Исследование и применение керамических материалов из ультрадисперсных порошков, полученных плазмохимическим синтезом
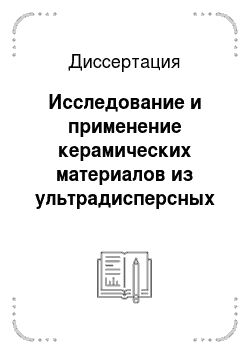
Диссертация
Термодинамическая метастабильность УДП позволяет синтезировать уникальные соединения и фазы, активируя важнейшие этапы процесса за счет химической поверхностной активности УДП. Однако эти же факторы обуславливают и их недостатки для порошковой технологии: агломерирование сорбирование примесей, пыление, плохую прессуемость и формуемость, вследствии низкой насыпной плотности. Присутствие… Читать ещё >
Содержание
- 1. КОНСТРУКЦИОННЫЕ КЕРАМИЧЕСКИХ МАТЕРИАЛЫ НА ОСНОВЕ УЛЬТРА (НАНО)ДИСПЕРСНЫХ ПОРОШКОВ А12Оэ и Zr02(Y)
- 1. 1. Оксид алюминия и диоксид циркония: фазовые превращения и механические свойства
- 1. 2. Особенности порошков, полученных различными методами синтеза
- 1. 3. Технология получения керамических материалов
- 1. 4. Литье термопластичных шликеров
- 1. 5. Технологическая подготовка порошков
- 2. ПОСТАНОВКА ЗАДАЧИ. МАТЕРИАЛ И МЕТОДИКА ИССЛЕДОВАНИЙ
- 2. 1. Постановка задачи
- 2. 2. Материалы исследований
- 2. 3. Методика исследований
- 3. ТЕХНОЛОГИЧЕСКАЯ ПОДГОТОВКА ПЛАЗМОХИМИЧЕСКИХ ПОРОШКОВ А1203 и Zr02(Y) ПЕРЕД ФОРМОВАНИЕМ
- 3. 1. Исследование физических и технологических свойств УДП при различных технологических схемах их обработки
- 3. 1. 1. Механическая обработка
- 3. 1. 2. Предварительный отжиг порошков
- 3. 1. 3. Отжиг и механическая обработка порошков
- 3. 2. Исследование фазового состава УДП при различных технологических схемах их обработки
- 3. 1. Исследование физических и технологических свойств УДП при различных технологических схемах их обработки
- 4. ТЕХНОЛОГИЯ ПОЛУЧЕНИЯ ТЕРМОПЛАСТИЧНЫХ ШЛИКЕРОВ НА
- ОСНОВЕ ПЛАЗМОХИМИЧЕСКИХ ПОРОШКОВ А1203 и Zr02(Y)
- 4. 1. Влияние операций технологической подготовки порошков на содержание термопластичной связки в шликере
- 4. 2. Исследование технологических свойств УДП при изменении технологических параметров шликерного
- 5. СТРУКТУРА, ФАЗОВЫЙ СОСТАВ И МЕХАНИЧЕСКИЕ СВОЙСТВА СПЕЧЕННЫХ МАТЕРИАЛОВ
- 5. 1. Изучение спекания образцов и изделий при изменении времени и среды обжига
- 5. 2. Микроструктура, фазовый состав УДП
- 5. 3. Механические характеристики спеченной керамики
- 5. 4. Технология получения керамических изделий и их применение
Список литературы
- Петрунин В.Ф., Рябев Л. Д. Состояние и перспективы развития проблемы «Ультрадисперсные (нано-) системы» // Физикохимия ультрадисперсных систем. Сборник научных трудов 1. Всероссийской конференции. М.: МИФИ, 1999.-С. 18−22.
- Андриевский Р.А. Наноструктурные материалы состояние разработок и перспективы // Перспективные материалы. — 2001. — № 6. — С.5−11.
- Швейкин Г. П. Керамика: прогнозы развития // Огнеупоры и техническая керамика. -№ 7. С.5−9.
- Лукин Е.С., Попова Н. А., Здвижнова Н. И. Прочная керамика на основе оксида алюминия и диоксида циркония // Стекло и керамика. 1993. — № 9−10. — С.25−30.
- Лукин Е.С. О влиянии методов синтеза и условий подготовки порошков оксидов в технологии высокоплотной и прозрачной керамики // Тр.Моск. хим,-технол. Ин-та им. Д. И. Менделеева, 1974. вып. 123. — С.5−16.
