Лукин В. И. //Передовой производственный опыт в автомобилестроении.- 1981.- № 5- с. 18−21.
- Астащенко, В.И. Структура и свойства стали 42ХМФА после закалки в водном растворе полимера./ Астащенко В. И., Янцен Г. И., Николаев В. В. // Технология автомобилестроения- 1982.- № 11- с. 11−14.
- Астащенко, В.И. Трещинообразование сталей при закалке в водных растворах полимера./ Астащенко В. И., Калинина Н. П., Янцен Г. И.// Автомобильная промышленность- 1982- № 4- с. 28−29.
- Астащенко, В.И. Улучшение обрабатываемости резанием поковок за счет реализации скрытых резервов в кузнечно-термическом производстве./
- Астащенко В.И., Мокроусов Ю. М., Родькин И. И. // Изв. вузов. Сев.-Кавк. регион. Технические науки. 2005 г. — Приложение № 2-с. 81−85.
- Астащенко, В.И. Упрочнение шатунов автомобильных двигателей при дробеочистке./ Астащенко В. И., Янцен Г. И., и др. // Автомобильная промышленность, — 1984.-№ 8- с. 10−11.
- Астащенко, В. И. Технологические методы управления структурообразованием стали при производстве деталей машин// Астащенко В. И., Шибаков В. Г. Камская госуд. инж.-эконом. академия — М.: Academia, 2006 — 328с.
- Астащенко, В.И. Особенности охлаждающей способности водных растворов полимеров. /Астащенко В.И.// Социально-экономические и технологические системы: онлайновый электронный научно-технический журнал. 2007 г. — № 1−6с. — Ресурс доступа: www.kampi.ru/sets.
- Баскаков, А.П. Нагрев и охлаждение металлов в кипящем слое./ Баскаков А. П.- М, Металлургия, 1974.- 271с.
- Баскаков, А.П. Опыт применения кипящего слоя охлаждающей среды при закалке некоторых изделий./ Баскаков А. П. и др. Сб.: Теоретические и технологические вопросы закалочного охлаждения, М.:1969.-с.124−130.
- Бернштейн, M.JI. Термомеханическая обработка стали./ Бернштейн М. Л., Займовский В. А., Капуткина Л. М. М.: Металлургия, 1983.- 480 с.
- Бичеев, A.M. Металлургия стали./ Бичеев A. M. М.: Металлургия, 1988.480 с.
- Блантер, М.Е. Методика исследования металлов и обработка опытных данных./Блантер М.Е. М.: Металлургиздат, 1982.- 444с.
- Блантер, М.Е. Скорость охлаждения при закалке и прокаливаемость стали./ Блантер М. Е. // Заводская лаборатория, 1949.- № 5- с. 557−567.
- Блантер, М.Е. Теория термической обработки./ Блантер М. Е.,-М.: Металлургия, 1984.- 328 с.
- Богачев. И. Н. П.П. Аносов и секрет булата./ Богачев И. Н.,-М.- Свердловск: Машгиз, 1952, 139с
- Богатырёв, Ю.М. Влияние скорости охлаждения на образование трещин при закалке./ Богатырёв Ю. М., Шкляров A.C., Шепеляковский К. З. // МиТОМ, 1967.-№ 4-с. 15−17.
- Богданов, C.B. Влияние закалки с ковочного нагрева на прокаливаемость сталей./Богданов С.В.//МиТОМ.- 1967.- № 3- с.77−79.
- Бронт, B.C. Применение ультразвука при термической обработке металлов./ Бронт B.C. М.: Металлургия, 1977.- 138 с.
- Будрин, Д.В. Водо-воздушное охлаждение при закалке./ Будрин Д. В., Кондратов В. М. // МиТОМ- 1965.- № 6- с. 22.
- Булгаков, В.А. Влияние исходной структуры на деформацию и коробление деталей после окончательной термической обработки.// МиТОМ- 1977.-№ 9- с. 45 47.
- Варагин, Н.И. «Кипящий слой» новая закалочная среда с регулируемой охлаждающей способностью. //МиТОМ, 1961.- № 6-с. 13−18.
