Влияние агрегации на эволюцию микроструктуры оксидных порошков в процессах синтеза, термической обработки и спекания
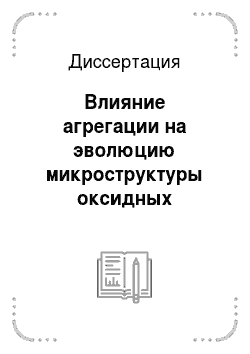
Диссертация
Практическая ценность работы связана с разработкой методов управления агрегатной структурой высокодисперсных оксидных порошков, основанных на использовании ультразвукового воздействия на промежуточных стадиях синтеза. Указанное воздействие позволяет в широких пределах регулировать величину усадки и размер кристаллитов при спекании компактированных порошков. Проведено также критическое… Читать ещё >
Содержание
- 1. ВВЕДЕНИЕ
- 2. ОБЗОР ЛИТЕРАТУРЫ
- 2. 1. Методы получения, химические свойства и 8 структура объектов исследована
- 2. 1. 1. Оксид железа (III)
- 2. 1. 2. Цирконат бария
- 2. 2. Морфологические аспекты процесса 16 термического разложения
- 2. 3. Методы исследования агрегированных порошков
- 2. 3. 1. Распределение частиц по размерам
- 2. 3. 2. Удельная площадь поверхности
- 2. 3. 3. Пористость
- 2. 3. 4. Плотность
- 2. 3. 5. Морфология частиц
- 2. 3. 6. Агрегация/агломерация 32 2.3. 7. Определение фрактальной размерности
- 2. 4. Рост зерна и спекание агрегированных 37 порошков
- 2. 5. Реология порошкообразных материалов
- 2. 5. 1. Сегрегация порошков во вращающихся цилиндрах
- 2. 5. 2. Неупорядоченные электрические цепи
- 2. 5. 3. Основные положения теории 5 6 детерминированного хаоса
- 2. 1. Методы получения, химические свойства и 8 структура объектов исследована
- 3. 1. Приготовление исходных образцов
- 3. 2. Термическая обработка
- 3. 3. Методы диспергирования
- 3. 4. Методы анализа
- 4. 2. Эволюция микроструктуры оксидного порошка в 82 процессах дополнительной термообработки и спекания
- 4. 3. Реологическое поведение смесей порошков
Список литературы
- A.G.Evans, J.Am.Ceram.Soc., 65 (1982) 497−501
- J.S.Reed, «Introduction to the principles of ceramics processing», pp.449−61, Wiley, Singapore 1989 «Gmelins Handbuch der Anorganischen Chemie», bearb. v. R.J.Meyer, Band 59(Fe), Teil Bl, S.63−73, Chemie, Berlin, 1929
- Encyclopaedia of Inorganic Chemistry", ed: R.B.King, vol.4, p. 1701, Wiley & Sons, 1994
- Gmelins Handbuch der Anorganischen Chemie", bearb. v. R.J.Meyer, Band 59(Fe), Teil B5, S.1001−4, Chemie, Weinheim, 1932
- H.Montgomery, R.V.Chastain et al., Acta Crystallographica, 22 (1967) 775−80
- E.N.Maslen, V.A.Streltsov et al., Acta Crystallographica1. B, 50 (1994) 435−41
- А.Уэллс, «Структурная неорганическая химия», под ред. М.А.Порай-Кошица, Москва, Мир, 1987 А.N.Shmakov, G.N.Kryukova et al., J. Appl.Cryst., 28 (1995) 141−5
- Baudisch, W.H.Hartung, Inorg.Synth. 1 (1939) 185 H. Takei, S. Chiba, J. Phys.Soc.Japan, 21 (1966) 1255 S. Kachi, K. Momiyama et al., J. Phys. Soc. Japan, 18 (1963) 106
- G.D.Renshaw, C. Roscoe, Nature, 224 (1969) 263−4 T. Katsura, A. Muan, Trans. AIME, 230 (1964) 80 A. Morawski, A. Paszewin et al., Superlattices & Microstructures, 21 Supp.A. (1997) 213−217