- Валкевич В.Л. Техническая керамика М.: Стройиздат. — 1968. — 198с.
- Галахов А.В., Цибайло Е. В. Неоднородность упаковки в порошковых компактах и прочность получаемой из них керамики // Огнеупоры и техническая керамика. -1997. № 5. — С.22−26.
- Скороход В.В., Солонин Ю. М., Уварова И. В. Химические диффузионные и реологические процессы в технологии порошковых материалов. Киев: Науко-ва думка, 1990. — 249с.
- Оно М. Ультрадисперсные частицы и новые процессы изготовления керамики. Эрэкуторонику сэрамикусу, 1986. — 17, № 3. — С.21- 25.
- Дубровина А.Н., Ахтямов Ю. Р., Князев Е. В., и др. Фазовый состав ультрадисперсных частиц А1203 и Zr02// Кристаллография. Том 26. 1981. Выпуск 3.- С637−639.
- Брон В.А. О рекристаллизации корунда // Доклады Академии Наук СССР. -1951. -Том LXXX, № 4. С.661−664.
- Шевченко В.Я., Баринов С. М. Техническая керамика.- М.: Наука, 1993. -187с.
- Гогоци Т.А. К вопросу о классификации малодеформирующихся материалов по особенностям их поведения при нагружении // Проблемы прочности. -1977. № 1. — С.77−82.
- Керамика из высокоогнеупорных окислов. Под ред. Д. Н. Полубояринова, Р. Я. Попильского. М.: Металлургия, 1977. — 304с.
- Баринов С.М., Шевченко В. Я. Прочность технической керамики. М.: Наука, 1996.- 159с.
- Лукин Е.С., Попов Н. А., Здвижнова Н. И. и др. Особенности получения плотной керамики, содержащей диоксид циркония // Огнеупоры и техническая керамика. 1999. — № 9. — С.5−9.
- Подзорова Л.И., Ильичева А. А., Михайлина Н. А., Пенькова О. И. Высокопрочные керамические материалы на основе поликристаллического тетрагонального Zr02, стабилизированного Lu203 // Огнеупоры и техническая керамика. 1999. — № 7.-С.33−36.
- Шевченко А.В., Рубан А. К., Дудник Е. В. Высокотехнологичная керамика на основе диоксида циркония // Огнеупоры и техническая керамика. 2000. — № 9. -С.2−8.
- Лаптев А. М. Зависимости между напряжениями и деформациями при пластическом деформировании пористых металлов. I. Теория пластического течения // Порошковая металлургия. 1985 — № 9. — С.9−10.
- Хейфец Л.И., Неймарк А. В. Многофазные процессы в пористых средах. -М.:Химия, 1982. С. 13−35.
- Грег. С., Синг К. Адсорбция. Удельная поверхность. Пористость. М.:Мир, 1984. — 306с.
- Jian-Lin Shi, Jian-Hua Gao, Zu-Xiang, and Tung-Sheng. Sintering Behavior of Agglomerated Ziconia Compacts // J. Am. Ceram. Soc., 1991. Vol.74. — № 5. -C.994−997.
- Морохов И.Д., Трусов Л. И., Чижик С.JI. Ультрадисперсные металлические среды. М.:Атомиздат, 1979. — 263с.
- Сысоев В.Ф., Зырянов В. В. Влияние механического диспергирования оксидных порошков на характеристики их структуры и спекаемость // Порошковая металлургия. 1991. — № 8. — С. 18−21.
- Дудник Е.В., Зайцева З. А., Шевченко А. В., Лопато Л. М. Методы получения дисперсных порошков на основе диоксида циркония (Обзор) // Порошковая металлургия. 1993. — С.24−30.
- Галахов А.В., Вязов И. В., Шевченко В. Я. Компактирование и спекание агломерированных ультрадисперсных порошков Z1O2 // Огнеупоры. 1989. — № 9. — СЛ 2−16.
- Дудник Е.В., Зайцева З. А., Шевченко А. В., Лопато Л. М. Спекание ультрадисперсных порошков на основе диоксида циркония (Обзор) // Порошковая металлургия. 1995. — № 5/6. — С.43−52.
- Галахов А.В., Цибайло Е. В. Неоднородность упаковки в порошковых компактах и прочность получаемой из них керамики // Огнеупоры и техническая керамика.-1997. № 5. — С. 14−19.
- Галахов А.В. Особенности спекания аэрозольных порошков // Огнеупоры и техническая керамика. 1998. — № 1−2. — С.29−33.