- Васильев, A.A. Закалка стали в вибропсевдосжиженном слое. // Металлургия, 1973.- с. 106−111.
- Вишняков, Д.Я. Технология обработки стали./ Вишняков Д. Я. -М.: Московский институт стали, 1948.-142 с.
- Влияние твердости, полученной при закалке стали 45 на ее выносливость после высокого отпуска./ Рудницкий Н. М. Казанчан Т.А.//Сб.научных трудов/НАМИ- 1966.-№ 85- с. 15−26.
- Вопросы закалочного охлаждения: сб. статей. / МДНТП им. Ф. Э. Дзержинского.- М.- 1969.-194 с.
- Вопросы теплообмена при изменении агрегатного состояния вещества, сталей./ Кутателадзе С. СЛ Сб. научных трудов.- М: Госэнергоиздат- 1953.-186с.
- Вульф, A.M. Резание металлов./ Вульф A.M.- Л.: Машиностроение, 1973.496 с.
- Вышковский, Ю.Г. Влияние температуры воды и водных растворов на образование трещин при закалке./ Вышковский Ю. Г. // МиТОМ-1960.-№ 2-с.32.
- Гиршович Н. Г. Кристаллизация и свойства чугуна в отливках./ Гиршович Н. Г., М.-Л.: Машиностроение, 1966,562с.
- Гладштейн, Л.И. Применение душа для закалки низколегированной стали. // МиТОМ-1964.- № 12- с. 2−6.
- Головин, Г. О., Зимин Н. В. Технология термической обработки металлов с применением индукционного нагрева./ Головин Г. О., Зимин Н. В. Л.: Машиностроение, 1979.- 242 с.
- Гольдштейн, Я. Е. Конструкционные стали повышенной обрабатываемости./Я. Е. Гольдштейн, А. Я. Заславский.- М.: Металлургия, 1977.- 248 с.
- Гончар, В.И. Влияние промежуточных структур на свойства конструкционных сталей./ Гончар В. И., Воскобойникова A.A., Щербакова А. Ф. // Изв. вузов «Машиностроение», 1966.- № 1- с. 149−153.
- Григорьев, П.А. Кипение криогенных жидкостей./ Григорьев П. А., Павлов Ю. М., Аметистов E.B. М.: Энергия, 1977.- 288 с.
- Григорьев, П. А. Физические свойства сталей и сплавов, применяемых в энергетике./Григорьев П.А.- Л.: Энергия, 1967.-218с.
- Гуляев, А.П. Влияние продуктов превращения на сопротивление разрушению улучшаемой конструкционной стали./ Гуляев А. П., Голованенко Ю. С., Зинеев В.Н.// МиТОМ, 1978.- № 7- с. 60−67.
- Гуляев, А.П. Металловедение/ А. П. Гуляев -М.: Металлургия, 1977.- 648 с.
- Гуляев, А.Н. Образование трещин при термической обработке стальных изделий./ Гуляев А. Н, Якушев С.П.// Станки и инструмент, 1961.- № 8-с.27.
- Гуляев, А.П. Определение порога хладноломкости стали микроскопическим методом./ Гуляев А. П., Шермазан И. В., Зеленова В. Д. // Заводская лаборатория 1966.- № 7- с. 879−882.
- Гуляев, А.П. Термическая обработка стали./Гуляев А. П.,-М.: Машгиз, 1960, 496с.
- Гуляев, Б. Б. Синтез сплавов./ Гуляев Б. Б., — М., Металлургия, 1984,160с.
- Давыдова, Л.Н. Свойства конструкционных сталей, рафинированных синтетическими шлаками./Давыдова Л. H. М.: Металлургия, 1969.-135 с.
- Дальский, A.M. Технологическое формирование показателей качества деталей машин./ Дальский A.M. // Технологические основы обеспечения качества машин.- М.: Машиностроение, 1990.- с. 212 234.
- Дедек, В. В. Закалка стальных полос./ Дедек В. В. М.: Металлургия, 1977.-248 с.