- A.Erb, E. Walker et al., Physica С 282 (1997) 459−460
- S.Gerhold, M. Aigner, W. Assmus, Physica С 282 (1997) 719 420
- R.X.Liang, D.A.Bonn, W.N.Hardy, Physica С 304 (1998) 10 511
- D.P.Birnie, M.H.Jilavi et al., J. Sol-Gel Science & Technology, 13 (1998) 855−859
- Y.B.Huang, R. Flukiger, Physica С 294 (1998) 71−82 M. Dhalle, A. Polcari et al., Physica С 310 (1998) 127−131 Y. Takao, M. Avano, Y. Kuwahara, AICHE Journal, 4 3 (1997) 2616−23
- H.Boudrine, M. Ausloos et al., Superconductor Science & Technology, 11 (1998) 803−809
- R.Cloots, В. Robertz et al., Mater.Sci. &Eng. B, 53 (1998) 154−158
- Gmelins Handbuch der Anorganischen Chemie", bearb. v. R.J.Meyer, Band 42 (Zr), S. 440−441, Chemie, Weinheim, 1958 N.J.Welham, Me tall. &Mater. Trans. B, 29 (1998) 603−10 V.M.Fuenzalida, M.E.Pilleux, J.Mater.Res., 10 (1995) 2749−54
- W.J.Zheng, C. Liu et al ., Mater.Lett., 30 (1997) 93−97 S. Gopalan, K. Mehta, A.V.Vikar, J.Mater.Res., 11 (1996) 1863−65
- H.Herrig, R. Hempelmann, Nanostruct. Mater., 9 (1997) 24 144
- B.C.Gaskins, J.J.Lannutti, J. Mater.Res., 11 (1996) 195 359
- E. P. Turevskaya, D.V.Berdyev, N.Y.Turova, J. Sol-Gel Science & Technology, 8 (1997) 111−15
- M.Veith, S. Mathur et al., Eur. J. Inorg. Chem., 9 (1998) 1327−32
- I.Martynenko, О.A.Shlyakhtin et al., Inorg. Mater., 34 (1998) 487−90
- G.Pfaff, Mater.Lett., 24 (1995) 393−97
- D.Dierickx, I. Houben et al., J. Mater.Sci.Lett., 15 (1996) 1573−76
- M.Paranthaman, S.S.Shoup et al., Mater.Res.Bull., 321 997) 1697−1704
- N.M.Alford, A. Templeton, S.J.Penn, Superconductor Science & Technology, 11 (1998) 703 J.C.Schmidt, A. Tigges, G.J.Schmitz, Mater.Sci. &Eng. B, 531 998) 115−118
- Gmelins Handbuch der Anorganischen Chemie", bearb. v. R.J.Meyer, Band 42(Zr), S.275−278, Chemie, Weinheim, 1958 ibid., S.215−250
- Phase Diagrams for Ceramists. 1975 Supplement", ed.: M.K.Reser, ACerS, Columbus, 1975, p. 76−78 L. Lutterotti, P. Scardi, J. Appl. Cryst., 23 (1990) 246−252 R.E.Hann, P.R.Suitch, J.L.Pentecost, J. Am.Ceram.Soc., 68 (1985) 285−286
- Gmelins Handbuch der Anorganischen Chemie", bearb. v. R.J.Meyer, Band 30(Ba), S.149−155, Chemie, Weinheim, 1932 W. Gerlach, Z. Phys. , 9 (1922) 184−192
- A.V.Shevchenko, L.M.Lopato et al. , Inorg.Mater., 23 (1987) 1322−25
- Phase Equilibria Diagrams. Volume XI. Oxides. «, ed.: R. S. Roth, ACerS, Westerville, 1991, pp.73−75
- H.D.Megaw, Proc.Phys.Soc.London, 58 (1946) 133−52 F.C.Tompkins, „Decomposition Reactions"/ in: „Treatise on Solid State Chemistry. Vol.4. Reactivity of Solids.“, ed.: N.B.Hannay, Plenum Press, N.Y.-London, 1976
- E.А.Продан, „Неорганическая топохимия“, под ред. В. В. Свиридова, Минск, Наука и Техника, 1986
- Chemical Kinetics. Vol.22. Reactions in the Solid State.“, eds.: C.H.Bamford and С.F.H.Tipper, Elsevier, 1980
- P.J.Herley, P.W.M.Jocobs, and P.W.Levy, Proc.Roy. Soc. Lond. A, 318 (1970) 197−211
- P.J.Herley, P.W.M.Jocobs, and P.W.Levy, J.Chem.Soc. A, (1971) 434