- Иванов Ю.Ф., Пауль А.в., Конева И. А. и др. Электронно-микроскопический анализ нанокристаллических материалов // Физика металлов и металловедение.- 1991.-№ 7. С.206−208.
- Вильк Ю.Н. Дисперсность и фазовый состав некоторых ультрадисперсных порошков содержащих Zr02// Огнеупоры и техническая керамика. 1998. — № 7.- С.22−25.
- Королёв П.В., Кульков С. Н. Микроструктура и фазовый состав ультрадисперсного плазмохимического порошка Zr02(Y) // Перспективные материалы. 1998. № 1. — С.67−72.
- Лёвина В.В., Рыжонков Д. И. Химические методы получения ультрадисперсных систем // Физикохимия ультрадисперсных систем. Сборник научных трудов IV Всероссийской конференции. М.: МИФИ, 1999. С.73−76.
- Галахов В.Я., Вязов И. В., Шевченко В. Я. Компактирование и спекание агломерированных ультродисперсных порошков Zr02 // Огнеупоры. 1989. — № 9.- С.12−16.
- Панова Т.И., Малышева С. И., Дроздова И. А., Глушкова В. Б. Золь-гель синтез твердых растворов Zr02 с Y203// ЖПХД995. Т. 68. — № 8. — С.1385−1387.
- Maskensia J.D. Applications of sol-gel method for glass and ceramics processing // Ultra-structure processing of ceramics glass and composites. New- York- London. -P. 15−26.
- Мержанов А.Г. Самораспространяющийся высокотемпературный синтез тугоплавких соединений // Вестник АН СССР, 1976. № 16. — С.20−22.
- Carrison R. The Shaping jf engineering ceramics//La Seramica, 1989. 10, — № 1. -P. 10−14.
- Радомысельский И.Д., Сердюк Г. Г., Щербань Н. И. Конструкционные порошковые материалы. Киев: Техника, 1985. — 152с.
- Takaki Masaki. Mechanical properties of toughened ZrCb Y203 ceramics // J. Am. Ceram. Soc. — 1986. — 69, — № 8. — P.638−640.
- Аксельрод Е.И., Вольсон П. В., Чуднова H.M. и др. Влияние способа изготовления керамики из диоксида циркония на её механическую прочность // Огнеупоры.-1990. № 9. — С.8−12.
- Галахов А.В., Цибайло Е. В. Неагломерированные порошки для трансфор-мационно-упрочненной конструкционной керамики // Огнеупоры и техническая керамика. 1997. — № 6. — С.5−8.
- Минин В.М. Использование ультразвука при обработке термопластичных шликеров // Порошковая металлургия. 1990. — № 11. — С.36−40.
- Прюммер Р. Обработка порошкообразных материалов взрывом. -М.:Мир, 1990.- 128с.
- Миронов B.JI. Магнитно-импульсное прессование. Рига.: Зинаатне, 1980. -196с.
- Роман О.В., Горобцов В. Г. Актуальные проблемы порошковой металлургии / Под ред. О. В. Романа, B.C. Аруначалама. М.:Металлургия, 1990. — С.78−100.
- Иванов В. В. Получение наноструктурных керамик с использованием импульсных методов компактирования порошков // Физикохимия ультрадиспрес-ных систем. Сборник научных трудов IV Всероссийской конференции. М. -МИФИ. 1999.- 336с.
- Шевченко А.В., Рубан А. К., Дудник Е. В. Высокотехнологичная керамика на основе диоксида циркония // Огнеупоры и техническая керамика. 2000. — № 9. — С.2−8.
- Гегузин Я.Е. Физика спекания. М.:Наука, 1984. — 242с.
- Янагида X. Тонкая техническая керамика. М.:Металлургия, 1986. — 279с.
- Slamovich Е., Lange F.F. Densification behavior of crystal and polycrystalline spherical particles of zirconia // J. Amer. Ceram. Soc. 1990. 73. — № 11. — P.3368−3375.
- Ристич М., Арсентьева И. П. Закономерности спекания ультрадисперсных порошков металлов // Физикохимия ультрадисперсных систем. Сборник научных трудов IV Всероссийской конференции. М. МИФИ. — 1999.- 336с.
- Herring С. Effect of Chang of Scale on Sintering Phenomena. // J.Appl.Phys. -1950. V21. — № 4. — P.301−303.