- Демкин, М.Б. Качество поверхности и контакт деталей машин./ Демкин М. Б., Рыжов Э. В. М.: Машиностроение, 1981.- 244 с.
- Демичев, А.Д. Высокочастотная закалка./ Демичев А. Д., Головин Г. Д., Шашкин C.B. М.-Л., Машиностроение, 1965.- 88 с.
- Домнина, Н. В. Процессы закалочного охлаждения в средах с обратной растворимостью на основе полиалкиленгликолей./Домнина Н. В., Помельникова А. С.// Изв. вузов. Черная металлургия. 2005-№ 2-с. 43−46.
- Заваров, A.C. Термическая обработка в кипящем слое./ Заваров A.C., Баскаков А. П., Грачёв С. Б. М.: Металлургия, 1981.- с. 84.
- Зеленова, В.Д. Механизм вязкого и хрупкого разрушения и методы оценки сопротивления разрушению металлов и сплавов./ Зеленова В. Д. М.: Машиностроение, 1975.-40с.
- Зеленова, В.Д. Электронно-микроскопический метод количественного определения вязкой составляющей в изломе./ Зеленова В. Д., Шермазан И. В. // Заводская лаборатория- 1972.- № 12 с. 1477−1481.
- Зимин, Н.В. Кинетика душевого охлаждения поверхности и охлаждающая способность душа различных жидкостей. // Металлургия и коксохимия -1973.-№ 36- с. 17−21.
- Зимин, Н.В. Об эффективности интенсивного душевого охлаждения.// МиТОМ-1970.- № 5-с. 34−36.
- Зимин, Н.В. Применение регулируемого душевого охлаждения при закалке сталей. // МиТОМ- 1977.- № 2- с. 31−36.
- Зинченко, В.М. Инженерия поверхности зубчатых колес методами химико-термической обработки./ Зинченко В. М. М.: МГТУ им. Н. Э. Баумана, 2001.-303 с.
- Зинченко, В.М. Интенсификация процесса цементации стали./ Зинченко В. М., Янцен Г. И., Астащенко В.И.// Автомобильная промышленность-1986.-№ 4- с. 30−31.
- Иванова, В. С. Природа усталости металлов. / Иванова В. С., Терентьев В. Ф. М., Металлургия, 1975, 456с.
- Кадыков, Н.С. Исследование структуры и прокаливаемости сталей при охлаждении водо-воздушными средами./ Кадыков Н. С., Корочкин А. Е. // Изв. Вузов. «Черная металлургия" — 1973, — № 4- с. 146−148.
- Казачков, И.В. Свойства закалочных средств на основе водорасворимых полимеров./ Казачков И. В., и др.// Технология автомобилестроения, 1977.- № 6- с. 21−29.
- Калинин, А.Т., Термическая обработка на Волжском автомобильном заводе./ Калинин А. Т., Тихонов А.К.// МиТОМ.- 1973.- № 9- с. 17.
- Качанов, H.H. Прокаливаемость стали./ Качанов H.H. М.: Металлургия, 1978.-192 с.
- Каюшников, П.Я. Бездефформационная закалка./ Каюшников П. Я. //МиТОМ- 1963.-№ 3-е. 18−19.
- Кидин, H.H. Электро химико — термическая обработка металлов и сплавов./ Кидин H.H. и др. — М.: Металлургия, 1978.- 320 с.
- Коваленко, В. С. Металлографические реактивы./ Коваленко В. С. М., Металлургия, 1973, 286с.
- Кобаско, Н.И. Влияние скорости охлаждения при закалке на образование трещин в стали 45./ Кобаско H.H., Прохоренко НИ. // МиТОМ, 1964.- № 2-с. 11−14.
- Кобаско, Н.И. Закалка стали в жидких средах под давлением./ Кобаско Н. И. Киев: „Наукова думка“, 1980.- 203 с.
- Кобаско, Н.И. Исследование с помощью ЭВМ тепловых процессов при закалке стали./ Кобаско Н. И. // МиТОМ, 1976.- № 10- с. 8−13.