- K.M.Towe, Nature 274 (1978) 239−40
- E.Traversa, P. Nunziante, et al., J.Mater.Res. 13 (1998) 1335−44
- Yu.D.Tretyakov, N.N.Oleinikov, 0.A.Shlyakhtin,
- Cryochemlcal Technology of Advanced Materials», Chapman & Hall, 1997
- S. A. Alconchel, M.A.Ulla, E. A. Lornbardo, Mater. Sci. Eng. В 38 (1996) 205−15
- F.F.Lange, Mat.Res.Soc.Symp.Proc. 24 (1984) 247−54
- J.W.Halloran, Role of Powder Agglomerates in Ceramics Processing/ in: «Forming of Cermics», eds.: J.A.Mangels and G.L.Messing, ACerS, Columbus OH, 1983, pp.67−75
- S.G.Malghan, P. S.Wang, and V.A.Hackley, Techniques for Characterization of Advanced Ceramic Powders/ in: «Chemical Processing of Ceramics», eds.: B.I.Lee and E.J.A.Pope, Marcel Dekker, N. Y -Basel-Hong Kong, 1994
- J.L.Shi, Z.X.Lin, et al., J. Eur.Ceram. Soc. 13 (1994) 26 573
- M.Q.Li, D.Z.Hu, and Z.N.Chi, «Determination of Agglomerate Strength in Zirconia Powders"/ in: Ceramic Transactions. Vol.22. Ceramic Powder Science IV., eds.: S. Hirano, G.L.Messing, and H. Hausner, ACerS, Westerville, Ohio, 1991
- S.G.Thoma, M. Ciftcioglu, and D.M.Smith, Powder Technology 68 (1991) 53−61
- S.G.Thoma, M. Ciftcioglu, and D.M.Smith ibid., 63−69
- S.G.Thoma, M. Ciftcioglu, and D.M.Smith, ibid., 71−78
- B.S.Park, D.M.Smith, S.G.Thoma, Powder Technology 7 6 (1993) 125−33
- Particle Size-Analysis», ed.: P.J.Lloyd, Wiley-Interscience, N.Y., 1988
- T.Allen, «Particle Size Measurement. 4th ed.», Chapman and Hall, London, 1991
- S.G.Malghan, et al., Powder Technology 73 (1992) 275−84 H.N.Frock and E.L.Weiss, Powder Technology 57 (1988) 3539
- T.Neesse, J. Dueck, and T. Thaufelder, Part.Part.Syst. Charact. 13 (1996) 295−300 S. Brunaur, P.H.Emmett, and S. Teller, J. Am.Chem.Soc. 60 (1938) 309−19
- S.G.Malghan, A.L.Dragoo, et al., Ceramics, Today-Tomorrow's Ceramics, Part D, 66D (1991) 3249−59
- S.Lowell and J.E.Shield, «Powder Surface Area and Porosity. 2nd ed.», Chapman and Hall, London, 1984 E.W.Washburn, Phys.Rev. 17 (1921) 273
- M.S.Mohammadi and N. Harnby, Powder Technology 92 (1997) 1−8
- D.E.Niesz, R.B.Bennett, and M. Snyder, Am. Ceram. Soc.Bull. 51 (1972) 677
- S.J.Lukasiewicz and J.S.Reed, Am. Ceram.Soc.Bull. 57 (1978) 789
- J.Feder, «Fractals», Plenum Press, N.Y.-London, 1988. J.K.Kjems, Fractals and Experiments/ in: «Fractals and Disordered Systems», eds.: A. Bunde, S. Halvin, Springer-y/erlag, Berlin, 1991, p.275
- D.A.Weitz, M. Oliveria, Phys.Rev.Lett. 52 (1984) 1433
- Physical Ceramics. Principles for Ceramic Science and Engineering." Eds.: Y.-M.Chiang, D.P.Birnie and W.D.Kingery, John Wiley & Sons, N.Y.-Toronto-Singapore, 1997
- C.D.Terwilliger, Ph.D. Thesis, MIT, 1993 M. Hillert, Acta Met., 13 (1965) 227
- M.F.Yan, R.M.Cannon, and H.K.Bower, in: «Ceramic Microstructures '76», eds.: R.M.Fulrath and J.A.Pask, Westview Press, Boulder CO, 1977, pp.27307 W. Cahn, Acta Met. 10 (1963) 789
- A.M.Glaeser, H.K.Bower and R.M.Cannon, J .Am. Ceram.Soc. 69 (1986) 119−25