- Шоршоров M.X., Алымов М. И. Ультрадисперсные и аморфные материалы в технологии порошковой металлургии // Материаловедение. 1997.- № 1.-С51−53
- Лукин Е.С., Макаров Н. А. Особенности выбора добавок в технологии корундовой керамики с пониженной температурой спекания // Огнеупоры и техническая керамика. 1999. — № 9. — С.10−13.
- Лукин Е.С., Аяди М. Б. и др. Прочная корундовая керамика с пониженной температурой спекания // Огнеупоры и техническая керамика- 1996.- № 10.-С.2−5.
- Грибовский П.О. Горячее литье керамических изделий. М.: Госэнергоиз-дат, 1956. — 176с.
- Уайт и Вэлтон. Форма и упаковка частиц // Журнал Американского керамического общества. № 5. — 1937.
- Попильский Р.Я., Кондрашов Ф. В. Прессование керамических порошков. -М.МеталлургияД968. С. 272.
- Попильский Р.Я., Пивинский Ю. Е. Прессование порошков керамических масс. М.:Металлургия, 1983. — 176с.
- Добровольский А.Г. Шликерное литьё. М.: Металлургия, 1977. — 240с.
- Третьяков Ю.Д., Твердофазные реакции. М.:Химия, 1978. — 359с.
- Гропянов В.М., Гропянов А. В. Взаимосвязь прочности керамики с кинетическими параметрами её спекания // Огнеупоры и техническая керамика.-2001.-№ 10.- с.37−40.
- Судзуки Т. Порошкообразный диоксид циркония и современное состояние в этой области. Сэрамиккусу, 1987. — Т.22.-С.22−28.
- Крюков В.А., Галахов А. В., Спекаемость порошков системы А12Оз Zr02 -У2Оз, полученных методом высокоскоростного затвердевания из расплава, в зависимости от исходной термической обработки // Огнеупоры и техническая керамика." 1998. № 7. — С. 17−19.
- Бутягин П.Ю. Проблемы и перспективы развития механохимии // Успехи химии. 1994. -Т.63. -№ 12. — С. 1031−1034.
- Хайнике Г. Трибохимия. М.:Мир, 1987. — 592с.
- Екобори Т. Физика и механика разрушения и прочность твердых тел. -М.Металлургия, 1971. 263с.
- ХодаковГ.С.Тонкое измельчение строительных материалов. М. :Стройиздат, 1972. 238с.
- Порошковая металлургия и напыление покрытий: Учебник для вузов // В. Н. Анциферов, Г. В. Бобров, JI.K. Дружинина и др. Б.С.-М.:Металлургия, 1987. -792с.
- Ходаков Г. С. Физика измельчения. М.:Наука, 1972. — 307с.
- Гусев А.И. //УФН, 1998. Т. 168. № 1.
- Павлушкин Н.М. Спеченный корунд. М.:Госстройиздат, 1961. — 210с.
- Прохоров И. Ю. Цирконийоксидные материалы из соосажденных порошков // Огнеупоры и техническая керамика. 1997. — № 12. — С.6−13.
- Дедов Н.В., Дорда Ф.А, Коробцев В. П., Кутявин Э. М., СоловьёвА.И. // Новые промышленные технологии. 1994. — № 1(261). — С.38−42.
- Гогоци Г. А., Галенко В. И. и др. К вопросу об оценке трещиностойкости керамики из S13N4, Zr02 И Огнеупоры и техническая керамика. 1996. — № 1. -С.21−25.
- Гогоци Г. А., Галенко В. И., Островой Д. Ю. Сопротивление индентированию керамики и кристаллов из диоксида циркония // Огнеупоры и техническая керамика. 1996. — № 3. С.2−11.
- Инструкция ИА-22−75−99. Дисперсные материалы. Газохроматографический метод определения радиуса, объёма пор, размера частиц. НИКИ. СХК. -инв.№ 11 139. 1999.
- Иванов В.В. Получение наноструктурных керамик с использованием магнитно-импульсного прессования порошков: Дис. докт. физ.-мат. наук.-Екатеринбург: ИЭФ УрО РАН.-1998.
- Порозова С.Е., Беккер В. Я., Кульметьева В. Б. Получение мелкозернистого композиционного материала на основе системы А1203 S1O2 — Zr02 // Огнеупоры и техническая керамика. — 2000. — № 2. — С.6−8.
- Карбань О.В., Саламатов Е. И. и др. АСМ-исследования нанокерамик А12Оэ, спечённых при различных температурах // Физикохимия ультрадисперсных систем. Сборник науч. трудов V Всероссийской конференции. Часть II. Екатеринбург: УрО РАН, 2001. С. 128−132.