- Кобаско, Н.И. Образование трещин при закалке стали./ Кобаско Н.И.// МиТОМ, 1970.-№ 11-е. 34−36.
- Кобаско, Н.И. Оценка охлаждающей способности закалочных сред с использованием характеристик процесса кипения./ Кобаско Н. И., Констанчук Д. М. // МиТОМ, 1973.- № 10- с. 21−26.
- Козловский И.С. Прокаливаемость стали./ Козловский И. С. М.: Машгиз, 1945- 95 с. с ил.
- Козловский, И.С. Химико-термическая обработка шестерен./ Козловский И. С. М.: Машиностроение, 1970.- 232 с.
- Конторович, Л.В. Приближенные методы высшего анализа./ Конторович Л. В., Крылов В. И. М: Физматгиз, 1962.-242 с.
- Контролируемая закалка в полимерных средах на базе полиакрилата натрия: экспресс информация.//Технология автомобилестроения, 1979.-№ 10-с.17−19.
- Крамаров, М.А. Оценка сопротивления разрушению стали 35ХНЭМФА для круглых заготовок./ Крамаров М. А. и др.// МиТОМ, 1976.- № 2- с. 14−16.
- Красиков, В.В. Влияние прокаливаемости стали на деформацию шестерен в процессе химико-термической обработки./ Красиков В. В., и др.// Автомобильная промышленность.- 1979.- № 8- с. 31.
- Кузнецов, Б.Л. Введение в литейное металловедение чугуна/ Кузнецов Б. Л. -М.: Машиностроение, 1995. 168 с. с ил.
- Курбатов, А.П. Закалка инструментальных сталей в кипящем слое./ Курбатов А. П., Муравьёв В. И. // МиТОМ, 1970.-№ 2- с.46−48.
- Кугультинов, С. Д. Технология обработки конструкционных материалов/ Кугультинов С. Д., Ковальчук А. К., Портнов И. И.// М.: Изд-во МГТУ им. Н. Э. Баумана, 2006−672с.
- Лапкин, П.А. Сжатый воздух как охлаждающая среда при поверхностной закалке. // МиТОМ- 1967. № 4-е. 7−8.
- Лахтин, Ю.М. Материаловедение: учебник для вузов/ Ю. М. Лахтин, В. П. Леонтьева.- М.: Машиностроение. 1990.- 528 с.
- Люты, В. Закалочные среды./ Люты В. // Под ред. Масленкова C.B., пер. с польского, Челябинск: Металлургия, 1990.- 192 с.
- Ляхович, Л.С. Борирование стали./ Ляхович Л. С., Ворошнин Л. Г. М.: Металлургия, 1967.- 119 с.
- Маклаков, В.Е. Применение негорючей закалочной жидкости „ТОСОЛ-К“ для закалки коленчатых валов./ Маклаков В. Е., Сорокин И. Е., Астащенко В. И. // Кузнечно-штамповочное производство- 1984, — № 2- с. 19−20.
- Малинкина, Е.И. Образование трещин при термической обработке стальных изделий./ Малинкина Е. И. М: Машиностроение, 1965.- 173с.
- Малинкина, Е.И. Прокаливаемость стали./ Малинкина Е. И., Ломакин В. Н. М.: Металлургия, 1969.- 190 с.
- Мединский, Л.Б. Непосредственное определение охлаждающей способности среды./ Мединский Л. Б. // Заводская лаборатория. 1959.- № 5-с.628−670.
- Меськин, B.C. Основы легирования стали./ Меськин В. С.- М.: Металлургия, 1964.- 684 с.
- Минкевич, А. Н. Химико-термическая обработка металлов и сплавов./ Минкевич А. Н.-М., Машиностроение, 1965, 491с.
- Моталин, А. А. Технологические методы повышения долговечности деталей машин. / Моталин А. А.-Киев, „Техннса, 1971, 144с.
- Муратов. В. С. Структурная наследственность и улучшение свойств изделий из алюминиевых сплавов.//Генная инженерия в сплавах: Тез. докл. Межд. НПК. Самара: Сам.ГТУ. 1998. с.44−45.