- R.J.Brook, J. Am.Ceram.Soc. 52 (1969) 59 J.C.Williams, Powder Technology 15 (1976) 245 D.S.Parsons, Powder Technology 13 (1976) 269 J. Bridgwater, Powder Technology 15 (1976) 215 T. Kohav, J.T.Richardson, and D. Luss, AIChE J. 41 (1995) 2465
- M.H.Cooke, D.J.Stephens, and J. Bridgwater, Powder Technology 15 (1976) 1
- A.Castellanos, J.M.Valverde, and A.T.Prez, Inorg.Mater. 35 (1999) 985−989 N. Nityanand, B. Manley, and H. Henein, Metall. Trans. B17 (1986) 247
- J.Rajchenbach, Phys.Rev.Lett. 65 (1990) 2221 M. Caponeri, S. Douady, S. Fauve, and C. Laroche, «Dynamics of Avalanches in a Rotating Cylinder"/ in: Mobile Particulate Systems, eds.: E. Guazzelli and L. Oger, Kluwer, Dordrecht, 1995, p.331
- G.Metcalfe, T. Shinbrot, et al., Nature 374 (1995) 39
- H.E.Rose, Trans. Inst. Chem. Eng. 31 (1959) 47 R.P.Behringer, Nature 375 (1995) 15
- C.M.Dury and G.H.Ristow, Phys. Fluids 11 (1999) 1387−94. S.D.Gupta, D.V.Khakhar, and S.K.Bhatia, Powder Technology 67 (1991) 145
- M.B.Donald and B. Roseman, Br.Chem.Eng. 7 (1962) 749. ibid., 823
- M.Nakagawa, Chem.Eng.Sci. 49 (1994) 2540
- S.B.Savage, in: «Disorder and Granular Media», eds.: D. Bideau and A. Hansen, North-Holland, Amsterdam, 1993, p. 255
- K.M.Hill, A. Caprihan, and J. Kakalios, Phys.Rev.Lett. 78 (1997) 50−53
- G.Metcalfe and M. Shattuck, Physica A 233 (1996) 709−17. T. Terao, A. Yamaya, and T. Nakayama, Phys.Rev.E 57 (1998) 4426−30
- B.H.Kaye, J. Grattonliimatainen, N. Faddis, Part.Part.Sys. Charact. 12 (1995) 232−236
- G.Grimmett, «Percolation», Springer-Verlag, N.Y.-Berlin-London-Paris-Tokio, 1989
- G.R.Grimmett and H. Kesten, Z. Wahrscheinlichkeitstheorie and Verwandte Gebiete 66 (1984) 335−66
- G.R.Grimmett, Random Flows: Network Flows and Electrical Flows through Random Media/ in: «Surveys in Combinatorics», ed.: I. Anderson, Cambridge University Press, 1985, pp.59−96
- H.Kesten, Annals of Probability 15 (1987) 12 31−71. Т. Шустер, «Детерминированный Хаос», Москва, Мир. 198 8. J.S.Kirkaldy, Sci. Metail.Mater. 24 (1990) 179. H.С.Akuezue, J. Stringer, Metal. Trans. A, 20A (1989) 2767−82
- S.L.Tags, С.L.LeMaster, С.В.LeMaster, D.A.McQuarrie, J.Chem.Edu. 71 (1994) 363
- R.J.Field, F.W.Schneider, J.Chem.Edu. 66 (1989) 195. R. Yoshikawa, S. Nakata, M. Yamonaka, T. Waki, J.Chem.Edu. 66 (1989) 205
- B.Rush, J. Newman, J. Electrochem. Soc. 142 (1995) 3770. A.J.Markworth, J. Stringer, R.W.Rollins, MRS Bull. 20 (1995) 20
- P.Paramananda, M.A.Rhode, G.A.Johnston, R.W.Rollins, H.D.Dewald, A.J.Markworth, Phys.Rev.E 49 (1994) 5007. H.D.Dewald, P. Paramananda, R.W.Rollins, J. Electrochem. Soc. 140 (1993) 1969
- К.Krischer, M. Lubke, W. Wolf, M. Eiswirth, G. Erti, Ber.Bunsenges.Phys.Chem. 95 (1991) 820
- С.А.Салтыков, «Стереометрическая металлография», М., аллургия, 1970, с.149−158.
- К.В.Томашевич, «Моделирование процессов эволюции странственных структур в твердом тел®-, Дипломная работа, МГУ, 1998.1. ФОССНЙСКАй1. ГТОСГД/PCTDEHH, 1. Челнощ?)'