- Быков Ю.В., Егоров С. В. и др. Микроволновое спекание нанодисперсных керамических материалов // Физикохимия ультрадисперсных систем. Сборник науч. трудов V Всероссийской конференции. Часть II. Екатеринбург: УрО РАН, 2001. С.14−19.
- Jenn-Ming Wu., Chih-Hsyong Wu. Sintering behaviour of highly agglomerated ultrafme zirconia powders // Journal of materials science 23 (1988). C.3290−3299.
- Lange F.F., Metcalf M. Processing-Related Fracture Origins: II, Agglomerate Motion and Cracklike Internal Surface Causes by Differential Sintering // J. Am. Ce-ram. Soc.-Vol.66. N0.6. — C.398−406.
- Королев П.В. Фазовые и структурные состояния в нанокристаллических порошках на основе диоксида циркония: Дисс. канд. физ.-мат. наук. Томск: ИФПМ. 1998. — 192с.
- Mikito Kitayama and Joseph A. Pask Formation and control of agglomerates in alumina powder // J. Am. Ceram. Soc. Vol.79. — №.8. — 1996. — P.2003−2011.
- Дабиджа А. А, Прокофьев A.B., Акимов Г. Я. и др. Роль механохимической активации в формировании структуры и свойств реакционносвязанной керамики на основе муллита и диоксида циркония // Огнеупоры. 1990. — № 4. — С.2−3.
- Анциферов В.Н., Овчинникова В. Н. Струтурная модель низкотемпературного фазового перехода и разрушения керамического материала на основе диоксида циркония // Огнеупоры и техническая керамика. 1997. — № 6. — С.2−4.
- Вильк Ю.Н. Дисперсность и фазовый состав некоторых порошков на основе диоксида циркония // Огнеупоры и техническая керамика. 2001. -№ 7. — С.22−25.
- Man F. Yan. Effect of Physical, Chemical, and Kinetic Factor on Ceramic Sintering // Advance in Ceramics, Vol.21: Cer. Powder Science, Cohyring, 1987, The Am. Ceram. Soc.
- Burke J.E. Some Factors Affecting the Rate of Grain Growth in metals // Trans. Metall. Soc. AIME. 1949. — 180. — P.73−91.
- Бакунов B.C., Беляков А. В. Перспективы повышения возпроизводимости структуры и свойств керамики // Огнеупоры и техническая керамика. 1998. -№ 2. — С.16−21.
- Икума Н., Мориеси Ю. Теория спекания // Коге дзайре.-1987. 35,№ 16. -С.24−29.
- Richard H.J. Hannnink, Michael V. Swain Metastability of the Martensitic Transformation in a 12 mol% Ceria-Zirconia Alloy: II, Grinding Studies//J. Am. Ceram. Soc. 72.-8. 1358−64 (1989).
- Annamalai V.E., Sornakumar Т., Gokularathnam C.V., Krishnamurthy R. Transformation during Grinding of Ceria-Stabilized Tetragonal Zirconia Polycryctals // J. Am. Ceram. Soc.75 9. 2559−64 (1992).
- Саблина Т.Ю. Формирование структуры и механические свойства спеченных в вакууме керамик: Дисс. канд. техн. наук.-Томск: ИФПМ. 1994.- 182с.
- Немытко В.Е., Галахов А. В. и др. Керамические материалы для уплотни-тельных элементов бытовой сантехнической арматуры // Огнеупоры и техническая керамика. 1997. — № 2. — С.25−28.
- Кульков С.Н., Мельников А. Г. и др. Вязкая конструкционная керамика: получения, свойства, применение // Сборник трудов «Механика и машиностроение». Томск. 2000. С.113−120.
- Кульков С.Н., Мельников А. Г., Андриец С. П., Рыжова JI.H., Батьян В. Г. Технологические свойства ультрадисперсных плазмохимических порошков // Стекло и керамика. 2001. — № 1. -С.20−22.
- Кульков С.Н., Мельников А. Г., Андриец С. П., Рыжова JI.H. Метод шликерного литья в технологии нанокристаллических порошковых материалов // Тез. докл. Всероссийской конференции «Физикохимия ультрадисперсных систем». -Томск, 19−23 августа 2002 г.
- S. Kulkov, S. Andriets, A. Melnikov and AJoukov. Shock treatment of oxide nanopowders I I In. Proc. Conf. On Modern Material and Tecnologies CIMTEC-2002. Florence, Italy, p. l 12.