- Никитин, В. И. Наследственность в литых сплавах/ Никитин В. И., Никитин К. В.- М. Машиностроение 1. 2005. 476с.
- Нихендзи, Ю. А. Стальное литье./ Нихендзи Ю. А.- М.: Металлургиздат., 1948. 766с.
- Николаев, Б.Н. Термическая обработка металлов токами высокой частоты: учебник./ Николаев Б. Н., Коротин И. М. М.: Высшая школа, 1977.- 214 с.
- Новиков, И.И. Теория термической обработки металлов./ Новиков И. И. -М.: Металлургия, 1974 400 с.
- Новые закалочные среды для термической обработки легированных сталей./ Алдырев Д. Л. и др.//Технология автомобилестроения: сб. научных трудов, — Ростов НД, 1979.- № 23- с.70−73.
- Обзор особенностей микроструктур при разрушении сколом./ Jloy Р.Д. //Сб.научных трудов“ Атомный механизм разрушения» М.: Металлургиздат, 1983.- с.84−88.
- Опыт разработки и внедрения в производство негорючих закалочных сред на водной основе и методы контроля их охлаждающей способности: Тезисы докладов и сообщений всесоюзного научно-технического семинара, Волгоград, ВНИИТмаш, 1982, 102с.
- Отработка режимов изотермического отжига поковок на Кузнечном заводе КамАЗа: Отчет о НИР (заключ.):181−75/ НИИТавтопром- рук. Кохова Г. М.- исп. Белугин И. И.
- Патент 56−11 731 Япония, С21Д '/бо- Охлаждающая жидкость для охлаждения при поверхностном упрочнении металлов./ Такомура Мотохира и др.-№ 48−68 274 заявл. 19.06.73.- опубл. 17.03.81.
- Патент № 3 902 929, США, кл.148−28(В23К 3524). Закалочная смесь на водной основе и метод закалки в ней./ Meszaros Anthony. № 3 865 642, заявл. 02.02.81.
- Патент № 3 902 929, США, кл. 148−28 (В23К 3524). Метод закалки и водный раствор для закалки, содержащей поливинилпирролидон./ Meszaros Anthony.-№ 3 794 422, заявл. 30.06.80.
- Патент № 1 242 660, ФРГ, кл.18 С б0 (С21Д '6о). Закалочная среда для закалки термически обрабатываемых материалов./-№ 3 306 421, заявл. 04.01.80.
- Патент № 49−40 324, Япония, кл. 10А742(С21Д 160). Закалочная среда./Такомура Мотохира и др.-№ 48−68 201, заявл. 19.11.73.
- Патент № 933 858, ПНР, кл. С21Д 160. Konzentrat do kapile hastownicrych./ Microwevar Andrey, Adowski Moriusz, Polesynski Tadeusz.-№ 621 414,зaявл. 31.12.76.
- Патент № 1 016 377 Российская Федерация МКИ3, С21Д Уб0. Закалочная среда./Николаев В. В. Маклаков В.Е., Астащенко В. И., Янцен Г. И.: заявитель и патентообладатель ОАО «КамАЗ» № 3 278 813- заявл. 21.04.81. Опубл. 07.05.83, Бюл. № 17−1981.-1 с.
- Патент № 1 712 462 Российская Федерация МКИ3 С23С 8/70 Порошкообразный состав для борирования стальных изделий./ Янцен Г. И., Астащенко В. И., Сергеева Е.И.-№ 4 792 103/02 заявл. 13.02.90.- опубл. 12.02.92. бюл. № 6, 1с.
- Петраш, JI.B. Закалочные среды./ Петраш JI.B. M-J1: Машгиз, 1960.106 с.
- Плетнева, H.A. Закономерность испарения капель в сфероидальном состоянии./ Плетнева H.A., Ребиндер П. А. // Физическая химия, 1946.-№ 9-с. 961.
- Попова JI. Е. Диаграммы превращения аустенита в сталях и бета-раствора в сплавах титана./Попова Л. Е. Попов А. А. М.: Металлургия, 1991−502с.
- Погодин, В.Г. Влияние ультразвуковых колебаний на охлаждающую способность закалочного масла.// МиТОМ- 1973-№ 10-с.12−13.
- Прибор для контроля закалочных сред фирмы «Хойтон». Пер. с нем., № Б-33 857, М.: НИИНавтопром, 1979.- 9 с.
- Прженосил. Б. Нитроцементация. Пер. с чешек. -М., Машиностроение, 1969, 210с.
- Приходько, B.C. Охлаждающие среды для закалки./ Приходько B.C. М.: Машиностроение, 1977.-32с.
- Расчетное определение температур и напряжений, возникающих в цилиндрических деталях при охлаждении с температур отпуска./ Устиловский С. А., Рудницкий Н. М., Шапкина H.A. // Сб. научных трудов/НАМИ-1978.- вып. 175. с. 3−14.
- Руссов, К.Д. Новая полимерная закалочная среда ЗСП-1./ Русов К. Д., Розенко Л. Б. // МиТОМ, 1977.-№ 2- с.36−37.
- Сагарадзе, B.C. Повышение надежности цементуемых деталей./ Сагарадзе B.C. М.: Машиностроение, 1975.- 216 с.
- Салтыков С. А. Стереометрическая металлография. М.: Металлургия, 1970−376с.
- Садовский В. Д. Структурная наследственность в стали. М.: Металлургия 1973−208С.
- Садовский В. Д. Происхождение структурной наследственности в стали//Физика металлов и металловедение, 1984, 57, № 2, с. 213−223.
- Сарак, В.И. Неоднородное распределение внутренних напряжений и склонность стали к хрупкому разрушению./ Сарак В. И. и др.//Физика металлов, 1969.-№ 1-с. 143.
- Серенсен, C.B. Несущая способность и расчет деталей на прочность./ Серенсен C.B., Кочаев В. П., Штейнцерович В. М. М.: Машиностроение, 1975.- 113 с.
- Склюев, П.В. Влияние скорости охлаждения температуры переохлаждения на ударную вязкость и переходную температуру стали 35X3MH и 34X3МН./ Склюев П. В. // МиТОМ, 1977.- № 8- с. 15−26.
- Смирнов, A.B. Закалка и цементация в жидких средах./ Смирнов A.B., Бабошин A.A., Масалов Н. И. М.: Госметаллургиздат, 1933.-184 с.
- Спектор, Н.И. Некоторые особенности охлаждения в во до-воздушной смеси при индуктивном нагреве./ Спектор Н. И., Грачева А. Н. // МиТОМ-1962.-№ 3-е. 38−39.
- Специальные стали. В 2 т. Т.1/ Э. Гудремон. М.: Металлургия, 1959.- 952 с.
- Справочник. Диаграммы горючей деформации, структура и свойства сталей. / M.JI. Бернштейн и др. -М.: Металлургия, 1989.- 543 с.
- Справочник. Химико-термическая обработка металлов и сплавов./ Борисенок Г. В. и др.- М., Металлургия, 1981.- 424 с.
- Справочник металлиста. В 5 т. Т2. /Под ред. Рахштадта А. Г. и Брострема В. А.- М.: Машиностроение, 1976- 720 с.
- Справочник. Термическая обработка в машиностроении/Под ред. Ю. М. Лахтина и А. Г. Рахштадта. М.: Машиностроение, 1980.- 783 с.
- Суслов, А.Г. Качество поверхностного слоя деталей машин./ Суслов А. Г. -М.: Машиностроение, 2000.- 320 с.
- Старокожев, Б.С. «Пятнистая» цементация сталей./ Старокожев Б. С., Ковригин В. А., Чернов И. А. // МиТОМ- 1978.- № 9- с. 17−19.
- Сызранцев, В.И. Диагностика нагруженности и ресурса деталей трансмиссий и несущих систем машин по показаниям датчиков деформаций интегрального типа./ Сызранцев В. И., Гольфаст С. П., Сызранцев К. В. Новосибирск.: Наука, 2004. — 188 с.
- Тамарин, А.И. Вибропсевдосжиженный слой новая закалочная среда./ Тамарин А. И. и др. // МиТОМ, 1968.- № 3- с. 10.
- Технология изотермического отжига: материалы симпозиума/Завод им. Лихачева- под ред. д-ра Вюннинга.- М, 1977,38 с.
- Технология термической обработки заготовок/Материалы фирмы «Хеннинг» (ФРГ) — 1956- 32 с.
- Толстоусов, А.Б. Новая закалочная среда на основе водорастворимого полимера./ Толстоусов А. Б., Банных O.A. // МиТОМ, 1981, — № 2-с. 5−8.
- Тылкин, М. А. Справочник термиста ремонтной службы./ Тылкин М. А., М.: Металлургия, 1981, 648с.
- Фельдштейн, Э.И. Обрабатываемость сталей в связи с условиями термической обработки/ Фельдштейн Э.И.- М.: Машгиз, 1953.- 254 с.
- Форма образца главный фактор для определения охлаждающей способности закалочной среды.// РЖ. «Металлургия», серия «Металловедение и термическая обработка», 1979.- № 5-с. 424.
- Хапонен, Н. А. Методика комплексного неразрушающего контроля стали у оборудования повышенной опасности/ Хапонен Н. А., Иванов Г. П., и др.//Безопасность труда в промышленности-2001-№ 8-с.34−36.
- Хина, M.JI. Закалочные среды на основе водорастворимых полимеров./ Хина М. Л., Васильков В. Ф., Кобзов И. С. // МиТОМ, 1978.- № 8- с.70−73.
- Чернышев, Г. Д. Повышение надёжности изделий ЯМЗ и автомобилей КрАЗ./ Чернышев Г. Д., Малышев А. А, Ханин Н. С. М.: «Машиностроение», 1977.- 288 с.
- Чижиков, A.C. Струйное охлаждение плоских изделий при термической обработке./ Чижиков A.C., Эйсмонд Ю. Г. // МиТОМ- 1975.- № 4- с. 3−6.
- Шаврин, О. И. Технология и оборудование термомеханической обработки деталей машин. М., Машиностроение, 1983. 176с.
- Шепеляковский, К.З. Термическая обработка стали при индукционном нагреве./ Шепеляковский К. З. // МиТОМ-1977.-№Ю-с.72−78.
- Шепеляковский, К.З. Упрочнение стали поверхностной закалкой при индукционном нагреве./ Шепеляковский К. З. М.: Машиностроение, 1972.-287с.
- Шибаков, В.Г. Борирование деталей машин и пресс-оснастки в порошкообразных смесях./ Шибаков В. Г., Астащенко В. И., Сергеева Е. И. // Упрочняющие технологии и покрытия- 2005 № 11- с.25−27
- Шибаков, В.Г. Унифицированная технология отжига стальных заготовок./ В. Г. Шибаков, В. И. Астащенко, Ю.М. Мокроусов//Заготовительные производства в машиностроении 2006 — № 9-с. 44−48.
- Шибаков, В.Г. Управление структурообразованием стали на стадии изготовления изделий пластическим деформированием./В.Г. Шибаков, В.И. Астащенко//Кузн.-штамп, пр-во и ОМД 2006 — № 6 — с.31−36
- Шмыков, A.A. Справочник термиста./ Шмыков A.A. М: Машгиз, 1961.-182 с.
- Штейнберг, С.С. Охлаждающие среды для закалки./ Штейнберг С. С. -М.: ПМО металлургов, 1939, леция № 14.
- Юзаев Б.Н. Теплопередача: учебник/ Юзаев Б.Н.- М.: Высшая школа, 1981.-209с.
- Abschreck-Medium «Asmanil»: проспект фирмы «OsmiroP'(OPr).-1970−44 с.
- Almand, Е. Surveilland des huiles de trempe./ Almand E., Damagnez M. //Trait. Therm., 1970.- № 49- c. 43−45.
- Beitz, H. Neuartiges wassriges Abschreckmedium fur die Hartung emflifindlicker nichtmartensitischer Abruhlungsvorgange: 7-ой международный симпозиум- Бухарест- 1979.- с.749−759.
- Blanckard, P.M. Properties of guenchants/ Blanckard P.M. //Metallyrgia and Metall Forming, 1973-№ 6- c. 177−180.
- Boor, Udo. «Ein vollautomatisirter Prufgerat zur Beuzteilung der Abschreckfahigkeit von Harteolen»./ Boor Udo. //TZ. F. prakt. Metallbearb., 1975.- № 9-c. 299−301.
- Burgdorf, E. Eigenschaften und Einsatzgebute Synthetischer. Abschrecklosungen./Burdorf E.//ZwF, 1979.- № 9-c. 431−436.
- Burgdorf, E. Flussige Abschreckmittel Pruflmg und Uberwachung./ Burgdorf E. //Techn. Zbe. Prakt. Metallbearb., 1979.- № 3- c. 109−114.
- Filipow, W.I. Badanie zdolnosci chlodzacych olejow hartowniczych./ Filipow W.I., Marmer E.N.//Metalozn. Obrol. Giepl., 1981.- № 51- c. 15−16.
- French H.I. Transactions ASST, vol. XVII, 1930.
- Quenchants and heat treatment fluids Bergen R.T.//Wire.Ind., — 1979.-№ 7-c.493.
- Laslay Stanley B. Metal guenching witch cils and syntetic malia//Ind.Heat., 1976.-№ 10-c. 8−14.
- Le Chatelier M.H. Revue de Metallurgie, vol.1, 473, 1904.
- Matuschka A. Konstr. Elem. Meth, 1973, Bd. 10, № 5, p. 54 — 58.
- Mohr Terry, W. A better way to evalate guenchants./ Mohr Terry W.//Metal. Pogr., 1974.- № 5-c. 85−86.
- Owaku, Shigeo. Охлаждающая способность закалочных жидкостей./ Owaku Shigeo./ZHewe cepu, Netsu shori, j.jap. Sec. Heat. Treat., 1980.- № 4- c. 152−157.
- Ohmari, 1./ Ohmari 1., Othani H., Kunitahe D. //Metal Sience, 1974.- № 8- 11-c. 357.
- Owaki, Snigeo. Охлаждающая способность закалочных жидкостей.//Мецу Сёра, Netsu Shori, J. Jap. Soc. Heat Treat. 1980.-№ 4- с. 152−157.
- Rosenbeild, A./ Rosenbeild A., Hohn G., Embury J. //Met. Trans., 1972.- № 11-c. 2797.
- Sandor, Leslie W. Szintikus edzofolgader tulajdonsagai es alkalbasasi lehetosegei.//Bangasz. Lapok. Kohasz-1979.-№ 10-c.447−454.
- Singleton, O.R. Untersuching neuer Abscheckmittel fur Aluminium. //Aluminium. 1969.- № 8- c.499−505.
- Seifert W. Erfahrung bei der praktieschen Anwendung des neuer Abschreckmittels «Aqua-Plast».: 2-й международный симпозиум, — Варна,-1969.-с. 72−74.
- Spezial-Konzentrat rum risspreisen Harten «Aquaguench»: проспект фирмы «Haughton» (ФРГ).-1969.-59 с.
- Suttie, N.R. The use of polumer guenchants for aluminium alloy heat treatment.//Heat. Treat.Metals. 1979.- № 1- c.19−21.
- Witold W. Austeniete Transformation Kinetics of Ferrows Alloys. Glimax Molibdenum Gompany, Grunwich, 1975, p. 84.
- Wyszkowski, J. «Wobol -3 «-neues Suntketischer Abschreckmedium das Ol oder Wasser ersatz.: 7 Simp. Jnt. Met. Fiz. Si tratamente term.-Bucuresti, 1979.- c. 769−778.
- УТВЕРЖДАЮ Главный инженер завода двигателей1. Н.С. Галкин» 1989 г. 1. АКТ
- Испытаний опытно-промышленных партий поковок из стали 15ХГН2ТА обработанных в цехе 208−210.
- В таблице приведены результаты расхода режущего инструмента из расчета на 1000 м/к при обработке промышленных партий.